1.2.3 Explore Multiple Locations In A Lab
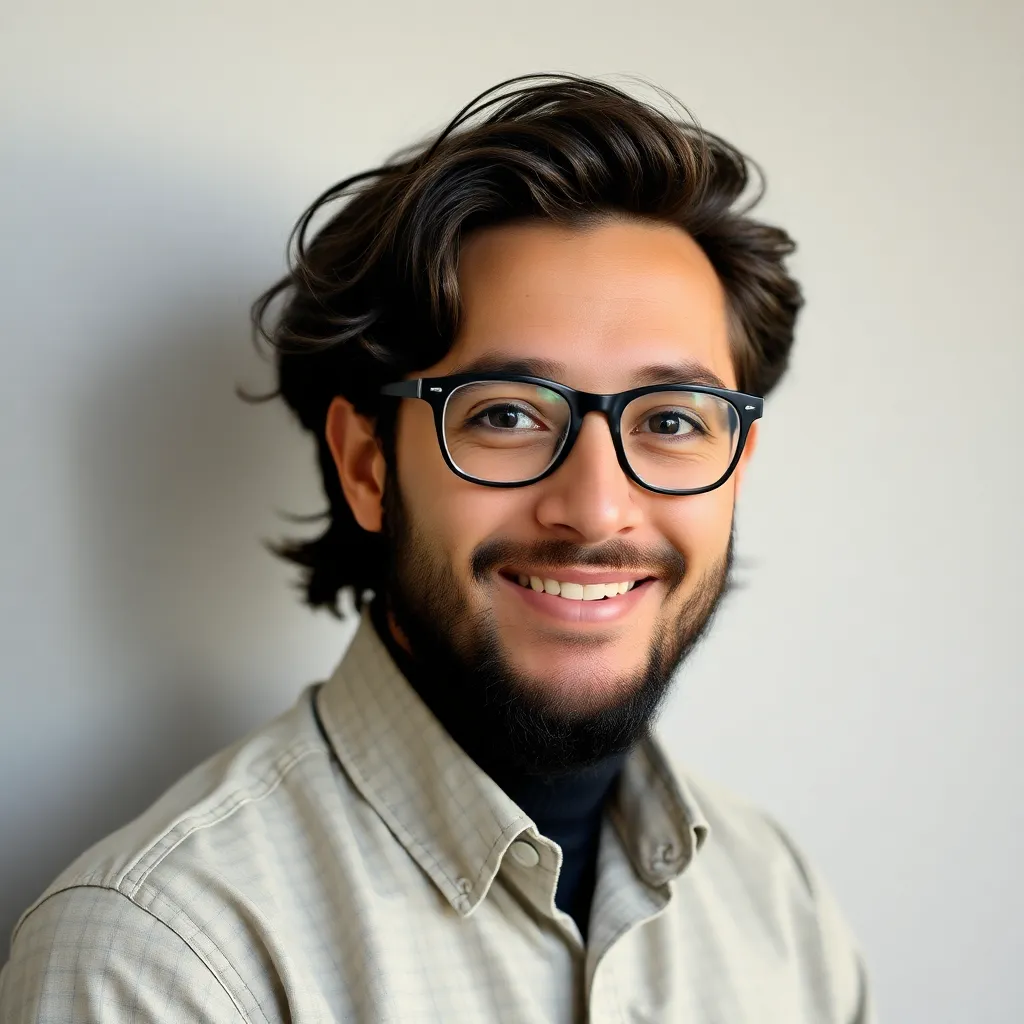
Onlines
Mar 19, 2025 · 6 min read
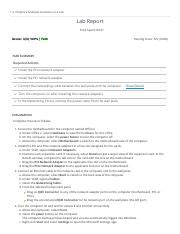
Table of Contents
1.2.3: Exploring Multiple Locations in a Lab Setting: A Comprehensive Guide
The ability to efficiently and safely navigate and manage multiple locations within a laboratory setting is crucial for researchers, technicians, and lab managers alike. This comprehensive guide explores the multifaceted aspects of managing multiple locations in a lab, delving into best practices, safety considerations, and technological solutions designed to streamline workflows and enhance overall efficiency. We will focus on the practical application of "1.2.3" as a mnemonic device to structure and remember key aspects of this process.
1. Inventory Management and Location Tracking: The Foundation of Efficiency
This first step, "1," focuses on the foundational element of effective multi-location lab management: precise inventory control and location tracking. This isn't simply about knowing what you have; it's about knowing where you have it, when it was last accessed, and who accessed it. This detailed level of tracking is essential for maintaining accuracy in research, preventing loss or damage of valuable samples or equipment, and ensuring regulatory compliance.
Utilizing Technology for Location Tracking
Several technological solutions can significantly improve location tracking:
-
Barcode and QR Code Systems: Assigning unique barcodes or QR codes to each item allows for rapid scanning and automated updating of inventory databases. This system provides real-time location tracking, minimizing search time and preventing misplacement. Integrating these systems with a laboratory information management system (LIMS) streamlines data management.
-
RFID (Radio-Frequency Identification) Technology: RFID tags offer a contactless solution for tracking items, eliminating the need for manual scanning. They are particularly useful for tracking temperature-sensitive materials or equipment, as they can be integrated with environmental monitoring systems.
-
Real-time Location Systems (RTLS): RTLS uses various technologies, including Bluetooth beacons, Wi-Fi, or ultra-wideband (UWB) to pinpoint the exact location of tagged assets within the lab. This level of precision is invaluable for managing expensive or sensitive materials.
-
Dedicated Laboratory Information Management Systems (LIMS): A robust LIMS acts as the central hub for all lab data, including inventory, location, and usage information. Integrating inventory management, location tracking, and sample management modules within a single LIMS creates a seamless workflow and reduces the risk of human error.
Implementing a Robust Inventory Management System
Regardless of the chosen technology, a well-defined inventory management system requires:
-
Regular Audits: Conducting frequent inventory audits ensures the accuracy of the system and identifies any discrepancies between the physical inventory and the recorded data.
-
Clear Labeling and Organization: Items should be clearly labeled with unique identifiers and stored in designated locations. A standardized system of shelving, labeling, and storage helps to maintain order and prevent confusion.
-
Designated Personnel: Assigning specific personnel responsibility for inventory management ensures accountability and consistency.
2. Safety Protocols and Emergency Procedures: Prioritizing Safety Across Multiple Locations
The second step, "2," emphasizes the paramount importance of safety within a multi-location lab setting. Establishing and rigorously enforcing safety protocols is crucial, particularly when dealing with hazardous materials, specialized equipment, or multiple teams operating concurrently in different locations.
Developing Location-Specific Safety Procedures
Safety procedures should be location-specific, considering the unique hazards and risks associated with each area. For example, a location handling chemicals requires different safety protocols than one housing sensitive equipment. The following aspects should be detailed in the location-specific safety plan:
-
Emergency Exits and Evacuation Routes: Clearly marked emergency exits and evacuation routes should be established for each location, with regular drills conducted to ensure staff familiarity.
-
Emergency Contacts: Easily accessible lists of emergency contacts, including security personnel, emergency services, and lab supervisors, should be prominently displayed in all locations.
-
Personal Protective Equipment (PPE): The appropriate PPE should be readily available in each location, tailored to the specific hazards present.
-
Spill Kits and Emergency Response Procedures: Each location should have readily accessible spill kits and detailed procedures for handling chemical spills, equipment malfunctions, or other emergencies.
-
Hazardous Waste Disposal: Clearly defined procedures for the disposal of hazardous waste should be in place, along with designated storage areas for such materials. This must comply with all relevant regulations.
Implementing a Comprehensive Training Program
A comprehensive training program is essential for ensuring staff awareness of safety protocols and emergency procedures. This program should include:
-
Regular Safety Training: Scheduled safety training sessions should cover all relevant topics, including chemical handling, equipment operation, and emergency response procedures.
-
Location-Specific Training: Staff should receive location-specific safety training to address the particular hazards associated with each area.
-
Emergency Drills and Simulations: Regular emergency drills and simulations help to familiarize staff with evacuation procedures and emergency response protocols.
3. Communication and Collaboration: Fostering Seamless Workflow Across Locations
The third and final step, "3," highlights the critical role of communication and collaboration in efficient multi-location lab management. Effective communication ensures smooth workflows, prevents errors, and promotes a safe and productive environment.
Utilizing Communication Technologies
Several technologies can improve communication and collaboration:
-
Instant Messaging and Collaboration Platforms: Tools like Slack, Microsoft Teams, or similar platforms allow for real-time communication and information sharing between teams in different locations.
-
Centralized Communication Hubs: A centralized system, such as a shared intranet or digital bulletin board, can be used to disseminate important announcements, safety updates, and procedural changes.
-
Video Conferencing: Video conferencing facilitates real-time collaboration and remote consultation, especially beneficial when addressing complex technical issues or coordinating research activities across multiple locations.
Implementing Best Practices for Communication
Effective communication transcends technological tools. Essential elements include:
-
Clear and Concise Communication: Information should be communicated in a clear, concise, and readily understandable manner. Ambiguity should be avoided.
-
Regular Team Meetings: Regular team meetings, both in person and virtual, should be scheduled to facilitate discussion, information sharing, and problem-solving.
-
Open Communication Channels: Open communication channels should be encouraged to foster a culture of collaboration and mutual support. Feedback mechanisms should be in place to identify and address potential issues proactively.
-
Document Management System: A well-organized document management system, preferably integrated with the LIMS, ensures easy access to important information, SOPs, and safety manuals. This system needs to be accessible from all locations.
Conclusion: Optimizing Multi-Location Lab Management for Efficiency and Safety
Effective management of multiple locations in a laboratory setting demands a multi-pronged approach, combining technological solutions with robust safety protocols and effective communication strategies. By implementing the principles outlined under the "1.2.3" framework – inventory management, safety protocols, and communication – laboratories can optimize their operations, ensuring efficiency, safety, and compliance with all relevant regulations. This approach minimizes risks, maximizes productivity, and fosters a collaborative environment conducive to groundbreaking research and scientific advancements. Remember that continuous evaluation and improvement are key to maintaining a safe and efficient multi-location laboratory. Regular review of procedures, technologies, and training programs will ensure the lab remains at the forefront of best practices.
Latest Posts
Latest Posts
-
Summary Of Brave New World Chapter 4
Mar 19, 2025
-
Symbols In Their Eyes Were Watching God
Mar 19, 2025
-
Analyzing History Causes Of Ww1 Worksheet Answers
Mar 19, 2025
-
En El Mar Cuando Fui De Vacaciones
Mar 19, 2025
-
Unit 6 Progress Check Mcq Apush
Mar 19, 2025
Related Post
Thank you for visiting our website which covers about 1.2.3 Explore Multiple Locations In A Lab . We hope the information provided has been useful to you. Feel free to contact us if you have any questions or need further assistance. See you next time and don't miss to bookmark.