1.2.5 Mechanical System Efficiency Vex Answers
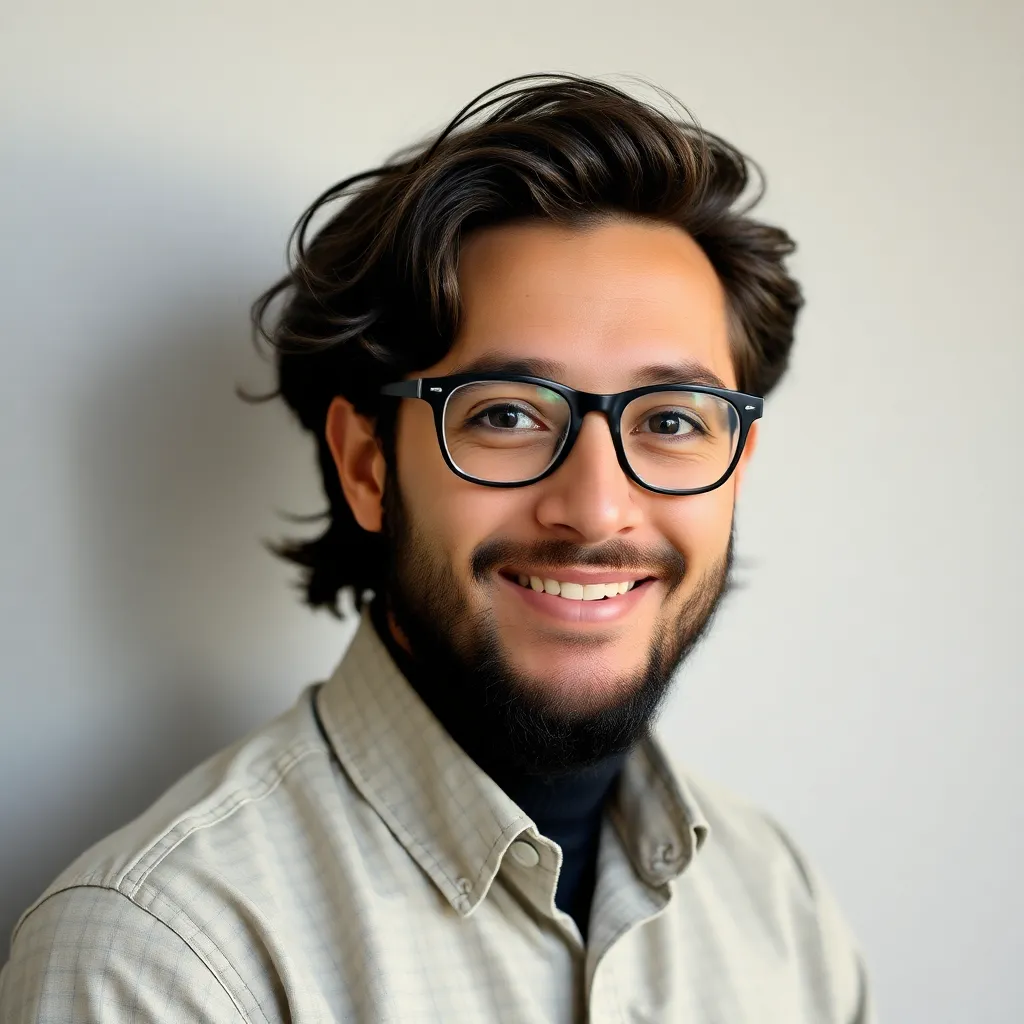
Onlines
Apr 05, 2025 · 5 min read
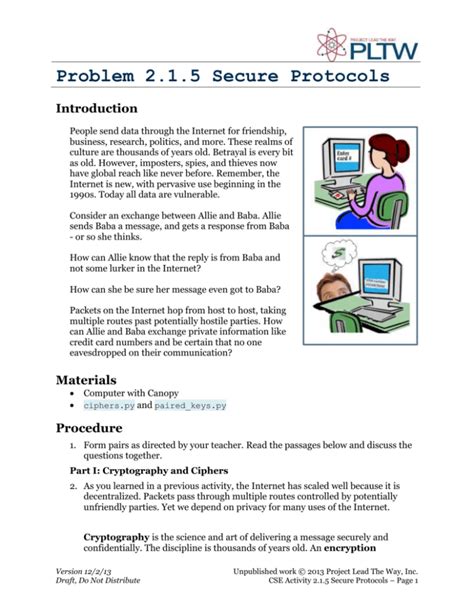
Table of Contents
Decoding VEX Robotics: A Deep Dive into Mechanical System Efficiency (1.2.5)
The VEX Robotics Competition challenges students to design, build, and program robots capable of complex tasks. Understanding mechanical system efficiency is crucial for success, and the 1.2.5 section often focuses on this critical aspect. This comprehensive guide will break down the concept of mechanical system efficiency within the VEX Robotics context, providing you with the knowledge and strategies to optimize your robot's performance. We'll explore various factors influencing efficiency, delve into practical applications, and offer solutions to common challenges.
What is Mechanical System Efficiency?
Mechanical system efficiency, in the context of VEX Robotics, refers to how effectively your robot converts the input energy (from the motor) into useful work (movement, lifting, etc.). A highly efficient system minimizes energy loss due to friction, inertia, and other inefficiencies, resulting in greater speed, power, and overall performance. It's about maximizing the output for a given input. A less efficient system wastes energy, leading to sluggish movement, reduced power, and potentially overheating motors.
Key Factors Affecting Mechanical System Efficiency
Several factors significantly impact a VEX robot's mechanical system efficiency:
1. Friction: This is perhaps the biggest culprit in energy loss. Friction occurs at various points:
- Gear Meshing: Improperly meshed gears or gears with excessive wear generate significant friction, reducing efficiency.
- Axle Bearings: Worn or poorly lubricated bearings create substantial resistance, slowing down movement.
- Chassis Contact: Friction between the chassis and the playing field surface can hinder movement, especially with heavy robots.
- Component Interactions: Any contact between moving parts that isn't precisely designed can introduce friction.
2. Gear Ratio: Selecting the appropriate gear ratio is paramount. A high gear ratio increases torque (rotational force) at the expense of speed, while a low gear ratio prioritizes speed over torque. The optimal ratio depends on the task; lifting heavy objects requires high torque, while fast traversing necessitates high speed. Choosing the wrong ratio can drastically reduce efficiency.
3. Inertia: Inertia is the resistance of an object to changes in its state of motion. A robot with a high moment of inertia (resistance to rotation) requires more energy to accelerate and decelerate, reducing overall efficiency. Careful weight distribution and the use of lighter components are crucial to minimize inertia.
4. Component Quality: The quality of individual components directly affects efficiency. High-quality gears, bearings, and motors are more efficient and durable than cheaper alternatives. This is an area where investing in better components often pays off in improved performance.
5. Design and Construction: A poorly designed or poorly constructed robot will inherently be less efficient. Clearance issues, misaligned components, and excessive play in the mechanisms all contribute to energy loss.
Optimizing Mechanical System Efficiency: Practical Strategies
Improving your VEX robot's mechanical system efficiency requires a multifaceted approach:
1. Minimizing Friction:
- Proper Lubrication: Regularly lubricate all moving parts with appropriate lubricant (such as bearing grease or silicone oil). Over-lubrication can be detrimental, so apply sparingly.
- High-Quality Bearings: Invest in high-quality bearings, ideally sealed to prevent contamination and maintain lubrication.
- Precise Gear Meshing: Ensure gears are properly meshed, avoiding excessive backlash (play). Use shims to fine-tune alignment if needed.
- Smooth Surfaces: Polish moving surfaces to reduce friction where possible.
- Reduce Contact Points: Design mechanisms to minimize contact between moving parts where possible.
2. Selecting the Right Gear Ratio:
- Analyze the Task: Carefully consider the required torque and speed for each mechanism. Simulations can help determine the best gear ratio.
- Experimentation: Test different gear ratios to find the optimal balance between torque and speed. VEXcode Pro and other programming platforms often allow for variable gear ratios.
- Consider Chain and Sprockets: Chains and sprockets can provide an efficient method of power transfer, particularly for mechanisms requiring higher torque and speed.
3. Managing Inertia:
- Strategic Weight Distribution: Distribute weight evenly throughout the robot to minimize its moment of inertia. Avoid placing heavy components at the extremities.
- Lightweight Components: Utilize lightweight yet durable components wherever possible. Carbon fiber and aluminum are strong options.
- Optimized Design: Design the robot's chassis and mechanisms to minimize unnecessary mass.
4. Component Selection:
- High-Quality Motors: Choose motors suitable for the task, considering their torque, speed, and stall current.
- Durable Gears: Select strong and durable gears designed for the expected loads. Metal gears generally offer superior durability and efficiency compared to plastic gears.
5. Precision in Design and Construction:
- CAD Modeling: Utilize CAD software to design and simulate the robot's mechanisms before building.
- Precise Assembly: Ensure all components are precisely aligned and securely fastened.
- Regular Inspection: Regularly inspect the robot for wear and tear, and address any issues promptly.
Troubleshooting Common Efficiency Problems
Encountering performance issues? Here are some common problems and solutions:
- Slow Movement: Check for excessive friction in bearings, gears, or chassis. Lubricate, replace worn components, or adjust gear ratios.
- Weak Lifting Power: Assess the gear ratio and motor selection. A higher gear ratio may be needed, or a more powerful motor might be required. Also, check for friction in the lifting mechanism.
- Overheating Motors: This suggests excessive load or inefficiency. Check for friction, optimize the gear ratio, or consider using a higher-capacity motor.
- Inconsistent Performance: This points to inconsistent friction or binding in the mechanism. Examine each component carefully for wear or misalignment.
Advanced Considerations: Beyond the Basics
For advanced VEX teams striving for peak performance, consider these enhancements:
- Finite Element Analysis (FEA): FEA software can simulate stress and strain on components, helping optimize designs for strength and weight reduction.
- Motor Control Algorithms: Advanced motor control algorithms can improve efficiency by precisely managing motor speed and torque.
- Energy Harvesting: Explore opportunities to recover energy during specific actions and reduce reliance on battery power. This is a niche area but can provide a significant edge.
Conclusion: The Pursuit of Efficiency
Mastering mechanical system efficiency is a continuous process of refinement and optimization. By meticulously addressing friction, selecting appropriate gear ratios, managing inertia, choosing quality components, and employing precision in design and construction, VEX Robotics teams can significantly enhance their robot's performance, ultimately leading to greater success in competitions. Remember, consistent evaluation, experimentation, and attention to detail are crucial for achieving optimal mechanical system efficiency in your VEX robot. Through diligent efforts, you can transform your robot from a good contender to a champion.
Latest Posts
Latest Posts
-
It Is Illegal For A Person 21 Years Of Age
Apr 06, 2025
-
Willem De Koonings Woman And Bicycle Is Controversial For Its
Apr 06, 2025
-
Compute Diffusion Coefficients For The Interdiffusion Of Carbon
Apr 06, 2025
-
Select The Sentence That Has The Correct Subject Verb Agreement
Apr 06, 2025
-
Identifying Transformations Homework 5 Answer Key
Apr 06, 2025
Related Post
Thank you for visiting our website which covers about 1.2.5 Mechanical System Efficiency Vex Answers . We hope the information provided has been useful to you. Feel free to contact us if you have any questions or need further assistance. See you next time and don't miss to bookmark.