2. Compute The Average Manufacturing Cost Per Drum Set.
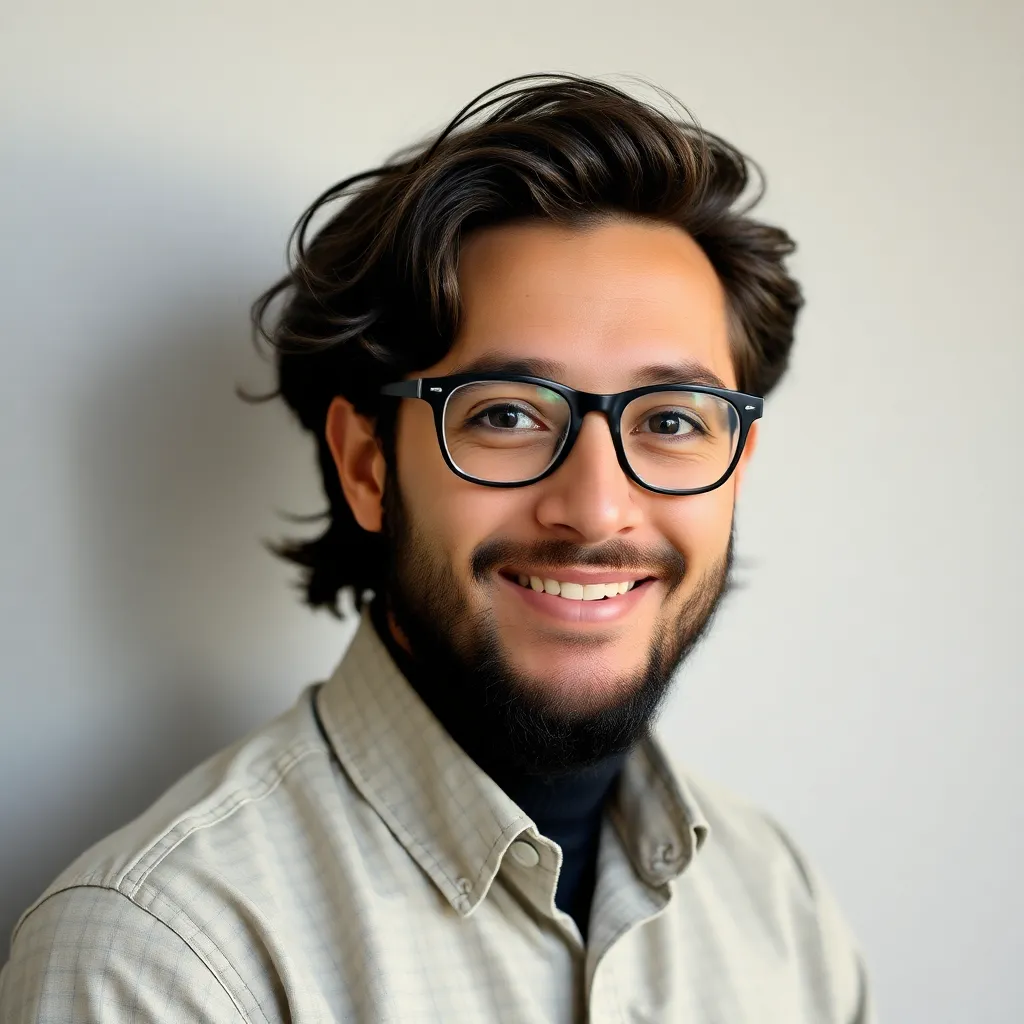
Onlines
May 10, 2025 · 6 min read
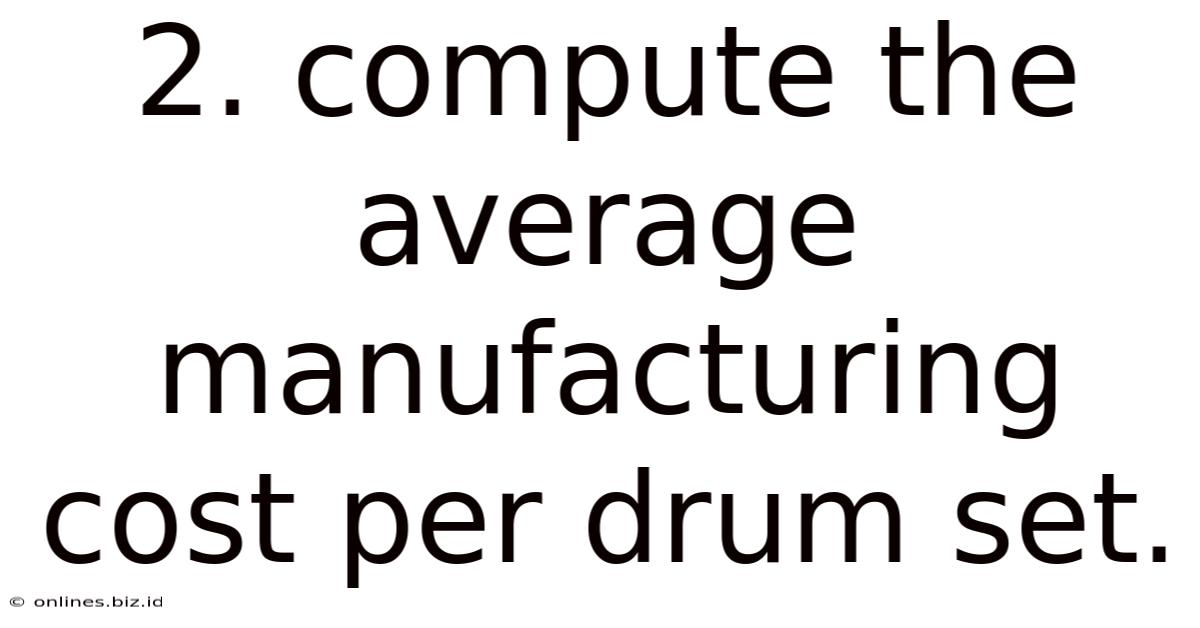
Table of Contents
Computing the Average Manufacturing Cost Per Drum Set: A Comprehensive Guide
Calculating the average manufacturing cost per drum set is crucial for any drum manufacturer aiming for profitability and competitive pricing. This process goes beyond simply adding up expenses; it requires a meticulous breakdown of all direct and indirect costs associated with production. This comprehensive guide will delve into the intricacies of this calculation, providing a step-by-step approach and exploring various factors that can influence the final cost.
Understanding Cost Components: Direct vs. Indirect Costs
Before diving into the calculation, understanding the different types of costs involved is paramount. Manufacturing costs are broadly categorized into:
1. Direct Costs: These are costs directly attributable to the production of a single drum set. They include:
-
Raw Materials: This is perhaps the most significant component, encompassing the cost of wood (various types like maple, birch, mahogany), hardware (lugs, hoops, bolts, etc.), drumheads (various brands and thicknesses), and any other materials used in the manufacturing process. Accurate costing requires tracking material usage per drum set and fluctuating material prices. Consider variations in wood quality and sourcing costs.
-
Direct Labor: This represents the wages and benefits paid to workers directly involved in the assembly of the drum set. This includes the time spent cutting, shaping, sanding, assembling, tuning, and finishing the drum shells and hardware. Consider labor efficiency and skill level impacting labor costs.
-
Manufacturing Overhead (Direct): This category can include costs directly tied to producing a single drum set, such as specialized tools used only for drum making or specific finishing supplies directly related to one drum set. This can be challenging to accurately allocate; methods such as activity-based costing can assist here.
2. Indirect Costs: These costs are not directly tied to a single drum set but are necessary for the overall manufacturing process. They are typically allocated based on a predetermined method.
-
Factory Overhead: This includes expenses like rent or mortgage payments for the factory, utilities (electricity, water, gas), factory maintenance, and depreciation of factory equipment.
-
Administrative Overhead: This covers costs related to general administration, such as salaries of administrative staff, office rent, and other administrative expenses. Accurate allocation of these costs requires a defined allocation method.
-
Selling, General, and Administrative (SG&A) Expenses: While not directly part of manufacturing, SG&A expenses contribute to the overall cost of bringing the product to market and should be considered for a complete picture of the product's cost.
Calculating the Average Manufacturing Cost: A Step-by-Step Approach
Let's assume we're analyzing the manufacturing cost of a basic five-piece drum set. Here's a step-by-step approach:
1. Gather Data: Begin by collecting comprehensive data on all cost components. Maintain meticulous records of raw material purchases, labor hours, and all overhead expenses. Use spreadsheets or dedicated cost accounting software for efficient data management.
2. Calculate Direct Costs: For each drum set, accurately determine the cost of raw materials used. Calculate the direct labor cost by multiplying the number of labor hours per drum set by the hourly wage rate (including benefits). Carefully allocate any direct manufacturing overhead.
3. Allocate Indirect Costs: Choose an appropriate allocation method to distribute indirect costs among the drum sets produced. Common methods include:
-
Machine Hours: Allocate overhead based on the machine hours used in production. This is suitable when machinery is a significant cost driver.
-
Direct Labor Hours: Allocate overhead based on the direct labor hours spent on each drum set. This method is simple but may not be accurate if the manufacturing process is highly automated.
-
Activity-Based Costing (ABC): ABC is a more sophisticated method that allocates overhead based on specific activities involved in production. It provides a more accurate cost allocation, particularly for complex manufacturing processes.
4. Calculate Total Manufacturing Cost per Drum Set: Sum the direct costs and the allocated indirect costs for a single drum set. This represents the total manufacturing cost of one unit.
5. Determine Average Manufacturing Cost: To calculate the average manufacturing cost across multiple drum sets produced within a specific period, divide the total manufacturing cost for all drum sets by the number of drum sets produced. This average provides a useful benchmark for pricing decisions and performance tracking.
6. Analyze and Refine: Regularly analyze the cost data to identify areas for potential cost reduction. Consider optimizing material usage, improving labor efficiency, and negotiating better prices with suppliers.
Example Calculation
Let's illustrate with a hypothetical example:
Cost Component | Cost per Drum Set |
---|---|
Raw Materials | $300 |
Direct Labor | $150 |
Direct Manufacturing Overhead | $50 |
Total Direct Costs | $500 |
Factory Overhead | $10,000 (Allocated over 100 drum sets) |
Administrative Overhead | $5,000 (Allocated over 100 drum sets) |
Total Indirect Costs | $150 |
Total Manufacturing Cost per Drum Set | $650 |
In this example, the average manufacturing cost per drum set is $650.
Factors Influencing Manufacturing Cost
Several factors can significantly impact the average manufacturing cost:
-
Material Prices: Fluctuations in the price of wood, hardware, and drumheads directly affect the cost. Securing reliable suppliers and negotiating favorable pricing are crucial.
-
Labor Costs: Wages, benefits, and labor productivity all contribute to labor costs. Automation and process optimization can help mitigate these costs.
-
Production Volume: Economies of scale often reduce the average cost per unit as production volume increases. Higher production allows for better negotiation with suppliers and more efficient use of resources.
-
Technology & Automation: Investing in advanced manufacturing technologies and automation can enhance efficiency and reduce labor costs, but requires substantial upfront investment.
-
Quality Control: Stringent quality control measures can increase costs but are necessary to maintain product quality and brand reputation.
-
Currency Fluctuations: If materials are sourced internationally, currency fluctuations can significantly affect input costs.
Beyond the Numbers: Strategic Implications
Computing the average manufacturing cost is not merely an accounting exercise; it's a strategic tool. Accurate cost data enables informed decision-making in several areas:
-
Pricing Strategy: The calculated cost provides a baseline for determining competitive and profitable pricing.
-
Product Development: Understanding cost drivers can inform product design and material choices, leading to more cost-effective products.
-
Inventory Management: Accurate cost data is crucial for effective inventory management to minimize holding costs and prevent stockouts.
-
Performance Measurement: Tracking changes in manufacturing costs over time allows for identifying areas needing improvement.
-
Investment Decisions: Cost data helps evaluate the feasibility of investing in new equipment or technologies.
Conclusion
Calculating the average manufacturing cost per drum set requires a detailed understanding of cost components and a systematic approach to data collection and analysis. By meticulously tracking direct and indirect costs, utilizing appropriate allocation methods, and regularly analyzing the data, drum manufacturers can optimize their production processes, establish competitive pricing, and achieve long-term profitability. Remember that this is an ongoing process; continuous monitoring and refinement are key to maintaining cost efficiency and competitiveness in the dynamic drum manufacturing market.
Latest Posts
Latest Posts
-
Which Of The Following Describes The Comparison Method Of Budgeting
May 10, 2025
-
Paint In Its Most Basic Form Is Composed Of
May 10, 2025
-
For The Holidays A Contractor Gives You A Historical
May 10, 2025
-
Color By Number Claim Evidence Reasoning
May 10, 2025
-
Concerts Musicals And Comedy Shows Are Examples Of
May 10, 2025
Related Post
Thank you for visiting our website which covers about 2. Compute The Average Manufacturing Cost Per Drum Set. . We hope the information provided has been useful to you. Feel free to contact us if you have any questions or need further assistance. See you next time and don't miss to bookmark.