A Bill Of Materials Contains The Blank______.
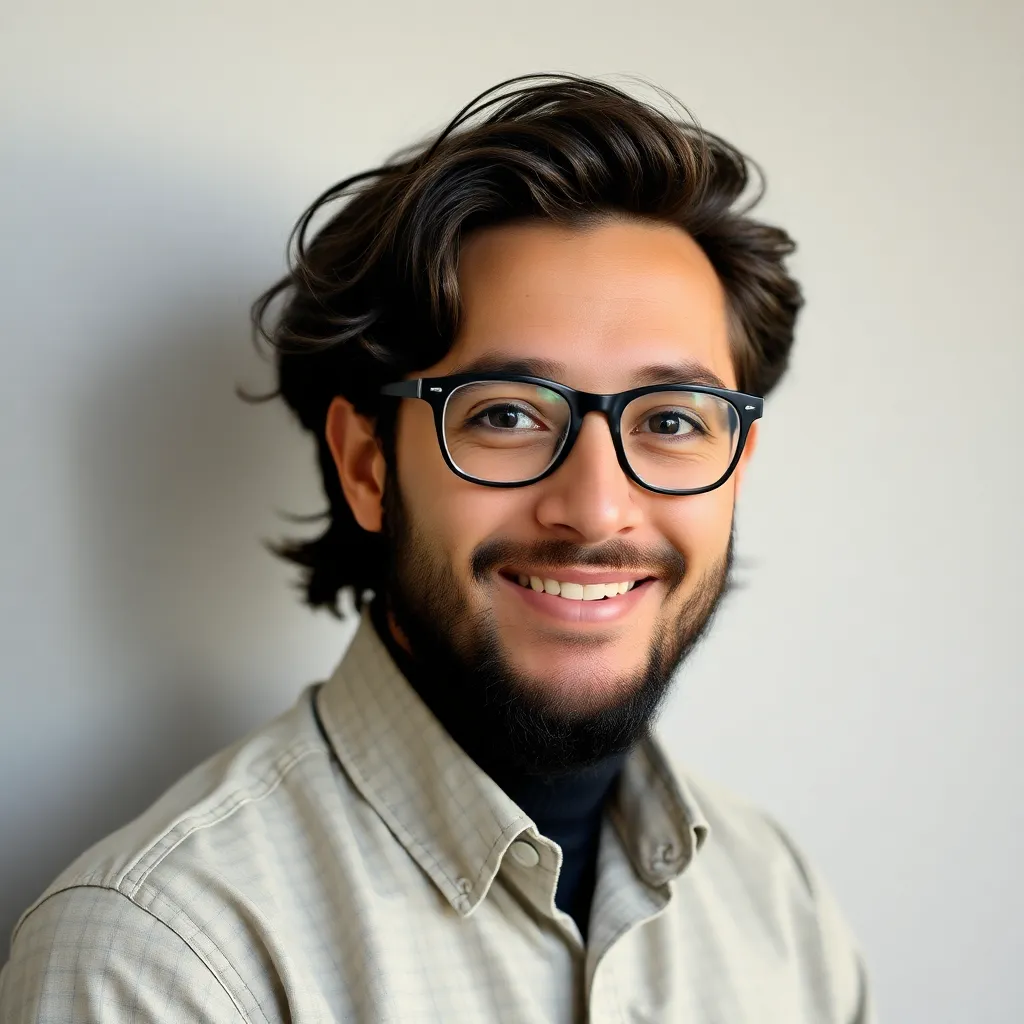
Onlines
May 12, 2025 · 6 min read
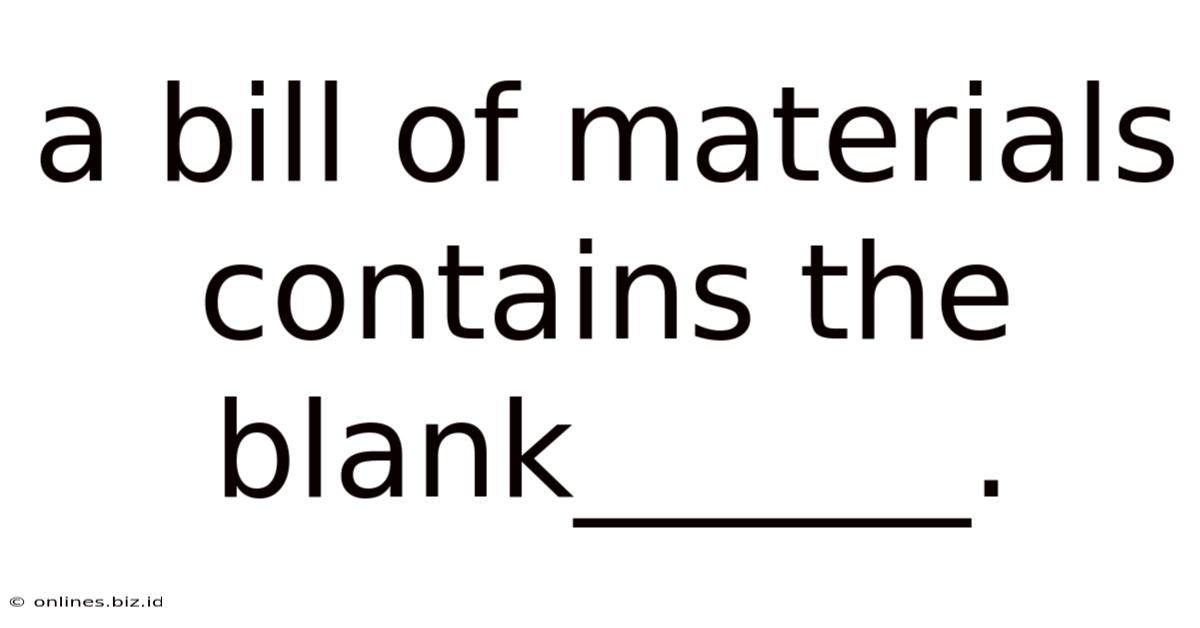
Table of Contents
A Bill of Materials Contains the Complete Recipe for Your Product
A Bill of Materials (BOM) is far more than just a simple list; it's the comprehensive recipe for your product. It's a crucial document in manufacturing, engineering, and project management, detailing every single component, subassembly, raw material, and part needed to create a finished product. Understanding its contents is vital for efficient production, accurate costing, and effective inventory management. This article delves deep into the components of a BOM, exploring its various types, uses, and the crucial information it contains.
The Core Ingredients: What a Bill of Materials Contains
At its heart, a BOM contains a detailed listing of every item required for production. This goes beyond simply naming the components; it includes crucial information that enables accurate manufacturing and planning. Here's a breakdown of the essential elements:
1. Item Number/Part Number: Unique Identification
Every item in the BOM has a unique identifier, often a part number. This allows for unambiguous identification and tracking throughout the entire lifecycle of the product, from design to manufacturing and beyond. This is critical for managing inventory, ordering parts, and tracking down issues during production.
2. Item Description: Precise Specification
The description must be incredibly precise, leaving no room for ambiguity. This includes detailed specifications like dimensions, materials, tolerances, and any relevant standards or certifications. Vague descriptions can lead to errors in procurement and manufacturing. Consider the difference between “screw” and “M6 x 12mm stainless steel screw, Phillips head”. The latter is far more precise and prevents costly mistakes.
3. Quantity: The Exact Amount
This specifies the exact number of each item needed for one unit of the finished product. Accuracy here is paramount; errors can significantly impact costs and lead times. The quantity is often expressed as a "per-unit" quantity.
4. Unit of Measure: Consistent Measurement
Clearly stating the unit of measure (e.g., each, meter, kilogram, liter) is crucial for avoiding confusion. Consistency in units of measure is essential across the entire BOM to prevent errors in calculations and procurement.
5. Material: Composition and Properties
Specifying the material is essential for both quality control and cost management. This should include the material type (e.g., steel, aluminum, plastic), grade, and any relevant properties such as tensile strength or chemical resistance.
6. Cost: Accurate Pricing
Including the cost per unit of each item allows for accurate calculation of the total cost of goods sold (COGS). This information is critical for pricing the finished product and managing profitability. This cost can be either the direct cost or a standard cost based on historical data.
7. Supplier Information: Source and Contact
Identifying the supplier of each component is crucial for efficient procurement. This includes the supplier's name, contact information, and any relevant part numbers used by the supplier.
8. Lead Time: Delivery Timeframes
Knowing the lead time (the time it takes for a supplier to deliver an item) is essential for accurate production scheduling. This helps prevent delays due to late deliveries and ensures smooth production flow.
Beyond the Basics: Advanced BOM Features
While the core elements listed above form the foundation of any BOM, more advanced features can greatly enhance its functionality and usefulness.
9. Revision Control: Tracking Changes
Implementing a revision control system is crucial, especially for products undergoing frequent design changes. This allows for tracking changes made to the BOM over time, ensuring everyone works with the most up-to-date version. This prevents costly errors stemming from outdated information.
10. Multi-Level BOMs: Complex Assemblies
For complex products with multiple sub-assemblies, a multi-level BOM is essential. This organizes the components hierarchically, showing the relationships between parts and sub-assemblies. This provides a clear picture of the entire product structure.
11. Engineering Changes: Managing Modifications
A well-structured BOM allows for easy management of engineering changes (ECOs). This ensures that all necessary updates are made consistently across the entire BOM, preventing inconsistencies and errors.
12. Images and Drawings: Visual References
Including images or drawings of each component can significantly improve clarity and reduce ambiguity. Visual aids are invaluable in complex assemblies where textual descriptions alone may not suffice.
13. Specifications and Standards: Compliance and Quality
Referencing relevant specifications and industry standards ensures compliance and maintains quality control. This is especially important for products subject to regulatory requirements.
14. Manufacturing Location: Origin Tracking
For global supply chains, indicating the manufacturing location of each component can be crucial for tracking origin, complying with trade regulations, and managing logistics.
15. Custom Fields: Tailored Information
Many BOM systems allow the addition of custom fields to capture specific information relevant to a particular industry or company. This allows tailoring the BOM to the unique needs of a project or product.
Types of Bills of Materials
The structure and content of a BOM can vary depending on its intended use. Here are some common types:
-
Single-Level BOM: Lists only the top-level components of a product, without detailing sub-assemblies. This is suitable for simple products with few components.
-
Multi-Level BOM: A more complex structure that shows the hierarchical relationship between components and sub-assemblies, suitable for complex products.
-
Indented BOM: A multi-level BOM displayed in an indented format, clearly showing the hierarchical structure. The indentation visually represents the level of subassembly.
-
Summary BOM: Provides a summary of all components and materials, usually used for high-level planning and cost estimation.
-
Phantom BOM: Used for planning and costing of components that are assembled and disassembled during the manufacturing process but are not part of the finished product.
-
Engineering BOM: Used primarily for design and engineering purposes, often containing detailed specifications and tolerances.
-
Manufacturing BOM: Specifically tailored for the manufacturing process, containing information necessary for production scheduling and inventory management.
The Importance of an Accurate BOM
An accurate BOM is the cornerstone of efficient and profitable manufacturing. Its importance cannot be overstated:
-
Accurate Costing: A precise BOM ensures accurate cost calculations, allowing for informed pricing decisions and improved profitability.
-
Efficient Procurement: It facilitates efficient procurement by providing a comprehensive list of required components and their specifications.
-
Streamlined Production: The BOM ensures all necessary components are available when needed, optimizing the production process and minimizing downtime.
-
Improved Inventory Management: It helps manage inventory levels, preventing stockouts and reducing waste due to excess inventory.
-
Effective Quality Control: An accurate BOM helps ensure the quality of the finished product by specifying the correct components and materials.
-
Reduced Errors: By providing clear and concise information, the BOM minimizes errors in procurement, manufacturing, and assembly.
-
Enhanced Collaboration: It serves as a central repository of information, facilitating seamless collaboration between different teams involved in the product lifecycle.
-
Traceability and Accountability: The BOM allows for easy tracing of components and materials throughout the supply chain, enhancing accountability and facilitating product recalls if necessary.
Conclusion: The Recipe for Success
A Bill of Materials is more than just a list; it’s a dynamic document that underpins the entire product lifecycle. By incorporating the detailed information outlined above, a BOM evolves from a simple inventory list to a powerful tool for efficient production, cost management, and quality control. Understanding the intricacies of a BOM is essential for any organization involved in manufacturing, engineering, or product development, forming the vital "recipe" for successful product creation. Investing in a well-structured and managed BOM system translates directly to improved efficiency, reduced costs, and enhanced profitability.
Latest Posts
Latest Posts
-
Astro 7n Unit 3 Part 3
May 12, 2025
-
Which Of The Following Correctly Describes Foodborne Illness
May 12, 2025
-
Analyze The Theme Of Disillusionment In Fitzgeralds Winter Dreams
May 12, 2025
-
Ap Calculus Unit 1 Progress Check Mcq Part B
May 12, 2025
-
Injury To Cervical Vertebrae C3 C4 Is Particularly Problematic Because
May 12, 2025
Related Post
Thank you for visiting our website which covers about A Bill Of Materials Contains The Blank______. . We hope the information provided has been useful to you. Feel free to contact us if you have any questions or need further assistance. See you next time and don't miss to bookmark.