A Company Studied The Number Of Lost-time Accidents
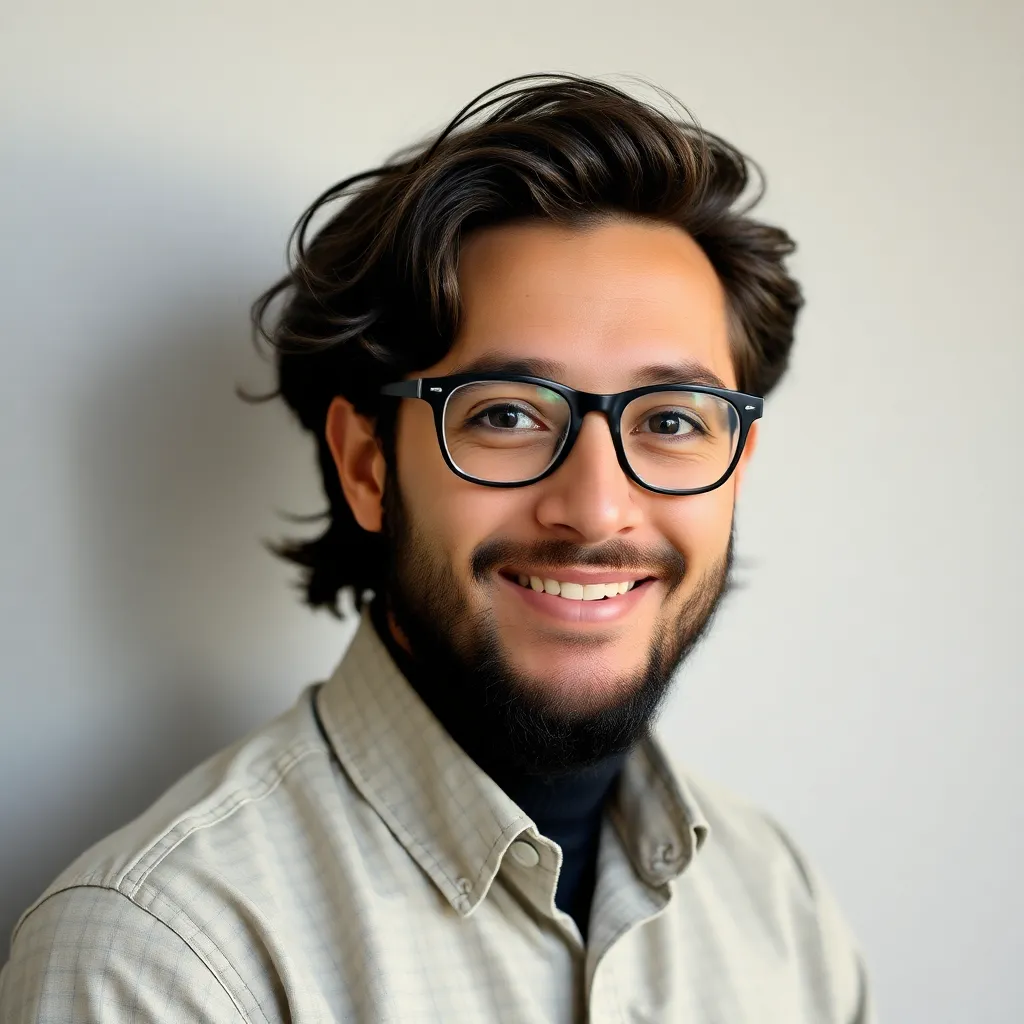
Onlines
May 07, 2025 · 7 min read
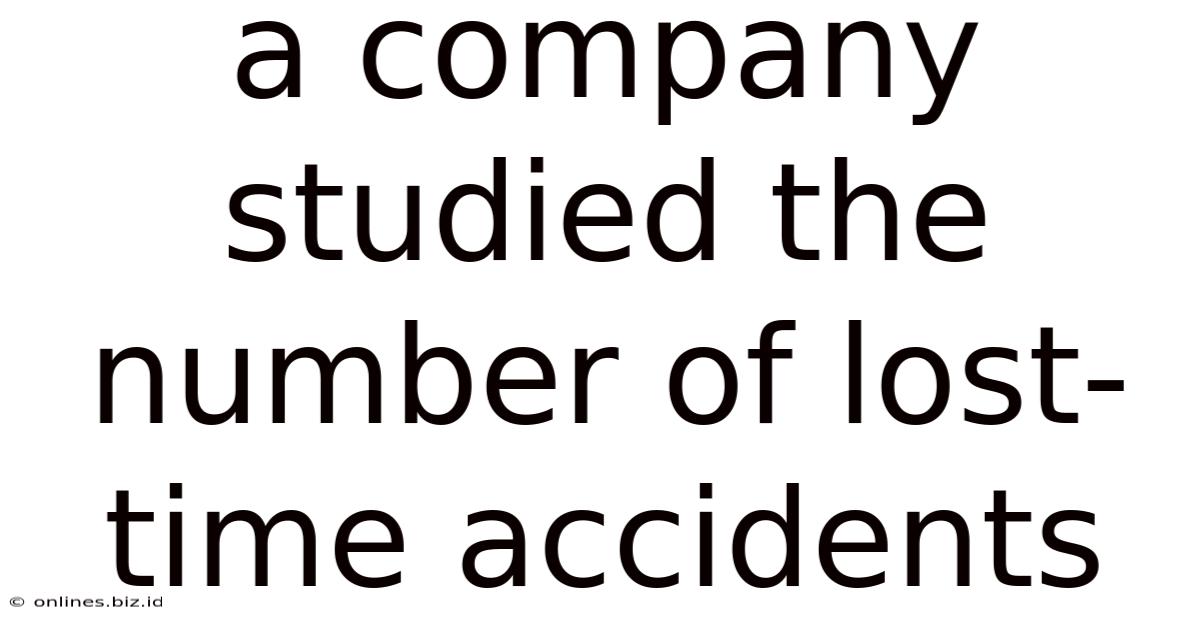
Table of Contents
A Company Studied the Number of Lost-Time Accidents: Unveiling Trends and Implementing Preventative Measures
The relentless pursuit of workplace safety is paramount for any successful organization. A significant indicator of a company's safety performance is the number of lost-time accidents (LTAs). These incidents, resulting in employee absences from work due to injury, carry substantial financial, operational, and ethical implications. This article delves deep into a hypothetical company's study of its LTAs, exploring the data analysis, identification of root causes, and the implementation of preventative measures. We'll examine best practices, highlight crucial safety metrics, and discuss the broader impact of proactive safety management.
Understanding Lost-Time Accidents (LTAs)
Before diving into the specifics of the company's study, it's crucial to define LTAs. A lost-time accident is any workplace incident that results in an employee being unable to perform their regular duties for at least one day beyond the day of the injury. This definition encompasses a wide range of incidents, from minor injuries requiring immediate medical attention to severe traumas necessitating extended periods of recovery. LTAs are not just about physical injuries; they also include illnesses directly related to the work environment.
The importance of accurately recording and analyzing LTAs cannot be overstated. They provide valuable insights into potential hazards and systemic weaknesses within an organization's safety program. A robust data collection system is the foundation for effective accident prevention.
The Company's Study: Data Collection and Analysis
Our hypothetical company, let's call it "Acme Industries," conducted a comprehensive study of its LTAs over a five-year period (2019-2023). This involved meticulous data collection, focusing on several key aspects:
Data Points Collected:
- Date and Time of Incident: Pinpointing when accidents occur can reveal patterns linked to specific work shifts, days of the week, or times of the year.
- Location of Incident: Identifying specific areas within the workplace where accidents are more frequent helps target preventative measures to those high-risk zones.
- Nature of Injury: Categorizing injuries (e.g., cuts, sprains, fractures, burns) helps understand the types of hazards present.
- Cause of Incident: This is a crucial element, often requiring detailed investigation. Causes can range from unsafe equipment to human error, inadequate training, or environmental factors.
- Employee Involved: Demographics (age, experience level, job role) can reveal trends related to specific employee groups.
- Direct Costs: This includes medical expenses, workers' compensation payments, and lost productivity.
- Indirect Costs: These are less obvious but equally important and can include investigation time, administrative costs, training, and potential legal fees.
Data Analysis Techniques:
Acme Industries used various analytical techniques to interpret the gathered data:
- Trend Analysis: Identifying increases or decreases in LTA frequency over time to pinpoint periods needing more attention.
- Root Cause Analysis (RCA): Techniques like the "5 Whys" were employed to delve deep into the underlying causes of each accident, going beyond the immediate event to understand the systemic issues.
- Statistical Analysis: Identifying correlations between different variables (e.g., age of employee and type of injury) to unearth hidden patterns.
- Data Visualization: Using charts and graphs to present the findings in a clear and easily understandable format, facilitating communication and action planning.
Key Findings and Root Cause Analysis
Acme Industries' study revealed some key findings:
- High Concentration of LTAs in the Manufacturing Department: A disproportionate number of accidents occurred in the manufacturing department, indicating a need for focused safety interventions in that specific area. Root Cause Analysis revealed inadequate machine guarding and insufficient training on the safe operation of machinery as major contributing factors.
- Increase in Musculoskeletal Disorders (MSDs): The study showed a rise in MSDs, such as back injuries and carpal tunnel syndrome. RCA indicated repetitive movements and improper lifting techniques as the main culprits. Ergonomic assessments and training programs were identified as necessary solutions.
- Lack of Consistent Use of Personal Protective Equipment (PPE): Many accidents could have been prevented or mitigated with proper PPE use. RCA highlighted poor communication and enforcement of PPE protocols as contributing factors. Improved training, better communication, and enhanced supervision were suggested.
- Seasonal Fluctuations: A noticeable increase in LTAs was observed during peak production seasons. RCA pointed to increased pressure and potential for rushed work practices during periods of high demand. Addressing this required better workforce planning and improved communication about safety during busy periods.
Implementing Preventative Measures
Based on the findings, Acme Industries implemented a multifaceted safety program focusing on several key areas:
1. Enhanced Training and Education:
- Comprehensive Safety Training: All employees received updated and more comprehensive safety training, emphasizing the correct use of machinery, safe lifting techniques, and the importance of PPE.
- Regular Refresher Courses: To ensure knowledge retention and address evolving safety standards, regular refresher courses were introduced.
- Interactive Training Modules: Engaging training methods, including simulations and interactive modules, were introduced to improve employee engagement and learning outcomes.
2. Improved Workplace Ergonomics:
- Ergonomic Assessments: Thorough ergonomic assessments were conducted in high-risk areas to identify and eliminate ergonomic hazards.
- Equipment Modifications: Necessary adjustments were made to equipment to improve its ergonomics and reduce the risk of MSDs.
- Job Redesign: Job tasks were redesigned to minimize repetitive motions and improve work posture.
3. Strengthened PPE Program:
- Improved Communication: Clearer communication of PPE policies and the importance of their correct usage was implemented.
- Enhanced Enforcement: Regular monitoring and supervision ensured consistent PPE use.
- Provision of High-Quality PPE: Employees were provided with high-quality, comfortable, and well-fitting PPE.
4. Enhanced Safety Procedures and Protocols:
- Improved Machine Guarding: Existing machinery was upgraded with enhanced safety guards, and regular inspections were implemented.
- Lockout/Tagout Procedures: Strict lockout/tagout procedures were enforced to prevent accidental equipment start-up during maintenance.
- Regular Safety Audits: Regular safety audits were conducted to identify potential hazards and assess the effectiveness of implemented safety measures.
5. Improved Communication and Collaboration:
- Open Communication Channels: Open communication channels were established to encourage employees to report near misses and potential hazards without fear of reprisal.
- Safety Committees: Employee safety committees were formed to provide a platform for collaborative problem-solving and proactive safety improvements.
- Regular Safety Meetings: Regular safety meetings were held to discuss safety incidents, lessons learned, and upcoming initiatives.
Measuring the Effectiveness of Preventative Measures
Acme Industries implemented key performance indicators (KPIs) to measure the effectiveness of its new safety initiatives:
- LTA Frequency Rate: This is the number of LTAs per 100 full-time employees. A reduction in this rate indicates improved safety performance.
- Days Away From Work (DAFW) Rate: This measures the number of days employees are away from work due to LTAs. A decrease signifies a positive trend.
- Lost Time Injury Frequency Rate (LTIFR): Similar to LTA frequency rate, but often used in specific industries.
- Total Recordable Incident Rate (TRIR): This includes all recordable injuries and illnesses, offering a broader view of workplace safety.
- Near Miss Reporting Rate: This measures the number of near misses reported, reflecting the effectiveness of employee reporting mechanisms and safety culture.
By regularly monitoring these KPIs, Acme Industries can track progress, identify areas needing further improvement, and demonstrate the effectiveness of its safety investment.
Long-Term Sustainability of Safety Initiatives
Sustaining improved safety performance requires ongoing commitment and continuous improvement. Acme Industries recognized that a one-time intervention is insufficient; rather, a continuous cycle of improvement is crucial. This includes:
- Regular Safety Training and Refresher Courses: Consistent reinforcement of safety procedures is key.
- Regular Safety Audits and Inspections: Regular checks identify potential hazards before they lead to accidents.
- Continuous Improvement Processes: Regular review and improvement of safety procedures are paramount.
- Investment in Technology: Leveraging technology for safety monitoring and data analysis.
- Strong Safety Culture: Cultivating a workplace culture where safety is a core value.
Conclusion: The Importance of Proactive Safety Management
The study conducted by Acme Industries underscores the critical importance of proactive safety management. By systematically collecting data, analyzing trends, identifying root causes, and implementing targeted preventative measures, companies can significantly reduce LTAs, fostering a safer and more productive work environment. The financial benefits, operational efficiencies, and enhanced ethical standing associated with a robust safety program far outweigh the initial investment. A proactive approach, built on continuous improvement and a strong safety culture, is the key to achieving long-term success in workplace safety. Remember, preventing accidents is not just a responsibility; it's an investment in the well-being of employees and the long-term success of the organization.
Latest Posts
Latest Posts
-
Which Of The Following Sentences Contains A Misplaced Modifier
May 08, 2025
-
Activity Guide Black And White Images
May 08, 2025
-
Actividad Formativa 6 Organismos Y Energia
May 08, 2025
-
Activity That Is Practiced Under The Water Spanish
May 08, 2025
-
Select The True Statement About Informative Comparison Contrast Essays
May 08, 2025
Related Post
Thank you for visiting our website which covers about A Company Studied The Number Of Lost-time Accidents . We hope the information provided has been useful to you. Feel free to contact us if you have any questions or need further assistance. See you next time and don't miss to bookmark.