A Company's Computers Monitor Assembly Lines And Equipment Using
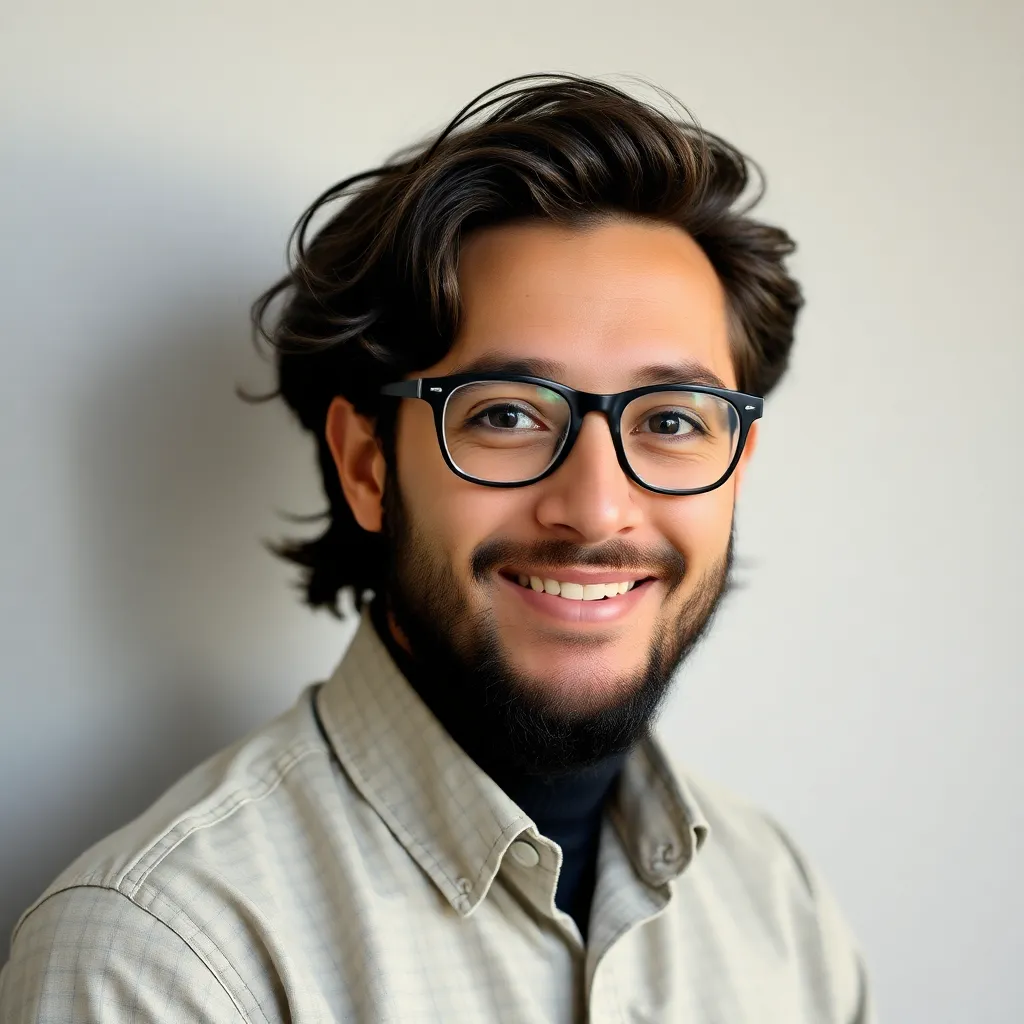
Onlines
May 06, 2025 · 6 min read

Table of Contents
Company's Computers Monitor Assembly Lines and Equipment Using AI and IoT: Revolutionizing Manufacturing Efficiency
The manufacturing landscape is undergoing a dramatic transformation, driven by the convergence of artificial intelligence (AI) and the Internet of Things (IoT). Companies are increasingly leveraging these technologies to monitor their assembly lines and equipment, achieving unprecedented levels of efficiency, productivity, and quality control. This article delves deep into how companies utilize computer-based systems to monitor their operations, examining the technologies involved, the benefits realized, and the challenges overcome.
The Rise of Smart Factories: AI and IoT Integration
The core of this revolution lies in the seamless integration of AI and IoT within manufacturing environments. Smart factories, as they are often called, utilize a network of interconnected sensors, machines, and software systems to collect and analyze vast amounts of data in real-time. This data provides crucial insights into every aspect of the production process, from individual machine performance to overall line efficiency.
IoT: The Foundation of Data Collection
The Internet of Things (IoT) forms the bedrock of this system. Sensors embedded in machines, assembly lines, and even individual components transmit data on various parameters, including:
- Temperature: Monitoring temperature fluctuations can prevent overheating, which can lead to equipment malfunction and production delays.
- Vibration: Unusual vibration patterns can indicate impending equipment failure, allowing for proactive maintenance.
- Pressure: Maintaining optimal pressure levels is crucial in many manufacturing processes. Sensors ensure consistent pressure, enhancing product quality.
- Power Consumption: Tracking energy usage helps identify inefficient machines and optimize energy management.
- Production Rate: Real-time monitoring of production rates allows for immediate detection of bottlenecks and adjustments to maintain optimal output.
- Product Defects: Sensors can detect defects during the manufacturing process, minimizing waste and enhancing quality control.
This data is then transmitted wirelessly to a central system for analysis and interpretation.
AI: Turning Data into Actionable Insights
The sheer volume of data generated by the IoT network would be overwhelming without the power of artificial intelligence. AI algorithms are employed to analyze this data, identifying patterns, predicting potential problems, and providing actionable insights. Specifically, AI plays a crucial role in:
- Predictive Maintenance: By analyzing historical data and identifying trends, AI can predict potential equipment failures, allowing for scheduled maintenance before breakdowns occur. This drastically reduces downtime and maintenance costs.
- Quality Control: AI-powered image recognition and analysis systems can detect defects that might be missed by human inspectors, ensuring consistent product quality.
- Process Optimization: AI algorithms can identify bottlenecks and inefficiencies in the production process, suggesting adjustments to optimize throughput and reduce waste.
- Real-time Anomaly Detection: AI can detect deviations from normal operating parameters, alerting operators to potential problems immediately. This allows for rapid intervention, minimizing disruptions.
- Supply Chain Management: By integrating data from various stages of the supply chain, AI can optimize inventory levels, predict demand fluctuations, and ensure timely delivery of materials.
Technologies Employed in Monitoring Assembly Lines and Equipment
Several key technologies are instrumental in implementing these smart factory solutions:
- Industrial IoT (IIoT) Platforms: These platforms provide the infrastructure for connecting and managing the vast network of sensors and devices within a manufacturing facility. They handle data collection, storage, and processing, providing a central hub for monitoring and control.
- Cloud Computing: Cloud-based solutions offer scalability and flexibility, allowing companies to adapt their monitoring systems to changing needs. The cloud provides the necessary computing power to process massive amounts of data generated by the IoT network.
- Machine Learning (ML): Machine learning algorithms are crucial for analyzing data, identifying patterns, and making predictions. ML models are trained on historical data to learn and improve their accuracy over time.
- Deep Learning (DL): Deep learning, a subfield of machine learning, is particularly effective in image and video analysis, allowing for automated defect detection and quality control.
- Computer Vision: Computer vision systems use cameras and AI algorithms to monitor the assembly line in real-time, detecting anomalies and ensuring proper assembly procedures are followed.
- Data Analytics and Business Intelligence (BI): Advanced data analytics tools provide insights into key performance indicators (KPIs), allowing companies to track progress, identify areas for improvement, and make data-driven decisions.
Benefits of Computer-Based Monitoring in Manufacturing
The implementation of computer-based monitoring systems yields numerous benefits for manufacturing companies:
- Increased Efficiency: By identifying and eliminating bottlenecks, optimizing processes, and preventing downtime, these systems significantly increase overall production efficiency.
- Reduced Costs: Predictive maintenance reduces repair costs and minimizes production downtime. Improved quality control minimizes waste and reduces the cost of rework.
- Enhanced Quality: Automated defect detection and real-time process monitoring ensure consistent product quality, enhancing customer satisfaction and brand reputation.
- Improved Safety: By monitoring equipment conditions and detecting potential hazards, these systems contribute to a safer working environment for employees.
- Data-Driven Decision Making: Access to real-time data and actionable insights empowers companies to make informed decisions based on factual data rather than intuition.
- Greater Agility and Flexibility: Smart factories are more adaptable to changing market demands and can quickly adjust production to meet fluctuating customer needs.
- Competitive Advantage: Companies that successfully leverage AI and IoT gain a significant competitive advantage in terms of efficiency, cost, and quality.
Challenges in Implementing Computer-Based Monitoring Systems
Despite the numerous benefits, implementing these systems presents certain challenges:
- High Initial Investment: The cost of implementing IoT sensors, AI software, and the necessary infrastructure can be substantial.
- Data Security and Privacy: Protecting sensitive data from unauthorized access and ensuring compliance with data privacy regulations is crucial.
- Integration Complexity: Integrating various systems and technologies can be complex and require specialized expertise.
- Data Analysis and Interpretation: Analyzing vast amounts of data and extracting meaningful insights requires skilled data scientists and analysts.
- Skills Gap: A shortage of skilled professionals with expertise in AI, IoT, and data analytics can hinder implementation efforts.
- Legacy Systems: Integrating new technologies with existing legacy systems can be challenging and require significant upgrades or replacements.
- Change Management: Successfully implementing these systems requires effective change management strategies to ensure buy-in from employees and overcome resistance to change.
The Future of Computer-Based Monitoring in Manufacturing
The future of computer-based monitoring in manufacturing is bright. Advancements in AI, IoT, and related technologies are continually enhancing the capabilities of these systems. We can expect to see:
- Increased Automation: Further automation of processes, leading to even higher efficiency and reduced labor costs.
- Enhanced Predictive Capabilities: More accurate and reliable predictive maintenance models, minimizing downtime and maximizing equipment lifespan.
- Advanced Analytics: More sophisticated data analytics tools will provide deeper insights into production processes, leading to further optimization.
- Greater Integration: Seamless integration of various systems across the entire supply chain, improving coordination and efficiency.
- Digital Twins: The use of digital twins, virtual representations of physical assets, will allow for advanced simulations and optimization strategies.
- Edge Computing: Processing data closer to the source (at the "edge" of the network) will reduce latency and improve real-time responsiveness.
- Blockchain Technology: Blockchain can enhance data security and transparency across the supply chain, improving traceability and accountability.
The integration of AI and IoT in manufacturing is not merely a technological advancement; it's a fundamental shift in how companies operate. Companies that embrace these technologies will be best positioned to thrive in the increasingly competitive global marketplace. By embracing innovation and overcoming the challenges, manufacturers can unlock unprecedented levels of efficiency, productivity, and profitability, paving the way for a future of smarter, more sustainable, and highly efficient manufacturing processes.
Latest Posts
Latest Posts
-
Draw The Bridged Bromonium Ion That Is Formed
May 06, 2025
-
Which Of The Following Currencies Are Involved In Causing Favorable
May 06, 2025
-
Which Of The Following Sentences Contains A Cliche
May 06, 2025
-
Identify The Bones In This Random Arrangement
May 06, 2025
-
Predict How Unfavorable Abiotic And Biotic Factors Affect A Species
May 06, 2025
Related Post
Thank you for visiting our website which covers about A Company's Computers Monitor Assembly Lines And Equipment Using . We hope the information provided has been useful to you. Feel free to contact us if you have any questions or need further assistance. See you next time and don't miss to bookmark.