A Company's Computers Monitor Assembly Lines And Equipment With
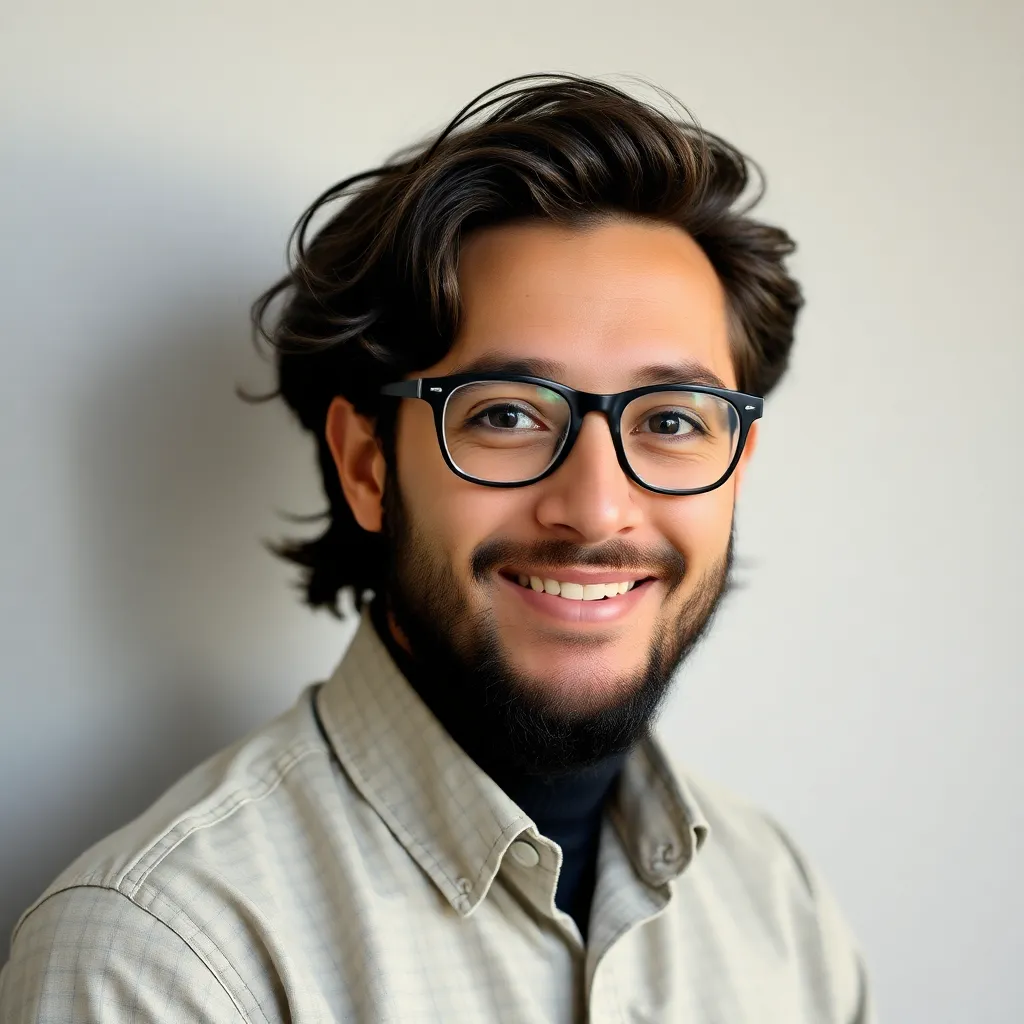
Onlines
May 11, 2025 · 6 min read
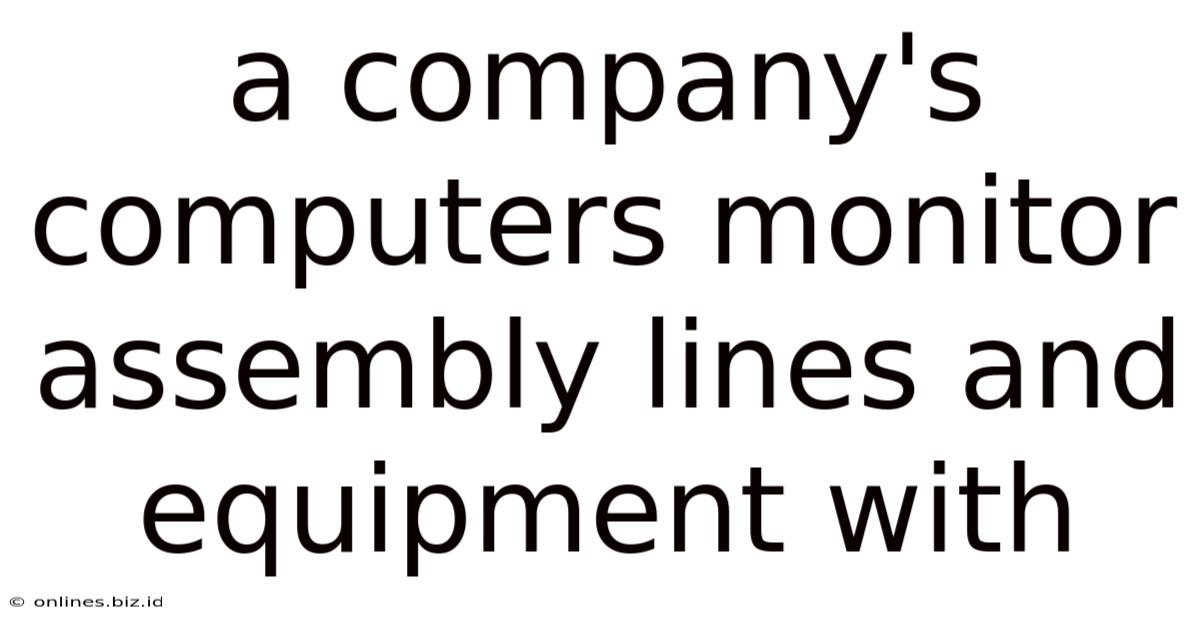
Table of Contents
Company's Computers Monitor Assembly Lines and Equipment with AI-Powered Predictive Maintenance
The modern manufacturing landscape is rapidly evolving, driven by advancements in technology and a relentless pursuit of efficiency. At the heart of this transformation lies the integration of sophisticated computer systems that monitor assembly lines and equipment, providing real-time insights and predictive capabilities that optimize production and minimize downtime. This article delves into the multifaceted role of computers in modern manufacturing, exploring the technologies employed, the benefits derived, and the future implications for companies embracing this transformative approach.
The Rise of Computerized Monitoring in Manufacturing
For decades, manufacturing relied heavily on manual monitoring and reactive maintenance. This approach often resulted in unexpected equipment failures, costly repairs, production delays, and compromised product quality. However, the advent of powerful computers and sophisticated software has revolutionized this paradigm. Companies now leverage computer systems to monitor various aspects of their operations, including:
Real-Time Data Acquisition and Analysis
Modern systems utilize a network of sensors and data acquisition devices strategically placed throughout the assembly line and equipment. These sensors collect a vast array of data, including:
- Machine performance: Speed, temperature, vibration, pressure, and power consumption.
- Environmental conditions: Temperature, humidity, and air quality.
- Product quality: Dimensions, weight, and other relevant parameters.
- Operator performance: Production rates, error rates, and downtime.
This data is then transmitted to a central computer system for analysis. Advanced algorithms process this information, identifying patterns and anomalies that indicate potential problems. This real-time monitoring allows for immediate intervention, preventing minor issues from escalating into major disruptions.
Predictive Maintenance: Preventing Problems Before They Occur
One of the most significant advancements in computerized monitoring is predictive maintenance. Instead of relying on scheduled maintenance intervals, predictive maintenance uses data analysis to anticipate equipment failures. By identifying subtle changes in machine performance, the system can predict when a component is likely to fail, allowing for proactive maintenance before it causes a breakdown. This approach offers numerous advantages:
- Reduced downtime: Proactive maintenance minimizes unplanned downtime, keeping production lines running smoothly.
- Lower maintenance costs: By addressing issues before they become major problems, companies save on costly repairs and replacements.
- Improved product quality: Consistent machine performance ensures the production of high-quality products.
- Increased efficiency: Optimized maintenance schedules maximize production output and minimize waste.
Predictive maintenance algorithms utilize sophisticated machine learning techniques to analyze historical data and identify patterns that correlate with equipment failures. These algorithms can forecast the remaining useful life of components, providing valuable insights for scheduling maintenance activities.
AI and Machine Learning in Predictive Maintenance
Artificial intelligence (AI) and machine learning (ML) are playing an increasingly crucial role in predictive maintenance. These technologies enable the development of more accurate and insightful predictive models. AI algorithms can:
- Identify complex patterns: AI can detect subtle anomalies that might be missed by traditional methods.
- Adapt to changing conditions: AI models can learn and adapt to changes in the manufacturing environment, improving the accuracy of predictions.
- Optimize maintenance schedules: AI can help determine the optimal time to perform maintenance, balancing the cost of downtime with the risk of equipment failure.
The integration of AI and ML is transforming predictive maintenance from a reactive approach to a proactive, data-driven strategy.
The Benefits of Computerized Monitoring for Companies
The implementation of computer systems for monitoring assembly lines and equipment offers a wide range of benefits for companies across various industries:
Enhanced Efficiency and Productivity
Real-time monitoring and predictive maintenance contribute significantly to increased efficiency and productivity. By minimizing downtime and optimizing maintenance schedules, companies can maximize their production output and meet demanding deadlines.
Improved Product Quality
Consistent machine performance and proactive maintenance contribute to improved product quality. By identifying and addressing potential issues early on, companies can minimize defects and ensure consistent product quality.
Reduced Costs
The cost savings associated with computerized monitoring are substantial. Reduced downtime, lower maintenance costs, and improved product quality contribute to significant cost reductions.
Enhanced Safety
Computer systems can also play a role in improving workplace safety. By identifying potential hazards and predicting equipment failures, companies can take proactive measures to prevent accidents and injuries.
Data-Driven Decision Making
The vast amount of data collected by computer systems provides valuable insights for data-driven decision making. Companies can use this data to optimize their processes, improve efficiency, and make informed strategic decisions.
Implementing Computerized Monitoring Systems: Challenges and Considerations
While the benefits of computerized monitoring are substantial, implementing such systems presents several challenges:
Data Integration and Management
Integrating data from various sources can be complex. Companies need to ensure that their systems can handle the large volume of data generated by sensors and other devices. Effective data management strategies are crucial for ensuring data accuracy and accessibility.
System Integration and Compatibility
Integrating new monitoring systems with existing IT infrastructure can be challenging. Companies need to ensure compatibility between different systems and platforms.
Skilled Workforce
Implementing and maintaining computerized monitoring systems requires a skilled workforce. Companies need to invest in training and development to ensure that their employees have the necessary expertise.
Cost of Implementation
Implementing computerized monitoring systems can be expensive. Companies need to carefully evaluate the costs associated with hardware, software, implementation, and training.
Data Security and Privacy
The collection and storage of sensitive data raises concerns about data security and privacy. Companies need to implement robust security measures to protect their data from unauthorized access and cyber threats.
The Future of Computerized Monitoring in Manufacturing
The future of computerized monitoring in manufacturing is bright. Advancements in artificial intelligence, machine learning, and the Internet of Things (IoT) will continue to drive innovation in this field. We can expect to see:
- More sophisticated predictive models: AI and ML will enable the development of more accurate and insightful predictive models.
- Increased automation: Automation will play a larger role in maintenance and repair activities.
- Greater integration of data: Data from various sources will be integrated to provide a more comprehensive view of the manufacturing process.
- Enhanced cybersecurity: Robust cybersecurity measures will be crucial to protect sensitive data.
- Wider adoption of digital twins: Digital twins will enable companies to simulate and optimize their manufacturing processes.
The integration of computer systems for monitoring assembly lines and equipment is transforming the manufacturing landscape, driving efficiency, improving product quality, and reducing costs. Companies that embrace this transformative technology will be well-positioned to compete in the increasingly demanding global marketplace. The continuous evolution of AI and related technologies promises even greater advancements in the years to come, further enhancing the capabilities and benefits of computerized monitoring in manufacturing. This data-driven approach to manufacturing is not simply a trend, but a fundamental shift towards a more efficient, resilient, and profitable future for industries worldwide. The companies that adapt and innovate in this space will be the ones that thrive in the coming decades.
Latest Posts
Latest Posts
-
An Ignition Switch Uses A Switch
May 11, 2025
-
Una Estudiante Desea Hablar Con Su Profesora De Biologia
May 11, 2025
-
For Which Writing Prompt Would You Use An Explanatory Thesis
May 11, 2025
-
Old Lithosphere Is Destroyed In Association With
May 11, 2025
-
Qualitative Energy Storage And Conservation With Bar Graphs
May 11, 2025
Related Post
Thank you for visiting our website which covers about A Company's Computers Monitor Assembly Lines And Equipment With . We hope the information provided has been useful to you. Feel free to contact us if you have any questions or need further assistance. See you next time and don't miss to bookmark.