A Company's Distribution And Warehouse Expenses
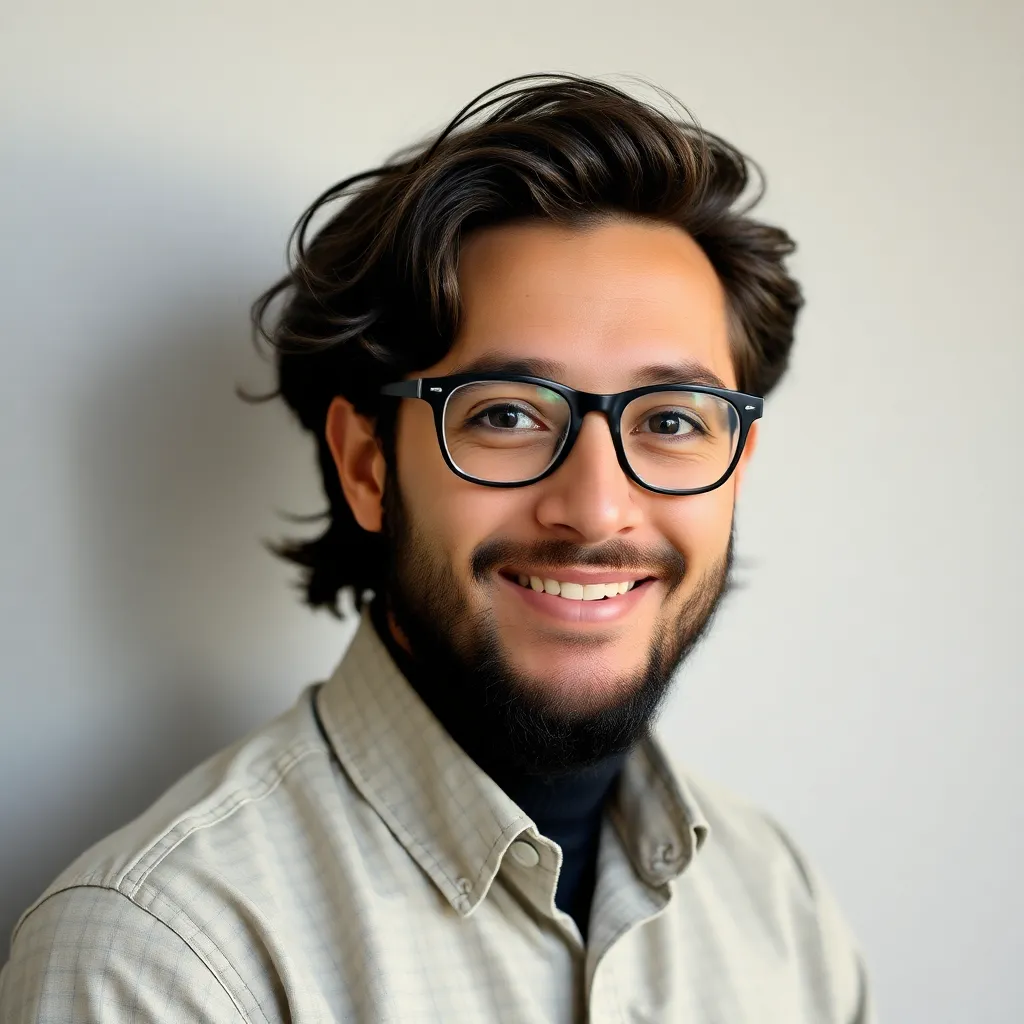
Onlines
Apr 18, 2025 · 6 min read

Table of Contents
A Deep Dive into Company Distribution and Warehouse Expenses: Optimizing for Profitability
Understanding and managing distribution and warehouse expenses is crucial for any company's profitability. These costs, often overlooked in initial business planning, can significantly impact your bottom line if not carefully controlled. This comprehensive guide delves into the intricacies of these expenses, providing strategies for optimization and highlighting key performance indicators (KPIs) to monitor.
Understanding the Components of Distribution and Warehouse Expenses
Distribution and warehouse expenses are multifaceted, encompassing various direct and indirect costs. Let's break them down into key categories:
Warehouse Expenses: The Costs of Storage and Handling
-
Rent and Utilities: This is a significant fixed cost, encompassing the lease or purchase price of your warehouse space, along with utilities like electricity, heating, cooling, and water. Strategic location selection can significantly impact these expenses. Consider factors like proximity to transportation hubs and labor availability.
-
Labor Costs: Warehouse operations require significant manpower. This includes salaries and benefits for warehouse workers, supervisors, and managers. Optimizing labor through efficient workflows and technology implementation is critical to controlling these costs.
-
Equipment and Maintenance: Warehouse equipment is essential for efficient operations. This includes forklifts, conveyor belts, pallet jacks, and shelving units. Regular maintenance is vital to prevent costly breakdowns and ensure operational efficiency. Consider leasing equipment as an alternative to outright purchase, especially for less frequently used machinery.
-
Inventory Costs: This encompasses the cost of goods stored in the warehouse, including the cost of the goods themselves, insurance, and potential obsolescence or spoilage. Efficient inventory management systems, including first-in, first-out (FIFO) and just-in-time (JIT) strategies, can help minimize inventory holding costs.
-
Insurance: Warehouse insurance is essential to protect against potential losses due to fire, theft, or damage. The cost will vary depending on the value of your inventory and the level of risk.
-
Security: Ensuring the safety and security of your warehouse and inventory is paramount. Costs associated with security systems, personnel, and monitoring contribute to overall warehouse expenses.
-
Technology: Investing in warehouse management systems (WMS), barcode scanners, and other technologies can significantly improve efficiency and reduce operational costs. The initial investment can be substantial, but the long-term ROI can be considerable.
-
Depreciation: Over time, the value of warehouse equipment and infrastructure depreciates. Accurately accounting for depreciation is important for financial reporting and tax purposes.
Distribution Expenses: The Costs of Getting Goods to Market
-
Transportation Costs: This is often the largest component of distribution expenses. It includes freight costs, fuel surcharges, and other transportation-related fees. Optimizing transportation routes, negotiating favorable rates with carriers, and utilizing efficient transportation modes (e.g., rail, trucking, air) are key cost-saving strategies.
-
Packaging and Handling: Packaging materials, such as boxes, tape, and fillers, are necessary to protect goods during transit. Careful selection of packaging materials can minimize costs without compromising product protection.
-
Shipping and Handling Fees: These include fees charged by carriers for pickup, delivery, and other services. Negotiating favorable rates and consolidating shipments can help reduce these costs.
-
Customs Duties and Taxes: For international shipments, customs duties and taxes can add significantly to distribution expenses. Careful planning and understanding of import regulations are vital to minimize these costs.
-
Insurance: Transportation insurance protects goods during transit against loss or damage. The cost varies depending on the value of the goods and the mode of transportation.
Optimizing Distribution and Warehouse Expenses: Strategies for Cost Reduction
Effective management of distribution and warehouse expenses requires a multifaceted approach that combines strategic planning, operational efficiency, and technological advancements. Here are some proven strategies:
1. Optimizing Warehouse Operations
-
Efficient Space Utilization: Maximize storage capacity by implementing effective shelving systems, optimizing layout, and minimizing wasted space.
-
Improved Inventory Management: Implement robust inventory management systems to minimize stockouts, reduce waste due to obsolescence or spoilage, and streamline order fulfillment.
-
Cross-Docking: This strategy involves unloading goods from incoming shipments and loading them directly onto outgoing shipments, minimizing storage time and related costs.
-
Automation: Utilize automated systems for tasks such as picking, packing, and sorting to increase efficiency and reduce labor costs. Consider technologies like automated guided vehicles (AGVs) and robotic process automation (RPA).
-
Lean Principles: Apply Lean manufacturing principles to identify and eliminate waste in warehouse operations. This involves continuous improvement and optimization of processes.
2. Streamlining Distribution Processes
-
Negotiate Favorable Transportation Rates: Establish strong relationships with carriers and negotiate favorable rates for shipping. Consider consolidating shipments to reduce per-unit costs.
-
Route Optimization: Utilize route optimization software to plan efficient delivery routes and minimize fuel consumption.
-
Multimodal Transportation: Combine different transportation modes (e.g., rail and trucking) to take advantage of the strengths of each and optimize costs.
-
Strategic Location Selection: Choose warehouse locations that are strategically positioned to minimize transportation costs and improve delivery times. Consider proximity to major transportation hubs and customer bases.
-
Effective Packaging Strategies: Utilize appropriate packaging materials to minimize damage and reduce waste. Optimize packaging size and weight to reduce shipping costs.
3. Leveraging Technology
-
Warehouse Management Systems (WMS): Implement a WMS to streamline warehouse operations, manage inventory effectively, and track shipments.
-
Transportation Management Systems (TMS): Utilize a TMS to optimize transportation routes, manage carrier relationships, and track shipments.
-
Data Analytics: Use data analytics to identify trends and patterns in distribution and warehouse expenses, allowing for proactive cost reduction measures.
-
Predictive Modeling: Utilize predictive modeling techniques to forecast demand and optimize inventory levels, reducing holding costs.
4. Regular Monitoring and Evaluation
-
Key Performance Indicators (KPIs): Track key performance indicators such as warehouse operating costs per unit, order fulfillment rate, inventory turnover rate, and transportation costs per unit. Regular monitoring of these KPIs allows for timely intervention and adjustments.
-
Cost Analysis: Conduct regular cost analysis to identify areas where expenses can be reduced. This involves analyzing historical data and identifying potential cost-saving opportunities.
-
Continuous Improvement: Foster a culture of continuous improvement within the organization, constantly seeking ways to improve efficiency and reduce costs.
The Impact of Distribution and Warehouse Expenses on Profitability
High distribution and warehouse expenses directly impact a company's profitability by reducing its net income. These costs can eat into profit margins, hindering growth and competitiveness. Effective management of these expenses is crucial for maintaining profitability and ensuring the long-term success of the business. Understanding the specific cost drivers within your business and implementing appropriate optimization strategies can dramatically improve your bottom line.
Conclusion: A Proactive Approach to Cost Management
Effective management of distribution and warehouse expenses is not merely about cost reduction; it’s about strategic optimization to improve efficiency, enhance customer service, and ultimately drive profitability. By implementing the strategies outlined above and consistently monitoring key performance indicators, companies can gain a competitive advantage in the marketplace. Remember, a proactive and data-driven approach to cost management is essential for long-term success in today's dynamic business environment. Continuous improvement, leveraging technology, and a focus on efficient operations are key to minimizing these expenses and maximizing profitability. This requires ongoing monitoring, analysis, and adaptation to changing business needs and market conditions. The investment in efficient systems and processes will ultimately pay off in the form of increased profitability and sustainable growth.
Latest Posts
Latest Posts
-
A Patient Is Entered Into The Patient List
Apr 19, 2025
-
Out Of The Silent Planet Synopsis
Apr 19, 2025
-
The Cartoon Above Is A Commentary On Late Nineteenth Century
Apr 19, 2025
-
Elmer The Owner Of An Auto Service Station
Apr 19, 2025
-
Nurse Alex Recommends That Ben Come To The Clinic
Apr 19, 2025
Related Post
Thank you for visiting our website which covers about A Company's Distribution And Warehouse Expenses . We hope the information provided has been useful to you. Feel free to contact us if you have any questions or need further assistance. See you next time and don't miss to bookmark.