A Flexible Sealing Element Subject To Motion Is A
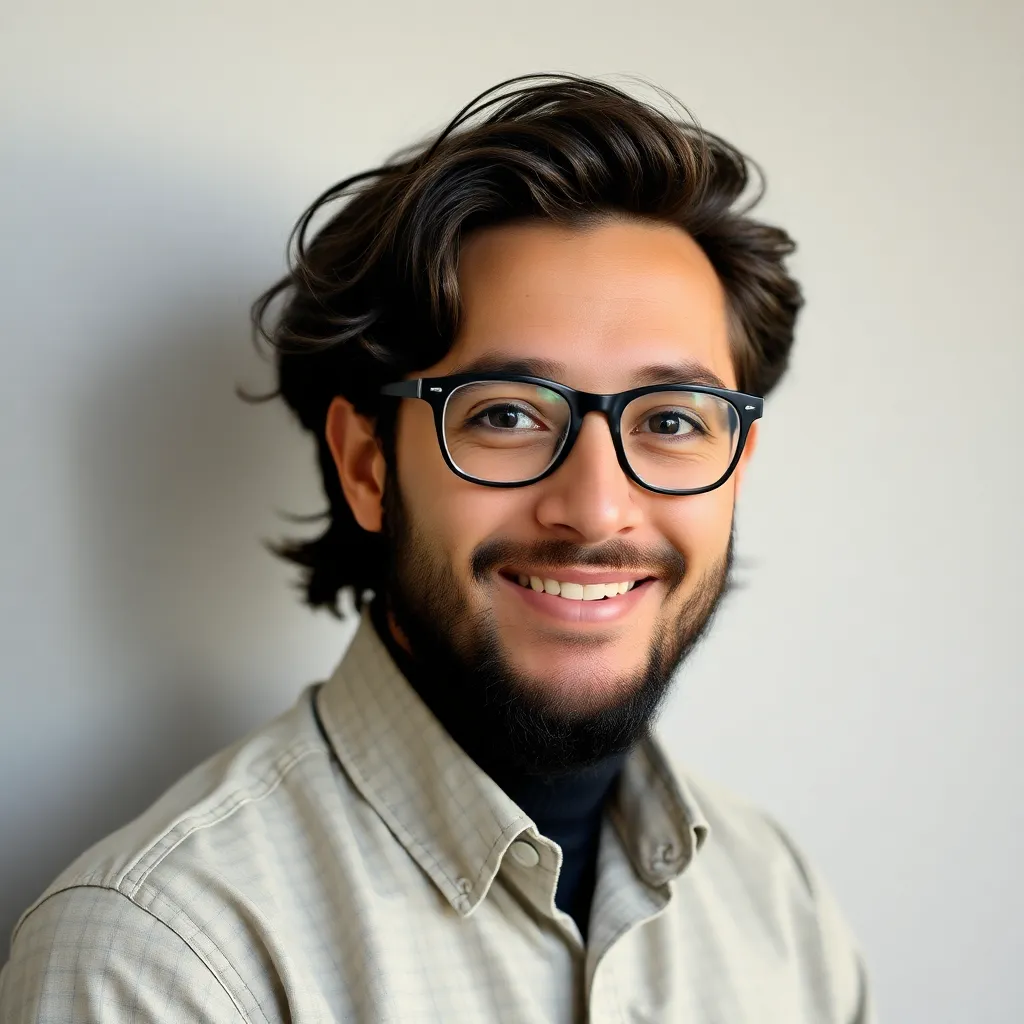
Onlines
May 10, 2025 · 6 min read
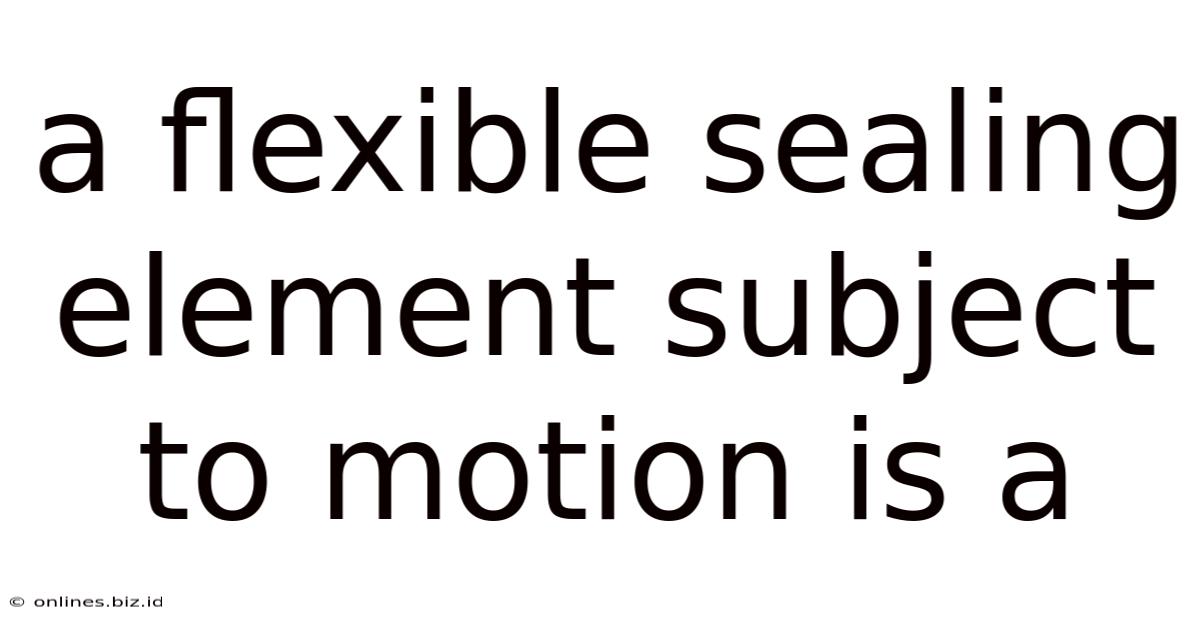
Table of Contents
A Flexible Sealing Element Subject to Motion Is a… Dynamic Challenge!
A flexible sealing element subject to motion is a dynamic challenge requiring careful consideration of material properties, design, and operating conditions. This isn't just about preventing leaks; it's about ensuring the longevity and efficiency of machinery, minimizing downtime, and maintaining safety. This comprehensive guide will delve into the complexities of these dynamic seals, exploring their various types, applications, and the crucial factors influencing their performance.
Understanding the Dynamic Sealing Environment
Before diving into specific seal types, it's essential to understand the environment these seals must endure. Movement introduces friction, wear, and the potential for leakage. The type of motion (reciprocating, rotary, oscillating) significantly impacts seal selection.
Factors Affecting Seal Choice:
-
Type of Motion: Reciprocating seals handle back-and-forth movement, rotary seals manage continuous rotation, and oscillating seals accommodate cyclical swinging motion. Each requires a different design to manage the specific stresses.
-
Operating Pressure: Higher pressures demand seals with greater strength and resistance to deformation. The pressure differential across the seal interface is a critical factor determining seal design and material.
-
Temperature Range: Extreme temperatures can cause material degradation or embrittlement, impacting seal performance. Temperature fluctuations should be considered when choosing seal materials.
-
Fluid Compatibility: The seal material must be chemically compatible with the fluid being contained to prevent swelling, degradation, or chemical attack. This is paramount to ensure the integrity of the seal and prevent contamination.
-
Speed of Movement: Higher speeds generate more heat and friction, demanding seals with enhanced wear resistance and heat dissipation capabilities.
-
Shaft Surface Finish: A rough shaft surface can damage the seal, leading to premature failure. Smooth shaft surfaces are essential for extending seal life.
Types of Flexible Sealing Elements Subject to Motion
Many different types of flexible seals exist, each optimized for particular applications and operating conditions. The choice depends heavily on the specific requirements of the system.
1. O-Rings: The Workhorse of Sealing
O-rings are ubiquitous, simple, and relatively inexpensive. Their circular shape creates a radial seal when compressed within a groove. While effective for static and low-speed dynamic applications, their limitations become apparent at high pressures, speeds, or temperatures. Extrusion, a phenomenon where the seal is squeezed out from the groove under pressure, is a common concern.
Suitable Applications: Low-pressure hydraulic systems, pneumatic applications, general-purpose sealing.
2. Lip Seals (Radial Shaft Seals): Precision Engineering for Rotary Applications
Lip seals, also known as radial shaft seals, are predominantly used in rotary applications. They feature a flexible lip that contacts the shaft, creating a sealing barrier. Their design incorporates spring elements to maintain consistent contact pressure, and they often include a secondary sealing element to prevent leakage.
Suitable Applications: Automotive transmissions, pumps, engines, compressors.
3. U-Cups: Versatile and Robust for Reciprocating Motion
U-cups are commonly employed in hydraulic and pneumatic cylinders for reciprocating motion. Their U-shaped design allows them to effectively seal against the rod or piston, accommodating both static and dynamic conditions. Material selection is crucial, as repeated compression and expansion can lead to premature wear.
Suitable Applications: Hydraulic cylinders, pneumatic actuators, linear motion systems.
4. Piston Seals: Designed for Axial Movement
Piston seals are specialized seals designed for axial movement within cylinders. They can be designed in various profiles, including cup-shaped, ring-shaped, and custom designs, to suit specific applications. Their main function is to create a pressure-tight seal between the piston and the cylinder wall.
Suitable Applications: Hydraulic cylinders, pneumatic cylinders, large-bore applications.
5. Rotary Shaft Seals: A Diverse Family for Rotating Applications
Rotary shaft seals encompass a wide variety of designs, including mechanical seals, face seals, and labyrinth seals. Each type is designed to handle the specific challenges posed by rotary motion, such as high speeds, high pressures, and harsh operating conditions. Mechanical seals are particularly robust and suited for high-pressure and high-speed applications.
Suitable Applications: Pumps, compressors, mixers, agitators.
6. Hydraulic Seals: Optimized for Fluid Power Systems
Hydraulic seals are designed to withstand the high pressures and harsh environments typical of hydraulic systems. They are often made from specialized elastomers or other materials that offer excellent resistance to hydraulic fluids. Their design must account for fluid compatibility and prevent extrusion under high pressure.
Suitable Applications: Hydraulic pumps, hydraulic motors, hydraulic actuators, hydraulic presses.
Material Selection: The Key to Seal Longevity
The material of a flexible sealing element is critical to its success. Various factors need careful consideration:
-
Elastomers: Materials like nitrile rubber (NBR), silicone rubber (VMQ), ethylene propylene rubber (EPDM), and fluoroelastomers (FKM) are frequently used. Each offers a unique set of properties regarding temperature resistance, chemical compatibility, and wear resistance.
-
Polymers: Polyurethane and PTFE are examples of polymers used in dynamic seals, offering good wear resistance and chemical compatibility in certain applications.
-
Metal-based seals: For high-temperature or highly aggressive environments, metal-based seals or those with metallic components might be needed.
The selection process must balance these material properties with the specific operational demands. For instance, a seal in a high-temperature application would require a material with a high heat deflection temperature, while one in a corrosive environment would require excellent chemical resistance.
Designing for Success: Key Considerations
Effective seal design goes beyond selecting the right material. Proper design minimizes friction, prevents extrusion, and ensures consistent sealing across the operating range. Several critical aspects must be addressed:
-
Seal Groove Design: The dimensions of the seal groove must be carefully designed to ensure proper seal compression without excessive stress. The groove should prevent the seal from extruding under pressure.
-
Surface Finish: The shaft or housing surface should have a smooth finish to minimize wear and tear on the seal. Rough surfaces can quickly damage the seal, leading to leakage.
-
Seal Compression: Proper seal compression is crucial for achieving a tight seal. Insufficient compression can lead to leakage, while excessive compression can cause premature wear and seal failure.
-
Installation Techniques: Proper installation procedures are essential to avoid damaging the seal during installation. Careful handling and use of appropriate lubricants are crucial for maintaining seal integrity.
-
Maintenance Considerations: Regular inspection and maintenance are key to ensuring the longevity of seals. This includes monitoring for leaks, wear, and other signs of seal deterioration.
Troubleshooting Common Seal Problems
Despite careful design and selection, seal failures can occur. Understanding common problems and their causes is crucial for effective troubleshooting.
-
Leakage: Leakage may be due to improper seal compression, wear and tear, material incompatibility, or improper installation. Investigating the source of the leak is critical.
-
Extrusion: Extrusion, the squeezing out of the seal from its groove, can occur under high pressure. Selecting a more resistant material or redesigning the seal groove might be necessary.
-
Wear and Tear: Wear and tear are inevitable over time. Regular inspection and replacement according to a planned maintenance schedule can prevent catastrophic failure.
-
Seal Damage: Improper installation, foreign debris, or rough shaft surfaces can lead to seal damage. Careful handling and installation procedures are essential.
Conclusion: A Holistic Approach to Dynamic Sealing
A flexible sealing element subject to motion represents a multifaceted engineering challenge. Success requires a holistic approach, considering every factor influencing seal performance – from material selection and design to installation and maintenance. By carefully understanding the dynamic sealing environment and utilizing appropriate technologies, engineers can ensure the effective and reliable operation of machinery, preventing leaks, minimizing downtime, and ensuring the safety of personnel. Continuous monitoring, proactive maintenance, and a deep understanding of seal technology are key to preventing costly seal failures and maintaining efficient industrial processes.
Latest Posts
Latest Posts
-
Unit 1 The Healthcare Setting Crossword Answers
May 10, 2025
-
Crafting A Deliberate Strategy Involves Developing Strategy Elements That
May 10, 2025
-
General Purpose Applications Include All Of The Following Except
May 10, 2025
-
Suppose The Government Imposes A Tax Of P
May 10, 2025
-
Raising Your Credit Standing Is An Advantage Of Equity Capital
May 10, 2025
Related Post
Thank you for visiting our website which covers about A Flexible Sealing Element Subject To Motion Is A . We hope the information provided has been useful to you. Feel free to contact us if you have any questions or need further assistance. See you next time and don't miss to bookmark.