A Manifold Pressure Gauge Is Designed To
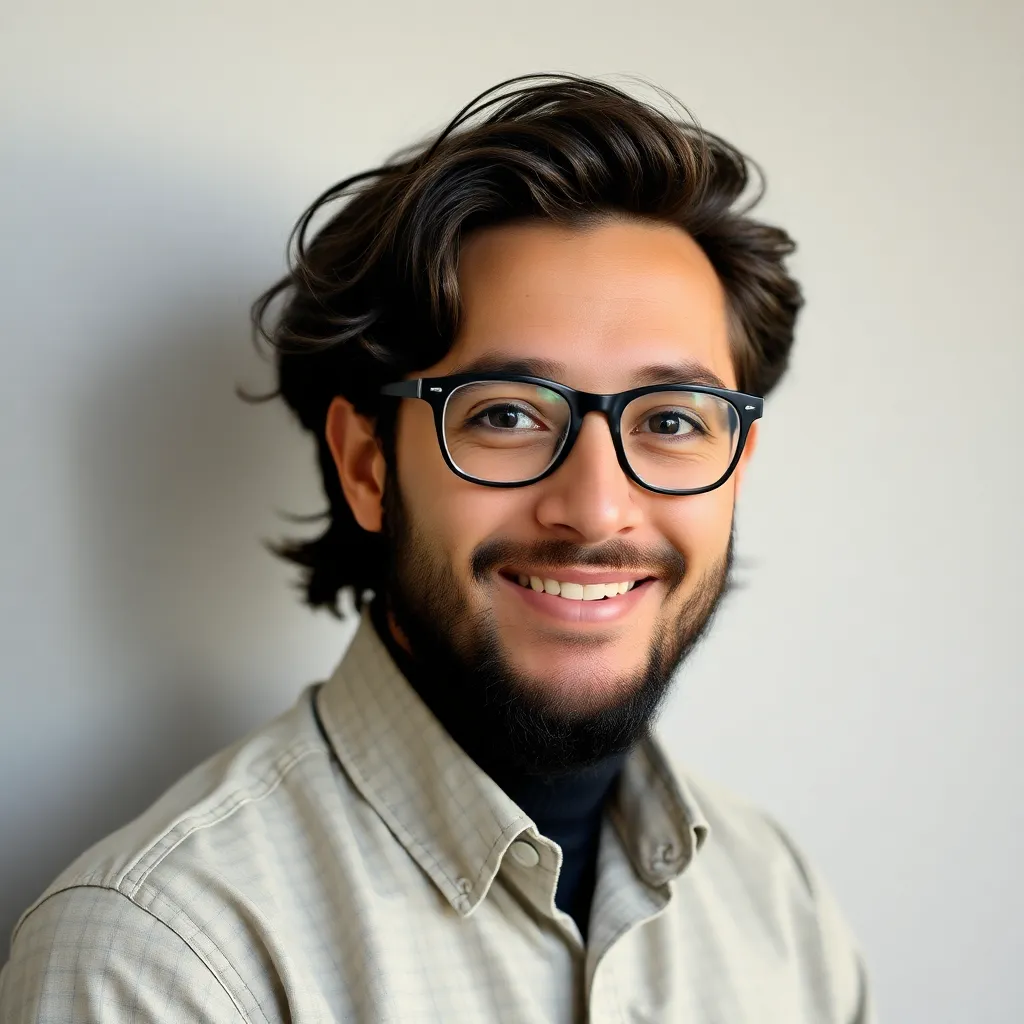
Onlines
Apr 27, 2025 · 6 min read

Table of Contents
A Manifold Pressure Gauge: Designed to Monitor Your Engine's Health
A manifold pressure gauge is a crucial instrument for monitoring the performance and health of internal combustion engines, particularly those utilizing carburetors or early fuel injection systems. While less critical in modern, electronically controlled engines with sophisticated sensors, understanding its function remains vital for maintaining optimal engine efficiency, detecting potential problems, and ensuring safety. This comprehensive guide delves deep into the design, function, and applications of a manifold pressure gauge, offering insights for both seasoned mechanics and curious enthusiasts.
Understanding Manifold Pressure: The Heart of the Matter
Before diving into the specifics of the gauge, it's crucial to grasp the concept of manifold pressure itself. Manifold pressure refers to the pressure of the air-fuel mixture within the intake manifold of an engine. This pressure is a direct indication of the engine's volumetric efficiency – its ability to draw in and utilize air during the intake stroke.
Factors Influencing Manifold Pressure
Several factors influence the manifold pressure reading:
- Throttle Position: The primary determinant. A wider open throttle allows more air into the manifold, increasing manifold pressure. A closed throttle restricts airflow, resulting in lower pressure.
- Engine Speed (RPM): Higher RPM generally equates to higher manifold pressure as the engine draws in more air with each cycle.
- Altitude: At higher altitudes, the air density is lower, resulting in lower manifold pressure even with the same throttle position and RPM.
- Engine Load: Heavier loads demand more fuel and air, generally increasing manifold pressure.
- Air Filter Condition: A clogged air filter restricts airflow, leading to reduced manifold pressure.
- Intake Leaks: Leaks in the intake system can significantly reduce manifold pressure, impacting engine performance.
- Boost Pressure (Turbocharged/Supercharged Engines): In forced induction systems, manifold pressure significantly increases beyond atmospheric pressure due to the compressor forcing air into the intake manifold.
The Design and Function of a Manifold Pressure Gauge
A manifold pressure gauge, essentially a pressure gauge calibrated in inches of mercury (Hg) or kilopascals (kPa), directly measures the pressure within the intake manifold. Its design usually involves:
- Pressure Sensor: This component detects the pressure variations within the intake manifold. In older systems, this might be a simple diaphragm-based sensor, while modern gauges may incorporate more sophisticated electronic sensors for enhanced accuracy and responsiveness.
- Transmission Mechanism (Analog Gauges): Analog gauges use a mechanical linkage or a Bourdon tube to translate the pressure changes detected by the sensor into visible needle movement across the gauge face. The movement is calibrated to accurately reflect the manifold pressure.
- Display (Analog & Digital Gauges): The display clearly shows the manifold pressure reading. Analog gauges use a needle and marked scale, while digital gauges offer a numerical readout.
- Calibration: Accurate calibration is critical for reliable readings. The gauge must be calibrated to accurately reflect pressure changes within the specified range.
- Housing and Mounting: The gauge is housed in a protective casing designed for robust mounting within the aircraft or vehicle's instrument panel.
Types of Manifold Pressure Gauges
Manifold pressure gauges are available in various types:
- Mechanical Gauges: These gauges rely on a mechanical linkage to translate pressure changes into needle movement. They're generally simpler, more robust, and less prone to electronic failures.
- Electronic Gauges: These incorporate electronic sensors and display units, providing greater accuracy and the ability to integrate with other electronic systems.
- Digital Gauges: These gauges display the manifold pressure as a numerical value, offering clear and unambiguous readings.
Applications of Manifold Pressure Gauges
The applications of manifold pressure gauges extend across various industries and contexts:
Aviation
In aviation, manifold pressure gauges are indispensable for monitoring the performance of piston aircraft engines. Pilots use the gauge to ensure that the engine is operating within its safe and efficient parameters. Monitoring manifold pressure helps pilots:
- Maintain Optimal Engine Performance: By keeping manifold pressure within the recommended range, pilots optimize engine power and fuel efficiency.
- Detect Engine Problems: Significant deviations from the normal manifold pressure range can indicate issues such as carburetor icing, leaks in the intake system, or engine malfunction.
- Ensure Safe Operation: Maintaining appropriate manifold pressure is crucial for safe engine operation and preventing engine damage.
Automotive Applications (Historically Significant)
While less common in modern vehicles due to advanced electronic engine management systems, manifold pressure gauges were crucial in older vehicles, particularly those with carburetors. They provided valuable information for:
- Carburetor Tuning: Mechanics used manifold pressure readings to fine-tune carburetor settings for optimal fuel delivery and engine performance.
- Troubleshooting Engine Issues: Low manifold pressure could indicate problems such as vacuum leaks, clogged air filters, or carburetor malfunctions.
- Performance Tuning: In performance applications, manifold pressure gauges helped monitor the effectiveness of modifications such as performance carburetors or intake systems.
Marine Applications
Similar to aviation, manifold pressure gauges play a vital role in monitoring the health and performance of marine engines. This is particularly true for older or naturally aspirated engines. The application is largely the same as in aviation.
Interpreting Manifold Pressure Readings
Interpreting manifold pressure readings requires understanding the engine's specifications and operating parameters. The manufacturer's specifications will usually provide a recommended manifold pressure range for various operating conditions.
Deviation from the normal range can signal problems:
- Low Manifold Pressure: Could indicate restricted airflow due to a clogged air filter, leaks in the intake system, carburetor problems (in older vehicles), or a faulty pressure sensor.
- High Manifold Pressure (in naturally aspirated engines): Usually indicates a problem with the throttle linkage, restricted exhaust system, or potentially internal engine damage.
- Fluctuating Manifold Pressure: Could indicate problems with the fuel system, ignition system, or a vacuum leak.
Maintaining and Troubleshooting Manifold Pressure Gauges
Regular maintenance ensures accurate readings and extends the lifespan of the gauge.
For mechanical gauges:
- Regular visual inspection: Check for any signs of damage or leaks.
- Calibration: Periodic calibration is essential to ensure accurate readings. This is typically done by a qualified technician using specialized equipment.
For electronic gauges:
- Check for power supply: Ensure proper power supply to the gauge.
- Sensor checks: Verify the functionality of the pressure sensor.
- Software updates: Some electronic gauges may require software updates to maintain optimal performance.
The Future of Manifold Pressure Monitoring
While manifold pressure gauges remain valuable tools, particularly in older technology engines, modern vehicles increasingly rely on sophisticated electronic engine management systems. These systems use multiple sensors, including mass airflow sensors and manifold absolute pressure (MAP) sensors, to accurately monitor and control air-fuel mixtures. These sensors provide the same essential information as a manifold pressure gauge, often with greater precision and integration with other engine control parameters.
However, even in modern vehicles, understanding the basic principles of manifold pressure and how it reflects engine health remains important for diagnostics and troubleshooting. A fundamental knowledge of this aspect of engine function will always be an asset to any mechanic or automotive enthusiast.
Conclusion
The manifold pressure gauge, a seemingly simple instrument, plays a crucial role in monitoring engine performance and health. Its design, function, and applications span diverse fields, underscoring its importance in ensuring efficient and safe operation. While the reliance on these gauges is reducing with advancements in electronic engine management, the fundamental principles of manifold pressure and its interpretation remain essential knowledge for anyone involved in engine maintenance or performance optimization. Understanding the information provided by a manifold pressure gauge, whether in an airplane, boat, or classic car, allows for proactive maintenance and ultimately prevents costly repairs and potential safety hazards. The legacy of the manifold pressure gauge stands as a testament to the importance of direct, tangible measurements in understanding the intricate workings of internal combustion engines.
Latest Posts
Latest Posts
-
4 03 Quiz Journalism And Research Develop Ideas
Apr 27, 2025
-
The Scarlet Letter Chapter 8 Summary
Apr 27, 2025
-
Que Significa Yield En Senales De Transito
Apr 27, 2025
-
2 3 1 Hexadecimal And Octal Number Systems
Apr 27, 2025
-
True Or False Fields Are Knowledge Objects
Apr 27, 2025
Related Post
Thank you for visiting our website which covers about A Manifold Pressure Gauge Is Designed To . We hope the information provided has been useful to you. Feel free to contact us if you have any questions or need further assistance. See you next time and don't miss to bookmark.