A New Piece Of Equipment Arrives And Your Supervisor
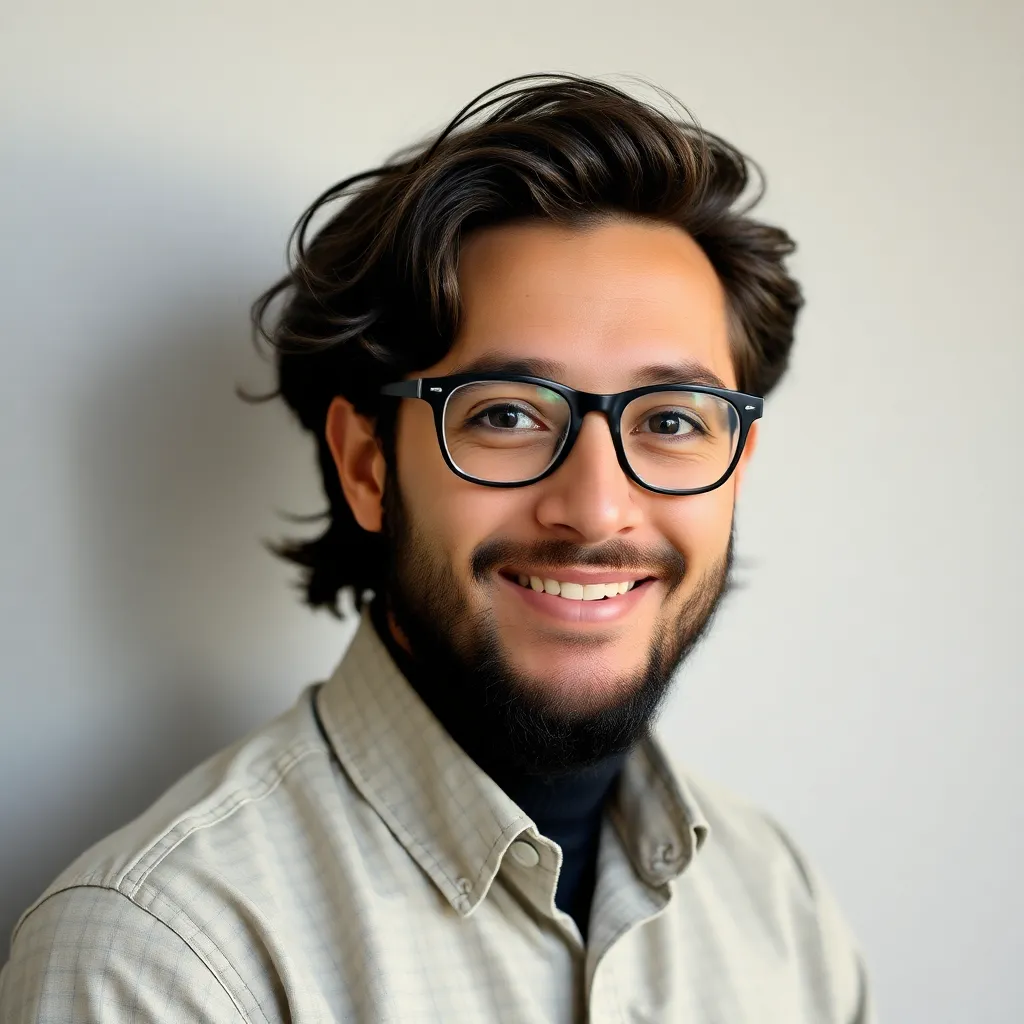
Onlines
May 12, 2025 · 6 min read
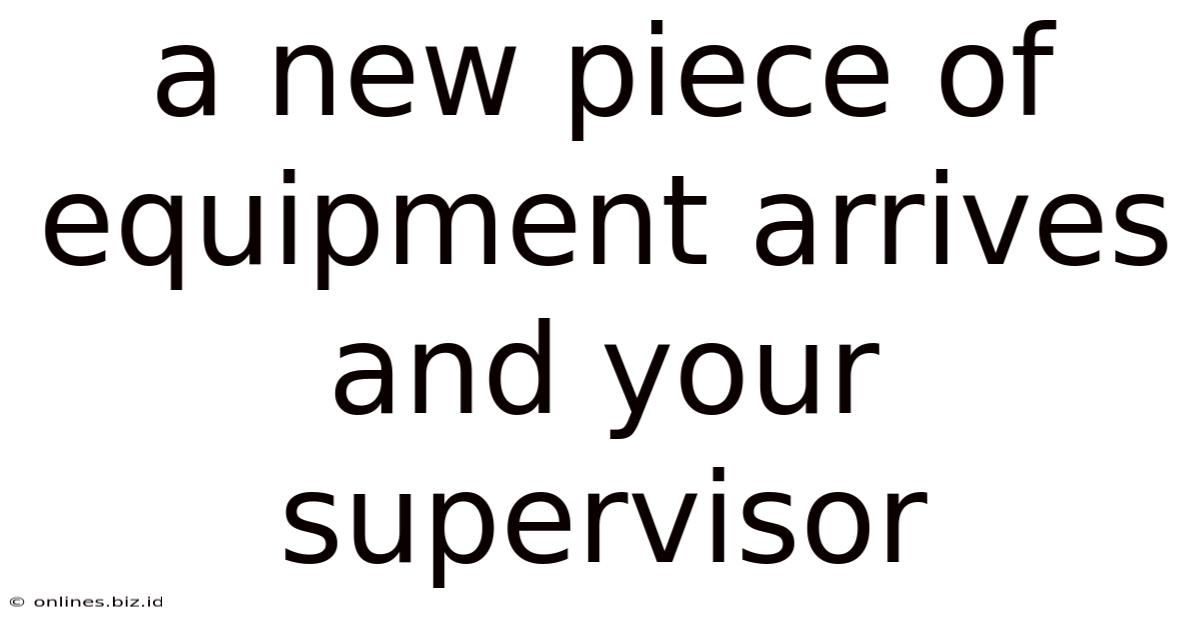
Table of Contents
A New Piece of Equipment Arrives: Navigating the Supervisor's Expectations and Team Dynamics
The arrival of new equipment in any workplace is a significant event. It promises increased efficiency, improved workflow, and potentially, a boost in overall productivity. However, the process isn't always smooth sailing. This article explores the multifaceted challenges and opportunities presented by the introduction of new equipment, focusing on the critical role of the supervisor and the dynamics within the team.
The Anticipation and Anxiety: Before the Equipment Arrives
Before the gleaming new machine even rolls through the door, a ripple of anticipation – and perhaps anxiety – runs through the team. This pre-arrival phase is crucial. A proactive and communicative supervisor plays a vital role in mitigating potential problems.
Effective Communication is Key
-
Transparency is paramount: Supervisors should openly communicate the reasons for the new equipment, its capabilities, and the anticipated changes to workflow. This helps alleviate uncertainty and reduces the likelihood of resistance to change. Detailed explanations, perhaps including visual aids like brochures or videos, can significantly improve understanding.
-
Addressing concerns proactively: Anticipating potential concerns – such as job security fears or worries about the learning curve – is essential. Supervisors should address these concerns directly and transparently, emphasizing opportunities for skill development and the collaborative nature of the transition. Open forums or Q&A sessions can be incredibly valuable.
-
Setting clear expectations: Before the equipment arrives, the supervisor should clearly articulate expectations regarding training, productivity targets, and the new procedures. This establishes a foundation for success and minimizes confusion later on. A well-defined timeline for implementation and training significantly enhances team morale and reduces stress.
The Arrival and Initial Training: A Supervisor's Crucial Role
The day the new equipment arrives is often a mixture of excitement and apprehension. The supervisor's role here is pivotal in ensuring a smooth transition.
The Importance of Hands-on Training
-
Structured training programs: Effective training is not just a one-time session; it's an ongoing process. Supervisors should implement a comprehensive training program that covers both the technical aspects of the equipment and its integration into the existing workflow. This could involve external trainers, internal experts, or a combination of both.
-
Practical application: Training should not be confined to theory. Sufficient time should be allocated for hands-on practice, allowing employees to gain confidence and proficiency with the new equipment. A phased approach, starting with simpler tasks and gradually increasing complexity, is often the most effective.
-
Mentorship and support: Supervisors should actively encourage mentorship among team members. More experienced colleagues can help newcomers, creating a supportive learning environment and fostering a sense of team cohesion. Continuous support and regular check-ins are crucial, especially during the initial learning phase.
Managing Team Dynamics During the Transition
-
Addressing individual learning styles: Supervisors must recognize that employees learn at different paces and have diverse learning styles. A flexible training approach, accommodating individual needs and preferences, is essential for maximizing learning outcomes.
-
Celebrating small wins: Acknowledging and celebrating early successes, even minor ones, can significantly boost team morale and reinforce positive behavior. Positive reinforcement motivates employees and encourages them to persevere through challenges.
-
Open communication channels: Maintaining open communication channels is vital throughout the transition. Supervisors should regularly solicit feedback from employees, addressing any concerns or difficulties promptly. This fosters a sense of collaboration and shared responsibility.
Integrating the New Equipment into Workflow: Optimization and Efficiency
Once the initial training is complete, the focus shifts to seamlessly integrating the new equipment into the existing workflow. This stage demands careful planning and execution from the supervisor.
Optimizing Work Processes
-
Streamlining workflows: The supervisor should work with the team to identify opportunities for optimizing existing workflows to fully leverage the capabilities of the new equipment. This might involve re-organizing tasks, assigning responsibilities differently, or even redesigning the workspace.
-
Data analysis and performance tracking: Regular data analysis is crucial to monitor the equipment's impact on productivity and identify areas for improvement. Supervisors should implement a system for tracking key performance indicators (KPIs), allowing for data-driven decision making.
-
Regular reviews and adjustments: Integrating new equipment is an iterative process. Supervisors should schedule regular reviews to assess the effectiveness of the new workflow and make necessary adjustments. Flexibility and willingness to adapt are essential for successful integration.
Addressing Potential Challenges
-
Technical glitches and downtime: Unexpected technical problems are inevitable. Supervisors should have a plan in place for addressing these issues quickly and efficiently, minimizing downtime and maintaining productivity. This might involve establishing a relationship with equipment maintenance providers or having backup systems in place.
-
Resistance to change: Some employees may be resistant to adopting the new equipment or changing their established routines. Supervisors should address this resistance empathetically, providing additional support and training where necessary. Open dialogue and collaborative problem-solving are key to overcoming resistance.
-
Safety concerns: Safety should always be a top priority. Supervisors must ensure that adequate safety training is provided and that all safety protocols are rigorously followed. Regular safety checks and inspections are crucial to prevent accidents.
The Long-Term Impact: Sustained Productivity and Team Growth
The successful integration of new equipment is not a one-off event; it's an ongoing process. The supervisor plays a crucial role in ensuring the long-term benefits of the investment.
Continuous Improvement and Training
-
Ongoing training and development: Technology evolves rapidly. Supervisors should ensure that employees receive ongoing training and development opportunities to keep their skills updated and to maximize the efficiency of the new equipment.
-
Regular performance reviews: Regular performance reviews, linked to the use of the new equipment, help identify areas for improvement and provide constructive feedback. These reviews should focus not only on individual performance but also on team dynamics and workflow efficiency.
-
Embracing innovation and adapting to change: The introduction of new equipment signals a commitment to innovation. Supervisors should foster a culture of continuous improvement, encouraging employees to explore new ideas and suggest improvements to processes and workflows.
Fostering a Positive and Productive Work Environment
-
Recognition and rewards: Acknowledging and rewarding employees for their efforts and achievements significantly boosts morale and encourages ongoing commitment. This could involve formal recognition programs or informal expressions of appreciation.
-
Promoting teamwork and collaboration: The successful integration of new equipment requires effective teamwork. Supervisors should actively promote collaboration and communication among team members, fostering a sense of shared purpose and collective achievement.
-
Measuring long-term success: Ultimately, the success of integrating new equipment should be measured by its long-term impact on productivity, efficiency, and overall team performance. Regular monitoring and evaluation are essential to ensure the investment yields the desired returns.
The arrival of new equipment is a transformative event, presenting both opportunities and challenges. A skilled and proactive supervisor is instrumental in navigating this transition successfully, ensuring a smooth integration, optimizing workflow, and fostering a positive and productive work environment. By embracing communication, providing comprehensive training, addressing concerns effectively, and fostering a culture of continuous improvement, supervisors can leverage the full potential of new equipment and pave the way for sustained growth and productivity.
Latest Posts
Latest Posts
-
According To The Chart When Did A Pdsa Cycle Occur
May 12, 2025
-
Bioflix Activity Gas Exchange The Respiratory System
May 12, 2025
-
Economic Value Creation Is Calculated As
May 12, 2025
-
Which Items Typically Stand Out When You Re Scanning Text
May 12, 2025
-
Assume That Price Is An Integer Variable
May 12, 2025
Related Post
Thank you for visiting our website which covers about A New Piece Of Equipment Arrives And Your Supervisor . We hope the information provided has been useful to you. Feel free to contact us if you have any questions or need further assistance. See you next time and don't miss to bookmark.