A Successful Quality Strategy Begins With
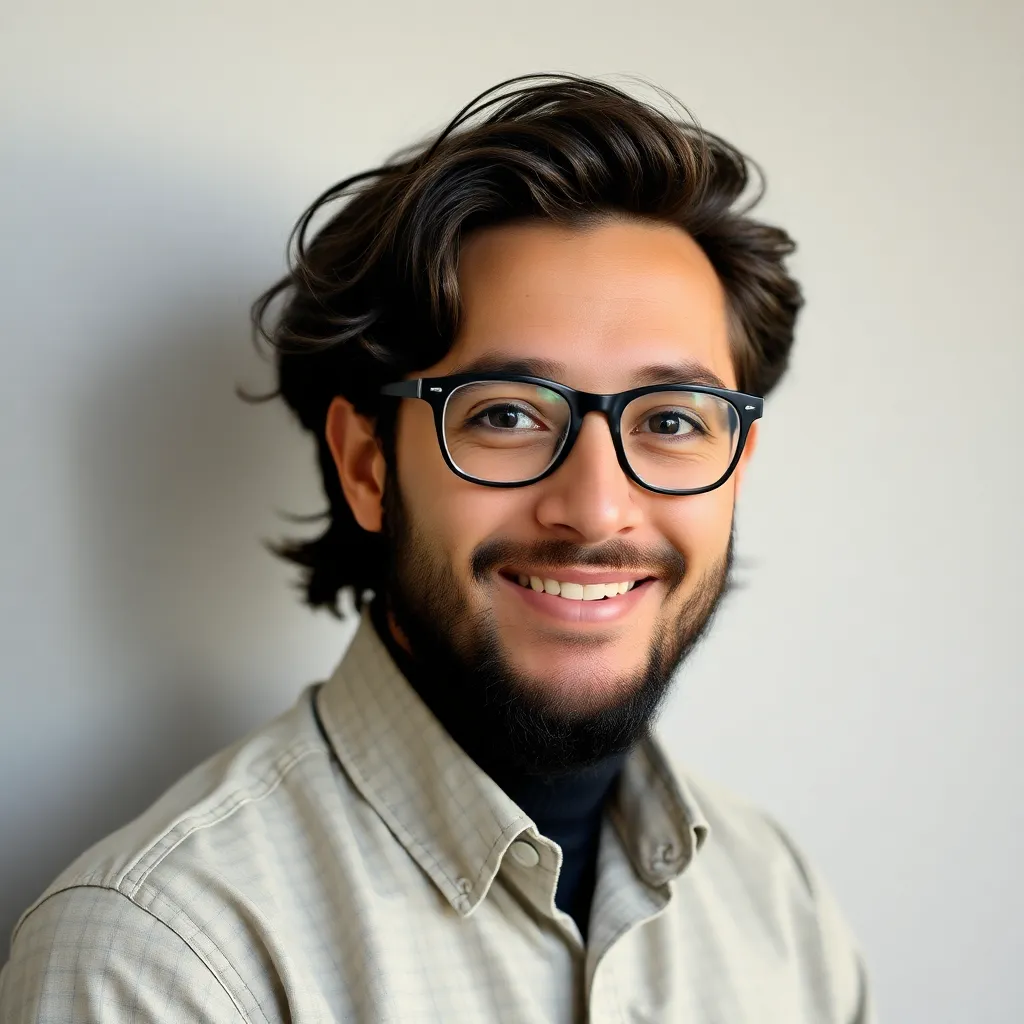
Onlines
May 10, 2025 · 6 min read
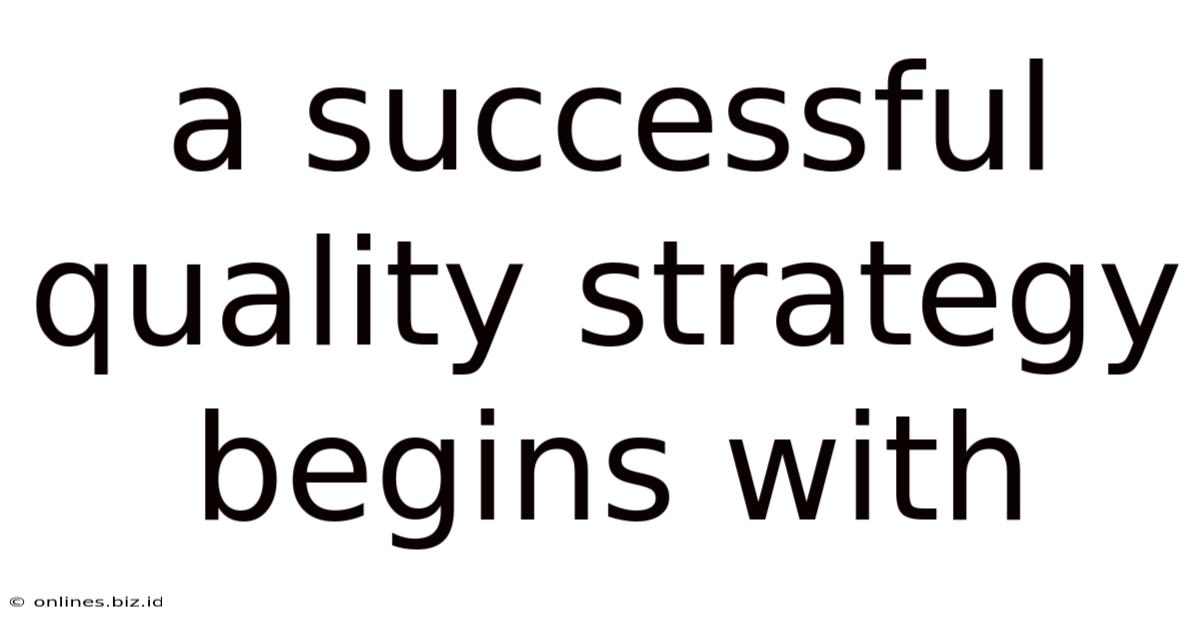
Table of Contents
A Successful Quality Strategy Begins With… Commitment
A successful quality strategy isn't a one-size-fits-all solution; it's a journey, a continuous improvement process deeply ingrained within the very fabric of an organization. While methodologies and tools play a vital role, the cornerstone of any successful quality initiative rests firmly on unwavering commitment from leadership down to the front lines. This commitment isn't merely lip service; it demands tangible action, visible investment, and a demonstrable dedication to prioritizing quality above all else.
Phase 1: Laying the Foundation - Defining Quality & Establishing a Vision
Before embarking on any quality improvement journey, a clear understanding of what "quality" means within the context of your organization is paramount. This isn't a generic definition; it needs to be specific, measurable, achievable, relevant, and time-bound (SMART).
Defining "Quality" for Your Organization:
- Internal Perspective: Consider internal processes, efficiency, employee satisfaction, and resource optimization. What internal benchmarks indicate a high-quality operation? This might involve reduced error rates, improved cycle times, or enhanced employee morale.
- External Perspective: Focus on customer satisfaction, product performance, and market competitiveness. How do your customers define quality? What are their expectations and needs? How does your product or service stack up against your competitors?
- Strategic Alignment: Ensure your quality definition aligns with your overall business objectives. How does achieving high quality contribute to your organization's strategic goals, such as increased market share, profitability, or brand reputation?
Once you've established a clear definition of quality, develop a compelling vision statement that articulates your aspirations. This vision should inspire and motivate your team to strive for excellence. It should be easily understood and communicated throughout the organization, fostering a shared understanding of the quality journey's ultimate goal.
Establishing Measurable Goals and KPIs:
Vague aspirations are meaningless without concrete, measurable goals. Identify key performance indicators (KPIs) that will track your progress towards achieving your quality vision. These KPIs should be:
- Specific: Clearly define what you're measuring.
- Measurable: Use quantifiable metrics to track progress.
- Achievable: Set realistic goals that are attainable within a reasonable timeframe.
- Relevant: Ensure your KPIs directly relate to your quality definition and strategic objectives.
- Time-bound: Set deadlines for achieving specific milestones.
Examples of relevant KPIs might include:
- Customer Satisfaction Scores (CSAT): Measured through surveys and feedback mechanisms.
- Defect Rates: The percentage of products or services with defects.
- Cycle Time: The time it takes to complete a process.
- Employee Turnover: A low turnover rate often indicates a positive work environment conducive to quality.
- Return on Investment (ROI) of Quality Initiatives: Measuring the financial benefits of quality improvements.
Phase 2: Building the Infrastructure - Implementing Quality Management Systems (QMS)
Implementing a robust QMS is crucial for driving consistent quality improvement. This system should provide a framework for:
Defining Roles and Responsibilities:
Clearly define the roles and responsibilities of individuals and teams involved in quality management. This ensures accountability and avoids duplication of effort. Designate a quality manager or team to oversee the implementation and maintenance of the QMS.
Establishing Processes and Procedures:
Document all critical processes and procedures related to product development, production, service delivery, and customer interaction. These documented processes should be easily accessible and understood by all relevant personnel. Regularly review and update these processes to ensure they remain effective and efficient.
Implementing Quality Control Measures:
Introduce quality control measures at various stages of your processes. This might involve regular inspections, testing, and audits to identify and address potential quality issues proactively. Embrace preventive measures alongside reactive ones to minimize defects and errors.
Selecting Appropriate Quality Tools and Techniques:
A range of tools and techniques can support your QMS. Consider incorporating:
- Statistical Process Control (SPC): Used to monitor and control processes through statistical analysis.
- Six Sigma: A data-driven methodology for improving processes and reducing variation.
- Lean Manufacturing: A set of principles aimed at eliminating waste and improving efficiency.
- Root Cause Analysis (RCA): Techniques to identify the underlying causes of quality problems.
- 5S Methodology: A workplace organization method focused on sorting, setting in order, shining, standardizing, and sustaining.
The choice of tools and techniques will depend on your specific needs and industry context. Don't feel obligated to implement every tool available; focus on those that best address your unique challenges.
Phase 3: Fostering a Culture of Quality - Empowering Employees and Driving Continuous Improvement
A successful quality strategy hinges on creating a culture where quality is not just a priority but a shared value. This requires:
Empowering Employees:
Empower employees at all levels to identify and address quality issues. Provide them with the training, resources, and authority to make improvements. Encourage a culture of open communication and feedback, where employees feel comfortable raising concerns and suggesting solutions.
Providing Training and Development:
Invest in training and development programs to equip employees with the skills and knowledge they need to contribute to quality improvement. Training should focus on quality management principles, relevant tools and techniques, and problem-solving methodologies.
Implementing Continuous Improvement Programs:
Establish a system for continuous improvement, such as Kaizen or Plan-Do-Check-Act (PDCA) cycles. Regularly review processes, identify areas for improvement, and implement changes to enhance quality. Encourage experimentation and learning from both successes and failures.
Recognizing and Rewarding Success:
Recognize and reward employees who contribute to quality improvement. This could involve formal awards, bonuses, or public acknowledgement. Celebrating successes reinforces the importance of quality and motivates employees to continue striving for excellence.
Fostering Collaboration and Communication:
Encourage collaboration and communication across departments and teams. Establish effective communication channels to share information, best practices, and lessons learned. Promote teamwork and a shared sense of responsibility for quality.
Phase 4: Measuring, Monitoring, and Adapting - Ensuring Continuous Improvement
Once your QMS is implemented, continuous monitoring and adaptation are essential.
Regular Monitoring and Measurement:
Regularly monitor your KPIs and track your progress towards your quality goals. This data will provide insights into the effectiveness of your quality initiatives and identify areas where improvements are needed. Utilize data visualization techniques to present your findings in a clear and concise manner.
Conducting Regular Audits:
Conduct regular internal audits to assess the effectiveness of your QMS and identify any areas of non-compliance. These audits should be comprehensive and involve a systematic review of processes, procedures, and documentation. Use audit findings to drive further improvements.
Adapting to Change:
The business landscape is constantly evolving. Regularly review your quality strategy and adapt it to changing customer needs, market conditions, and technological advancements. Be flexible and willing to adjust your approach as needed to maintain its effectiveness.
Utilizing Feedback Mechanisms:
Implement robust feedback mechanisms to gather input from customers, employees, and other stakeholders. Use this feedback to identify areas for improvement and refine your quality strategy. Actively solicit feedback and use it to drive continuous improvement.
Conclusion: The Enduring Commitment to Quality
Building a successful quality strategy is a marathon, not a sprint. It demands consistent effort, unwavering commitment, and a willingness to adapt and evolve. By focusing on laying a strong foundation, building a robust infrastructure, fostering a culture of quality, and continuously measuring and adapting, organizations can achieve sustainable quality improvements that drive enhanced performance, increased profitability, and enhanced customer satisfaction. Remember, the journey towards excellence is ongoing; the commitment to quality should be unwavering.
Latest Posts
Latest Posts
-
Aerobic Exercise Became Part Of This Movement In The 1970s
May 11, 2025
-
Which One Of The Following Is A Capital Structure Decision
May 11, 2025
-
The 18 Month Career Development Board
May 11, 2025
-
Where Do Much Of The Seafood We Eat Begin Life
May 11, 2025
-
Convert The Lewis Structure Below Into A Skeletal Structure
May 11, 2025
Related Post
Thank you for visiting our website which covers about A Successful Quality Strategy Begins With . We hope the information provided has been useful to you. Feel free to contact us if you have any questions or need further assistance. See you next time and don't miss to bookmark.