A Successful Quality Strategy Features Which Of The Following Elements
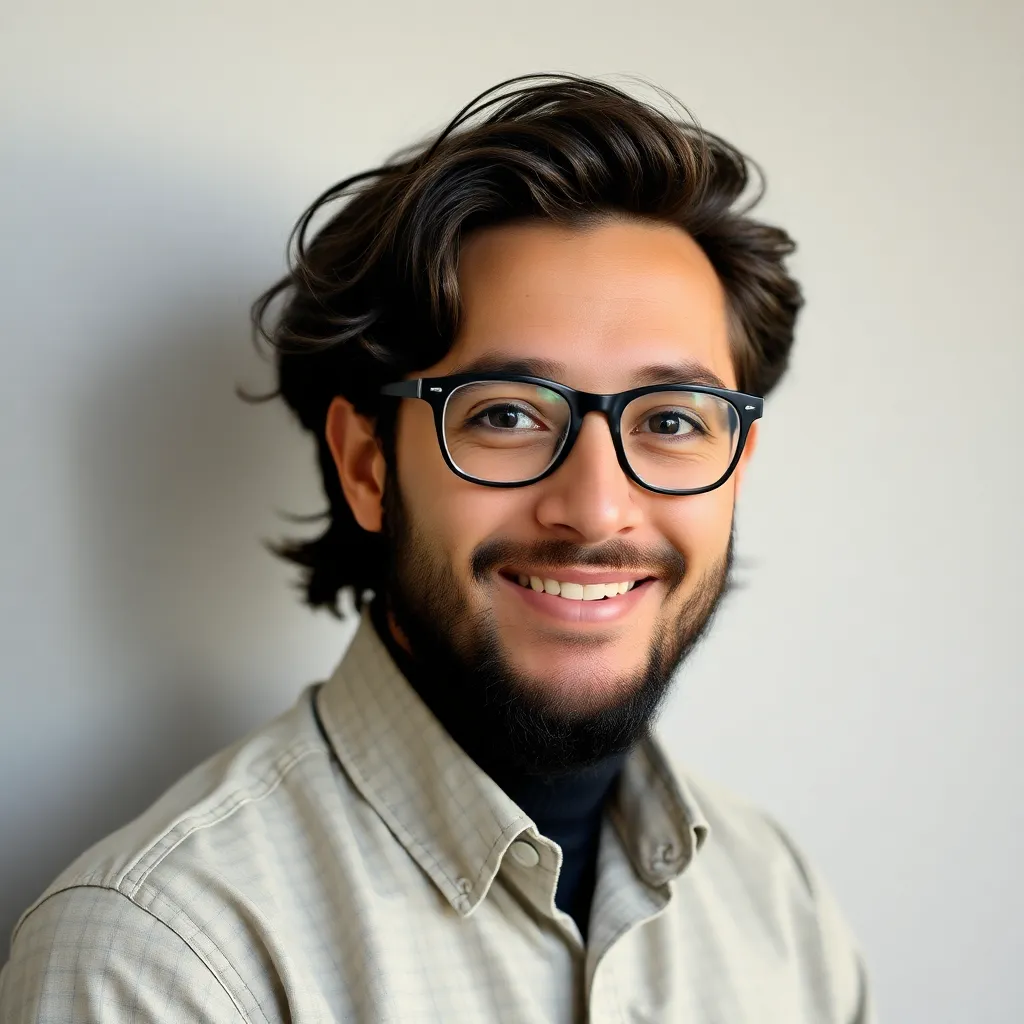
Onlines
May 07, 2025 · 7 min read
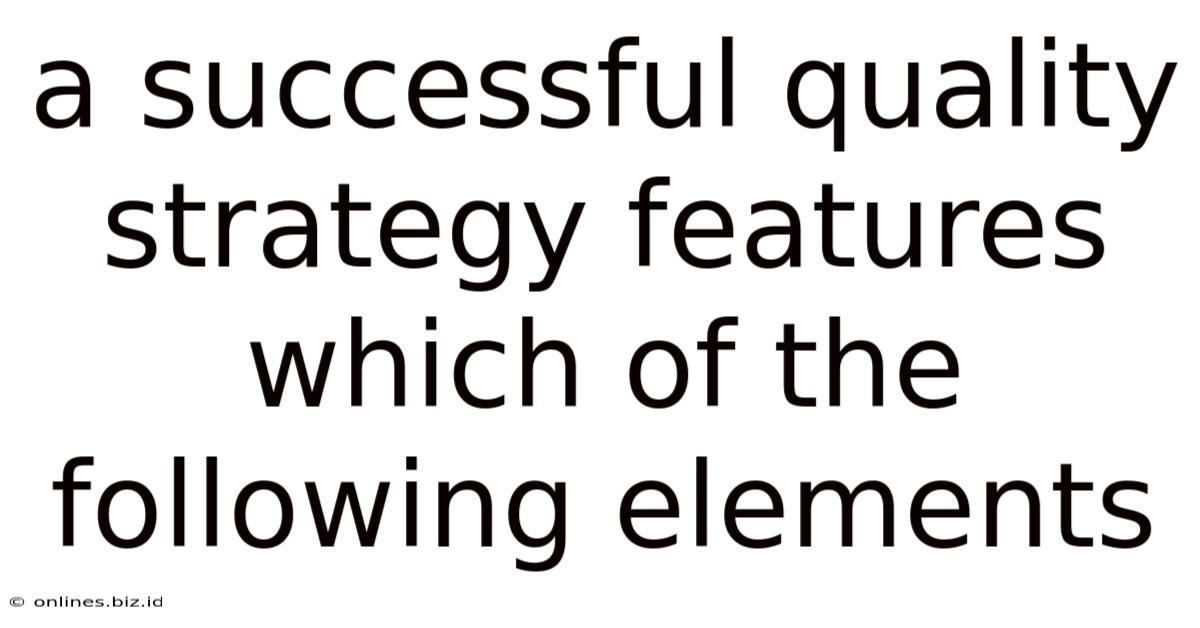
Table of Contents
A Successful Quality Strategy: Key Elements for Achieving Excellence
Implementing a successful quality strategy is paramount for any organization aiming for sustainable growth and competitive advantage. It's not merely about producing defect-free products or services; it's about embedding a quality-centric mindset throughout the entire organization, impacting every aspect from product design to customer service. This comprehensive guide delves into the essential elements of a thriving quality strategy, exploring how each contributes to overall success.
1. Strong Leadership Commitment and Vision
A successful quality strategy starts at the top. Leadership commitment isn't just lip service; it's a demonstrable dedication to quality woven into the fabric of the organization's culture. This commitment manifests in several ways:
- Clear articulation of quality goals: Leadership must define specific, measurable, achievable, relevant, and time-bound (SMART) quality goals. These goals should cascade down through the organization, providing clear direction and accountability at all levels.
- Resource allocation: Investing sufficient resources – financial, human, and technological – is crucial. This includes providing employees with the necessary training, tools, and technology to perform their jobs effectively and efficiently.
- Promoting a culture of continuous improvement: Leaders need to foster a culture where quality improvement is seen as an ongoing process, not a one-time event. This involves encouraging employees to identify and address quality issues proactively, rewarding successful initiatives, and creating a safe space for constructive feedback.
- Leading by example: Leaders must embody the quality values they expect from their employees. This includes adhering to quality standards in their own work and demonstrating a commitment to continuous learning and improvement.
The Power of a Shared Vision
Beyond commitment, a shared vision of quality is essential. This means aligning the entire workforce around a common understanding of what quality means within the organization and how it contributes to the overall strategic objectives. This shared vision provides a cohesive framework for decision-making and problem-solving. It encourages collaboration and ensures that everyone is working towards the same quality goals.
2. Customer Focus and Understanding
Understanding customer needs and expectations is foundational to any successful quality strategy. A truly customer-centric approach involves:
- Voice of the Customer (VOC): Actively soliciting feedback from customers through surveys, focus groups, feedback forms, and social media monitoring. This provides valuable insights into their preferences, pain points, and expectations.
- Customer Relationship Management (CRM): Implementing a robust CRM system to manage customer interactions, track feedback, and personalize the customer experience. This enables the organization to proactively address customer concerns and build stronger relationships.
- Customer Segmentation: Understanding different customer segments and tailoring quality initiatives to meet their specific needs. This ensures that the organization is addressing the diverse requirements of its customer base effectively.
- Proactive Customer Service: Going beyond reactive problem-solving and proactively anticipating and addressing potential customer issues. This builds trust and loyalty, enhancing the overall customer experience.
Turning Customer Feedback into Actionable Insights
The value of customer feedback lies not just in collecting it, but in analyzing it and translating it into actionable improvements. This requires establishing clear processes for collecting, analyzing, and acting upon customer feedback. This feedback loop ensures that quality initiatives are directly aligned with customer needs and expectations.
3. Robust Processes and Procedures
Effective quality management relies on well-defined processes and procedures. This involves:
- Process Mapping: Visually representing the steps involved in each key process to identify bottlenecks, inefficiencies, and potential areas for improvement.
- Standard Operating Procedures (SOPs): Developing clear and concise SOPs for each process to ensure consistency and reduce variability. This minimizes errors and promotes efficiency.
- Documentation and Record Keeping: Maintaining detailed records of processes, quality metrics, and customer feedback. This provides valuable data for continuous improvement initiatives.
- Regular Process Audits: Conducting regular audits to evaluate the effectiveness of processes and identify areas for improvement. This ensures that processes remain aligned with quality standards.
The Importance of Standardization
Standardization is key to consistent quality. By establishing and adhering to clearly defined processes and procedures, organizations can reduce variability, minimize errors, and ensure that products and services meet specified quality standards consistently. This also facilitates training and onboarding of new employees.
4. Continuous Improvement Methodology
Continuous improvement is not merely a goal; it's a mindset and a systematic approach embedded within a successful quality strategy. Popular methodologies include:
- Lean: Focuses on eliminating waste and maximizing efficiency in all processes.
- Six Sigma: A data-driven approach to reducing variation and improving quality.
- Kaizen: Emphasizes small, incremental improvements made continuously over time.
- Plan-Do-Check-Act (PDCA) Cycle: A structured approach to problem-solving and process improvement.
Choosing the Right Methodology
The choice of methodology depends on the specific needs and context of the organization. However, the underlying principle remains consistent: a commitment to ongoing improvement and adaptation.
5. Employee Empowerment and Training
A successful quality strategy empowers employees at all levels to contribute to quality improvement. This involves:
- Training and Development: Providing employees with the necessary skills and knowledge to perform their jobs effectively and contribute to quality improvement.
- Empowerment and Ownership: Giving employees the authority and responsibility to identify and address quality issues.
- Recognition and Rewards: Acknowledging and rewarding employees who contribute to quality improvement. This fosters a culture of ownership and accountability.
- Open Communication: Creating a culture of open communication where employees feel comfortable raising concerns and sharing ideas.
Investing in Your Workforce
Investing in employee training and development is a crucial element of a successful quality strategy. Well-trained employees are more likely to be engaged, productive, and committed to quality.
6. Technology and Data Analytics
Leveraging technology and data analytics can significantly enhance quality management. This includes:
- Quality Management Systems (QMS) Software: Utilizing QMS software to manage quality processes, track metrics, and facilitate collaboration.
- Data Analytics: Using data analytics to identify trends, patterns, and root causes of quality issues. This enables proactive problem-solving and continuous improvement.
- Automation: Automating quality control processes to improve efficiency and reduce errors.
- Predictive Analytics: Using predictive analytics to anticipate potential quality issues and prevent them from occurring.
The Power of Data-Driven Decision Making
Data analytics is a game-changer in quality management. By collecting and analyzing data, organizations can gain valuable insights into their processes, identify areas for improvement, and make data-driven decisions that enhance quality.
7. Supplier Management
Maintaining strong relationships with suppliers is crucial for ensuring consistent product quality. This involves:
- Supplier Selection: Carefully selecting suppliers based on their quality systems, capabilities, and track record.
- Supplier Performance Monitoring: Regularly monitoring supplier performance to ensure that they meet quality standards.
- Supplier Development: Working with suppliers to help them improve their quality systems and capabilities.
- Collaboration and Communication: Establishing clear communication channels with suppliers to facilitate collaboration and problem-solving.
Building Strong Supplier Partnerships
Successful supplier management is not just about monitoring; it's about building strong, collaborative partnerships. By working closely with suppliers, organizations can ensure consistent product quality and achieve mutually beneficial outcomes.
8. Regular Review and Improvement
A successful quality strategy isn't static; it requires continuous review and improvement. This involves:
- Regular Management Reviews: Conducting regular management reviews to assess the effectiveness of the quality management system and identify areas for improvement.
- Performance Monitoring and Reporting: Tracking key quality metrics and reporting regularly on progress toward quality goals.
- Corrective and Preventive Actions (CAPA): Implementing robust CAPA processes to address quality issues and prevent recurrence.
- Adaptation and Innovation: Continuously adapting the quality strategy to meet changing customer needs and market demands.
The Cycle of Continuous Improvement
The process of reviewing, monitoring, and adapting is a continuous cycle. By regularly evaluating the effectiveness of the quality strategy and making necessary adjustments, organizations can ensure that it remains relevant and effective.
Conclusion: Building a Culture of Quality
A successful quality strategy is more than just a set of procedures; it's a fundamental shift in organizational culture, placing quality at the heart of everything the organization does. By embracing the elements outlined above – strong leadership, customer focus, robust processes, continuous improvement, employee empowerment, technology, supplier management, and ongoing review – organizations can build a sustainable quality culture that drives excellence and delivers exceptional results. This commitment to quality is not just a competitive advantage; it's a foundation for long-term success and sustained growth in today's dynamic marketplace.
Latest Posts
Latest Posts
-
Consider The Mechanics Of The Pinhole Camera
May 11, 2025
-
Age Fatigue Inattentiveness Eyesight And Footwear Are
May 11, 2025
-
Arc Strikes Outside Of The Weld Groove
May 11, 2025
-
Which Statement About Stereotyping Is True
May 11, 2025
-
What Is Not A Function Of Cerumen
May 11, 2025
Related Post
Thank you for visiting our website which covers about A Successful Quality Strategy Features Which Of The Following Elements . We hope the information provided has been useful to you. Feel free to contact us if you have any questions or need further assistance. See you next time and don't miss to bookmark.