A Worker-machine Operation Was Found To Involve 3.0 Miuntes
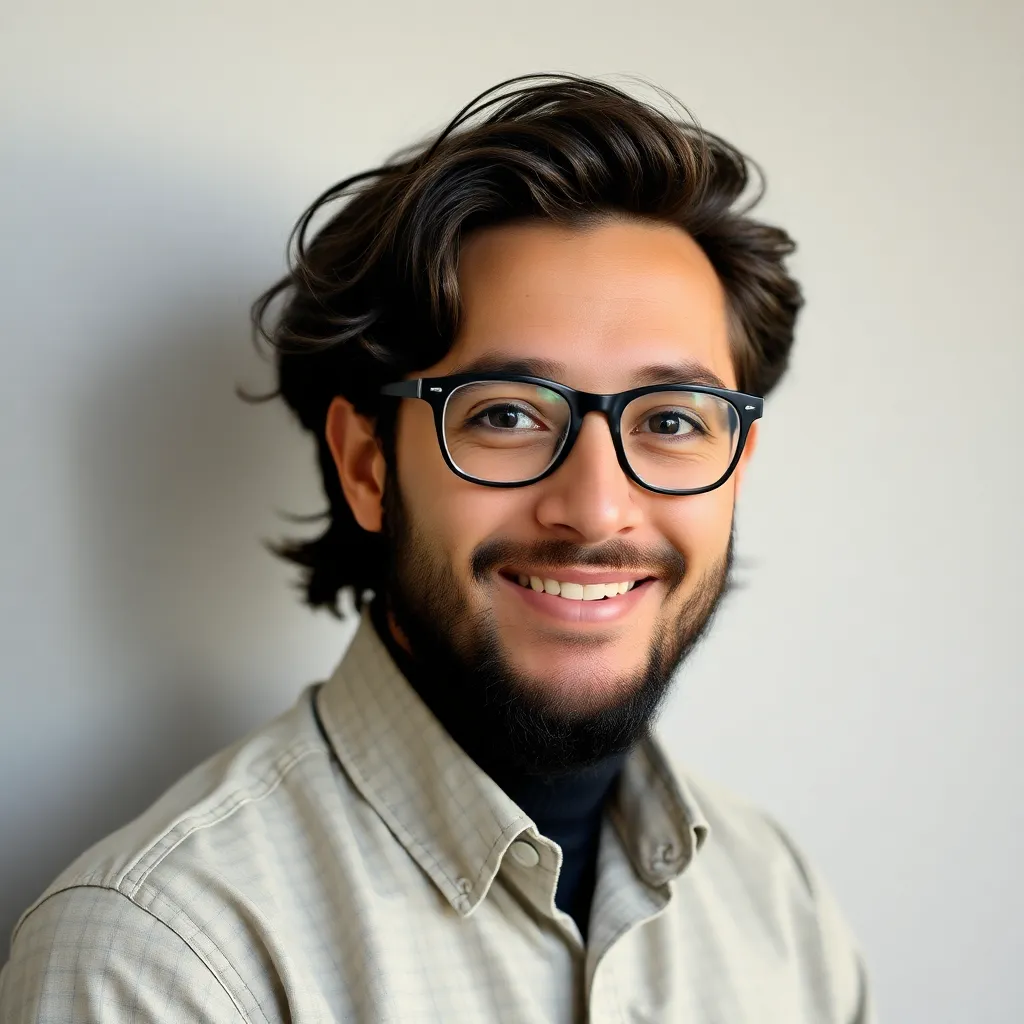
Onlines
Mar 10, 2025 · 6 min read

Table of Contents
A Worker-Machine Operation: Deconstructing a 3-Minute Process for Optimized Efficiency
A seemingly simple 3-minute worker-machine operation hides a multitude of opportunities for optimization. Understanding the intricacies of this seemingly short process—from identifying bottlenecks to leveraging technology—can significantly impact productivity, reduce costs, and improve overall efficiency. This in-depth analysis explores various aspects of a 3-minute worker-machine operation, offering practical strategies for enhancing its performance.
Dissecting the 3-Minute Operation: Identifying Key Components
Before diving into optimization strategies, it's crucial to thoroughly understand the specific tasks involved in this 3-minute operation. This requires a detailed breakdown of the process, identifying each step and its duration. Let's assume, for the sake of example, that the operation involves a worker assembling a small component onto a larger assembly using a specialized machine. A possible breakdown might look like this:
Step-by-Step Breakdown (Example):
- Fetching Components (30 seconds): The worker retrieves the necessary components from a designated storage area. This includes locating the specific parts, potentially involving searching and sorting.
- Machine Preparation (15 seconds): The worker prepares the machine for operation, which could include turning it on, adjusting settings, or verifying its proper functionality.
- Component Placement (15 seconds): Precisely placing the smaller component onto the larger assembly within the machine's operational area.
- Machine Operation (45 seconds): The machine performs the assembly process, typically involving automated actions like fastening or joining.
- Component Removal and Inspection (30 seconds): The worker removes the assembled component from the machine and performs a brief visual inspection for quality control.
- Placement of Finished Product (15 seconds): The worker places the finished product into a designated collection area or container.
- Idle Time (30 seconds): This represents any downtime, such as waiting for the machine to complete its cycle or short breaks between operations.
Note: This is a hypothetical breakdown. The actual steps and durations will vary widely depending on the specific operation. Accurate time-motion studies are crucial for obtaining realistic data.
Optimization Strategies: Maximizing Efficiency in a 3-Minute Operation
Once we have a detailed understanding of the operation's constituent parts, we can begin to identify potential areas for improvement. Optimization strategies can be broadly categorized into:
1. Process Optimization:
- Eliminating Waste: Analyze each step to identify and eliminate any unnecessary movements, delays, or redundant actions. For instance, improving the storage and organization of components can reduce the time spent fetching them. Streamlining the preparation process by pre-setting machine parameters can also save time.
- Improving Workflows: Re-engineer the sequence of operations to improve flow and minimize idle time. Can certain steps be performed concurrently? Can the machine cycle time be reduced through machine upgrades or maintenance?
- Ergonomics: Optimize the workstation layout to ensure comfortable and efficient working conditions. This can significantly reduce fatigue and improve productivity. Proper seating, lighting, and tool placement are crucial elements to consider.
- Standardization: Develop standard operating procedures (SOPs) to ensure consistent execution of the operation and minimize variations in performance. This ensures quality and reduces the likelihood of errors.
2. Technology Integration:
- Automation: Consider automating repetitive tasks to reduce worker involvement and increase speed. This could involve incorporating robotic arms or advanced automated systems. Automated guided vehicles (AGVs) can be used to deliver and transport materials, further reducing wasted time and improving efficiency.
- Machine Upgrades: Invest in newer, faster machines with improved capabilities. This can significantly shorten the machine operation time and boost overall productivity. Regular maintenance is key to keeping the machines in optimal condition.
- Data Analytics: Implement a data tracking system to monitor performance metrics, identify bottlenecks, and track progress. This data-driven approach enables informed decision-making for continuous improvement. Software solutions can provide real-time insights into process efficiency.
- Smart Manufacturing Technologies: Explore technologies like the Internet of Things (IoT) and predictive maintenance to enhance machine uptime and prevent unplanned downtime. IoT sensors can monitor machine conditions, predicting potential issues and reducing the time spent on repairs.
3. Human Factors Optimization:
- Training and Development: Invest in comprehensive training for workers to ensure they possess the necessary skills and knowledge to perform the operation efficiently and accurately. Regular refresher training can reinforce good practices.
- Motivation and Engagement: A motivated and engaged workforce is crucial for productivity. Foster a positive work environment that encourages teamwork and collaboration. Recognizing and rewarding good performance can significantly improve morale and productivity.
- Job Design: Ensure the job is challenging and rewarding, providing opportunities for skill development and advancement. Job enrichment can lead to greater worker satisfaction and better performance.
- Reducing Physical Strain: Analyze the physical demands of the operation and implement measures to minimize strain on workers. This could involve providing ergonomic tools or adjusting work schedules to reduce fatigue.
Measuring Success: Key Performance Indicators (KPIs)
To effectively track the impact of optimization efforts, establishing relevant KPIs is crucial. These could include:
- Cycle Time: The overall time taken to complete the entire operation. A reduction in cycle time is a clear indicator of success.
- Throughput: The number of units produced per hour or per day. Improvements in throughput represent higher productivity.
- Defect Rate: The percentage of defective units produced. A lower defect rate indicates improved quality control.
- Overall Equipment Effectiveness (OEE): A comprehensive measure of machine efficiency, incorporating availability, performance, and quality.
- Worker Satisfaction: Measures of worker morale and job satisfaction. A happy and productive workforce contributes to improved efficiency.
Addressing Potential Challenges in Optimization
Implementing optimization strategies can present certain challenges:
- Initial Investment: Implementing some strategies, such as automation or machine upgrades, requires significant upfront investment. Conduct a thorough cost-benefit analysis before committing to such changes.
- Resistance to Change: Workers may resist changes to established processes. Proper communication and training are crucial to address concerns and foster acceptance.
- Unforeseen Complications: Implementing new technologies or processes may reveal unforeseen complications. Be prepared for potential setbacks and adjust strategies accordingly.
- Data Acquisition and Analysis: Accurate data is critical for successful optimization. Implementing a robust data collection and analysis system is essential.
Conclusion: Continuous Improvement in a 3-Minute World
A seemingly insignificant 3-minute worker-machine operation holds immense potential for optimization. By meticulously analyzing the process, identifying bottlenecks, and strategically implementing improvement strategies, businesses can significantly enhance productivity, reduce costs, and improve overall efficiency. Remember that continuous improvement is key. Regularly reviewing the process, monitoring KPIs, and adapting strategies as needed are crucial for maintaining optimal performance in a dynamic operational environment. This iterative approach, focusing on both technological advancements and human factors, ensures sustainable efficiency and long-term success. The 3-minute operation, once optimized, can become a model of streamlined efficiency, setting a benchmark for other processes within the organization.
Latest Posts
Latest Posts
-
To Kill A Mockingbird Summary Each Chapter
Mar 10, 2025
-
Unit 6a The Nature Of Waves Practice Problems Answer Key
Mar 10, 2025
-
Nos Van A Servir El Cafe
Mar 10, 2025
-
Which Statements Characterize Spanish Settlement In Texas
Mar 10, 2025
-
The Narrow Road To The Deep North Basho Summary
Mar 10, 2025
Related Post
Thank you for visiting our website which covers about A Worker-machine Operation Was Found To Involve 3.0 Miuntes . We hope the information provided has been useful to you. Feel free to contact us if you have any questions or need further assistance. See you next time and don't miss to bookmark.