A Workpiece Clamp Should Be Rated
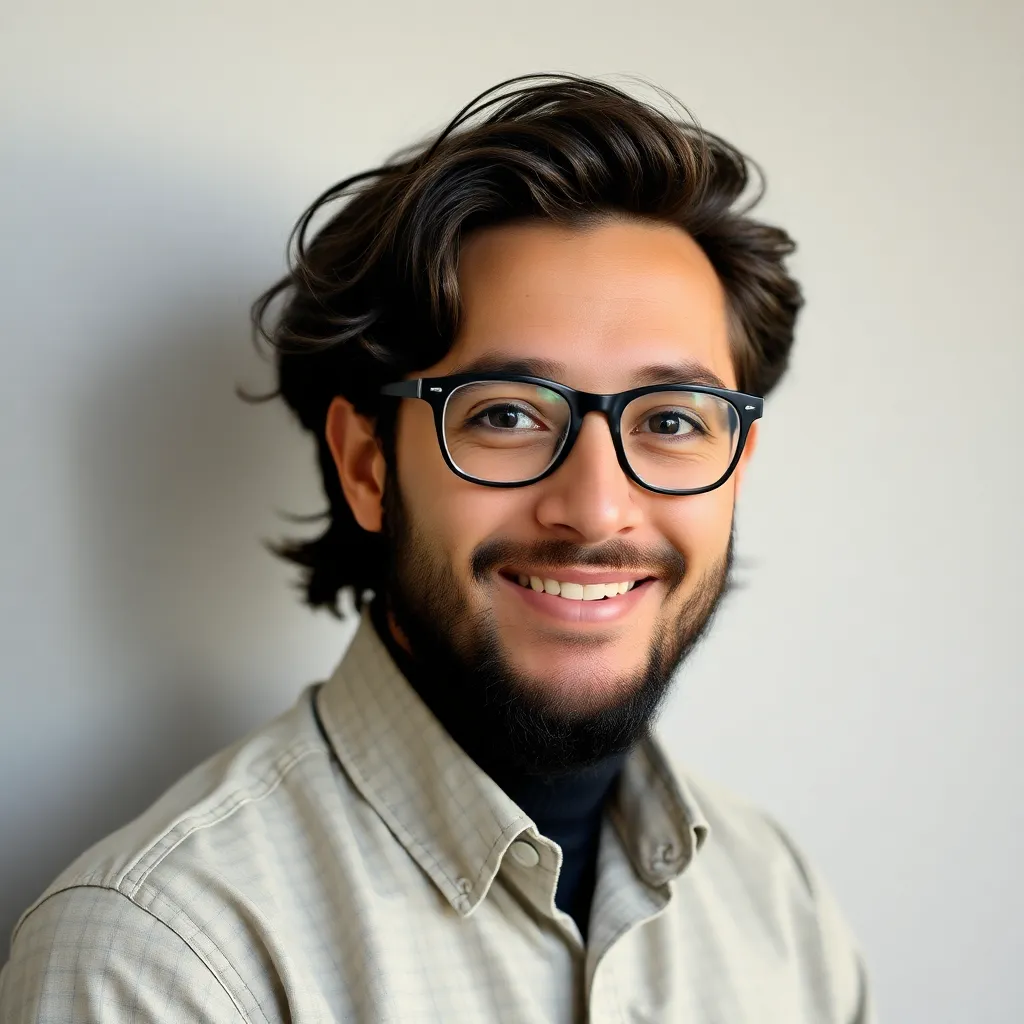
Onlines
May 12, 2025 · 6 min read
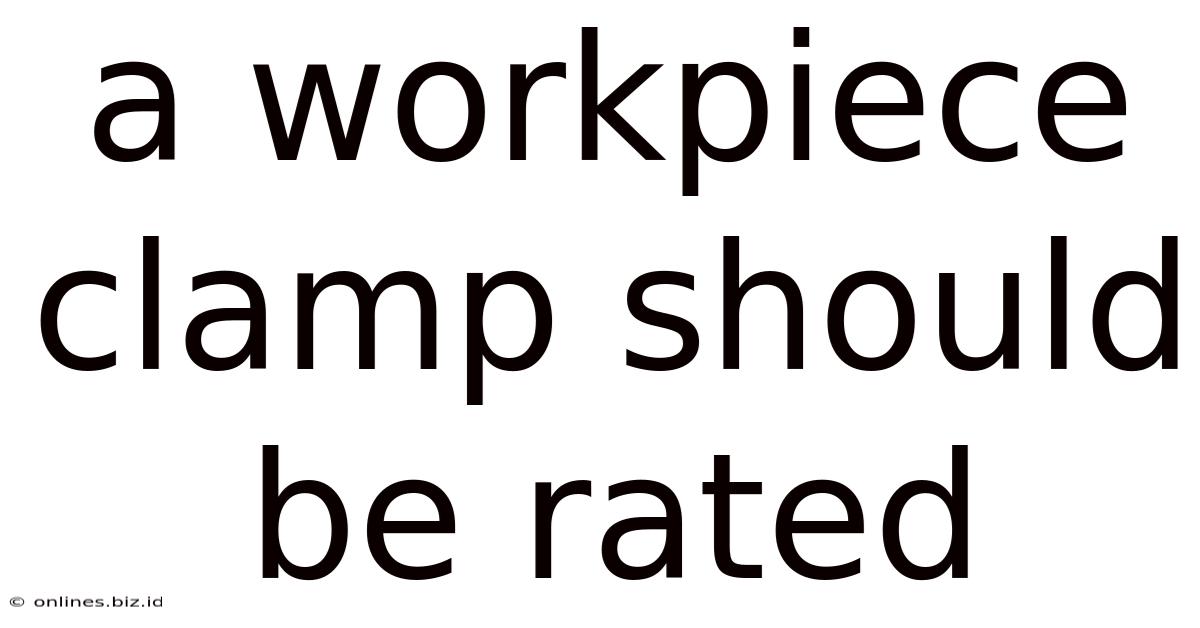
Table of Contents
A Workpiece Clamp Should Be Rated: A Comprehensive Guide to Selecting the Right Clamp for Your Needs
Choosing the right workpiece clamp is crucial for ensuring safety, efficiency, and the quality of your work. A poorly chosen clamp can lead to workpiece damage, injury, or even project failure. This comprehensive guide delves into the critical rating factors you should consider when selecting a workpiece clamp, ensuring you make the best choice for your specific application.
Understanding Workpiece Clamp Ratings: What to Look For
Workpiece clamps are rated based on several key factors, each impacting their suitability for different applications. Ignoring these ratings can lead to dangerous situations and compromised work quality. Let's explore the essential ratings and what they signify:
1. Clamping Force (Holding Capacity):
This is arguably the most crucial rating. Clamping force, typically measured in pounds (lbs) or kilograms (kg), indicates the maximum pressure the clamp can exert on the workpiece. This pressure is critical for securely holding the workpiece in place during machining, welding, assembly, or other operations. Choosing a clamp with insufficient clamping force risks the workpiece shifting, leading to inaccurate work or injury.
- Consider the material and size of your workpiece: Larger, denser workpieces require significantly higher clamping force. Soft materials may require less clamping force to avoid damage.
- Account for vibration or shock: If your application involves vibration or impact, you'll need a clamp with a higher clamping force to maintain a secure hold.
- Safety margin: Always select a clamp with a clamping force exceeding your estimated needs – a safety margin is crucial.
2. Throat Depth:
The throat depth refers to the maximum distance between the clamp's jaws and the base. This determines the maximum workpiece thickness you can clamp. Choosing a clamp with insufficient throat depth will prevent you from securing your workpiece properly.
- Measure your workpiece thickness: Accurate measurement is essential to ensure the clamp's throat depth is sufficient.
- Consider future projects: If you anticipate clamping thicker workpieces in the future, choose a clamp with a greater throat depth to avoid limitations.
3. Jaw Capacity/Opening:
The jaw capacity or opening represents the maximum distance the jaws can open. This determines the maximum size of the workpiece you can clamp. Inadequate jaw capacity will prevent you from clamping the workpiece securely.
- Measure the widest dimension of your workpiece: This will determine the minimum required jaw capacity.
- Account for variations: Consider variations in workpiece size to ensure the clamp can accommodate all dimensions.
4. Jaw Material and Design:
The material and design of the jaws significantly impact the clamp's performance and durability. Different jaw materials offer varied properties:
- Steel jaws: Offer exceptional strength and durability, ideal for heavy-duty applications.
- Soft jaws: Made from softer materials like aluminum or plastic, these protect workpiece surfaces from damage during clamping. They are essential for delicate or easily marred materials.
- Jaw design: The shape and design of the jaws influence how well they grip different workpiece shapes. Consider clamping surfaces such as flat, round, or irregular shapes. Specialized jaws may be necessary for optimal clamping.
5. Body Material and Construction:
The clamp's body material influences its durability, strength, and resistance to wear. Common materials include:
- Steel: Offers superior strength and resistance to deformation, ideal for heavy-duty applications.
- Aluminum: Lighter than steel but still strong, offering a good balance of strength and weight.
- Cast iron: Provides excellent rigidity and vibration damping properties.
The construction quality also plays a role. Look for well-built clamps with robust construction, free from flaws, and smooth operation.
6. Swivel Capabilities:
Some clamps offer swiveling jaws, enabling flexible clamping of workpieces at various angles. This is particularly beneficial when dealing with irregularly shaped or angled workpieces. Consider the need for swiveling capabilities based on your application requirements.
7. Adjustment Mechanism:
The adjustment mechanism determines how easily you can adjust the clamp's gripping force and position. Common mechanisms include:
- Screw-type: Simple, reliable, and widely used.
- Lever-type: Offers faster clamping and adjustment.
- Quick-release mechanisms: Ideal for rapid clamping and unclamping.
The choice depends on your preference and the speed of adjustment required.
8. Safety Features:
Safety is paramount. Consider clamps with safety features such as:
- Protective coatings: To prevent corrosion and accidental injury.
- Ergonomic handles: For comfortable and safe operation.
- Overload protection: Preventing damage to the clamp and potential injury.
9. Size and Weight:
The clamp's size and weight influence its portability and suitability for different applications. Larger clamps offer greater clamping force and capacity but are less portable. Smaller clamps are more portable but may have lower capacity.
Selecting the Right Clamp for Your Application: A Step-by-Step Guide
Selecting the correct clamp for your application involves a methodical approach:
- Identify the workpiece material and dimensions: Measure the workpiece's thickness, width, and length. Note any irregular shapes or features.
- Determine the clamping force required: Consider the workpiece material, size, and the forces involved during the process (machining, welding, etc.). Always add a safety margin.
- Assess the throat depth needed: Ensure the clamp's throat depth is sufficient to accommodate the workpiece thickness.
- Choose the appropriate jaw capacity: Select a clamp with a jaw capacity that comfortably accommodates the workpiece's dimensions.
- Select the correct jaw material: Opt for steel jaws for robust applications or soft jaws to protect delicate workpieces.
- Consider swivel capabilities: If required, choose a clamp with swiveling jaws for flexible clamping.
- Select the desired adjustment mechanism: Consider the speed and ease of adjustment needed.
- Verify safety features: Look for protective coatings, ergonomic handles, and overload protection.
- Evaluate size and weight: Balance portability with clamping capacity.
- Check for certifications and compliance: Ensure the clamp meets relevant safety standards and regulations.
Beyond the Ratings: Other Crucial Factors
While ratings provide essential information, other factors significantly impact clamp selection:
- Durability and longevity: Choose a clamp from a reputable manufacturer known for producing high-quality, durable products.
- Ease of use: Select a clamp with an intuitive design and smooth operation.
- Maintenance requirements: Consider the clamp's maintenance requirements and ensure you can easily maintain it.
- Cost: Balance cost with performance and durability. A more expensive, high-quality clamp may offer long-term cost savings compared to cheaper, less durable options.
- Availability of spare parts: This is crucial for long-term usability.
Conclusion: The Importance of Proper Clamp Selection
Selecting a correctly rated workpiece clamp is not just a matter of convenience; it's a critical aspect of safety and productivity. By carefully considering the factors discussed in this guide, you can ensure you choose the right clamp for your application, minimizing the risk of accidents, maximizing efficiency, and achieving the highest quality results in your work. Remember, a well-chosen clamp is an investment in your safety and the success of your projects. Don't compromise on quality – choose wisely.
Latest Posts
Related Post
Thank you for visiting our website which covers about A Workpiece Clamp Should Be Rated . We hope the information provided has been useful to you. Feel free to contact us if you have any questions or need further assistance. See you next time and don't miss to bookmark.