Acc 311 Module 4 Problem Set
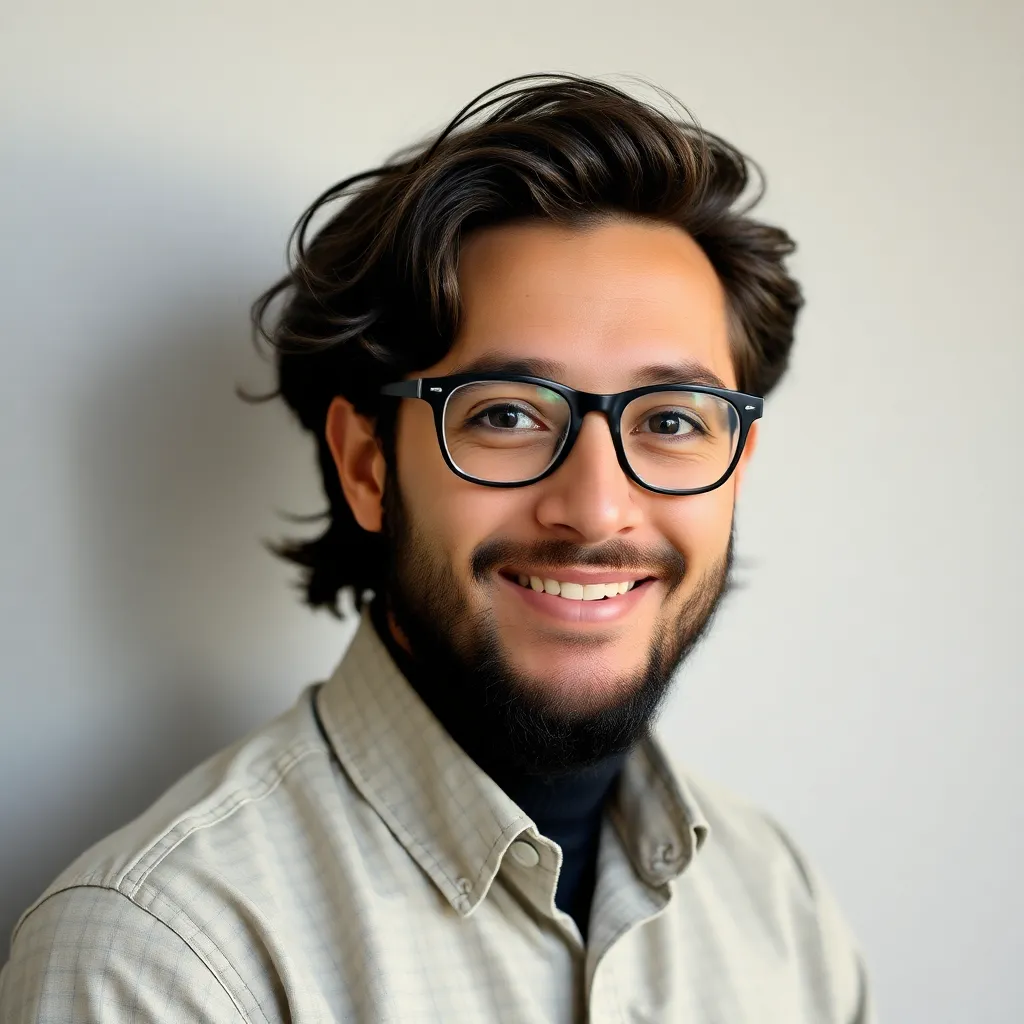
Onlines
Mar 21, 2025 · 5 min read
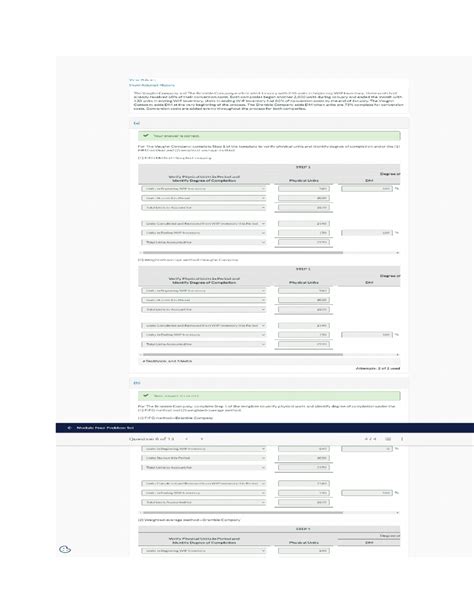
Table of Contents
ACC 311 Module 4 Problem Set: A Comprehensive Guide
Accounting can be challenging, and mastering concepts like those covered in ACC 311 Module 4 requires diligent effort and a clear understanding. This module often delves into crucial topics such as cost accounting, job order costing, and process costing. This comprehensive guide will break down common problem sets encountered in ACC 311 Module 4, providing detailed explanations and practical examples to solidify your understanding.
Understanding Cost Accounting Fundamentals
Before tackling specific problems, let's review the core principles. Cost accounting is a specialized field of accounting that focuses on tracking and analyzing costs associated with production or providing services. Its purpose is to provide management with information for making informed decisions regarding pricing, production, and profitability. Key concepts within cost accounting include:
1. Direct Costs:
These are costs that can be directly traced to a specific product or service. Examples include:
- Direct Materials: Raw materials that become part of the finished product.
- Direct Labor: Wages paid to employees directly involved in production.
2. Indirect Costs (Overhead):
These are costs that cannot be directly traced to a specific product or service and are allocated instead. Examples include:
- Factory Rent: Cost of renting the production facility.
- Utilities: Electricity, gas, and water used in the factory.
- Depreciation on Equipment: The allocation of the cost of factory equipment over its useful life.
- Supervisory Salaries: Salaries paid to supervisors overseeing production.
3. Cost Behavior:
Understanding how costs behave in relation to changes in activity levels is critical. Costs can be classified as:
- Variable Costs: Costs that change in direct proportion to changes in activity levels (e.g., direct materials).
- Fixed Costs: Costs that remain constant regardless of activity levels (e.g., rent, salaries).
- Mixed Costs: Costs that contain both fixed and variable components (e.g., utilities).
Job Order Costing: A Detailed Walkthrough
Job order costing is a cost accounting system used to track costs for individual projects or jobs. This is particularly useful for companies producing unique or customized products or services. Each job is treated as a separate cost center, and costs are accumulated for each job throughout its lifecycle.
Steps Involved in Job Order Costing:
- Identify the Job: Assign a unique job number to each project or job.
- Accumulate Direct Costs: Track all direct materials and direct labor costs associated with the job.
- Allocate Overhead Costs: Assign indirect costs to the job using a predetermined overhead rate. This rate is typically calculated by dividing estimated overhead costs by an estimated activity base (e.g., direct labor hours, machine hours).
- Calculate Total Job Cost: Add together direct materials, direct labor, and allocated overhead costs to determine the total cost of the job.
- Cost of Goods Sold: Once the job is completed, its cost is transferred to the Cost of Goods Sold account.
Example Problem:
Let's assume a custom furniture maker, "Wood Wonders," completed Job #123. The following costs were incurred:
- Direct Materials: $1,000
- Direct Labor: $500 (50 hours at $10/hour)
- Predetermined Overhead Rate: $15 per direct labor hour
Calculation:
- Overhead Costs: 50 hours * $15/hour = $750
- Total Job Cost: $1,000 (Direct Materials) + $500 (Direct Labor) + $750 (Overhead) = $2,250
Therefore, the total cost of Job #123 is $2,250.
Process Costing: A Different Approach
Process costing is used when a company produces large quantities of identical products or services. Unlike job order costing, costs are tracked for the entire production process rather than for individual jobs. Costs are then averaged across all units produced.
Steps in Process Costing:
- Summarize Costs: Track all direct materials, direct labor, and overhead costs incurred during the period.
- Calculate Equivalent Units: Determine the equivalent number of completed units based on the stage of completion of partially finished goods. This is crucial for accurate cost allocation.
- Calculate Cost per Equivalent Unit: Divide total costs by the number of equivalent units.
- Assign Costs to Units: Allocate the cost per equivalent unit to finished goods and work in process (WIP) inventory.
Example Problem:
Let's say "Perfect Pies," a bakery, produced 1,000 pies in a month. The following costs were incurred:
- Direct Materials: $2,000
- Direct Labor: $1,000
- Overhead Costs: $500
Calculation:
- Total Costs: $2,000 + $1,000 + $500 = $3,500
- Cost per Unit: $3,500 / 1,000 units = $3.50 per pie
Therefore, the cost of each pie is $3.50.
Advanced Concepts and Problem Solving Strategies
ACC 311 Module 4 often includes more complex problems involving:
- Reconciling Cost Flows: Tracking the flow of costs through various accounts (e.g., Work in Process, Finished Goods, Cost of Goods Sold).
- Variance Analysis: Comparing actual costs to budgeted costs to identify areas for improvement.
- Multiple Production Departments: Allocating overhead costs across multiple departments.
- Weighted-Average Method vs. FIFO Method: Choosing the appropriate method for calculating equivalent units in process costing.
Tips for Success:
- Thoroughly understand the definitions of all key terms.
- Practice, practice, practice. Work through numerous problems to build your understanding and problem-solving skills.
- Use a systematic approach. Organize your work clearly and meticulously, ensuring that all calculations are accurate.
- Break down complex problems into smaller, manageable steps.
- Utilize visual aids such as charts and tables. This can help you organize information and visualize cost flows.
- Seek help when needed. Don't hesitate to ask your instructor or classmates for clarification if you are struggling with a particular concept or problem.
- Review previous modules. Many concepts in Module 4 build upon foundations laid in earlier modules.
Common Mistakes to Avoid
- Incorrectly classifying costs: Carefully distinguish between direct and indirect costs.
- Using the wrong overhead allocation method: Ensure the chosen method is appropriate for the situation.
- Errors in calculating equivalent units: Accurate calculation of equivalent units is crucial in process costing.
- Ignoring the impact of beginning and ending work in process inventory: These inventories affect the calculation of cost per equivalent unit.
- Failing to account for spoilage and rework: These factors can significantly impact the cost of production.
Expanding Your Knowledge
Beyond the core concepts, explore additional resources to deepen your understanding. Consider researching different overhead allocation methods (e.g., plantwide overhead rate, departmental overhead rates), variance analysis techniques, and the implications of different costing systems for managerial decision-making. This broader perspective will enhance your ability to tackle complex problems within the framework of ACC 311 Module 4 and beyond.
By diligently studying these concepts, working through practice problems, and seeking clarification when necessary, you can successfully navigate the challenges of ACC 311 Module 4 and build a solid foundation in cost accounting. Remember, consistent effort and a methodical approach are key to mastering this important subject.
Latest Posts
Latest Posts
-
Investigation Mitosis And Cancer Answer Key
Mar 22, 2025
-
1 2 Additional Practice Transformations Of Functions
Mar 22, 2025
-
Our Customer Retention Rate Has Decreased
Mar 22, 2025
-
Marcos Esta Pidiendo El Folleto Turistico
Mar 22, 2025
-
Which Of These Choices Is Considered An Environmental Cost
Mar 22, 2025
Related Post
Thank you for visiting our website which covers about Acc 311 Module 4 Problem Set . We hope the information provided has been useful to you. Feel free to contact us if you have any questions or need further assistance. See you next time and don't miss to bookmark.