Acct 2302 -23650 Exam 1: Chapters 13-16
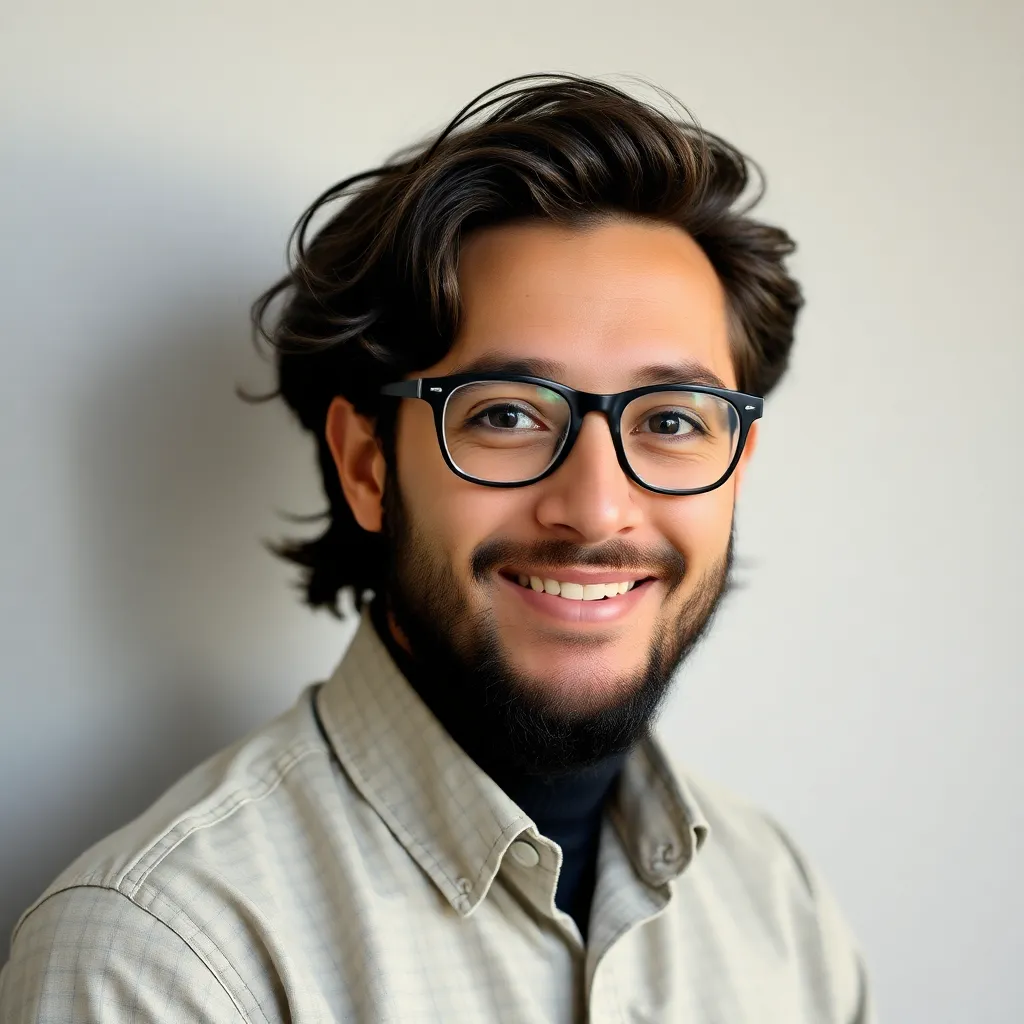
Onlines
Mar 03, 2025 · 6 min read
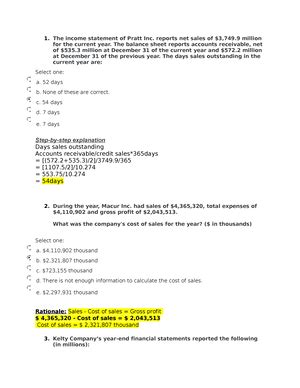
Table of Contents
ACCT 2302-23650 Exam 1: Mastering Chapters 13-16
This comprehensive guide is designed to help you ace your ACCT 2302-23650 Exam 1, covering the crucial material from Chapters 13-16. We'll break down key concepts, provide practical examples, and offer effective study strategies to maximize your understanding and performance. Remember to consult your textbook and lecture notes for specific details relevant to your course.
Chapter 13: Cost-Volume-Profit (CVP) Analysis
This chapter forms the bedrock of managerial accounting. Understanding CVP analysis is essential for effective decision-making. Let's delve into the core components:
13.1: Understanding CVP Relationships
CVP analysis examines the relationship between costs, volume, and profit. It helps businesses predict profits at various sales volumes, understand the impact of cost changes, and make informed decisions regarding pricing and production. Key terms to master include:
-
Contribution Margin: This is the revenue remaining after deducting variable costs. It represents the amount available to cover fixed costs and contribute to profit. The formula is: Sales Revenue - Variable Costs = Contribution Margin.
-
Break-Even Point: The point where total revenue equals total costs (both fixed and variable), resulting in zero profit or loss. This is a crucial metric for businesses to understand their minimum sales required for survival. It can be calculated using several methods, including the formula: Break-Even Point (in units) = Fixed Costs / Contribution Margin per Unit.
-
Margin of Safety: This indicates the cushion a company has between its actual sales and the break-even point. A higher margin of safety indicates less risk. The formula is: Actual Sales - Break-Even Sales = Margin of Safety.
13.2: Applications of CVP Analysis
CVP analysis has numerous practical applications:
-
Pricing Decisions: Understanding the contribution margin helps determine optimal pricing strategies to maximize profit.
-
Sales Mix Analysis: For businesses selling multiple products, CVP analysis can help determine the optimal sales mix to achieve desired profit levels.
-
Budgeting and Forecasting: CVP analysis is a key component of budgeting and forecasting, allowing businesses to predict future performance based on different sales scenarios.
-
Cost Control: By understanding the impact of variable and fixed costs on profit, businesses can implement cost control measures to improve profitability.
13.3: Assumptions and Limitations of CVP Analysis
It's crucial to understand that CVP analysis relies on certain assumptions:
-
Linearity: It assumes a linear relationship between costs and volume. In reality, costs may not always be perfectly linear.
-
Constant Sales Price: It assumes a constant sales price per unit. Price changes can significantly impact the analysis.
-
Constant Costs: It assumes fixed costs remain constant within a relevant range. However, fixed costs can change due to capacity limitations.
Chapter 14: Job Order Costing
Job order costing is a costing method used to assign costs to individual projects or jobs. This is particularly relevant for businesses that produce unique or customized products or services.
14.1: The Job Order Costing System
This system tracks costs for each individual job. Key steps include:
-
Cost Accumulation: Gathering direct materials, direct labor, and manufacturing overhead costs for each job.
-
Cost Assignment: Assigning these accumulated costs to specific jobs.
-
Cost Reconciliation: Ensuring that the total costs accumulated are accurately reflected in the final job cost.
14.2: Direct Materials, Direct Labor, and Manufacturing Overhead**
Understanding the different cost categories is crucial:
-
Direct Materials: Materials directly traceable to specific jobs.
-
Direct Labor: Labor costs directly involved in producing the job.
-
Manufacturing Overhead: Indirect costs related to production, such as factory rent, utilities, and depreciation. These costs are allocated to jobs using a predetermined overhead rate. The formula is typically: Predetermined Overhead Rate = Estimated Manufacturing Overhead Costs / Estimated Activity Base. Common activity bases include direct labor hours or machine hours.
14.3: Applying Overhead Costs
Overhead costs are allocated to jobs using the predetermined overhead rate. This allows for cost assignment even before the actual overhead costs are known. Any difference between the actual and applied overhead is known as overhead variance and is analyzed separately.
14.4: Cost of Goods Sold (COGS) and Work-in-Process (WIP)**
-
Work-in-Process (WIP): The cost of partially completed jobs.
-
Cost of Goods Sold (COGS): The cost of goods that have been completed and sold.
Chapter 15: Process Costing
Process costing is another costing method, but unlike job order costing, it's used for mass production of identical or similar products.
15.1: The Process Costing System
This system tracks costs for each production department or process rather than individual jobs. The costs are then allocated to the units produced.
15.2: Cost Flows in a Process Costing System**
Costs flow through different stages:
-
Beginning Work-in-Process (WIP): Costs from previous periods.
-
Costs Added During the Period: Direct materials, direct labor, and manufacturing overhead costs incurred during the period.
-
Ending Work-in-Process (WIP): Costs of partially completed units at the end of the period.
-
Cost of Goods Transferred Out: Costs of completed units transferred to finished goods.
15.3: Equivalent Units**
This is a crucial concept in process costing. Equivalent units represent the number of fully completed units that could have been produced given the amount of work done on both completed and partially completed units. There are several methods to calculate equivalent units, including the FIFO and Weighted-Average methods.
15.4: Cost per Equivalent Unit**
This is calculated by dividing the total costs by the equivalent units. It represents the cost of producing one complete unit.
15.5: Cost Reconciliation**
Similar to job order costing, reconciliation is important in process costing to ensure accurate cost assignment and tracking.
Chapter 16: Activity-Based Costing (ABC)
Activity-based costing is a more sophisticated costing method that assigns overhead costs based on the activities that consume those costs. It's particularly useful for businesses with diverse product lines or complex operations.
16.1: Traditional Costing vs. ABC**
Traditional costing systems often use a single overhead rate, which can lead to cost distortions, particularly for products requiring different levels of resources. ABC addresses this by assigning costs based on specific activities.
16.2: Activity Cost Pools**
Overhead costs are grouped into activity cost pools based on the activities that drive them. Examples include machine setups, material handling, and quality control.
16.3: Activity Rates**
An activity rate is calculated for each activity cost pool. This rate represents the cost of each activity. The formula is: Activity Rate = Total Cost of Activity / Total Activity Driver. The activity driver is a measure of the activity, such as number of setups, number of materials handled, etc.
16.4: Assigning Costs to Products**
Costs are assigned to products based on their consumption of activities. Products that require more of a particular activity will be assigned a higher cost for that activity.
16.5: Advantages and Disadvantages of ABC**
Advantages: Provides more accurate product costing, facilitates better management decisions, and allows for improved cost control.
Disadvantages: Can be more complex and time-consuming than traditional costing, requires significant data collection, and might not be cost-effective for all businesses.
Exam Preparation Strategies:
-
Review your lecture notes and textbook: Ensure you understand all key concepts, formulas, and terminology.
-
Practice problems: Work through numerous practice problems to solidify your understanding and identify areas where you need further study.
-
Create flashcards: Use flashcards to memorize key terms and formulas.
-
Form a study group: Collaborating with peers can help you clarify doubts and reinforce your learning.
-
Get adequate rest: Ensure you're well-rested before the exam.
-
Manage your time effectively: Allocate sufficient time to each chapter based on its weight in the exam.
By diligently following this guide and employing effective study strategies, you will significantly increase your chances of success in your ACCT 2302-23650 Exam 1. Remember to stay organized, practice consistently, and utilize all available resources to achieve your academic goals. Good luck!
Latest Posts
Latest Posts
-
Life Of Pi Book Summary Of Each Chapter
Mar 03, 2025
-
Demand Management Is A Strategy For Implementing Category Management
Mar 03, 2025
-
I Am Malala Chapter By Chapter Summary
Mar 03, 2025
-
What Are The Four Purposes Of Government
Mar 03, 2025
-
How Does A Preservative Facial Differ From A Corrective Facial
Mar 03, 2025
Related Post
Thank you for visiting our website which covers about Acct 2302 -23650 Exam 1: Chapters 13-16 . We hope the information provided has been useful to you. Feel free to contact us if you have any questions or need further assistance. See you next time and don't miss to bookmark.