Activity 1.1 5 Gears Pulley Drives And Sprockets Practice Problems
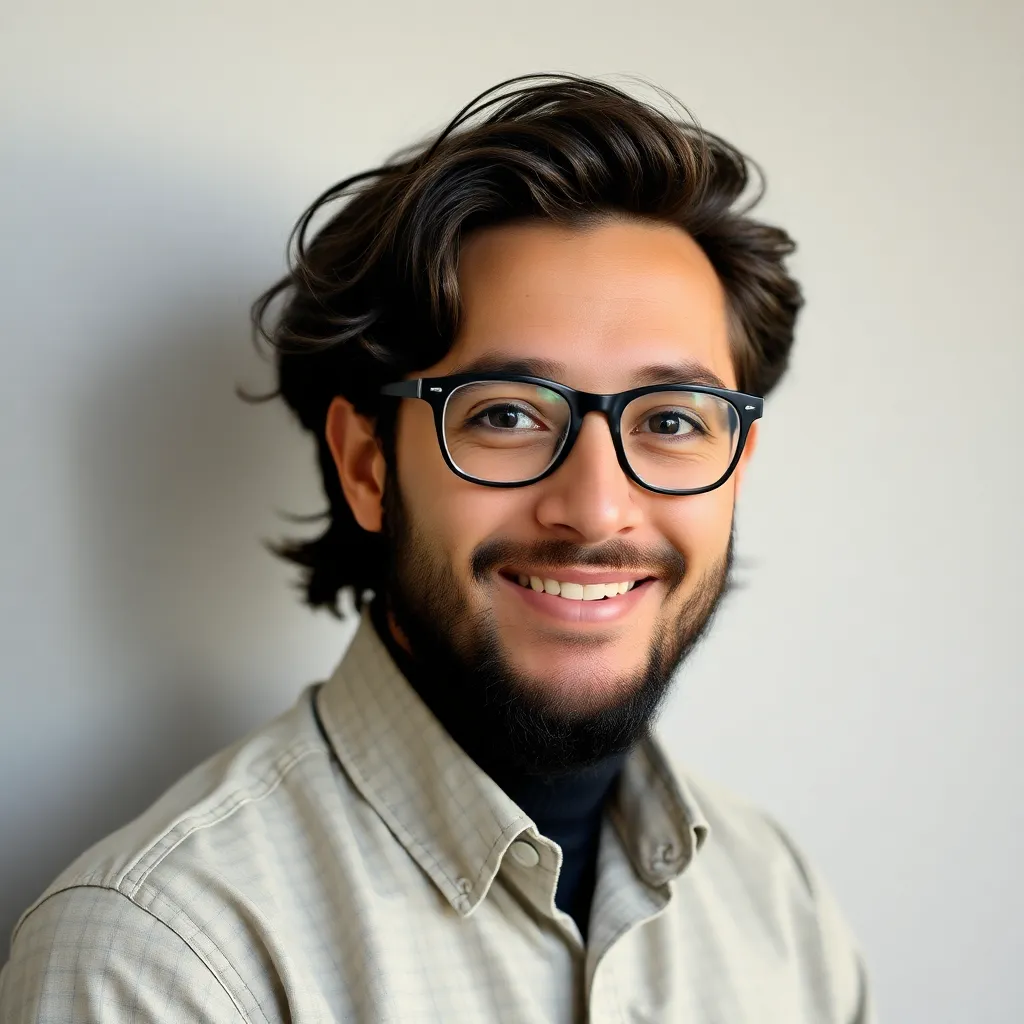
Onlines
May 08, 2025 · 6 min read
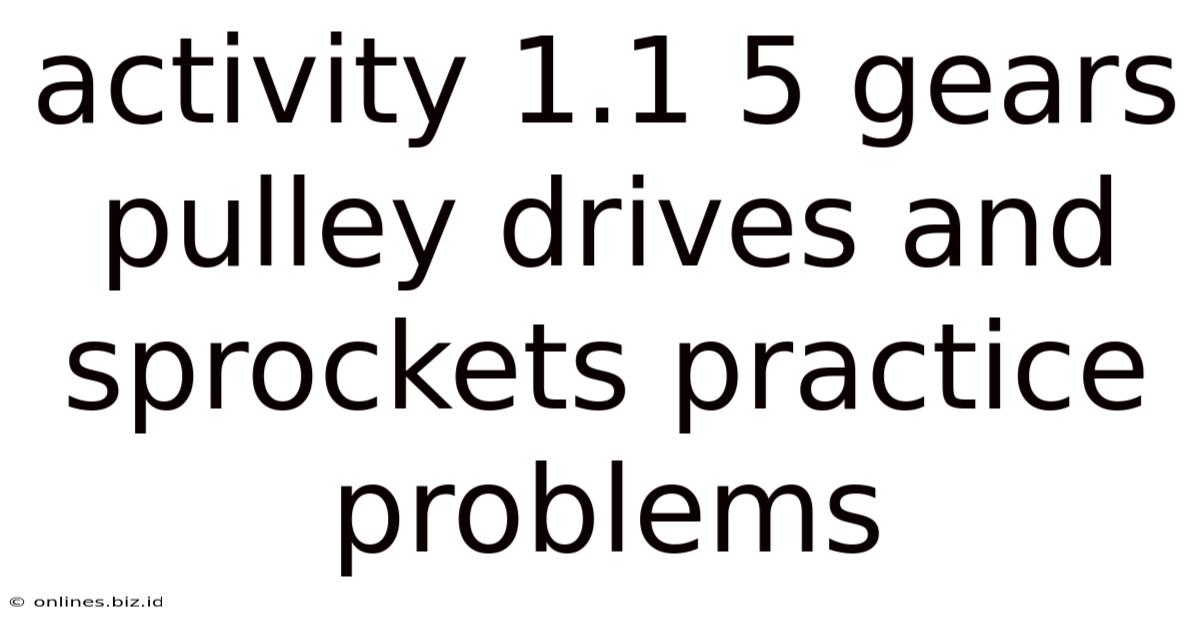
Table of Contents
Activity 1.1: 5 Gears, Pulleys, and Sprockets Practice Problems: A Deep Dive
This comprehensive guide delves into the world of gear, pulley, and sprocket systems, focusing on practical problem-solving. We'll explore the fundamental principles governing their operation and provide numerous examples to solidify your understanding. This guide is perfect for students, engineers, and anyone seeking a robust grasp of mechanical power transmission.
Understanding the Fundamentals: Gears, Pulleys, and Sprockets
Before tackling complex problems, let's establish a firm foundation in the core concepts.
Gears: The Interlocking Teeth
Gears are toothed wheels that mesh together to transmit rotational motion and torque. Their primary function is to change speed and torque, offering various ratios depending on the number of teeth. Key parameters include:
- Number of Teeth (N): Directly influences the gear ratio.
- Module (m): A measure of gear size; it's the ratio of the reference diameter to the number of teeth.
- Pitch Diameter (d): The diameter of the pitch circle, where the teeth of meshing gears contact.
- Gear Ratio (GR): The ratio of the number of teeth on the driven gear to the number of teeth on the driving gear (GR = N<sub>driven</sub> / N<sub>driving</sub>). A gear ratio greater than 1 indicates a speed reduction (increased torque), while a ratio less than 1 indicates a speed increase (reduced torque).
Pulleys: The Rotating Discs
Pulleys are simple machines that use ropes, belts, or chains to transmit power. They're often used in systems where a change in speed or direction is required. Key factors include:
- Diameter (D): Determines the speed ratio in a pulley system.
- Belt/Rope/Chain Length: Affects the overall system geometry and operation.
- Speed Ratio (SR): The ratio of the speed of the driven pulley to the speed of the driving pulley (SR = D<sub>driving</sub> / D<sub>driven</sub>). A speed ratio greater than 1 implies a speed reduction (increased torque), while a ratio less than 1 indicates speed increase (reduced torque).
Sprockets: The Chain-Driven Wheels
Sprockets are toothed wheels designed to work with chains, transferring power and motion efficiently. They are commonly found in bicycles, motorcycles, and industrial machinery. Key aspects are:
- Number of Teeth (N): Similar to gears, it dictates the speed and torque ratios.
- Pitch: The distance between corresponding points on adjacent teeth.
- Chain Length: Crucial for proper system functionality and avoiding chain slack or tension.
- Chain Speed: The linear speed of the chain.
Practice Problems: Gears
Let's delve into some illustrative problems involving gear systems:
Problem 1: A driving gear with 20 teeth meshes with a driven gear with 60 teeth. If the driving gear rotates at 120 RPM (revolutions per minute), what is the rotational speed of the driven gear?
Solution:
The gear ratio (GR) is 60/20 = 3. The rotational speed of the driven gear is the driving gear's speed divided by the gear ratio: 120 RPM / 3 = 40 RPM.
Problem 2: Two gears, A and B, are in mesh. Gear A has 30 teeth and rotates at 150 RPM. Gear B has a speed of 75 RPM. How many teeth does gear B have?
Solution:
The gear ratio (GR) is the ratio of the speeds: 150 RPM / 75 RPM = 2. Therefore, the number of teeth on Gear B is 2 * 30 teeth = 60 teeth.
Problem 3: A gear train consists of three gears: A, B, and C. Gear A has 24 teeth and rotates at 100 RPM. Gear B has 48 teeth, and Gear C has 12 teeth. Calculate the speed of Gear C.
Solution:
First, find the speed of Gear B: 100 RPM * (24/48) = 50 RPM. Then, find the speed of Gear C: 50 RPM * (48/12) = 200 RPM.
Practice Problems: Pulleys
Let's apply similar problem-solving techniques to pulley systems:
Problem 1: A driving pulley with a diameter of 20 cm rotates at 300 RPM. It's connected to a driven pulley with a diameter of 10 cm. What is the rotational speed of the driven pulley?
Solution:
The speed ratio (SR) is 20 cm / 10 cm = 2. The driven pulley's speed is the driving pulley's speed multiplied by the speed ratio: 300 RPM * 2 = 600 RPM.
Problem 2: Two pulleys are connected by a belt. The driving pulley has a diameter of 30 cm and rotates at 100 RPM. The driven pulley rotates at 200 RPM. What's the diameter of the driven pulley?
Solution:
The speed ratio (SR) is 100 RPM / 200 RPM = 0.5. The diameter of the driven pulley is the diameter of the driving pulley divided by the speed ratio: 30 cm / 0.5 = 60 cm.
Practice Problems: Sprockets
Now, let's tackle problems involving sprocket systems:
Problem 1: A driving sprocket with 15 teeth rotates at 150 RPM. It's connected to a driven sprocket with 45 teeth. Calculate the speed of the driven sprocket.
Solution:
The gear ratio (similar to sprocket ratio) is 45/15 = 3. The driven sprocket's speed is 150 RPM / 3 = 50 RPM.
Problem 2: A bicycle has a front sprocket with 48 teeth and a rear sprocket with 16 teeth. If the cyclist pedals at 80 RPM, what is the rotational speed of the rear wheel (assuming the rear wheel is directly connected to the rear sprocket)?
Solution:
The gear ratio is 48/16 = 3. The rear wheel speed is 80 RPM * 3 = 240 RPM.
Advanced Concepts and Considerations
The problems above represent simplified scenarios. Real-world applications often involve additional factors such as:
- Friction: Friction in the bearings and between meshing components reduces efficiency.
- Slippage: Belts and chains can experience slippage, affecting the accuracy of speed and torque transmission.
- Efficiency: The efficiency of a system is the ratio of output power to input power. Losses due to friction and slippage reduce efficiency.
- Backlash: The clearance between meshing gears can cause backlash, leading to inaccuracies in position control.
- Gear Tooth Wear: Over time, gear teeth can wear down, impacting the accuracy and longevity of the system.
Troubleshooting and Optimization
Understanding potential issues and optimization strategies is crucial. Here are some key areas to consider:
- Noise: Excessive noise can indicate worn gears, misalignment, or lubrication problems.
- Vibration: Unbalanced components or misalignment can cause significant vibrations, affecting the system's lifespan.
- Overheating: Excessive friction or inadequate lubrication can lead to overheating, potentially causing damage.
- Lubrication: Proper lubrication is vital for reducing friction and extending component life.
- Maintenance: Regular inspection and maintenance are essential for identifying and addressing potential problems.
Conclusion
Mastering gear, pulley, and sprocket systems requires a thorough understanding of fundamental principles and the ability to apply them to real-world scenarios. This guide has provided a solid foundation, equipping you with the knowledge and problem-solving skills to confidently tackle a wider range of mechanical power transmission challenges. Remember to consider the factors mentioned above for a comprehensive and realistic understanding of system behavior. By consistently applying these principles and addressing potential issues proactively, you can design and maintain highly efficient and reliable mechanical systems.
Latest Posts
Latest Posts
-
How Does The Real Life Dante Differ From The Fictional Dante
May 09, 2025
-
Cpalms Hey Rock How Old Are You
May 09, 2025
-
An Article Reports That Blue Eyed People Earn Less
May 09, 2025
-
List The Companies The Interviewees Worked For
May 09, 2025
-
Nicole Is Socially Inhibited And Oversensitive To Negative Evaluation
May 09, 2025
Related Post
Thank you for visiting our website which covers about Activity 1.1 5 Gears Pulley Drives And Sprockets Practice Problems . We hope the information provided has been useful to you. Feel free to contact us if you have any questions or need further assistance. See you next time and don't miss to bookmark.