Activity 1.2 5 Mechanical System Efficiency Vex
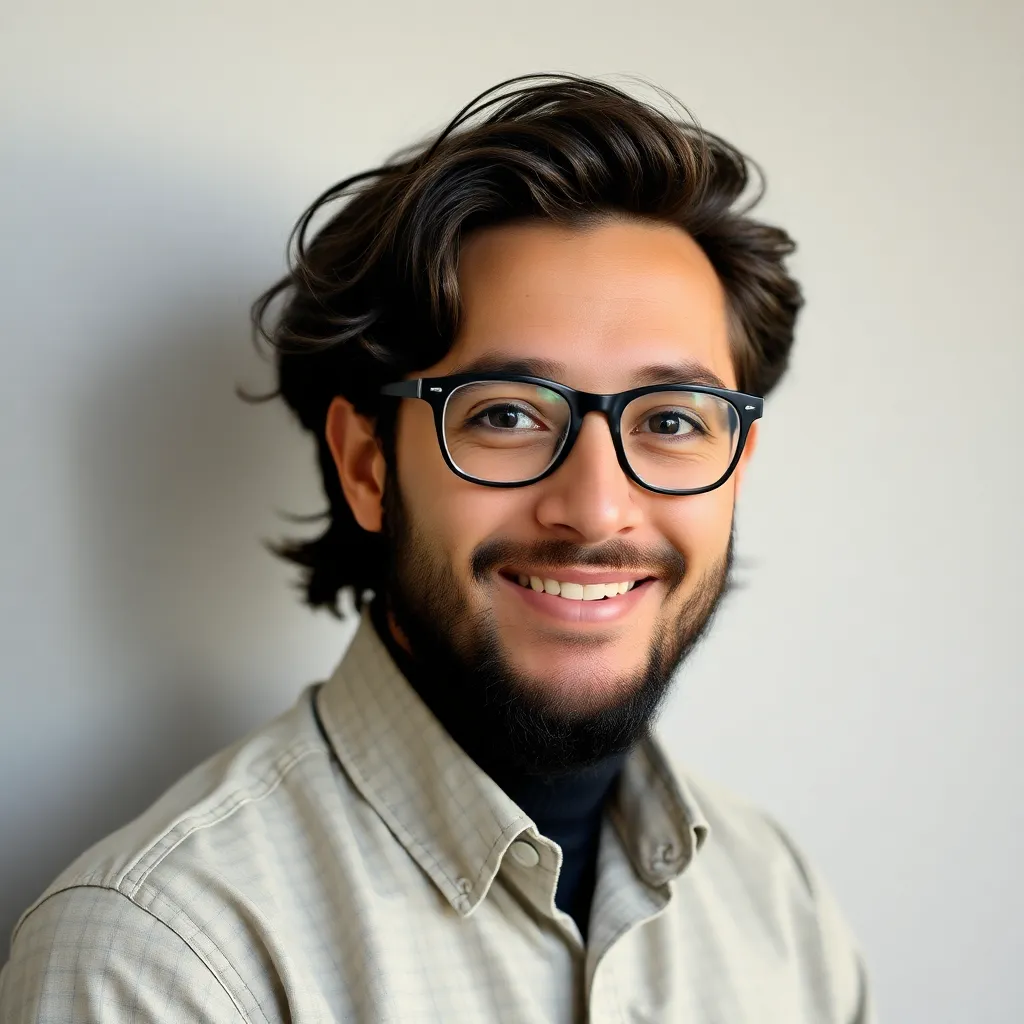
Onlines
Apr 15, 2025 · 7 min read

Table of Contents
Activity 1.2: Dissecting Mechanical System Efficiency in VEX Robotics
VEX Robotics competitions demand not only innovative designs but also highly efficient mechanical systems. Activity 1.2, often a cornerstone of introductory VEX curriculum, focuses on understanding and improving the efficiency of these systems. This article delves deep into the nuances of Activity 1.2, exploring the key concepts, practical applications, and strategies for maximizing mechanical system efficiency within the VEX Robotics framework. We'll cover everything from identifying sources of inefficiency to implementing solutions, ensuring your robot achieves peak performance.
Understanding Mechanical Efficiency in VEX
Before diving into Activity 1.2 specifics, let's establish a firm understanding of mechanical efficiency. In simple terms, mechanical efficiency is the ratio of useful work output to the total work input. In a VEX robot, this translates to how effectively the motor's energy is converted into the desired robot motion (e.g., driving, lifting, manipulating game objects). A highly efficient system minimizes energy loss due to friction, inertia, and other resistances.
Key Factors Affecting Mechanical Efficiency:
- Friction: This is a major culprit in reduced efficiency. Friction occurs between moving parts, such as gears, axles, and wheels. Minimizing friction is crucial for optimal performance.
- Gear Ratios: Selecting appropriate gear ratios is essential for balancing speed and torque. An inefficient gear ratio can lead to excessive energy loss.
- Lubrication: Proper lubrication reduces friction between moving parts, significantly improving efficiency.
- Inertia: The resistance to changes in motion. Heavier components require more energy to accelerate and decelerate, decreasing efficiency. Minimizing unnecessary weight is critical.
- Mechanical Design: Poorly designed systems, like those with misaligned components or excessive play, experience higher friction and energy loss. A robust and well-designed system is fundamental.
- Material Selection: The materials used in constructing the mechanical system influence its efficiency. Materials with lower friction coefficients are preferred.
Decoding Activity 1.2: A Practical Approach
Activity 1.2 typically involves a series of experiments and analyses designed to help students grasp these concepts practically. While the exact activities may vary slightly depending on the curriculum, the core principles remain consistent. The overall aim is to understand how different factors affect the efficiency of a simple mechanical system, often a lifting mechanism.
Typical Activity 1.2 Components:
- Motor: The power source driving the system. Often a VEX motor, providing measurable torque and speed.
- Gears: Used to modify the speed and torque of the motor. Different gear ratios are experimented with.
- Axle/Shafting: Transmits power from the motor to the load.
- Load: Represents the work being done, often a weight being lifted.
- Measurement Tools: Essential for collecting data, typically including a timer to measure time taken for the load to be lifted, a ruler or scale to measure the distance the load is lifted, and a means of measuring the motor's current draw (often an ammeter).
Step-by-Step Analysis of a Typical Activity 1.2 Experiment:
-
Baseline Measurement: The first step involves establishing a baseline. This entails measuring the time taken to lift a specific load using a particular gear ratio without any modifications. The motor's current draw is also recorded.
-
Introducing Variables: The next steps involve systematically introducing variables to observe their impact on efficiency. This might involve:
- Changing Gear Ratios: Experimenting with different gear ratios to observe the trade-off between speed and torque. A higher gear ratio increases speed but might reduce torque and potentially efficiency depending on the load and friction. A lower gear ratio provides more torque but might compromise speed.
- Altering Load Weight: Changing the weight of the load allows investigation of the system's ability to handle different levels of resistance. Heavier loads will generally decrease efficiency.
- Adding Friction: Intentionally adding friction (e.g., by applying slight pressure to the moving parts) demonstrates the negative effect of friction on efficiency.
- Lubrication: Introducing lubrication to reduce friction highlights the importance of maintaining well-lubricated parts.
-
Data Collection and Analysis: Throughout the experiments, precise data is collected, including the time taken for the load to be lifted, the distance lifted, and the current draw of the motor. This data allows calculation of the work done and the efficiency of the system.
-
Efficiency Calculation: Mechanical efficiency is calculated using the following formula:
Efficiency (%) = (Useful Work Output / Work Input) x 100
- Useful Work Output: This is the work done in lifting the load (Weight x Distance Lifted).
- Work Input: This is the energy consumed by the motor, which can be estimated by analyzing the motor's current draw and operational time. More sophisticated analysis could involve measuring the motor's power consumption directly.
-
Interpreting Results: The final stage involves analyzing the collected data and drawing conclusions. This involves identifying the factors that significantly impact efficiency and proposing solutions to improve performance.
Optimizing Mechanical System Efficiency: Practical Strategies
Activity 1.2 isn't just about understanding the theory; it's about developing practical skills for improving robot performance. Here are some key strategies for optimizing the efficiency of VEX robotic systems:
1. Minimize Friction:
- Proper Lubrication: Use appropriate lubricants designed for the materials in your system.
- Smooth Surfaces: Ensure that all moving parts have smooth surfaces to reduce friction.
- Optimized Bearings: Use high-quality bearings to minimize friction in rotating components.
- Tight Tolerances: Precisely manufactured parts with minimal play between them reduces friction.
2. Optimize Gear Ratios:
- Understanding the Load: Analyze the specific requirements of the task. If you need high speed, a higher gear ratio is appropriate, but if you need high torque, a lower gear ratio is preferred.
- Iterative Testing: Experiment with different gear ratios to determine the optimal balance between speed and torque for your specific application. Often, there's a point of diminishing returns where increasing the gear ratio doesn't proportionally increase efficiency.
3. Reduce Unnecessary Weight:
- Material Selection: Choose lightweight yet strong materials for your robot components.
- Minimalist Design: Avoid adding unnecessary components that add weight without contributing significantly to functionality.
- Component Consolidation: Combine functions where possible to reduce the number of individual components.
4. Improve Mechanical Design:
- Alignment: Ensure all components are precisely aligned to prevent binding and friction.
- Robust Construction: A well-constructed system reduces the chance of parts flexing or binding under load.
- Stiffness: Use stiff materials and structural supports to minimize flexing and energy loss during operation.
5. Employ Advanced Techniques:
- Belt and Pulley Systems: These can be more efficient than direct gear drives in certain applications, offering flexibility in gear ratio adjustments.
- Chain Drives: Similar to belt and pulley systems, chain drives can be a robust and efficient option for transferring power.
Beyond Activity 1.2: Applying Efficiency Principles to Complex VEX Robots
The principles learned in Activity 1.2 are fundamental to building highly efficient VEX robots. While the initial activity may focus on a simple lifting mechanism, these principles directly translate to more complex designs. Consider these advanced applications:
- Drivetrain Efficiency: Optimizing the drivetrain, including wheel choice, gear ratios, and motor selection, is crucial for maximizing robot speed and maneuverability.
- Manipulator Efficiency: Efficient manipulators are essential for effectively interacting with game objects. This involves careful consideration of gear ratios, link lengths, and gripping mechanisms.
- Energy Management: For longer autonomous periods, efficient energy management is vital. This involves minimizing energy consumption through optimized mechanical systems and intelligent control strategies.
- System Integration: Even the most efficient individual systems will perform poorly if not integrated effectively. This necessitates careful consideration of power distribution, communication between components, and overall system coordination.
Conclusion: Efficiency as a Competitive Advantage
Activity 1.2 serves as a crucial introduction to the concept of mechanical efficiency in VEX Robotics. By mastering the principles outlined in this activity and applying them to more complex designs, you significantly improve your robot's overall performance. High efficiency translates to increased speed, greater torque, improved maneuverability, and ultimately, a competitive advantage in VEX competitions. Remember that continuous refinement and testing are essential for optimizing efficiency and achieving peak performance. The journey from a basic understanding to expert-level efficiency is an iterative one, built on careful observation, data-driven analysis, and a commitment to continuous improvement.
Latest Posts
Latest Posts
-
A Student Drew The Following Flowchart
Apr 16, 2025
-
National Junior Honor Society Letter Of Recommendation Template
Apr 16, 2025
-
2 20 Unit Test Dynamic Earth Part 1
Apr 16, 2025
-
What Is Resource Market In Economics
Apr 16, 2025
-
Lifes Greatest Miracle Video Questions Answers
Apr 16, 2025
Related Post
Thank you for visiting our website which covers about Activity 1.2 5 Mechanical System Efficiency Vex . We hope the information provided has been useful to you. Feel free to contact us if you have any questions or need further assistance. See you next time and don't miss to bookmark.