Activity 2.2.2 Manufacturing Processes Answer Key
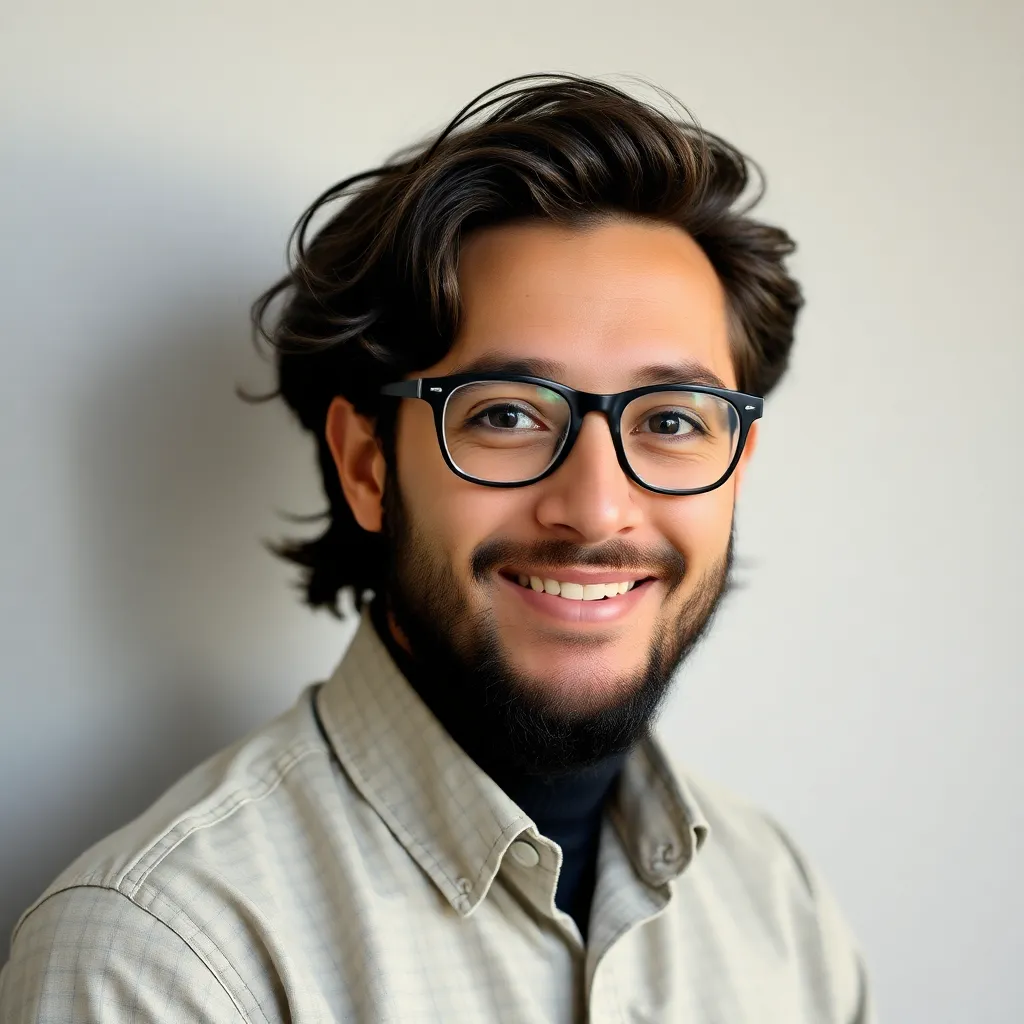
Onlines
May 02, 2025 · 5 min read

Table of Contents
I cannot provide a complete answer key for Activity 2.2.2 on manufacturing processes. This is because:
-
Copyright Restrictions: The specific activity likely belongs to a copyrighted educational resource (textbook, online course, etc.). Providing the answers would be a violation of copyright and intellectual property rights.
-
Context is Missing: I need the actual content of Activity 2.2.2 to provide answers. The activity description is insufficient for me to generate accurate responses. Different textbooks and courses will have different activities under the same title.
-
Ethical Concerns: Providing answers undermines the learning process. The purpose of activities like this is to test understanding and encourage critical thinking. Simply providing the answers removes the educational value.
However, I can offer a comprehensive overview of common manufacturing processes and the types of questions that might appear in an activity like "Activity 2.2.2 Manufacturing Processes." This should help you understand the concepts and answer your own activity.
Understanding Manufacturing Processes: A Deep Dive
Manufacturing processes encompass a wide range of techniques and technologies used to transform raw materials into finished goods. These processes can be broadly categorized, and understanding these categories is key to mastering this subject.
1. Material Removal Processes: Shaping Through Subtraction
These processes begin with a larger piece of material and remove portions to achieve the desired shape and dimensions. Examples include:
- Turning: A rotating workpiece is shaped by a cutting tool. This is used for creating cylindrical parts.
- Milling: A rotating cutting tool removes material from a stationary workpiece. Used for creating complex shapes.
- Drilling: Creating holes in a workpiece using a rotating drill bit.
- Grinding: Using abrasive materials to remove small amounts of material, achieving high precision and surface finish.
- Lapping and Honing: Fine finishing processes used to achieve extremely precise dimensions and surface smoothness.
- Electrical Discharge Machining (EDM): Using electrical sparks to erode material, enabling the creation of intricate shapes in hard materials.
Questions to Consider: What are the advantages and disadvantages of each process? What types of materials are best suited for each? What factors influence the accuracy and surface finish?
2. Material Addition Processes: Building Up the Form
These processes add material to create the final product. Popular methods include:
- Casting: Pouring molten material into a mold, allowing it to solidify into the desired shape. This includes sand casting, investment casting, die casting, and others.
- Forging: Shaping metal by applying compressive forces. This improves the material's strength and ductility. Examples include hammer forging and press forging.
- Welding: Joining two or more pieces of material by melting and fusing them together. Different welding techniques exist, including arc welding, MIG welding, TIG welding, etc.
- Additive Manufacturing (3D Printing): Creating three-dimensional objects by adding material layer by layer. Various techniques exist, like Fused Deposition Modeling (FDM), Stereolithography (SLA), Selective Laser Melting (SLM), and more.
- Extrusion: Forcing material through a die to create a continuous shape (like pipes or profiles).
Questions to Consider: What are the material limitations for each process? Which processes are best suited for mass production? How do different casting processes compare in terms of cost and precision? What are the strengths and weaknesses of additive manufacturing?
3. Material Deformation Processes: Shaping Through Change
These processes alter the shape of a material without removing or adding substantial amounts of it.
- Rolling: Reducing the thickness of a material by passing it through rollers.
- Drawing: Pulling material through a die to reduce its diameter.
- Bending: Changing the shape of a material by applying a force that causes it to flex.
- Stamping: Using a die to shape sheet metal.
Questions to Consider: What factors influence the material properties after deformation? What are the limitations of these processes in terms of achievable shapes and complexity? How does the selection of the material affect the outcome of these processes?
4. Joining Processes: Combining Components
Beyond welding, several other methods effectively join components in manufacturing.
- Bolting and Screwing: Simple, readily reversible mechanical joining methods.
- Riveting: Permanent joining using rivets.
- Adhesives: Using bonding agents to join materials.
Questions to Consider: What are the strengths and weaknesses of each joining method in terms of strength, cost, and ease of assembly? What factors influence the choice of adhesive for specific applications? What are the considerations for selecting appropriate bolt sizes and thread types?
5. Surface Finishing Processes: Enhancing Appearance and Performance
These processes improve the aesthetic qualities and functional properties of finished parts.
- Painting: Applying protective and decorative coatings.
- Plating: Depositing a thin layer of metal onto a surface for corrosion resistance or aesthetics.
- Polishing: Smoothing the surface to improve appearance and reduce friction.
- Anodizing: Creating a protective oxide layer on aluminum.
Questions to Consider: What are the various types of paint finishes? What are the properties of different plating materials? What factors determine the choice of surface finishing technique?
Addressing Potential Activity Questions
Given the broad range of manufacturing processes, "Activity 2.2.2" could encompass a variety of questions, such as:
- Matching: Match the manufacturing process to its description.
- Multiple Choice: Select the most appropriate process for a given application.
- Short Answer: Describe the advantages and disadvantages of a particular process.
- Problem Solving: Calculate the material removal rate for a specific machining operation.
- Essay: Compare and contrast two different manufacturing processes.
- Diagram: Draw and label a diagram of a specific manufacturing process.
To effectively answer your activity, carefully review the course materials focusing on the specific processes discussed. Pay close attention to the advantages, disadvantages, applications, and limitations of each method. Understanding the underlying principles behind each process will enable you to correctly answer any questions posed within the activity. Remember to utilize any provided diagrams or examples within your textbook or online learning module. Good luck!
Latest Posts
Latest Posts
-
Which Of The Following Is An Inductive Argument
May 03, 2025
-
Firms Need To Continue To Innovate Because Customer Needs
May 03, 2025
-
Summary Of Chapter 16 Of The Scarlet Letter
May 03, 2025
-
Match Each Exercise To Its Corresponding Muscle Or Muscle Group
May 03, 2025
-
A Perfect Day For A Bananafish Summary
May 03, 2025
Related Post
Thank you for visiting our website which covers about Activity 2.2.2 Manufacturing Processes Answer Key . We hope the information provided has been useful to you. Feel free to contact us if you have any questions or need further assistance. See you next time and don't miss to bookmark.