Advance Study Assignment Analysis Of An Aluminum Zinc Alloy
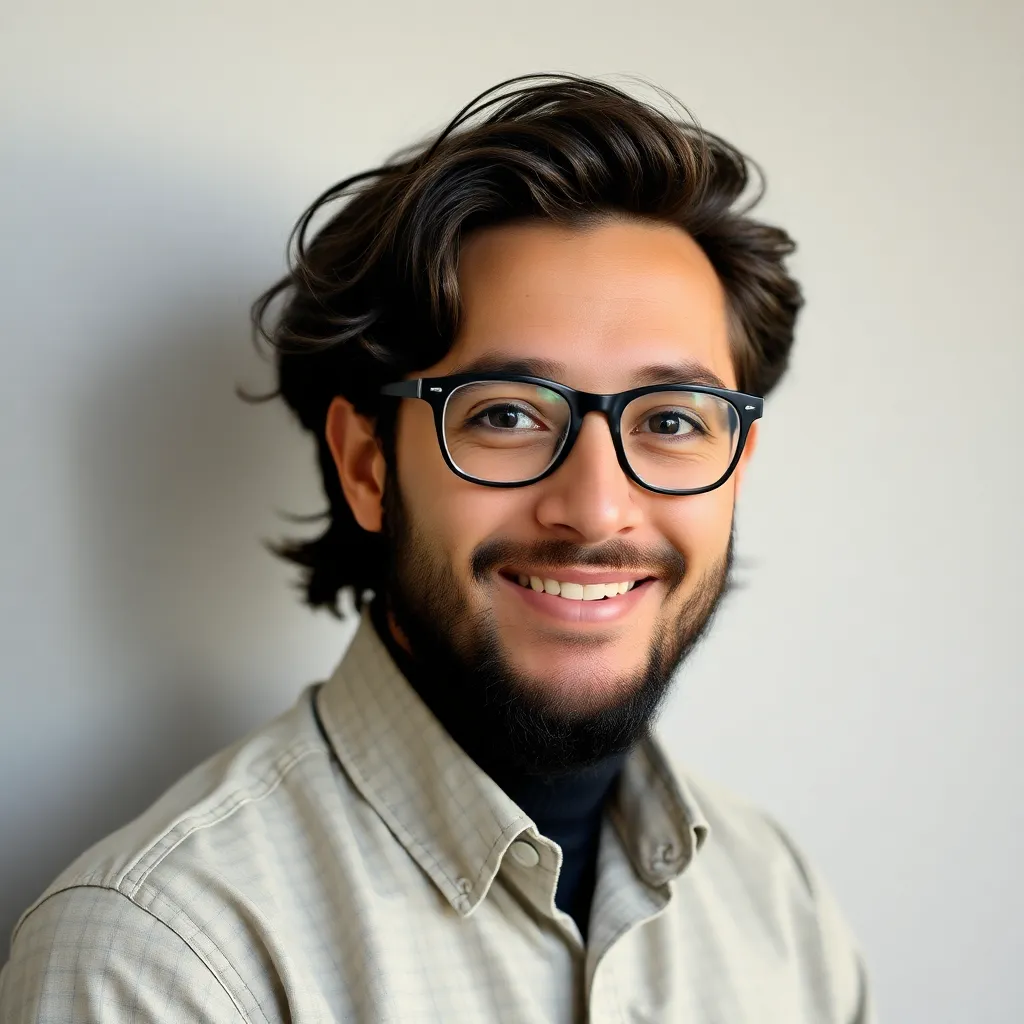
Onlines
May 09, 2025 · 6 min read
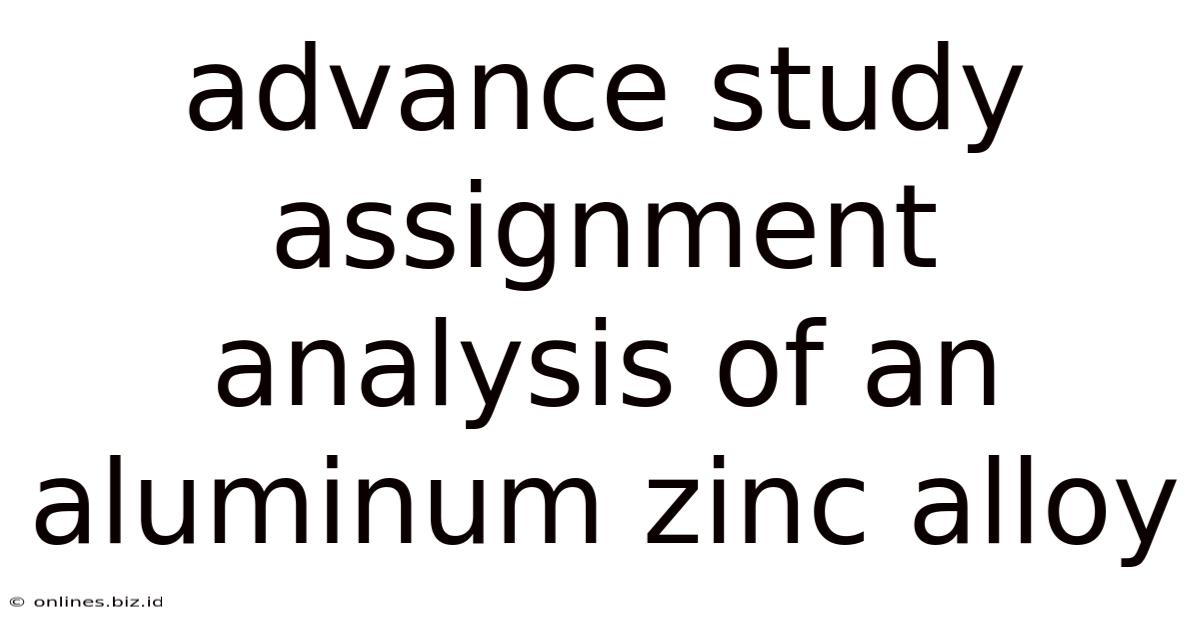
Table of Contents
Advanced Study Assignment Analysis of an Aluminum Zinc Alloy
This advanced study assignment delves into the comprehensive analysis of an aluminum zinc (Al-Zn) alloy, exploring its metallurgical properties, mechanical behavior, and potential applications. Understanding the intricacies of Al-Zn alloys requires a multifaceted approach, encompassing theoretical knowledge and practical application. This analysis will cover various aspects, from the alloy's microstructure and phase transformations to its response under different loading conditions and its suitability for specific engineering applications.
Understanding the Al-Zn Alloy System
Aluminum zinc alloys are known for their excellent combination of properties, making them suitable for diverse applications. The specific properties of an Al-Zn alloy are strongly dependent on its composition, specifically the percentage of zinc (Zn) present. The addition of zinc to aluminum significantly alters its mechanical properties, primarily increasing its strength and hardness. This enhancement is achieved through solid solution strengthening and the precipitation hardening mechanism.
Phase Transformations and Microstructure
The microstructure of an Al-Zn alloy plays a crucial role in determining its mechanical properties. At higher zinc concentrations, specific intermetallic phases can form, significantly influencing the alloy's overall performance. These phases can be detrimental or beneficial depending on their morphology, distribution, and size. Understanding the phase diagram of the Al-Zn system is critical for predicting the microstructure and consequently, the mechanical properties.
-
Solid Solution Strengthening: The addition of zinc atoms into the aluminum lattice causes lattice distortion, hindering dislocation movement and thus increasing the material's strength.
-
Precipitation Hardening: This is a crucial mechanism in Al-Zn alloys. During heat treatment, specific precipitates form within the aluminum matrix. These precipitates further impede dislocation movement, resulting in enhanced strength and hardness. The size, distribution, and type of precipitates significantly impact the alloy's properties. Precise control over heat treatment is therefore essential to achieve desired mechanical performance.
Mechanical Characterization of Al-Zn Alloys
Mechanical testing is paramount in characterizing the behavior of Al-Zn alloys under various loading conditions. Different tests provide valuable insights into various aspects of the material's mechanical behavior.
Tensile Testing
Tensile testing is a fundamental technique to determine the yield strength, ultimate tensile strength, elongation, and reduction in area. These parameters provide crucial information about the alloy's strength, ductility, and overall formability. The tensile test curve reveals the material's elastic and plastic behavior, along with its strain-hardening characteristics. Analyzing the stress-strain curve can provide valuable insights into the alloy's microstructural features.
Hardness Testing
Hardness testing, methods like Brinell, Rockwell, or Vickers, provides a measure of the alloy's resistance to indentation. This property is directly related to the material's strength and is often used as a rapid screening test. Changes in hardness can indicate microstructural variations or effects of heat treatments.
Fatigue Testing
Fatigue testing involves subjecting the alloy to cyclic loading to determine its fatigue life and fatigue strength. This is critical for applications where the material experiences repeated stress cycles, such as in aerospace or automotive components. Fatigue failure is often catastrophic, so understanding the fatigue behavior of Al-Zn alloys is essential for ensuring reliability and safety.
Creep Testing
Creep testing measures the material's deformation under sustained stress at elevated temperatures. This is especially important for applications involving high-temperature exposure, as creep can lead to significant dimensional changes and potential failure. Understanding the creep behavior is critical for designing components that will operate reliably under these conditions.
Fracture Toughness Testing
Fracture toughness testing assesses the material's resistance to crack propagation. This property is crucial for ensuring the structural integrity of components, particularly in the presence of flaws or defects. The fracture toughness of Al-Zn alloys is influenced by several factors, including microstructure, grain size, and the presence of second-phase particles.
Influence of Microstructural Features on Mechanical Properties
The relationship between the microstructure and the mechanical properties of Al-Zn alloys is complex but well-defined. Several microstructural features significantly impact the overall performance of the material.
Grain Size
Grain size affects the strength and ductility of the alloy. Smaller grain sizes generally lead to higher strength but lower ductility. This is due to the increased grain boundary area, which impedes dislocation movement. Grain refinement techniques can be employed to improve the overall mechanical properties.
Precipitate Size and Distribution
The size, distribution, and type of precipitates significantly impact the alloy's strength and hardness. Fine, uniformly distributed precipitates are generally desirable, as they effectively impede dislocation motion. Heat treatment plays a critical role in controlling the size and distribution of precipitates.
Second Phase Particles
The presence of second-phase particles can either strengthen or weaken the alloy, depending on their nature, size, and distribution. Some particles can act as obstacles to dislocation movement, leading to strengthening. However, others can act as stress concentrators, reducing the alloy's toughness and increasing the susceptibility to cracking.
Applications of Al-Zn Alloys
The unique combination of properties exhibited by Al-Zn alloys makes them suitable for a variety of applications across different industries.
Aerospace Industry
Al-Zn alloys are used extensively in the aerospace industry due to their high strength-to-weight ratio and good corrosion resistance. They are frequently employed in aircraft structures, components, and engine parts where weight reduction is crucial.
Automotive Industry
In the automotive industry, Al-Zn alloys find application in various components where both strength and lightweight design are important factors. They can be used in body panels, chassis components, and engine parts.
Electronics Industry
The good electrical conductivity of Al-Zn alloys makes them suitable for use in electronic packaging and heat sinks.
Other Applications
Other applications for Al-Zn alloys include sporting goods, packaging materials, and architectural components.
Advanced Analytical Techniques
Advanced analytical techniques are employed to gain a deeper understanding of the Al-Zn alloy system. These techniques provide insights into the alloy's microstructure, chemical composition, and mechanical behavior at a much finer scale.
Transmission Electron Microscopy (TEM)
TEM is a powerful technique for characterizing the microstructure at the nanoscale. It allows the visualization of individual precipitates, dislocations, and other microstructural features, providing crucial information about their size, shape, and distribution.
Scanning Electron Microscopy (SEM)
SEM provides high-resolution images of the alloy's surface morphology and microstructure. It can be used to analyze the grain size, shape, and distribution, as well as the morphology and distribution of second-phase particles.
X-ray Diffraction (XRD)
XRD is used to identify the phases present in the alloy and to determine their crystallographic structure. This information is crucial for understanding the alloy's phase transformations and their impact on its mechanical properties.
Electron Probe Microanalysis (EPMA)
EPMA provides quantitative information about the chemical composition of the alloy at a micron scale. This is important for understanding the homogeneity of the alloy and the distribution of alloying elements.
Conclusion
This in-depth analysis of Al-Zn alloys highlights the importance of understanding their complex interplay between composition, microstructure, and mechanical properties. The ability to tailor the properties of these alloys through precise control of composition and heat treatment makes them highly versatile materials suitable for a wide range of engineering applications. Continued research and development in this field will undoubtedly lead to further improvements in the performance and applications of Al-Zn alloys. Further studies could focus on developing novel alloy compositions with enhanced properties or exploring new processing techniques to optimize the microstructure and achieve even better mechanical performance. The potential for innovation in this area remains significant, promising advancements in various industries that rely on high-performance lightweight materials.
Latest Posts
Latest Posts
-
Match Each Theoretical Approach With The Way It Studies Personality
May 09, 2025
-
Affidavit Of Repudiation To Secretary Of State
May 09, 2025
-
Which Tube Has The Highest Protein Concentration
May 09, 2025
-
An Angry Caller Who Sounds As Though
May 09, 2025
-
The Metric Prefix Denoting 1000x Is
May 09, 2025
Related Post
Thank you for visiting our website which covers about Advance Study Assignment Analysis Of An Aluminum Zinc Alloy . We hope the information provided has been useful to you. Feel free to contact us if you have any questions or need further assistance. See you next time and don't miss to bookmark.