An Ideal Spring Is Used To Stop Blocks
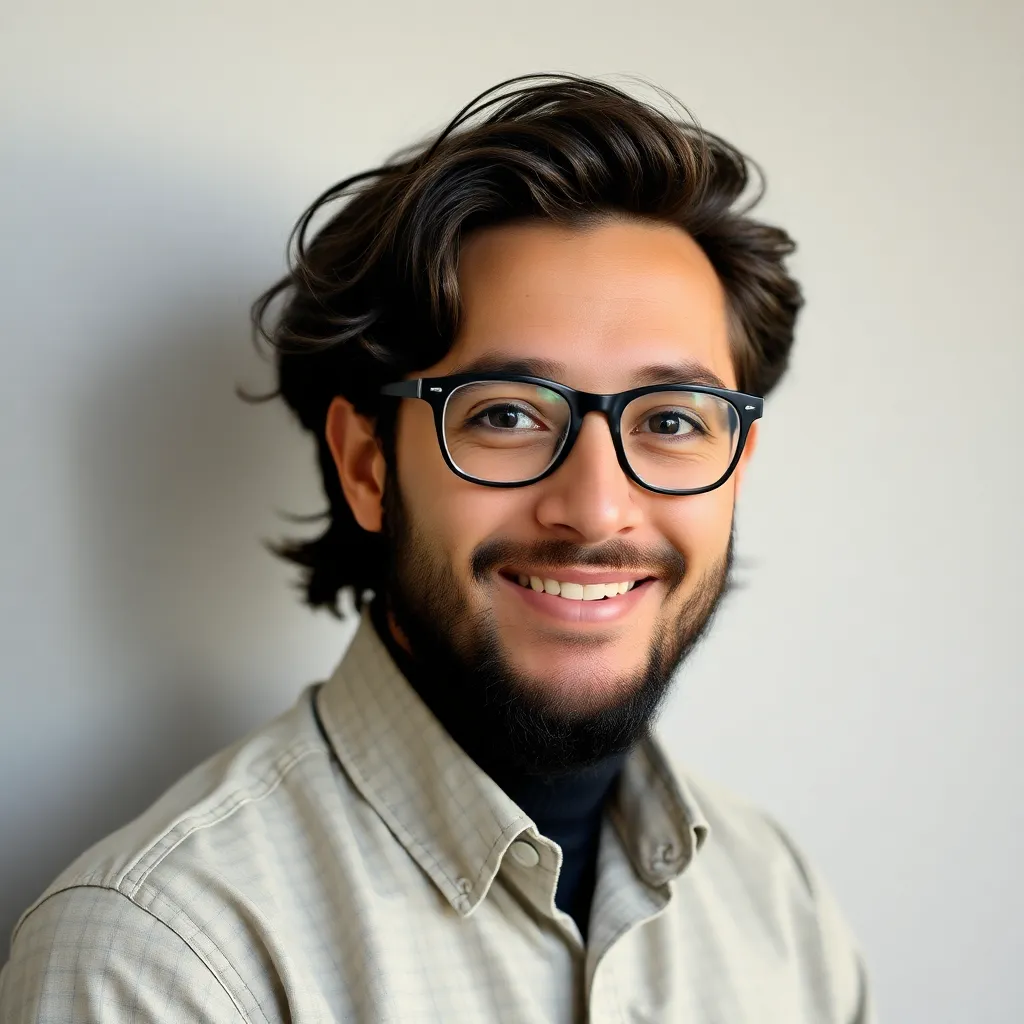
Onlines
May 08, 2025 · 5 min read
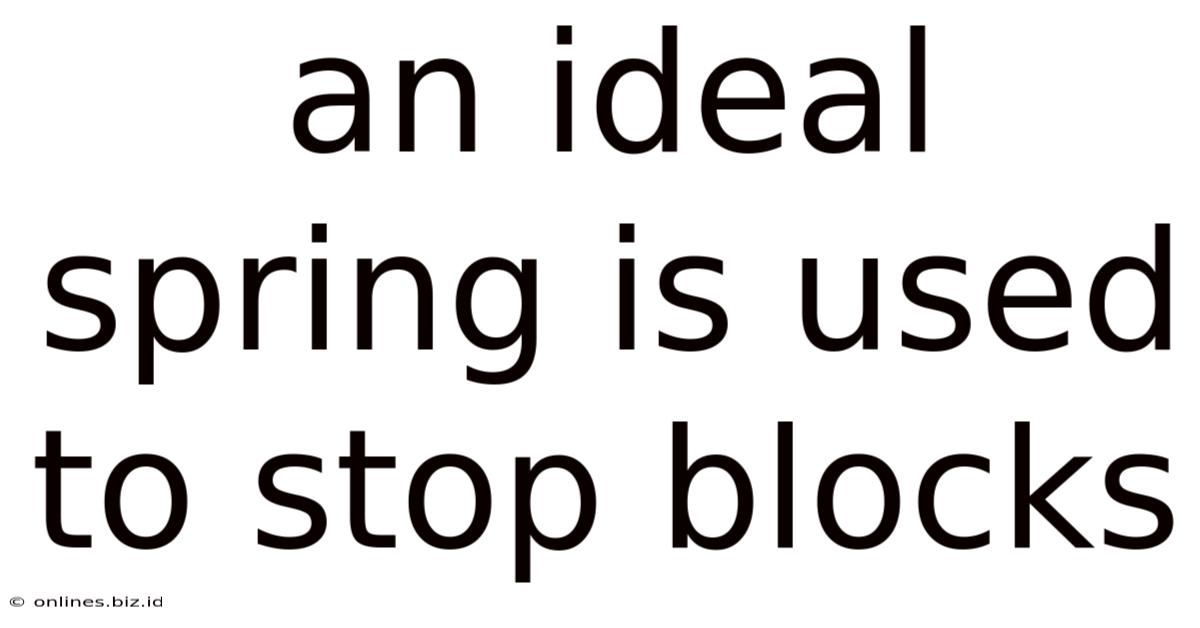
Table of Contents
An Ideal Spring Used to Stop Blocks: A Comprehensive Analysis
The seemingly simple act of stopping a moving block using a spring conceals a rich tapestry of physics principles. This article delves deep into the mechanics involved, exploring the ideal spring scenario and its implications, considering factors like energy conservation, impact forces, and the limitations of the ideal model. We'll examine the mathematical formulations underpinning these processes, exploring different scenarios and offering a comprehensive understanding of this classic physics problem.
Understanding the Ideal Spring
Before we dive into the complexities of stopping blocks, let's define our ideal spring. An ideal spring is a theoretical construct exhibiting perfect elasticity. This means:
- It obeys Hooke's Law perfectly: The force exerted by the spring is directly proportional to its displacement from its equilibrium position (F = -kx, where F is the force, k is the spring constant, and x is the displacement).
- It has negligible mass: The mass of the spring is insignificant compared to the mass of the block.
- It experiences no energy loss (damping): There is no energy lost due to internal friction or heat generation during compression or expansion.
While a perfect ideal spring doesn't exist in the real world, this model serves as a crucial starting point for understanding the fundamental principles involved. Real-world springs deviate from this ideal, exhibiting damping and potentially non-linear behavior at high compressions. However, the ideal spring model allows for simpler, more elegant solutions, providing a valuable foundation for further, more complex analyses.
Energy Conservation in the System
The core principle governing the interaction between the moving block and the ideal spring is the conservation of mechanical energy. Assuming no external forces (like friction) act on the system, the total mechanical energy remains constant. This energy is comprised of the kinetic energy of the block and the potential energy stored in the spring.
Kinetic Energy
The kinetic energy (KE) of a moving block is given by the formula:
KE = (1/2)mv²
where:
- m = mass of the block
- v = velocity of the block
Potential Energy of the Spring
The potential energy (PE) stored in an ideal spring is given by:
PE = (1/2)kx²
where:
- k = spring constant
- x = displacement of the spring from its equilibrium position
Conservation of Energy Equation
Applying the principle of energy conservation, we can equate the initial kinetic energy of the block to the maximum potential energy stored in the compressed spring:
(1/2)mv² = (1/2)kx²<sub>max</sub>
This equation allows us to determine the maximum compression (x<sub>max</sub>) of the spring, given the block's mass, velocity, and the spring constant. It's crucial to note that this equation assumes the block comes to a complete stop after compressing the spring.
Calculating Maximum Compression and Impact Force
From the energy conservation equation, we can solve for the maximum compression:
x<sub>max</sub> = √[(mv²)/k]
This equation clearly demonstrates the relationship between the block's initial kinetic energy and the maximum spring compression. A higher initial velocity or mass results in greater compression. A stiffer spring (higher k) will result in less compression.
The impact force exerted by the spring on the block is not constant during the compression process. It varies according to Hooke's Law (F = -kx). The maximum impact force occurs at the point of maximum compression (x<sub>max</sub>):
F<sub>max</sub> = kx<sub>max</sub> = k√[(mv²)/k] = √[kmv²]
This equation reveals that the maximum impact force is dependent on the spring constant, the mass of the block, and its initial velocity. A stiffer spring will exert a greater maximum force, as will a higher mass and velocity.
Analyzing Different Scenarios
The basic model can be expanded to include more realistic scenarios:
Scenario 1: Friction Present
Introducing friction significantly alters the energy balance. Some of the block's initial kinetic energy is converted into heat due to friction, reducing the energy available for spring compression. The energy conservation equation needs to be modified to account for the work done by friction (W<sub>friction</sub> = μmgd, where μ is the coefficient of friction, g is the acceleration due to gravity, and d is the distance over which friction acts). The revised equation becomes:
(1/2)mv² - μmgd = (1/2)kx²<sub>max</sub>
Solving for x<sub>max</sub> in this scenario requires iterative methods or numerical solutions, as the equation is not easily solvable algebraically.
Scenario 2: Non-Ideal Spring
Real-world springs deviate from Hooke's Law, particularly at high compressions. The force-displacement relationship might become non-linear, requiring more complex mathematical models (e.g., including higher-order terms in the force equation) to accurately predict the behavior of the system.
Scenario 3: Multiple Blocks
The scenario can be extended to consider multiple blocks impacting the spring sequentially or simultaneously. The analysis becomes significantly more complex, requiring consideration of momentum conservation and potentially complex interactions between the blocks and the spring. Numerical methods, like finite element analysis (FEA), are often employed to model such intricate scenarios.
Implications and Applications
The principles discussed here have wide-ranging implications across various engineering and physics domains. Understanding the interaction between moving objects and springs is crucial in:
- Vehicle Safety: Designing crumple zones in vehicles to absorb impact energy and protect occupants.
- Shock Absorption: Developing shock absorbers in vehicles and other machinery to dampen vibrations and protect components.
- Packaging and Cushioning: Designing protective packaging to minimize damage to fragile goods during transport.
- Impact Testing: Conducting impact tests to assess the strength and durability of materials and structures.
- Robotics: Designing robotic systems capable of safely interacting with their environment, handling objects, and absorbing impacts.
Conclusion
Analyzing the interaction between an ideal spring and a moving block provides a fundamental understanding of energy conservation, impact forces, and the limitations of ideal models. While the ideal spring model simplifies the analysis, it offers a crucial starting point for understanding the core principles involved. Incorporating real-world factors like friction and non-linear spring behavior requires more sophisticated mathematical models, often necessitating numerical techniques for accurate solutions. The principles explored here are crucial across numerous engineering and physics disciplines, highlighting the importance of understanding this seemingly simple interaction. The application of these principles extends to a variety of safety and design considerations, ensuring the efficient and safe operation of numerous systems in various industries. Further research into more complex scenarios with multiple blocks and non-ideal conditions would enhance our understanding and improve design capabilities across various fields.
Latest Posts
Latest Posts
-
What Was Beneathas Family Doing When George Came In
May 11, 2025
-
University Of New England Online Physics
May 11, 2025
-
A Surplus Of Shoes Will Cause
May 11, 2025
-
Five Hours To Simla Quick Check
May 11, 2025
-
Which Of The Following Is Vicarious Responsibility Based On
May 11, 2025
Related Post
Thank you for visiting our website which covers about An Ideal Spring Is Used To Stop Blocks . We hope the information provided has been useful to you. Feel free to contact us if you have any questions or need further assistance. See you next time and don't miss to bookmark.