As A Rule Of Thumb A Safety And Health Program
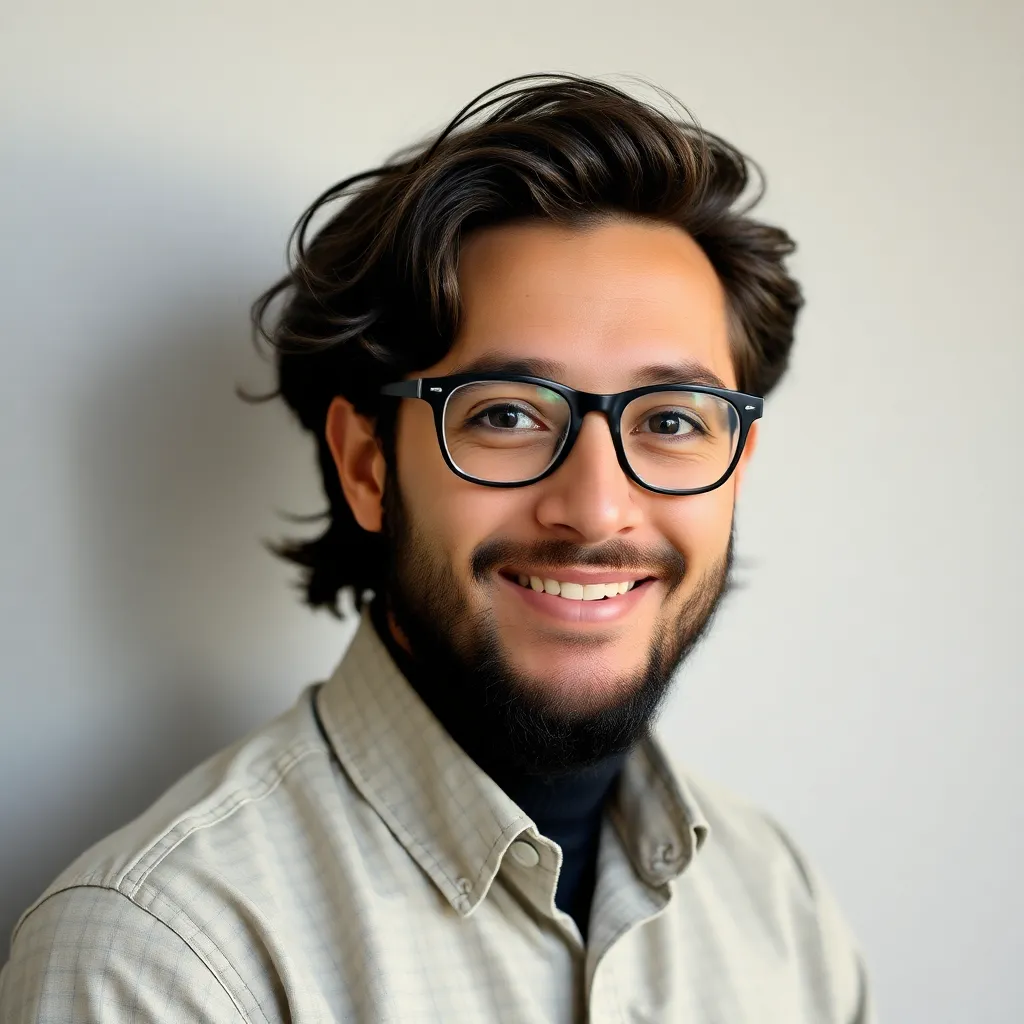
Onlines
May 10, 2025 · 6 min read
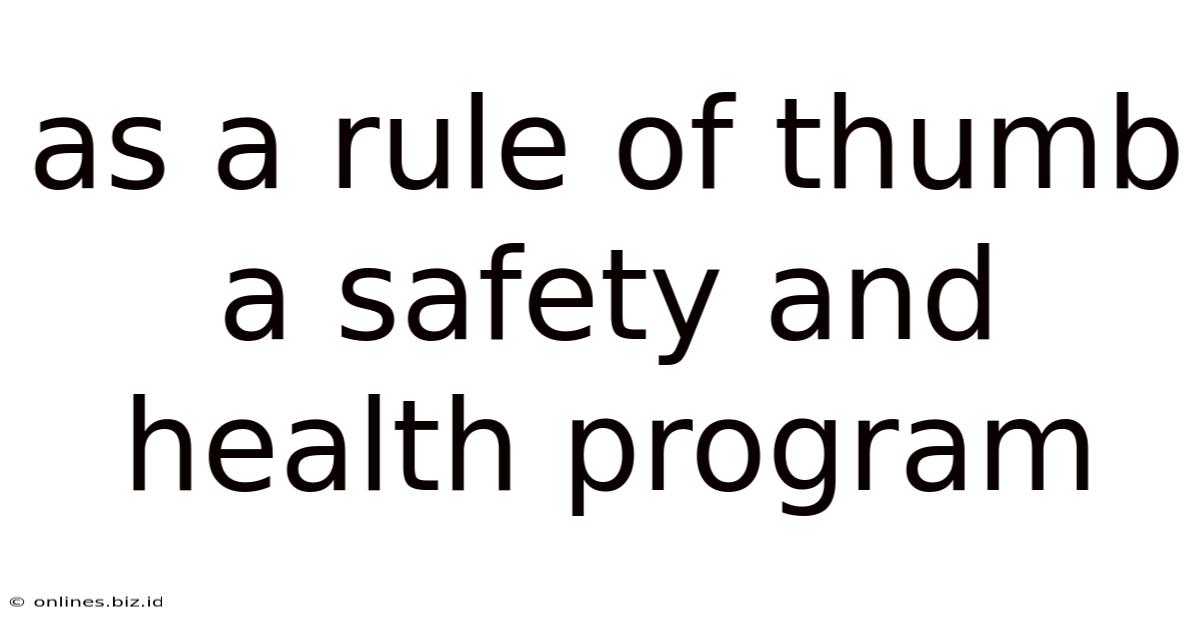
Table of Contents
As a Rule of Thumb: A Comprehensive Guide to Safety and Health Programs
Creating a robust safety and health program isn't just about ticking boxes; it's about fostering a culture of care and responsibility within your organization. This comprehensive guide will delve into the essential elements of a successful safety and health program, offering practical advice and actionable steps to ensure the well-being of your employees and the success of your business. Remember, a proactive approach to safety is far more cost-effective than reacting to accidents.
Why a Robust Safety and Health Program is Crucial
Beyond the ethical imperative to protect your employees, a well-structured safety and health program offers significant advantages:
Reduced Workplace Accidents & Injuries:
A strong safety program significantly reduces the likelihood of workplace accidents, resulting in fewer injuries, illnesses, and fatalities. This translates to lower workers' compensation costs, decreased absenteeism, and improved productivity.
Improved Employee Morale & Productivity:
Employees who feel valued and safe are more engaged, productive, and loyal. A commitment to safety demonstrates your organization's concern for their well-being, fostering a positive and supportive work environment.
Enhanced Company Reputation & Brand Image:
A strong safety record enhances your company's reputation, attracting top talent and building trust with clients and stakeholders. It showcases your commitment to ethical and responsible business practices.
Reduced Insurance Premiums & Legal Costs:
Proactive safety measures can lead to lower insurance premiums and mitigate the risk of costly lawsuits resulting from workplace accidents. A demonstrable commitment to safety can significantly reduce your liability.
Increased Operational Efficiency:
A well-managed safety program can streamline operations, reduce downtime caused by accidents, and improve overall efficiency. By preventing incidents, you avoid the disruption and costs associated with investigations, repairs, and replacements.
Core Components of a Successful Safety and Health Program
A truly effective safety and health program needs a multi-faceted approach, encompassing several crucial elements:
1. Management Commitment & Leadership:
Strong leadership is paramount. Senior management must champion the safety program, allocating sufficient resources, establishing clear expectations, and holding everyone accountable. This commitment needs to be visible and unwavering, permeating all levels of the organization.
- Establish clear safety policies and procedures: These policies should be readily accessible, easily understandable, and regularly reviewed and updated.
- Provide adequate training and resources: Invest in comprehensive safety training for all employees, including supervisors and managers. Equip them with the necessary resources and tools to perform their jobs safely.
- Regularly monitor and evaluate the program: Conduct regular safety audits and inspections to identify potential hazards and areas for improvement. Analyze accident data to identify trends and implement corrective actions.
2. Hazard Identification & Risk Assessment:
Proactive hazard identification is key. Regularly assess your workplace for potential hazards, both obvious and subtle. This involves a thorough examination of all work processes, equipment, materials, and the environment.
- Conduct workplace inspections: Regularly inspect your workplace for potential hazards, paying close attention to areas with a high risk of accidents.
- Utilize job hazard analyses (JHAs): JHAs systematically break down tasks into steps, identifying potential hazards associated with each step and recommending control measures.
- Employee involvement: Encourage employees to actively participate in hazard identification. They often have valuable insights into the everyday risks they face.
3. Control Measures & Implementation:
Once hazards are identified, implement appropriate control measures to eliminate or minimize risks. This is often referred to as the hierarchy of controls:
- Elimination: The most effective control measure is eliminating the hazard entirely. If feasible, remove the hazardous substance, process, or equipment.
- Substitution: Replace the hazardous substance or process with a safer alternative. For example, substitute a toxic cleaning agent with a less toxic one.
- Engineering Controls: Implement physical changes to the workplace to reduce exposure to hazards. Examples include installing guards on machinery, improving ventilation, or providing better lighting.
- Administrative Controls: Modify work practices to minimize risks. This could include implementing safe work procedures, providing additional training, or reducing work hours in hazardous areas.
- Personal Protective Equipment (PPE): Provide and ensure the proper use of PPE, such as safety glasses, gloves, hearing protection, and respirators, as a last resort when other controls are not feasible. Remember that PPE is only effective when used correctly.
4. Training & Communication:
Comprehensive training is essential. All employees should receive training on relevant safety procedures, hazard recognition, and the use of PPE. Communication should be clear, consistent, and accessible.
- Develop customized training programs: Tailor training to the specific hazards and risks associated with different jobs and tasks.
- Provide regular refresher training: Keep employees updated on new safety regulations, procedures, and best practices.
- Utilize various communication channels: Use a combination of methods such as toolbox talks, safety meetings, posters, and online resources to ensure everyone receives the necessary information.
- Promote open communication: Encourage employees to report near misses, unsafe conditions, and concerns without fear of reprisal.
5. Emergency Preparedness & Response:
Having a well-defined emergency plan is critical. This plan should outline procedures for responding to various emergencies, including fires, medical emergencies, and natural disasters.
- Develop comprehensive emergency response plans: Ensure the plans cover evacuation procedures, first aid protocols, and contact information for emergency services.
- Conduct regular drills and simulations: Practice emergency procedures to ensure employees are familiar with the plan and can respond effectively in a real-life situation.
- Provide adequate emergency equipment: Ensure sufficient fire extinguishers, first aid kits, and other essential equipment are readily available.
6. Record Keeping & Reporting:
Maintaining accurate records is crucial. This includes documenting accidents, near misses, safety inspections, training records, and any corrective actions taken.
- Develop a system for tracking safety incidents: This allows for identifying trends, assessing the effectiveness of safety measures, and preventing future incidents.
- Report accidents and near misses promptly: Timely reporting allows for prompt investigations and implementation of corrective actions.
- Regularly review safety data: Analyze accident data to identify trends and areas for improvement.
7. Continuous Improvement:
Continuous improvement is a key principle. Regularly review and update your safety program based on performance data, new regulations, and best practices.
- Conduct regular program reviews: Assess the effectiveness of your safety program and identify areas for improvement.
- Implement corrective actions promptly: Address any identified deficiencies or shortcomings in a timely manner.
- Stay updated on new regulations and best practices: Keep your program current by staying informed on the latest safety regulations and industry best practices.
Integrating Technology into Your Safety Program
Technology offers powerful tools to enhance your safety and health program:
- Safety Management Software: Streamline safety procedures, track incidents, manage training, and conduct risk assessments.
- Wearable Technology: Monitor employee health and safety in real-time, providing alerts and data analysis.
- Virtual Reality (VR) Training: Offer immersive training simulations in a safe environment.
The Legal Landscape of Workplace Safety
Compliance with relevant occupational safety and health regulations is not merely advisable, but legally mandatory. Ignorance of these regulations is not a defense against potential penalties. Familiarize yourself with the specifics of the laws and standards in your jurisdiction.
Conclusion: Building a Culture of Safety
Building a robust safety and health program requires a sustained commitment, proactive approach, and a genuine dedication to employee well-being. It's not a one-time project but an ongoing process of continuous improvement and adaptation. By implementing these guidelines and fostering a culture of safety, you can create a workplace where employees feel valued, protected, and empowered to contribute their best, leading to a safer, more productive, and successful organization. Remember, safety isn't just a program; it's a value.
Latest Posts
Latest Posts
-
Security Personnel Whose Post Is Located
May 10, 2025
-
Which Of The Following Best Exemplifies A Reflex
May 10, 2025
-
Angle Of Impact Blood Spatter Worksheet
May 10, 2025
-
A Grocery Store Receives Delivery Of Corn
May 10, 2025
-
Homework 4 Congruent Chords And Arcs
May 10, 2025
Related Post
Thank you for visiting our website which covers about As A Rule Of Thumb A Safety And Health Program . We hope the information provided has been useful to you. Feel free to contact us if you have any questions or need further assistance. See you next time and don't miss to bookmark.