As The Refractory Temperature Increases The Combustion Efficiency
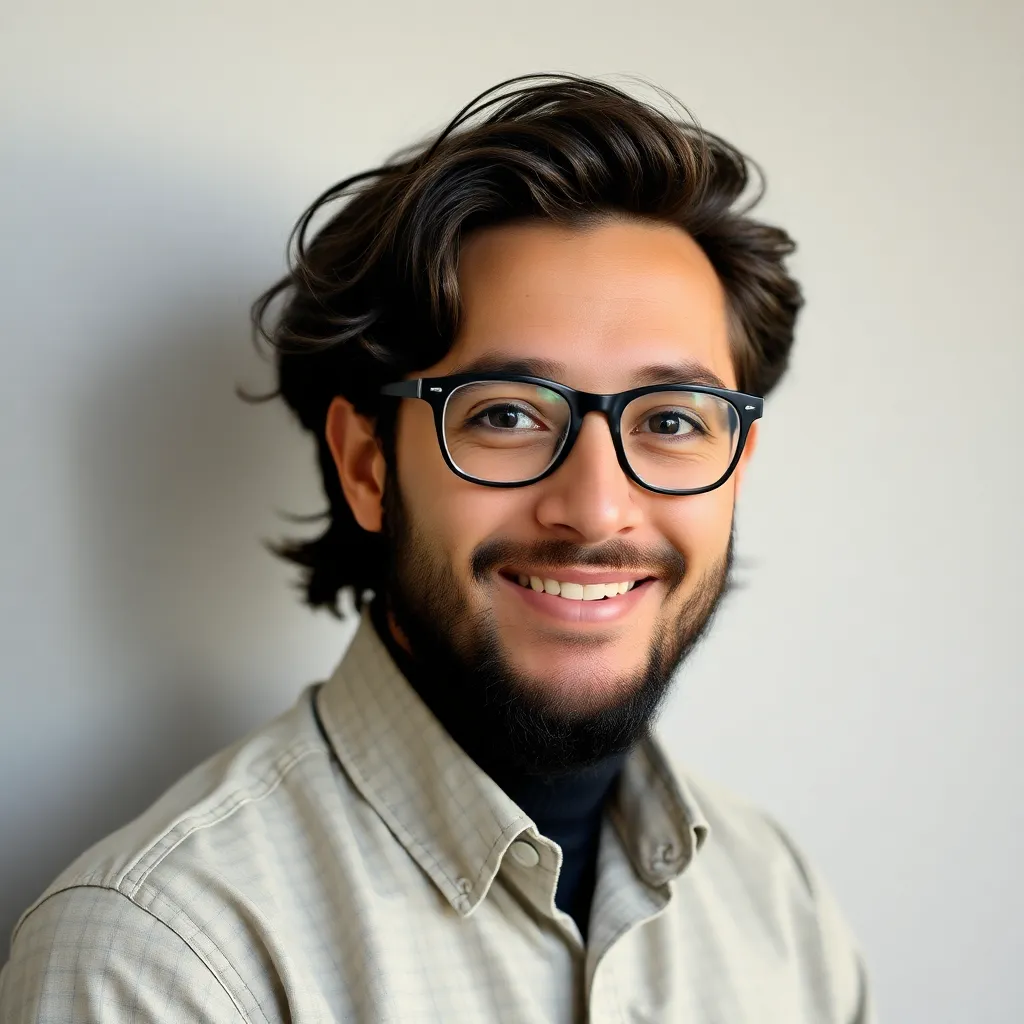
Onlines
May 08, 2025 · 5 min read
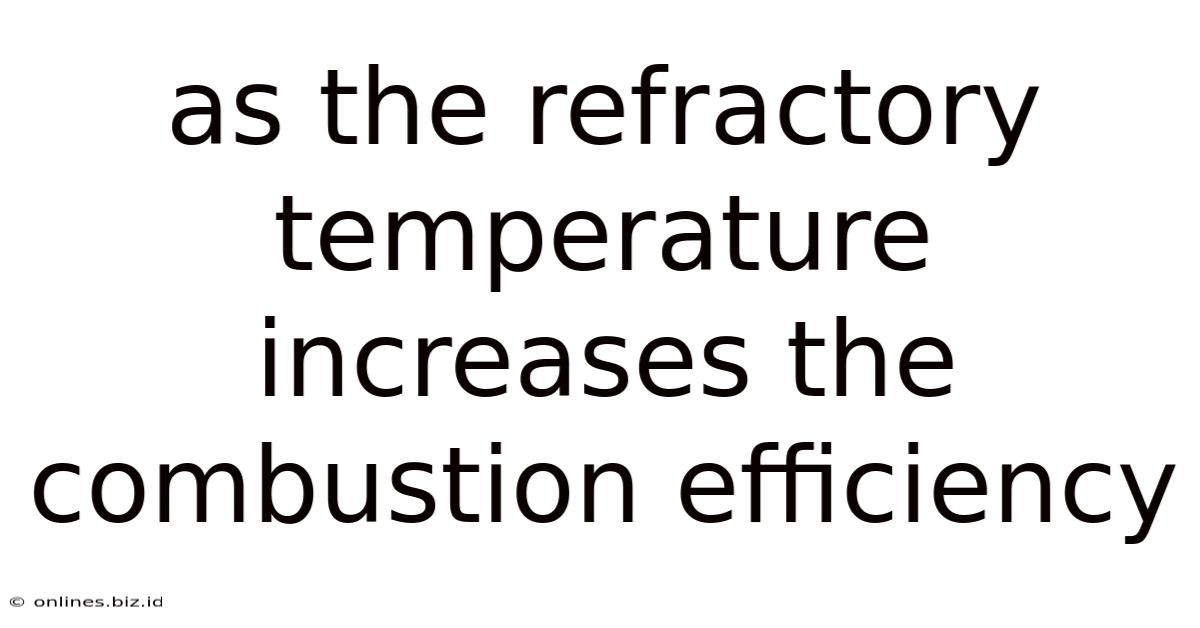
Table of Contents
As Refractory Temperature Increases, Combustion Efficiency: A Deep Dive
The efficiency of combustion processes is intrinsically linked to the temperature of the refractory materials lining the combustion chamber. Understanding this relationship is crucial for optimizing energy consumption, minimizing emissions, and extending the lifespan of industrial furnaces and boilers. This article delves into the complex interplay between refractory temperature and combustion efficiency, exploring the underlying mechanisms and practical implications.
The Role of Refractory Materials in Combustion
Refractory materials are high-temperature resistant materials used to line the interior walls of combustion chambers. Their primary function is to:
- Withstand extreme temperatures: Combustion processes generate intense heat, often exceeding 1500°C (2732°F). Refractory materials possess the necessary thermal resistance to prevent damage and ensure operational integrity.
- Insulate the chamber: Efficient insulation minimizes heat loss to the surroundings, maximizing the energy transferred to the process material (e.g., metal being smelted, water being heated).
- Protect the outer shell: Refractory linings act as a barrier, shielding the outer shell of the furnace from the extreme heat, preventing structural damage and extending the lifespan of the equipment.
- Reflect radiation: Certain refractory materials possess high emissivity, effectively reflecting radiated heat back into the combustion zone, enhancing heat transfer and combustion efficiency.
The choice of refractory material depends on the specific application, considering factors such as temperature requirements, chemical environment, and thermal shock resistance. Common materials include fireclay brick, alumina-silica brick, magnesia-chromite brick, and zirconia-based refractories.
The Impact of Refractory Temperature on Combustion Efficiency
The temperature of the refractory lining directly influences several aspects of the combustion process, ultimately impacting efficiency:
1. Heat Transfer and Retention
Higher refractory temperatures lead to more effective heat transfer within the combustion chamber. A hotter refractory surface increases the rate of radiative heat transfer to the combustion gases, promoting faster and more complete fuel oxidation. This enhanced heat retention reduces heat loss to the surroundings, directly contributing to improved combustion efficiency.
Key Factors influencing Heat Transfer:
- Refractory material properties: Thermal conductivity, emissivity, and specific heat capacity directly influence the rate of heat transfer.
- Furnace geometry and design: The shape and size of the combustion chamber affect the path length of radiation and the overall heat transfer dynamics.
- Gas flow patterns: Proper gas flow ensures uniform heat distribution across the refractory surface, optimizing heat transfer.
2. Flame Stability and Ignition
The temperature of the refractory lining plays a significant role in flame stability. A sufficiently hot refractory surface helps initiate and sustain the combustion process by providing a localized hot spot for ignition. This is particularly crucial in applications involving difficult-to-ignite fuels or low-temperature combustion.
Factors affecting Flame Stability:
- Fuel type and composition: Different fuels have varying ignition temperatures and flame propagation characteristics.
- Air-fuel ratio: The precise mixing of fuel and air is vital for stable and efficient combustion.
- Turbulence levels: Higher turbulence promotes better mixing of reactants and enhances flame stability.
3. Minimizing Heat Losses
One of the major contributors to reduced combustion efficiency is heat loss through the furnace walls. Higher refractory temperatures can actually reduce heat loss through several mechanisms:
- Reduced temperature gradient: A hotter refractory surface reduces the temperature difference between the inside and outside of the furnace, diminishing conductive heat loss.
- Improved insulation: The inherent insulation properties of refractory materials become more effective at higher temperatures, further reducing heat loss.
However, it's crucial to note that excessively high refractory temperatures can lead to increased heat loss through radiation if the insulation fails or the refractory material degrades.
4. NOx Formation
While higher refractory temperatures improve efficiency, they can also lead to increased formation of nitrogen oxides (NOx), a significant air pollutant. High temperatures promote the thermal fixation of nitrogen in the air with oxygen to form NOx. Careful control of the combustion process, including air-fuel ratio and temperature management, is crucial to mitigate NOx formation.
Strategies to Minimize NOx:
- Low NOx burners: Specialized burners designed to promote efficient mixing and lower peak flame temperatures.
- Selective Catalytic Reduction (SCR): Post-combustion technology that uses a catalyst to convert NOx into less harmful nitrogen and water.
- Selective Non-Catalytic Reduction (SNCR): Similar to SCR but doesn't require a catalyst, generally less efficient.
- Staged combustion: Introducing fuel in multiple stages to optimize the combustion process and reduce peak temperatures.
Optimizing Refractory Temperature for Maximum Combustion Efficiency
Achieving optimal combustion efficiency requires careful management of refractory temperature. This involves several considerations:
- Material Selection: Selecting appropriate refractory materials based on the operating temperature and chemical environment. Materials with high thermal shock resistance and low thermal conductivity are preferred.
- Furnace Design: Optimizing furnace geometry and insulation to minimize heat loss and promote uniform heat distribution.
- Combustion Control: Precisely controlling the air-fuel ratio and combustion air preheating temperature to achieve complete combustion and minimize NOx formation.
- Monitoring and Maintenance: Regularly monitoring refractory temperature and condition using thermocouples and infrared cameras. Performing timely repairs and replacements to prevent damage and maintain efficiency.
Practical Implications and Case Studies
The relationship between refractory temperature and combustion efficiency has significant practical implications across various industries:
- Cement Industry: Rotary kilns are critical in cement production, and maintaining optimal refractory temperature is paramount for energy efficiency and clinker quality.
- Steel Industry: Blast furnaces and steelmaking converters rely heavily on refractory linings, and the temperature management directly impacts productivity and energy costs.
- Power Generation: Boiler furnaces in power plants need efficient refractory systems to optimize combustion and reduce emissions.
- Waste Incineration: Incineration plants employ refractory materials to withstand high temperatures and promote complete combustion of waste materials.
Case Study Example: A study on a cement kiln found that increasing refractory temperature by a modest 50°C resulted in a 3% improvement in fuel efficiency and a 2% reduction in CO2 emissions. However, this improvement was only achieved with careful monitoring and control to prevent excessive NOx formation.
Conclusion
The temperature of the refractory lining in combustion chambers significantly influences combustion efficiency. Higher refractory temperatures generally promote better heat transfer, flame stability, and reduced heat loss, ultimately leading to higher efficiency. However, this must be balanced against potential increases in NOx emissions and refractory degradation. Optimizing refractory temperature requires careful consideration of material selection, furnace design, combustion control, and regular monitoring and maintenance. By understanding and implementing these strategies, industries can significantly improve combustion efficiency, reduce energy costs, and minimize environmental impact. Further research into advanced refractory materials and combustion technologies will continue to refine these techniques and improve efficiency even further.
Latest Posts
Latest Posts
-
Rococo Style Was Most Closely Associated With Which Group
May 11, 2025
-
Weekly Math Review Q2 6 Answer Key
May 11, 2025
-
Which Of The Following Are Supporting Elements Of The Jis
May 11, 2025
-
Long Days Journey Into Night Characters
May 11, 2025
-
The Half Circle Is Most Often Used To Move The Hair
May 11, 2025
Related Post
Thank you for visiting our website which covers about As The Refractory Temperature Increases The Combustion Efficiency . We hope the information provided has been useful to you. Feel free to contact us if you have any questions or need further assistance. See you next time and don't miss to bookmark.