Blueprint Reading For Welders 9th Edition Answer Key Unit 6
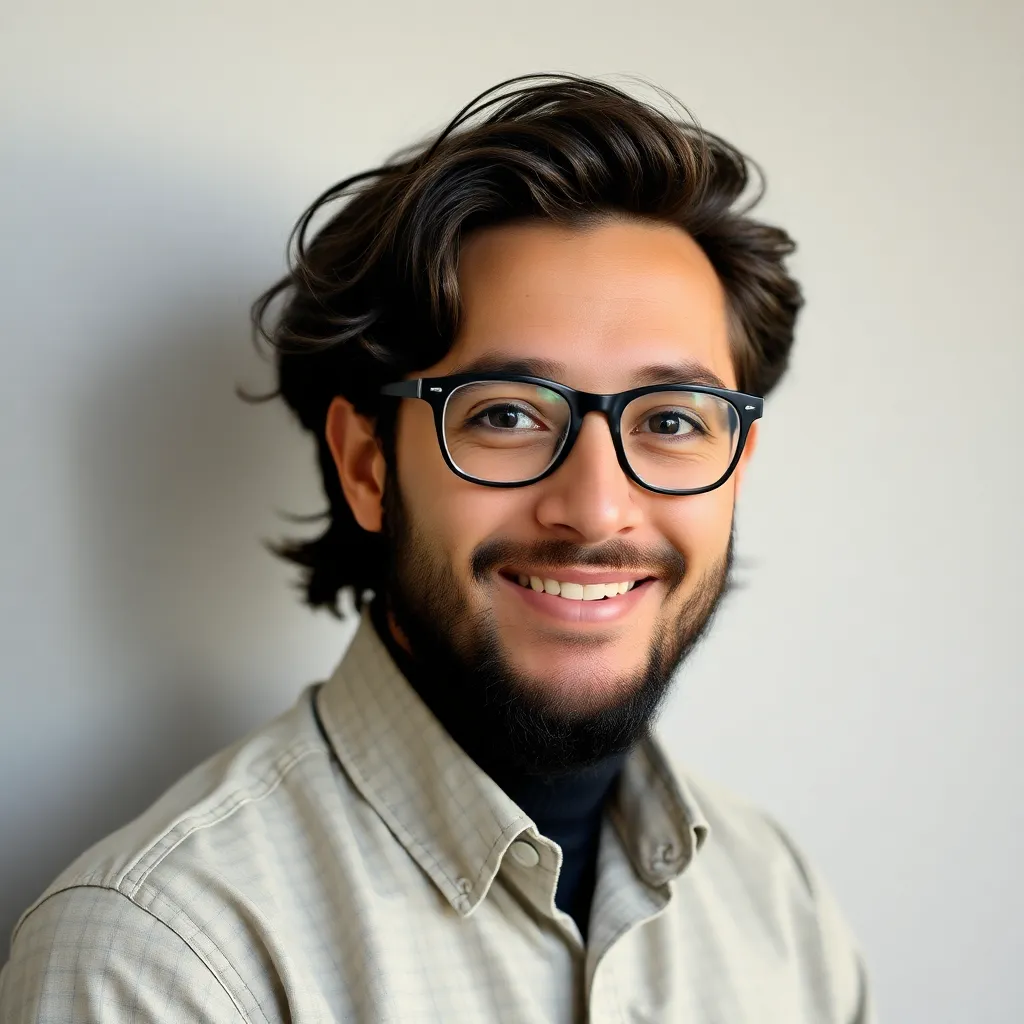
Onlines
Apr 19, 2025 · 6 min read

Table of Contents
- Blueprint Reading For Welders 9th Edition Answer Key Unit 6
- Table of Contents
- Blueprint Reading for Welders 9th Edition: Mastering Unit 6 – Welding Symbols and Processes
- Understanding the Language of Welding Symbols
- Deciphering Common Weld Symbols and Their Applications
- Understanding Joint Preparations and Their Impact on Welding
- Welding Processes and Their Representation on Blueprints
- Interpreting Supplementary Symbols and Additional Specifications
- Practical Application and Problem-Solving
- Advanced Concepts and Beyond Unit 6
- Latest Posts
- Latest Posts
- Related Post
Blueprint Reading for Welders 9th Edition: Mastering Unit 6 – Welding Symbols and Processes
Blueprint reading is a fundamental skill for any welder, forming the bridge between design and fabrication. This article delves into Unit 6 of the popular "Blueprint Reading for Welders" 9th edition textbook, focusing on welding symbols and processes. While we won't provide direct answers to specific questions from the textbook (as that would infringe on copyright), we will equip you with the comprehensive knowledge needed to confidently tackle the unit's challenges and master the crucial concepts within.
This guide offers a detailed exploration of welding symbols, their components, and their applications in various welding processes. Understanding these symbols is critical for accurately interpreting blueprints and ensuring the correct weld is executed. We'll examine different weld types, joint preparations, and the significance of various symbol elements. This deep dive will prepare you for any assessment or real-world application of blueprint reading in your welding career.
Understanding the Language of Welding Symbols
Welding symbols, as depicted on blueprints, are a concise yet precise method of conveying essential welding information. They are not merely illustrations but a standardized language understood by welders and engineers worldwide. Mastering this language is paramount for producing high-quality, safe, and compliant welds. This section breaks down the key elements of a typical welding symbol:
- Reference Line: This is the baseline of the symbol, indicating the location of the weld on the blueprint. It’s crucial to note the relationship between the reference line and the weld location.
- Arrow Side: This denotes the side of the joint where the weld is applied. Sometimes the weld is located on both sides, needing corresponding symbols.
- Other Side: This specification clarifies if welding is required on the opposite side of the joint. A symbol on the other side of the reference line often signifies this.
- Weld Symbol: This symbol indicates the specific type of weld to be executed (e.g., fillet weld, groove weld, spot weld). Variations within these weld types will also have specific symbols.
- Dimensioning: Crucial for specifying weld sizes (leg length, throat depth, etc.). These dimensions are crucial for the welder to achieve the specified weld.
- Process Specification: This often accompanies the symbol to indicate the preferred or required welding process (e.g., SMAW, GMAW, GTAW).
- Finishing Symbols: Symbols indicating post-weld treatments, like grinding or cleaning, are often included for a finished product.
- Supplementary Symbols: These symbols convey additional information, such as the type of joint preparation required, the specific weld profile needed, etc.
Deciphering Common Weld Symbols and Their Applications
Let's examine some of the most prevalent weld symbols you'll encounter in blueprints:
1. Fillet Welds: These welds connect two members at an angle, typically forming a triangular cross-section. The symbol for a fillet weld is a short, slanted line. The length of the line often represents the size (leg length) of the weld. The location of the symbol relative to the reference line indicates where the weld is placed.
2. Groove Welds: These welds are used to join two members edge to edge, creating a continuous joint. The symbol for a groove weld is often a more substantial line, sometimes with details indicating the groove preparation (e.g., V-groove, U-groove, bevel groove). Understanding the different groove types and their corresponding symbols is essential for correct weld preparation.
3. Spot Welds: Used in sheet metal joining, these welds are localized points of fusion. The symbol is usually a small circle or dot located on the reference line, with accompanying specifications on the size and spacing of the welds.
4. Seam Welds: A continuous weld along a seam, commonly used for joining sheet metal or pipe. Its symbol might resemble a continuous wavy line along the reference line.
5. Plug and Slot Welds: Used to reinforce holes, these welds fill holes or slots. They're represented by symbols depicting plugs or slots with dimensions specified.
Understanding Joint Preparations and Their Impact on Welding
Joint preparation is the process of shaping the edges of the members being joined before welding. The type of joint preparation directly affects the weld's quality, strength, and appearance. Blueprints will clearly specify the required joint preparation using symbols and dimensions. Understanding these preparations is vital for the welder:
- Square Groove: A simple joint with minimal preparation. Not ideal for stronger welds.
- V-Groove: A common preparation where the edges are beveled at an angle, creating a V-shaped groove.
- U-Groove: Similar to a V-groove, but with a wider and more rounded groove.
- Bevel Groove: One edge is beveled, and the other is flat.
- J-Groove: A single-bevel groove, typically used for thicker materials.
- Double-Bevel Groove: Both edges are beveled, forming a wider groove.
Welding Processes and Their Representation on Blueprints
The blueprint also specifies the welding process to be used. Each process has unique characteristics affecting the choice of filler metal, parameters, and weld quality. Common welding processes represented on blueprints include:
- Shielded Metal Arc Welding (SMAW): Often denoted by the abbreviation "SMAW" or a specific electrode type.
- Gas Metal Arc Welding (GMAW): This is commonly indicated by "GMAW" or "MIG." The shielding gas used (e.g., CO2, Argon/CO2 mix) might also be specified.
- Gas Tungsten Arc Welding (GTAW): Also known as "TIG" welding, this process uses a non-consumable tungsten electrode. The symbol will likely indicate "GTAW" or "TIG," specifying the shielding gas if necessary.
- Submerged Arc Welding (SAW): For high-volume applications, this process often requires a specific symbol indicating the submerged arc technique.
Interpreting Supplementary Symbols and Additional Specifications
Beyond the fundamental welding symbols, blueprints may include supplementary symbols providing additional details:
- Weld All Around: This specifies that the weld should encompass the entire perimeter of the joint.
- Intermittent Welds: These are welds applied at intervals, rather than continuously. The blueprint will specify the length and spacing of these intermittent welds.
- Field Welds: Welds performed outside the factory or controlled environment. This often requires additional considerations.
- Weld Reinforcement: Indicates the amount of weld metal extending beyond the joint surface.
- Finish Symbols: These symbols denote post-weld finishing requirements, such as grinding, chipping, or cleaning.
Practical Application and Problem-Solving
The real test of your understanding lies in practical application. To solidify your understanding of Unit 6, practice interpreting various welding symbols and their accompanying specifications. Work through example blueprints, focusing on identifying each element of the symbol and understanding its implications for the welding process.
Consider creating your own practice blueprints. Sketch a simple joint and design your own weld symbols, specifying weld types, dimensions, processes, and supplementary details. This hands-on approach will significantly reinforce your knowledge and improve your ability to decipher complex blueprints.
Advanced Concepts and Beyond Unit 6
While Unit 6 focuses on the fundamentals, continued learning is crucial for professional growth. Explore advanced concepts such as:
- Weldability of Different Materials: Understanding the properties of different metals and their suitability for various welding processes is vital.
- Weld Defects and Their Prevention: Familiarity with common weld defects and methods for their prevention is crucial for quality control.
- Welding Codes and Standards: Adherence to relevant codes and standards is essential for ensuring the safety and integrity of welds.
- Welding Procedures: Development and implementation of detailed welding procedures based on blueprint specifications.
By mastering the content of Unit 6 and expanding your knowledge beyond it, you’ll become a more proficient and knowledgeable welder, capable of accurately interpreting blueprints, executing high-quality welds, and contributing significantly to any welding project. Remember, consistent practice and a keen eye for detail are key to becoming a master of blueprint reading for welders.
Latest Posts
Latest Posts
-
A Small Hair Salon In Denver Colorado Averages About
May 07, 2025
-
Match The Earthquake Term With Its Correct Description
May 07, 2025
-
Which Of The Following Statements About Privacy Act Are True
May 07, 2025
-
Choose The Best Translation Actually Actualmente Atender En Verdad Sensible
May 07, 2025
-
Methodological Behaviorism Is Equivalent To Psychological Positivism
May 07, 2025
Related Post
Thank you for visiting our website which covers about Blueprint Reading For Welders 9th Edition Answer Key Unit 6 . We hope the information provided has been useful to you. Feel free to contact us if you have any questions or need further assistance. See you next time and don't miss to bookmark.