Bruce Corporation Makes Four Products In A Single Facility
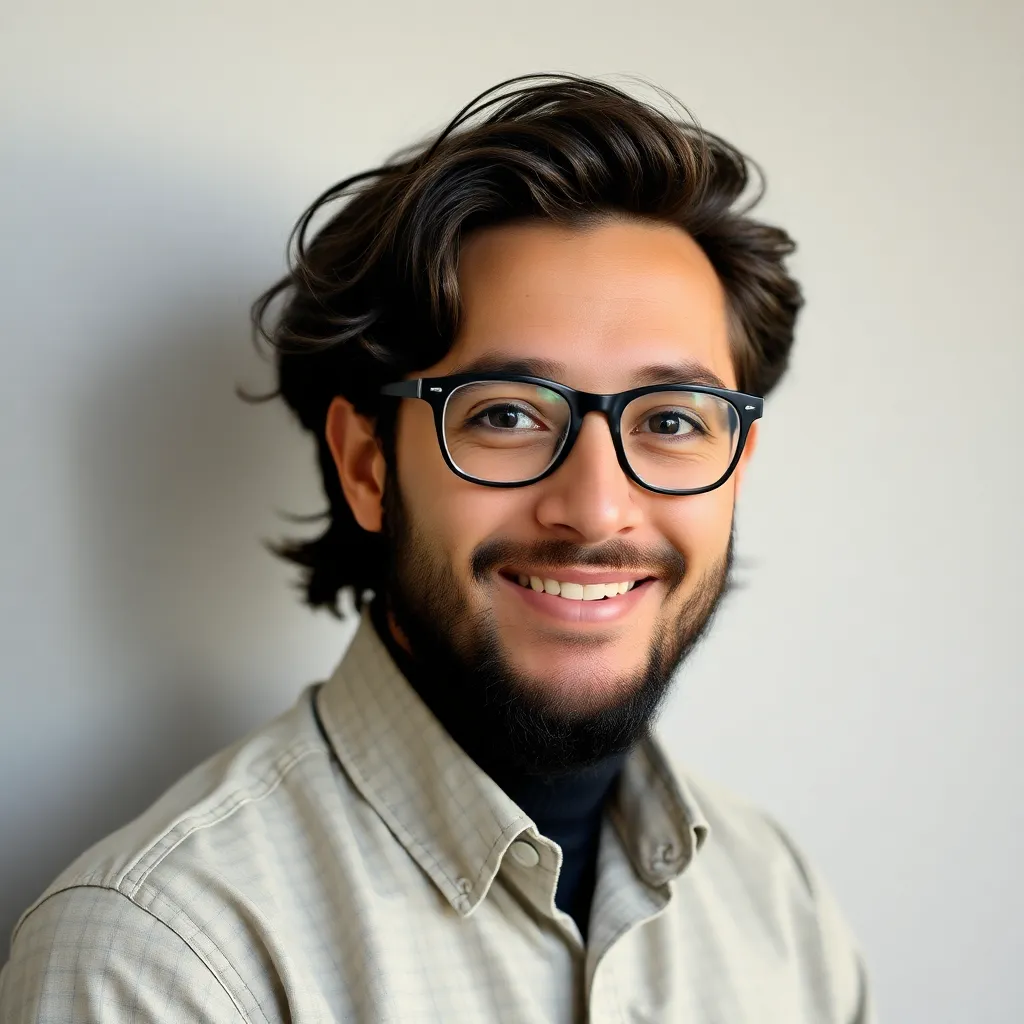
Onlines
May 09, 2025 · 6 min read
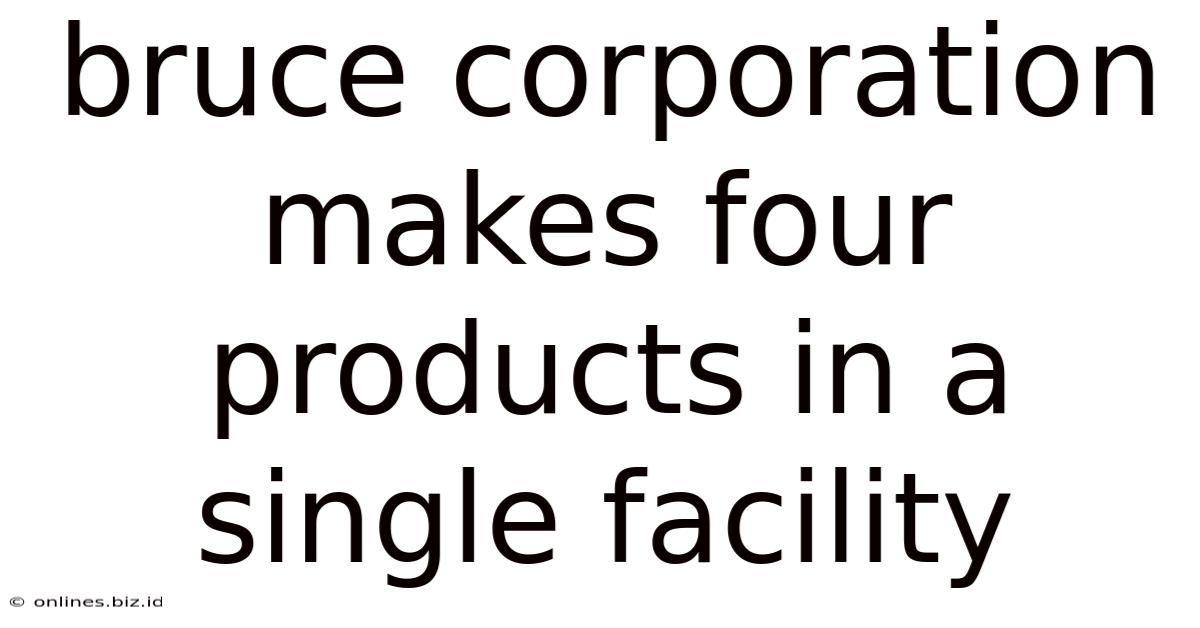
Table of Contents
Bruce Corporation: Optimizing Multi-Product Production in a Single Facility
Bruce Corporation, a hypothetical manufacturing giant, presents a fascinating case study in operational efficiency. Their single facility houses the production of four distinct products, demanding a sophisticated approach to resource allocation, inventory management, and overall production planning. This article delves deep into the challenges and potential solutions Bruce Corporation faces in streamlining their multi-product operation, exploring best practices in manufacturing management and highlighting key strategies for maximizing profitability and minimizing waste.
The Four Products: A Diverse Portfolio
Bruce Corporation's product portfolio showcases a considerable degree of diversity. Let's assume, for the sake of illustration, these four products are:
-
Product A: A high-volume, low-margin product demanding efficient, automated production lines. Think of a standard commodity item, perhaps a basic plastic component used in various industries. High demand necessitates consistent, high-throughput manufacturing.
-
Product B: A medium-volume, medium-margin product requiring a balance between automation and skilled labor. This could be a more specialized component requiring precision assembly and quality control checks. Demand is stable but not as high as Product A.
-
Product C: A low-volume, high-margin product demanding highly skilled labor and meticulous attention to detail. This might represent a customized or bespoke product with a niche market. Flexibility and adaptability are paramount.
-
Product D: A seasonal product with fluctuating demand, requiring flexible manufacturing capabilities and effective inventory management. This could be a product tied to specific times of the year, like holiday decorations or seasonal clothing. Predicting demand accurately is crucial.
Challenges of Multi-Product Manufacturing
Producing four vastly different products within a single facility introduces a multitude of challenges:
1. Resource Allocation and Capacity Planning:
Efficiently allocating resources—machinery, labor, raw materials—across four distinct production lines is critical. Over-allocation to one product can lead to bottlenecks and delays in others. Under-allocation, on the other hand, can result in unmet demand and lost revenue. Effective capacity planning, considering both current and forecasted demand, is essential. This often involves employing sophisticated forecasting models and production scheduling software.
2. Inventory Management:
Balancing inventory levels for four products with varying demand profiles is a complex undertaking. Overstocking of slow-moving products ties up capital and increases storage costs. Understocking, however, can lead to production delays and lost sales. Implementing a robust inventory management system, potentially using just-in-time (JIT) inventory techniques for high-volume products and safety stock for products with fluctuating demand, is crucial.
3. Production Scheduling and Sequencing:
Determining the optimal production sequence for the four products to minimize setup times and maximize throughput is a significant challenge. Switching between production lines for different products inevitably results in downtime. Advanced scheduling algorithms and techniques like lean manufacturing principles (e.g., minimizing waste, maximizing flow) can help optimize the production sequence.
4. Quality Control and Assurance:
Maintaining consistent quality across four diverse product lines demands a rigorous quality control system. Each product has its specific quality standards and testing requirements. Implementing comprehensive quality checks at each stage of production, incorporating statistical process control (SPC), and investing in quality management systems (QMS) are vital for maintaining product excellence.
5. Skilled Labor Management:
The varying skill requirements for the four products necessitate a diverse and well-trained workforce. Recruiting, training, and retaining skilled labor across different specializations can be costly and challenging. Investing in employee development programs and implementing a robust talent management system are crucial for maintaining a skilled and efficient workforce.
Strategies for Optimizing Multi-Product Production
To overcome these challenges, Bruce Corporation can implement various strategies:
1. Implementing Lean Manufacturing Principles:
Adopting lean manufacturing principles, focusing on eliminating waste (muda) in all its forms – overproduction, waiting, transportation, over-processing, inventory, motion, and defects – can significantly improve efficiency. Value stream mapping can help identify areas for improvement in the production process. Kaizen (continuous improvement) events can foster a culture of ongoing optimization.
2. Employing Advanced Production Scheduling Software:
Investing in sophisticated production scheduling software allows Bruce Corporation to optimize production sequencing, resource allocation, and inventory management. These systems can consider various factors, including demand forecasts, production capacity, setup times, and inventory levels, to generate optimal production schedules.
3. Utilizing Enterprise Resource Planning (ERP) Systems:
An integrated ERP system provides real-time visibility into all aspects of the business, from production planning and inventory management to sales and finance. This allows for better decision-making, improved coordination across departments, and enhanced overall efficiency.
4. Implementing Just-in-Time (JIT) Inventory Management:
For high-volume products like Product A, implementing JIT inventory can significantly reduce inventory holding costs and improve cash flow. This requires close collaboration with suppliers to ensure timely delivery of raw materials.
5. Employing Flexible Manufacturing Systems (FMS):
Investing in flexible manufacturing systems allows Bruce Corporation to adapt quickly to changes in demand and product specifications. FMS utilizes programmable machines and automated material handling systems to efficiently produce different products on the same production lines.
6. Investing in Automation and Robotics:
Automating repetitive tasks, especially in the high-volume production of Product A, can increase efficiency, reduce labor costs, and improve product consistency. Robotics can play a crucial role in automating various aspects of the production process, from material handling to assembly.
7. Implementing a Robust Quality Management System:
A comprehensive quality management system, encompassing all aspects of production, is crucial for maintaining consistent product quality across all four product lines. This includes regular quality checks, statistical process control, and continuous improvement initiatives.
Long-Term Strategic Considerations
Beyond immediate operational improvements, Bruce Corporation should consider several long-term strategic initiatives:
-
Market Analysis and Forecasting: Understanding market trends and accurately forecasting demand for each product is essential for effective capacity planning and inventory management. This requires robust market research and the utilization of advanced forecasting techniques.
-
Product Diversification Strategy: While producing four products already provides diversification, continually evaluating the market and exploring opportunities for new product development can help mitigate risks associated with relying on a limited product portfolio.
-
Technological Advancements: Staying abreast of technological advancements in manufacturing, such as additive manufacturing (3D printing), artificial intelligence (AI), and the Internet of Things (IoT), can provide competitive advantages and improve operational efficiency.
-
Supply Chain Optimization: Analyzing and optimizing the entire supply chain, from raw material sourcing to product distribution, can reduce costs, improve lead times, and enhance overall responsiveness to market demands.
-
Sustainability Initiatives: Implementing sustainable manufacturing practices can reduce environmental impact, improve corporate social responsibility, and potentially attract environmentally conscious customers.
Conclusion: A Path to Sustainable Success
Bruce Corporation's challenge of efficiently managing four distinct products within a single facility presents a complex yet solvable problem. By strategically implementing lean manufacturing principles, investing in advanced technologies, and fostering a culture of continuous improvement, Bruce Corporation can optimize its operations, improve efficiency, and achieve sustainable, long-term success. This requires a holistic approach that integrates production planning, inventory management, quality control, and strategic decision-making to navigate the complexities of multi-product manufacturing and secure a leading position in its respective markets. The journey requires ongoing adaptation and refinement, but the potential rewards – increased profitability, enhanced efficiency, and strengthened market position – make it a worthwhile endeavor.
Latest Posts
Latest Posts
-
Jayda Started A Corporation That Creates Software Products For Clients
May 10, 2025
-
Through Their Actions Project Managers Can Convey A Sense Of
May 10, 2025
-
What Can You Conclude From The Graph
May 10, 2025
-
A Job Analysis Results In Two Written Statements They Are
May 10, 2025
-
Which Of The Following Are Used To Control Bleeding Sere
May 10, 2025
Related Post
Thank you for visiting our website which covers about Bruce Corporation Makes Four Products In A Single Facility . We hope the information provided has been useful to you. Feel free to contact us if you have any questions or need further assistance. See you next time and don't miss to bookmark.