Cam-ground Pistons Are Installed In Some Aircraft Engines To
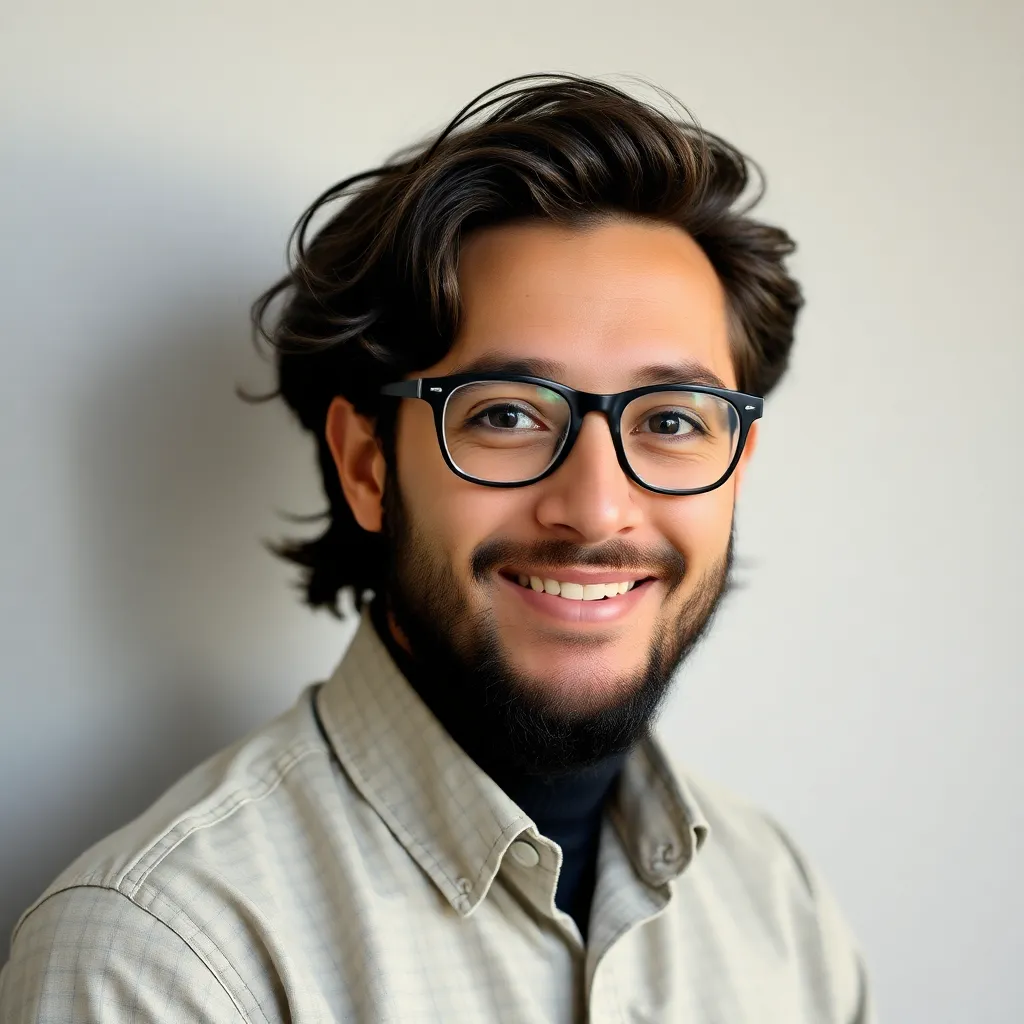
Onlines
May 11, 2025 · 6 min read
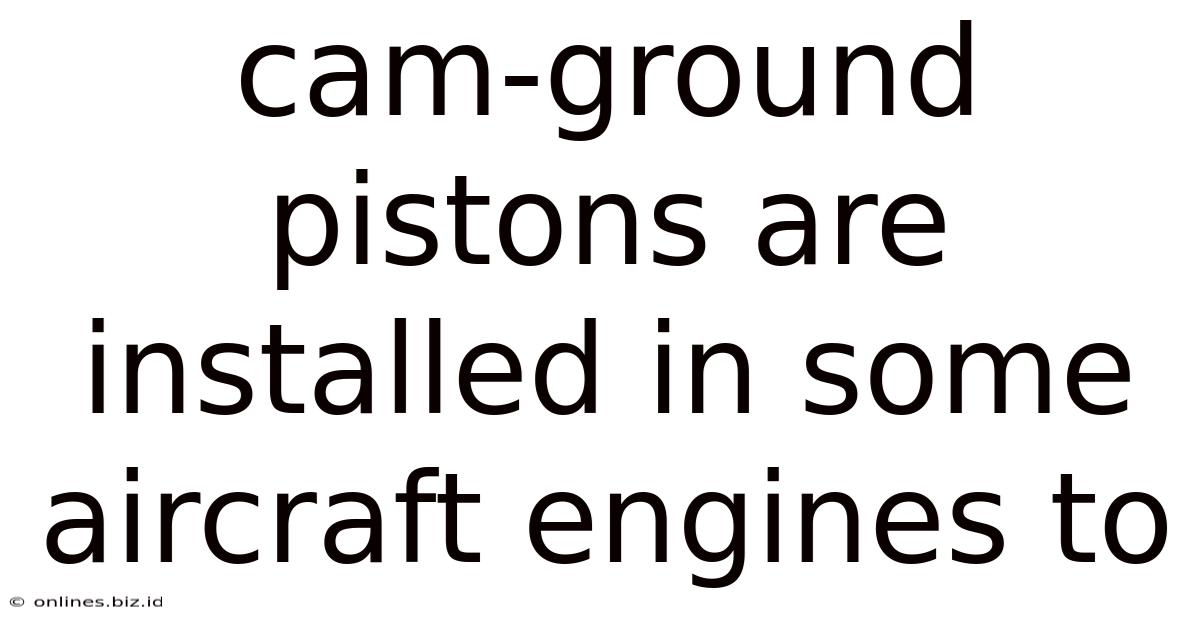
Table of Contents
Cam-Ground Pistons: A Deep Dive into Aircraft Engine Design
Cam-ground pistons represent a fascinating aspect of aircraft engine design, often overlooked by those unfamiliar with internal combustion intricacies. Their specific application and the reasons behind their choice are crucial to understanding the performance and longevity of certain aircraft powerplants. This article delves into the specifics of cam-ground pistons, exploring their design, advantages, disadvantages, and why they're employed in some aircraft engines, but not others.
Understanding Piston Design Basics
Before diving into the nuances of cam-ground pistons, it’s essential to establish a foundational understanding of piston design principles. Pistons, in their most basic form, are cylindrical components that reciprocate within the cylinder of an engine, converting the energy of combustion into mechanical work. Key design features influencing performance and longevity include:
Material Selection:
The material choice for a piston is critical. Aircraft engines often utilize high-strength aluminum alloys for their lightweight yet robust characteristics. These alloys must withstand extreme temperatures, pressures, and cyclic stresses. Other materials, such as forged steel, might be employed in specialized applications requiring even greater durability.
Skirt Design:
The piston skirt is the lower portion of the piston, responsible for maintaining alignment and minimizing friction within the cylinder. Skirt design can significantly affect engine performance and efficiency. Different skirt designs are optimized for specific operating conditions and engine types.
Piston Rings:
Piston rings are critical components sealing the combustion chamber, preventing the leakage of combustion gases past the piston. They also help control oil consumption by scraping excess oil from the cylinder wall. The material, number, and design of the piston rings are carefully selected to match the engine's operating parameters.
Pin and Connecting Rod:
The piston pin connects the piston to the connecting rod, which in turn transfers the piston's reciprocating motion to the crankshaft, converting it into rotational energy. The design and material selection of the pin and connecting rod are optimized for strength, durability, and minimal weight.
Cam-Ground Pistons: A Closer Look
Cam-ground pistons represent a specific machining process that results in a unique piston skirt design. Instead of a perfectly cylindrical skirt, cam-ground pistons feature a slightly elliptical or cam-shaped skirt. This non-circular profile offers several advantages, primarily concerning piston-to-cylinder wall contact and friction reduction.
The Cam-Grinding Process
The cam-grounding process uses specialized machinery to precisely shape the piston skirt. This process removes material in a carefully controlled manner, creating the elliptical shape. The precise control of the machining ensures consistent cam shape across all pistons, crucial for engine balance and performance.
Advantages of Cam-Ground Pistons
The distinctive cam shape of cam-ground pistons provides several key benefits:
-
Reduced Friction: The elliptical skirt minimizes the contact area between the piston and the cylinder wall, substantially reducing frictional losses. This leads to improved engine efficiency and reduced wear.
-
Improved Piston Ring Seal: The cam shape helps maintain consistent piston ring pressure against the cylinder wall throughout the piston's stroke, resulting in a more effective combustion seal and lower oil consumption.
-
Enhanced Piston Stability: The cam-ground profile enhances the piston's stability within the cylinder, particularly at high speeds and under high loads, minimizing the potential for piston slap and wear.
-
Better Heat Dissipation: The reduced contact area between the piston and cylinder wall can improve heat transfer from the piston to the cylinder, potentially reducing piston temperature and increasing durability.
Disadvantages of Cam-Ground Pistons
Despite their advantages, cam-ground pistons also have potential drawbacks:
-
Increased Manufacturing Complexity: The specialized machining required to create the cam shape increases manufacturing complexity and cost compared to conventionally machined pistons.
-
Potentially Increased Cylinder Wear: The reduced contact area, while beneficial in terms of friction reduction, could increase the risk of localized wear on the cylinder wall, particularly if not properly lubricated. Precise cylinder honing is critical to mitigate this risk.
-
Sensitivity to Cylinder Condition: The effectiveness of cam-ground pistons relies heavily on the precision of the cylinder bore. Any deviations from the ideal cylinder roundness or surface finish can compromise the benefits of the cam-ground design.
-
Higher Initial Cost: The added manufacturing steps translate into a higher initial cost compared to standard pistons.
Why Cam-Ground Pistons are Used in Some Aircraft Engines
The decision to employ cam-ground pistons in an aircraft engine is a complex one, weighing the advantages against the disadvantages. Several factors influence this decision:
-
High-Performance Applications: Cam-ground pistons often find their place in high-performance aircraft engines where the benefits of reduced friction and improved efficiency are particularly valuable. The slight increase in manufacturing cost is often outweighed by the performance gains.
-
Engine Operating Conditions: Engines subjected to high speeds, high loads, and extreme temperatures could benefit significantly from the enhanced stability and heat dissipation capabilities of cam-ground pistons.
-
Engine Life and Maintenance Costs: While the initial cost is higher, the reduced friction and enhanced durability may translate into extended engine life and lower long-term maintenance costs.
-
Fuel Efficiency: The gains in fuel efficiency resulting from the reduced friction can be a significant factor in the operational economics of an aircraft, especially for commercial or long-haul applications.
-
Specific Engine Design: The overall engine design, including cylinder bore characteristics and lubrication system capabilities, will also influence the suitability of cam-ground pistons.
Comparison with Other Piston Designs
To fully appreciate the role of cam-ground pistons, it's useful to compare them with other piston designs commonly found in aircraft engines:
Standard Pistons:
These are conventionally machined pistons with a cylindrical skirt. They are simpler and less expensive to manufacture but may exhibit higher friction and less stability compared to cam-ground pistons.
Forged Pistons:
Forged pistons are manufactured using a forging process, resulting in superior strength and durability compared to cast pistons. They can be either standard or cam-ground designs.
Slipper Pistons:
Slipper pistons are characterized by a reduced skirt area, often employing a slipper-like shape at the bottom. They can reduce friction, but not to the same extent as cam-ground pistons.
Maintenance Considerations for Cam-Ground Pistons
Proper maintenance is crucial to ensure the optimal performance and longevity of cam-ground pistons. This includes:
-
Regular Oil Changes: Using high-quality engine oil at the recommended intervals helps maintain effective lubrication and minimize wear on both the pistons and cylinder walls.
-
Proper Cylinder Honing: Maintaining the precision of the cylinder bore is vital for the efficient functioning of cam-ground pistons.
-
Careful Inspection: Regular engine inspections should include careful examination of the pistons and cylinder walls for any signs of wear, scoring, or damage.
Conclusion: Optimizing Aircraft Engine Performance
Cam-ground pistons represent a sophisticated advancement in piston design, offering significant performance benefits in specific aircraft engine applications. While they come with increased manufacturing complexity and cost, the gains in efficiency, durability, and overall engine performance often justify their use in high-performance or demanding environments. Their effectiveness hinges on careful engine design, precise manufacturing, and rigorous maintenance practices. The choice between cam-ground and other piston designs is a complex engineering decision driven by a careful consideration of operational needs, cost-benefit analysis, and long-term operational efficiency. Understanding these factors is key to appreciating the sophisticated engineering behind the power plants that propel the world's aircraft.
Latest Posts
Latest Posts
-
The Sociological Study Of Masculinities Demonstrates That
May 11, 2025
-
A Requirement Of Two Resource Sequencing Rule Is That
May 11, 2025
-
Developing An Explanation For Tuskless Elephants Answer Key
May 11, 2025
-
One Of Your Co Workers Yuri Found Classified
May 11, 2025
-
Rewrite The Exchange Between The Two Friars
May 11, 2025
Related Post
Thank you for visiting our website which covers about Cam-ground Pistons Are Installed In Some Aircraft Engines To . We hope the information provided has been useful to you. Feel free to contact us if you have any questions or need further assistance. See you next time and don't miss to bookmark.