Cellular Manufacturing Combines Aspects Of Both
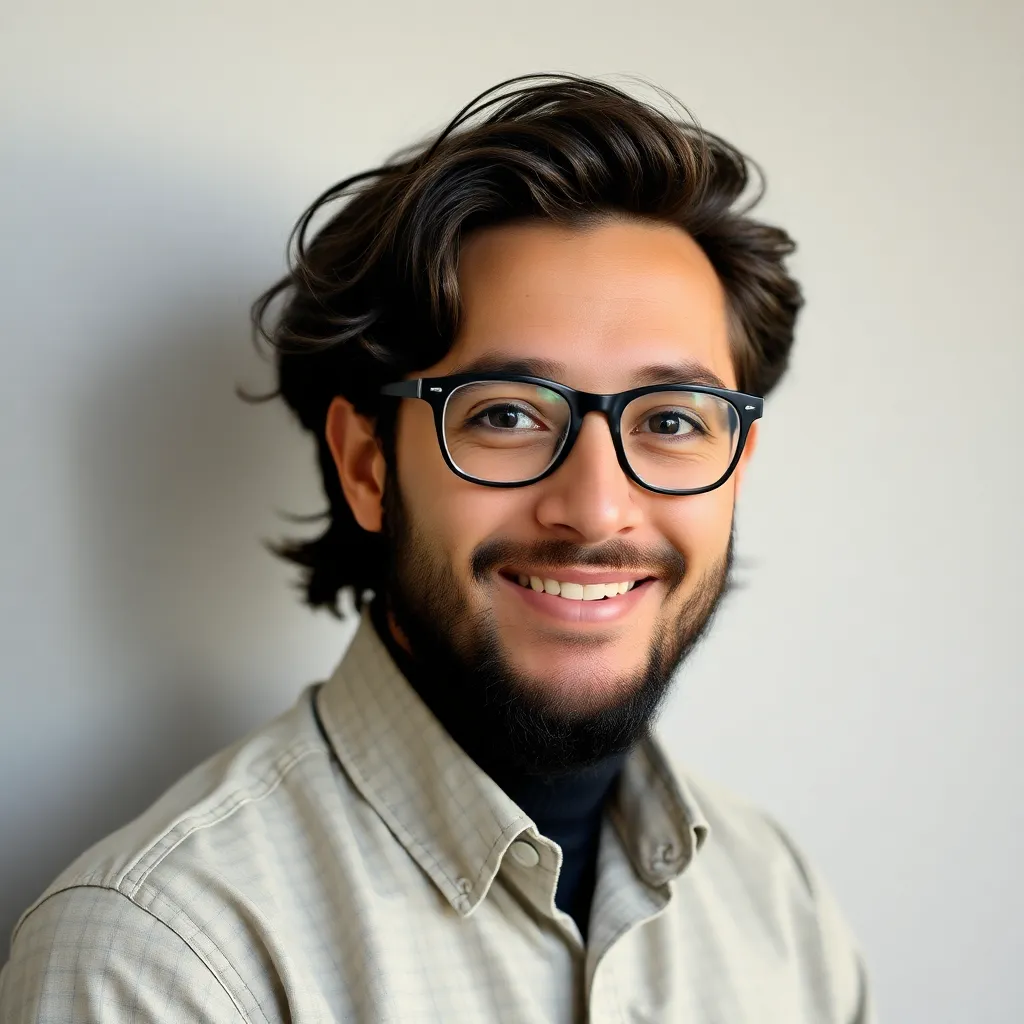
Onlines
May 10, 2025 · 6 min read
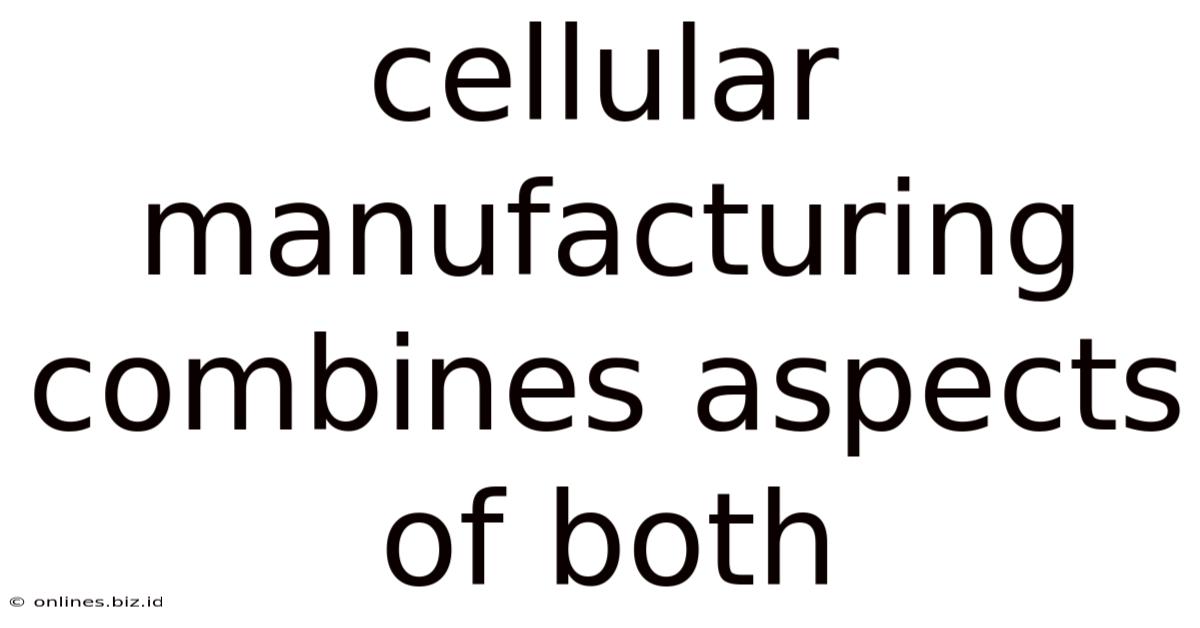
Table of Contents
Cellular Manufacturing: A Hybrid Approach Combining the Best of Batch and Continuous Production
Cellular manufacturing represents a significant advancement in manufacturing methodologies, cleverly blending the strengths of both batch and continuous production systems. This hybrid approach offers a compelling solution for manufacturers seeking to enhance efficiency, flexibility, and overall productivity. Understanding its core principles and the advantages it provides is crucial for businesses looking to optimize their operations. This article delves deep into the nature of cellular manufacturing, exploring its characteristics, benefits, implementation strategies, and the challenges associated with its adoption.
Understanding the Fundamentals of Cellular Manufacturing
Cellular manufacturing organizes machines and workers into self-contained cells, each dedicated to producing a family of similar parts or products. This contrasts sharply with traditional job shop or mass production methods. In a job shop, individual machines are scattered, and parts move between them in a sequential, often chaotic manner. Mass production, on the other hand, relies on a highly specialized, linear assembly line, generally unsuitable for diversified product ranges.
Cellular manufacturing bridges this gap. It borrows the efficiency of specialized setups from mass production while retaining the flexibility of a job shop in handling variations in product demand. The key is the creation of these "cells," which are mini-factories within the larger facility. Each cell is designed to handle a specific product family, minimizing material handling and maximizing efficiency through dedicated machinery and skilled personnel.
Key Characteristics of Cellular Manufacturing:
- Product Family Focus: Parts within a family share similar processing requirements, allowing for efficient cell design and setup.
- U-Shaped Cell Layout: This common configuration minimizes movement of parts and materials within the cell, maximizing throughput and minimizing waste.
- Reduced Work-in-Process (WIP): The compact nature of cells minimizes the inventory of parts in various stages of production.
- Improved Flow: Materials and information move smoothly through the cell, resulting in faster cycle times.
- Increased Worker Involvement: Cell members often assume a greater degree of responsibility and autonomy, enhancing job satisfaction and quality control.
- Reduced Setup Times: Dedicated machinery and tooling within each cell lead to significantly shorter setup times compared to traditional methods.
The Advantages of Cellular Manufacturing:
The benefits of adopting cellular manufacturing extend across various aspects of a manufacturing operation:
1. Enhanced Productivity and Efficiency:
By streamlining processes and reducing material handling, cellular manufacturing significantly boosts productivity. The optimized layout and dedicated equipment minimize wasted time and resources, resulting in quicker cycle times and higher output.
2. Increased Flexibility and Responsiveness:
Cellular manufacturing offers a degree of flexibility unmatched by traditional mass production lines. It can adapt to changing customer demands and product variations more easily because individual cells can be reconfigured or retooled with relative ease.
3. Improved Quality Control:
The reduced complexity and increased worker involvement in cellular manufacturing often lead to improved quality control. Workers are more closely involved in the entire process, enabling quicker identification and correction of defects.
4. Reduced Inventory Costs:
The minimized WIP within cellular manufacturing systems leads to significantly lower inventory carrying costs. This frees up capital and reduces storage space requirements.
5. Enhanced Employee Morale and Job Satisfaction:
The increased worker empowerment and autonomy within cellular manufacturing often translate into higher job satisfaction and improved morale. Workers take pride in their contributions and the finished product, leading to increased productivity and decreased absenteeism.
6. Shorter Lead Times:
The streamlined workflow and reduced bottlenecks inherent in cellular manufacturing dramatically shorten lead times, allowing for faster delivery of products to customers.
7. Reduced Manufacturing Costs:
The combined effect of increased efficiency, reduced inventory, improved quality, and shorter lead times ultimately translates into lower overall manufacturing costs.
Implementing Cellular Manufacturing:
The successful implementation of cellular manufacturing requires a careful and systematic approach. Several key steps are essential:
1. Product Family Selection:
The first crucial step is identifying suitable product families for cell formation. This requires a detailed analysis of existing products, considering their processing requirements, similarities, and demand patterns. Part families should be formed based on their operational similarities, not just their design similarities. This ensures that the chosen families are truly suitable for cellular manufacturing.
2. Machine Grouping and Cell Design:
Once product families are defined, the next step is to group machines within cells based on the processing requirements of each product family. This often involves analyzing process flow charts and considering factors such as machine capacity, setup times, and material handling requirements. The optimal cell layout, often U-shaped, should minimize movement within the cell. Careful consideration must be given to machine placement to maximize efficiency and minimize bottlenecks.
3. Cell Layout and Design Optimization:
This stage involves optimizing the physical layout of the machines and workstations within the cell, ensuring an efficient and ergonomic workspace. This may involve the use of specialized software tools to simulate and analyze different layout options.
4. Workload Balancing:
Careful consideration must be given to balancing the workload across different workstations within the cell. This is crucial for maintaining a smooth and efficient workflow and preventing bottlenecks.
5. Training and Employee Involvement:
Effective training of cell members is vital for the successful implementation of cellular manufacturing. Workers need to understand their roles, responsibilities, and the overall processes within the cell. Employee involvement in the design and implementation process is crucial for fostering buy-in and commitment.
6. Continuous Improvement and Monitoring:
Once a cellular manufacturing system is implemented, it's crucial to continuously monitor its performance and make necessary improvements. This involves tracking key metrics such as cycle times, throughput, and defect rates, and implementing corrective actions when necessary. Regular review and adaptation are essential for maintaining the effectiveness of the cellular manufacturing system in the long term.
Challenges in Implementing Cellular Manufacturing:
While cellular manufacturing offers significant advantages, its implementation presents certain challenges:
1. Initial Investment Costs:
The initial investment required for reconfiguring machinery and tooling can be substantial. This may include purchasing new equipment or relocating existing machines.
2. Resistance to Change:
Introducing a new manufacturing system can encounter resistance from employees accustomed to traditional methods. Careful change management strategies are essential to overcome this resistance.
3. Complexity of Implementation:
Implementing cellular manufacturing can be complex, requiring detailed planning, analysis, and coordination. It necessitates a thorough understanding of the manufacturing processes and the capabilities of the workforce.
4. Balancing Workload:
Achieving a balanced workload across workstations within each cell can be a significant challenge. Inadequate workload balancing can lead to bottlenecks and inefficiencies.
5. Product Variety and Demand Fluctuations:
Cellular manufacturing can be less adaptable to significant changes in product variety or demand fluctuations compared to more flexible job-shop environments. However, careful cell design and flexible cell layout can mitigate this to some extent.
6. Maintaining Skilled Workforce:
Cellular manufacturing requires a skilled workforce capable of operating multiple machines and performing multiple tasks. Training and development programs are crucial to maintain a skilled workforce.
Conclusion:
Cellular manufacturing provides a powerful approach to manufacturing optimization, blending the best aspects of batch and continuous production. Its focus on efficiency, flexibility, and worker empowerment offers substantial benefits for businesses seeking to improve their competitiveness. While implementation challenges exist, careful planning, effective training, and a commitment to continuous improvement can overcome these hurdles and unlock the full potential of cellular manufacturing. By carefully considering the factors discussed in this article, manufacturers can make informed decisions about the suitability of cellular manufacturing for their specific operational contexts and reap the rewards of this powerful hybrid approach. The successful adoption of cellular manufacturing demonstrates a commitment to continuous improvement and a forward-thinking approach to manufacturing that benefits both the business and its employees.
Latest Posts
Latest Posts
-
The Macromolecule That Runs Your Body And Expresses Your Traits
May 11, 2025
-
Center For Writing Excellence University Of Phoenix
May 11, 2025
-
Gold Forms A Substitutional Solid Solution With Silver
May 11, 2025
-
Because God Is Self Sending God
May 11, 2025
-
Kpv Enterprises Charge On Credit Card
May 11, 2025
Related Post
Thank you for visiting our website which covers about Cellular Manufacturing Combines Aspects Of Both . We hope the information provided has been useful to you. Feel free to contact us if you have any questions or need further assistance. See you next time and don't miss to bookmark.