Changeover Reduction Is Best Described As
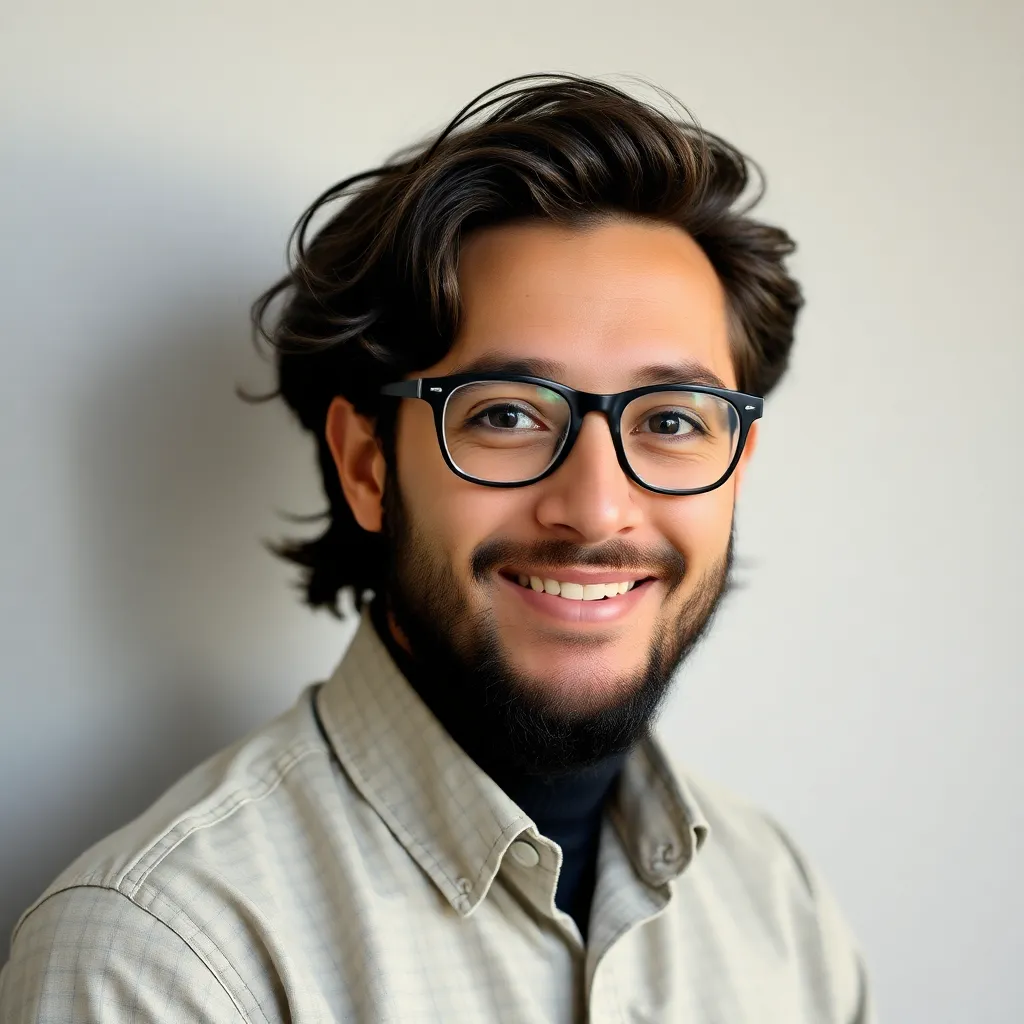
Onlines
May 10, 2025 · 5 min read
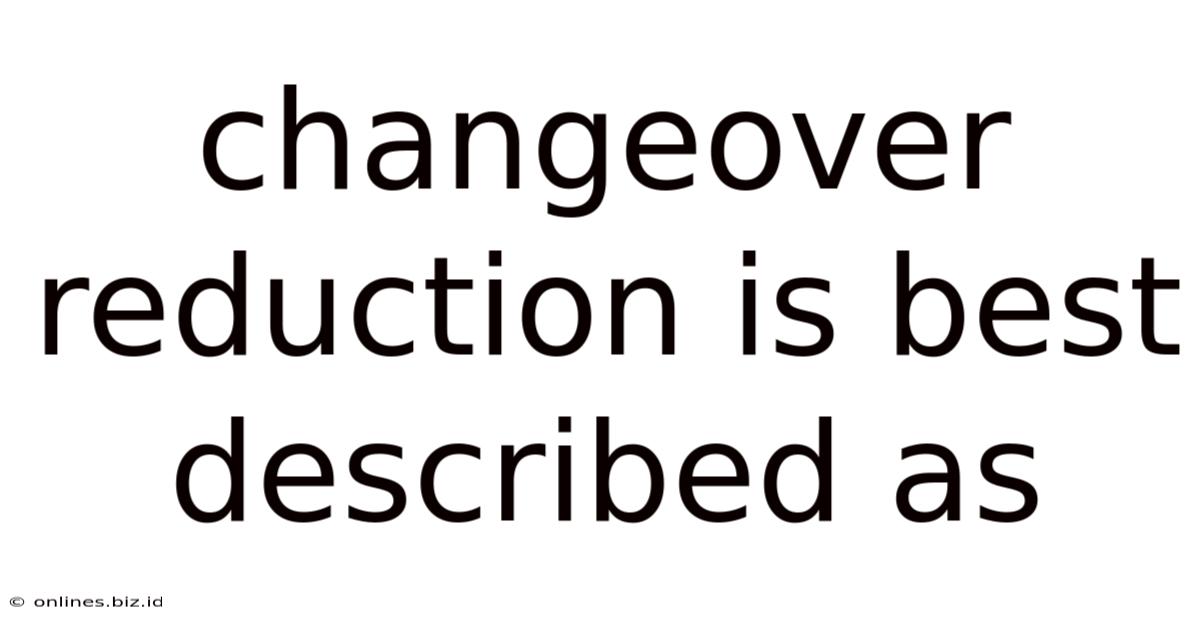
Table of Contents
Changeover Reduction: The Ultimate Guide to Lean Manufacturing Efficiency
Changeover reduction, also known as setup reduction, is a crucial lean manufacturing principle focused on minimizing the time and resources required to switch between different products or production processes. It's not just about speed; it's about eliminating waste, improving flexibility, and boosting overall manufacturing efficiency. This comprehensive guide delves deep into the intricacies of changeover reduction, exploring its benefits, methodologies, and practical implementation strategies.
Understanding the Impact of Changeovers
Before diving into the solutions, it's essential to understand the significant impact lengthy changeovers have on manufacturing operations. Prolonged changeover times directly contribute to:
1. Increased Downtime:
Machines stand idle during changeovers, representing lost production time and directly impacting output. This downtime translates into lost revenue and missed deadlines.
2. Higher Inventory Costs:
To buffer against the downtime caused by changeovers, manufacturers often hold larger inventories of work-in-progress (WIP) and finished goods. This increases storage costs, ties up capital, and increases the risk of obsolescence.
3. Reduced Productivity:
The overall productivity of the manufacturing process suffers due to the interruption caused by frequent and lengthy changeovers. This leads to decreased efficiency and increased unit costs.
4. Bottlenecks in Production:
Long changeovers can create bottlenecks in the production line, disrupting the smooth flow of materials and finished goods. This disruption can have a ripple effect, impacting downstream processes.
5. Increased Labor Costs:
Changeovers often require significant labor input, increasing labor costs. Moreover, the time spent on changeovers could be used for more productive activities.
6. Lower Quality:
Rushed changeovers can lead to errors and defects, impacting the quality of the products and potentially leading to increased scrap and rework.
The SMED Methodology: A Cornerstone of Changeover Reduction
Single-Minute Exchange of Die (SMED) is a highly effective methodology for drastically reducing changeover times. Developed by Shigeo Shingo, a pioneer in lean manufacturing, SMED focuses on separating internal and external changeover activities.
Internal Changeovers:
These activities can only be performed while the machine is stopped. The goal is to minimize the number of these activities, making the actual changeover as short as possible.
External Changeovers:
These activities can be performed while the machine is still running. The key here is to pre-position tools, materials, and components so they're ready when the machine stops.
Implementing SMED involves a systematic approach:
-
Identify and Document Current Changeover Process: Start by meticulously documenting every step of the current changeover process, including the time taken for each step.
-
Separate Internal and External Activities: Analyze the documented process to identify activities that can be performed while the machine is running (external) and those that require the machine to be stopped (internal).
-
Convert Internal to External Activities: This is the core of SMED. Focus on converting as many internal activities as possible into external activities through careful planning and preparation. This often involves using tools and techniques like pre-setting, standardization, and improved tooling.
-
Streamline and Simplify: After converting internal activities, optimize both internal and external processes by eliminating unnecessary steps, improving workflows, and implementing efficient methods.
-
Continuous Improvement: SMED is an iterative process. Continuously monitor, evaluate, and improve the changeover process to further reduce times.
Beyond SMED: Additional Strategies for Changeover Reduction
While SMED is a powerful tool, several other strategies can be employed to enhance changeover reduction efforts:
1. Standardization:
Standardize tools, procedures, and materials to ensure consistency and minimize the time required for adjustments and corrections during changeovers. This also reduces variability and increases predictability.
2. 5S Methodology:
Implement 5S (Sort, Set in Order, Shine, Standardize, Sustain) to create a clean, organized, and efficient work environment. This minimizes the time spent searching for tools and materials, streamlining the changeover process.
3. Poka-Yoke (Mistake-Proofing):
Implement poka-yoke techniques to prevent errors during changeovers. This can involve using visual aids, jigs, and fixtures to guide operators and ensure consistent performance.
4. Improved Tooling and Fixtures:
Investing in improved tooling and fixtures can significantly reduce changeover times. Quick-change tooling, automated clamping systems, and pre-set tools are examples of such improvements.
5. Training and Empowerment:
Properly trained and empowered operators are key to successful changeover reduction. Provide operators with the necessary training and give them the autonomy to improve the process.
Measuring and Tracking Progress: Key Performance Indicators (KPIs)
Tracking the progress of changeover reduction efforts is vital to ensure their effectiveness. Key Performance Indicators (KPIs) to monitor include:
- Changeover Time: The total time required to complete a changeover. This should be tracked before and after implementing improvements.
- Downtime: The time the machine is idle during the changeover. Reducing downtime is a direct measure of successful changeover reduction.
- Production Output: The number of units produced per shift or per day. Improved changeover times will directly increase output.
- Inventory Levels: Monitor Work-in-Progress (WIP) and finished goods inventory levels. Successful changeover reduction should lead to lower inventory levels.
- Defect Rates: Track the number of defects produced during and after changeovers. Improved changeovers should lead to fewer defects.
Changeover Reduction: A Culture of Continuous Improvement
Successfully implementing changeover reduction requires a culture of continuous improvement. This involves:
- Teamwork and Collaboration: Changeover reduction is a team effort. Involve operators, engineers, and management in the process to leverage collective knowledge and expertise.
- Data-Driven Decision Making: Track KPIs and use data to identify areas for improvement and measure the effectiveness of implemented changes.
- Kaizen Events: Conduct regular Kaizen events (rapid improvement workshops) to focus on specific aspects of the changeover process and identify improvement opportunities.
- Regular Review and Adjustment: Continuously review and adjust the changeover process to reflect evolving needs and technological advancements.
Conclusion: Reaping the Rewards of Reduced Changeovers
Changeover reduction is not merely a cost-cutting measure; it's a strategic initiative that significantly enhances overall manufacturing efficiency. By reducing downtime, improving flexibility, and increasing production output, manufacturers can gain a significant competitive advantage. Implementing methodologies like SMED and incorporating other strategies outlined above, coupled with a commitment to continuous improvement, enables organizations to optimize their manufacturing processes and achieve significant returns on investment. The journey towards efficient changeovers requires dedication, collaboration, and a relentless pursuit of perfection, but the rewards are well worth the effort. This comprehensive approach ensures your manufacturing operations remain agile, competitive, and highly productive in today's dynamic market.
Latest Posts
Latest Posts
-
Aba Diversity And Perception Piecing It Together
May 10, 2025
-
A Nurse Is Caring For A Term Macrosomic Newborn
May 10, 2025
-
Anita Is Designing An Advertisement Poster To Go With
May 10, 2025
-
Which Expression Is Equivalent To This Polynomial Expression
May 10, 2025
-
Summary Of Aldo Leopold The Land Ethic
May 10, 2025
Related Post
Thank you for visiting our website which covers about Changeover Reduction Is Best Described As . We hope the information provided has been useful to you. Feel free to contact us if you have any questions or need further assistance. See you next time and don't miss to bookmark.