Cng Containers Need To Be Inspected _________.
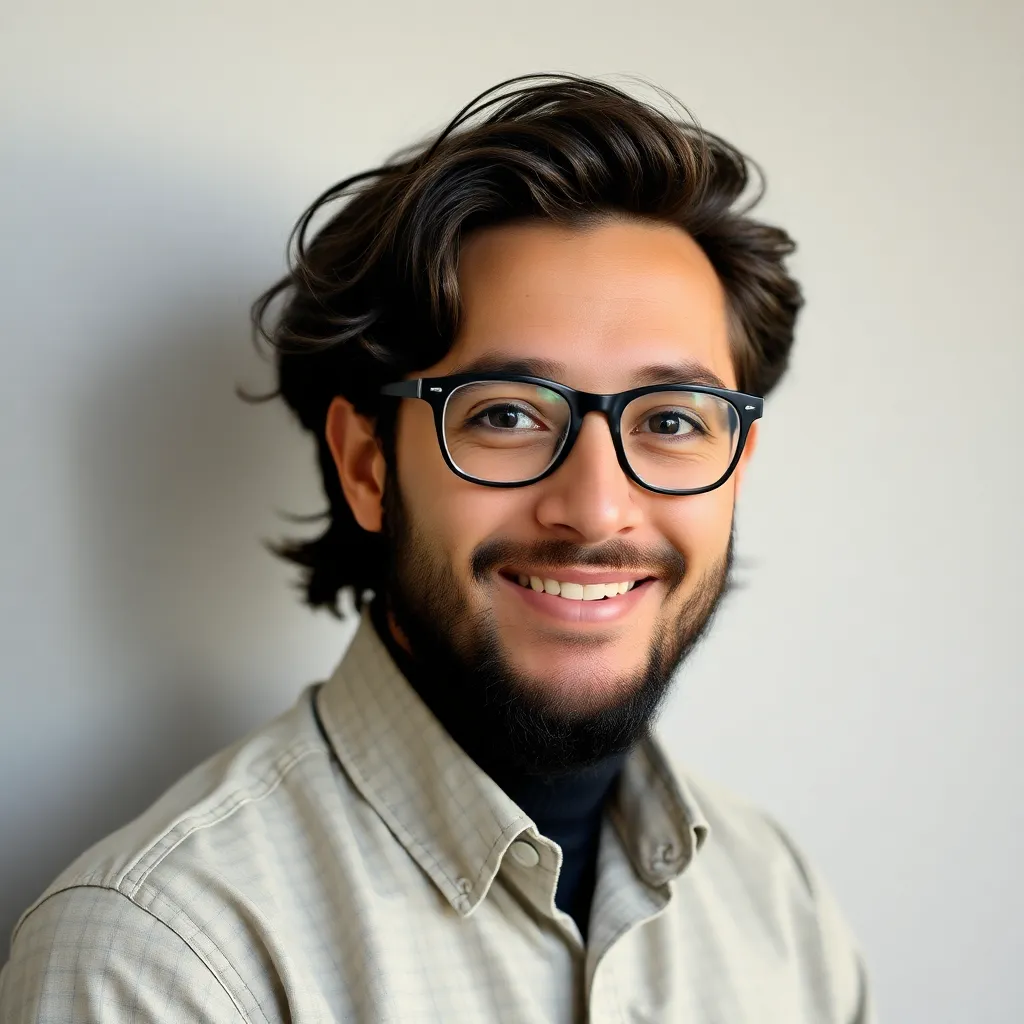
Onlines
Mar 05, 2025 · 6 min read
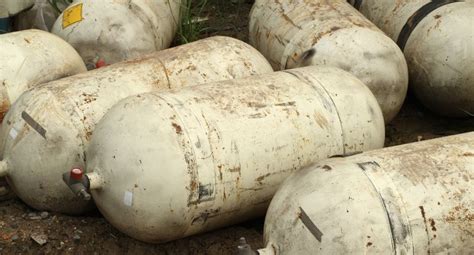
Table of Contents
CNG Containers Need to Be Inspected Regularly: A Comprehensive Guide
Compressed Natural Gas (CNG) containers are vital components in various applications, from powering vehicles to providing fuel for industrial processes. Their safe operation relies heavily on meticulous maintenance and regular inspections. Neglecting these inspections can lead to catastrophic consequences, including explosions, fires, and significant property damage or even loss of life. This comprehensive guide delves into the crucial aspects of CNG container inspections, emphasizing the frequency, methods, and importance of adhering to strict safety protocols.
Why Regular CNG Container Inspections Are Non-Negotiable
The high-pressure environment within CNG containers necessitates rigorous inspection schedules. The constant compression and decompression cycles, along with exposure to various environmental factors, can weaken the container's structural integrity over time. These potential issues include:
Material Degradation:
- Corrosion: Exposure to moisture and other corrosive elements can gradually weaken the container material, increasing the risk of leaks or ruptures.
- Fatigue: Repeated pressure cycles can cause microscopic cracks to form and propagate, eventually compromising the container's strength.
- Embrittlement: Certain environmental factors can make the container material more brittle, making it more susceptible to cracking.
Component Failure:
- Valve malfunctions: Valves are critical components that regulate the flow of CNG. Malfunctions can lead to uncontrolled gas release.
- Pressure gauge inaccuracy: Inaccurate pressure gauges can lead to overfilling or underfilling, both posing significant risks.
- Seal deterioration: Damaged seals can result in gas leaks, creating a hazardous environment.
External Damage:
- Physical impact: Collisions or impacts can cause dents or cracks in the container, compromising its structural integrity.
- Exposure to extreme temperatures: Exposure to extreme heat or cold can negatively affect the container's material properties.
Ignoring these potential issues can lead to:
- Gas leaks: Uncontrolled gas release can lead to asphyxiation, explosions, and fires.
- Container failure: A catastrophic failure can cause significant damage and injury.
- Environmental hazards: CNG leaks contribute to greenhouse gas emissions.
- Compliance violations: Failure to adhere to inspection regulations can result in hefty fines and legal repercussions.
Frequency of CNG Container Inspections: A Detailed Breakdown
The frequency of CNG container inspections varies depending on factors such as:
- Container type: Different container designs and materials have different service life expectancies.
- Operating conditions: Harsh operating environments may require more frequent inspections.
- Regulatory requirements: Local, regional, and national regulations dictate specific inspection schedules.
However, a general guideline is to conduct inspections at least annually, with more frequent checks depending on the aforementioned factors. This includes:
- Visual inspections: These should be conducted regularly, potentially monthly, to check for any visible damage, leaks, or corrosion.
- Hydrostatic testing: This involves filling the container with water under pressure to test its structural integrity. The frequency of hydrostatic testing is usually determined by regulations and container age. It's typically required at specific intervals, often every few years.
- Non-destructive testing (NDT): Techniques such as ultrasonic testing or radiographic testing can be used to detect internal flaws without damaging the container. These tests are usually conducted less frequently than visual inspections or hydrostatic tests but are essential for assessing the container's long-term health.
Specific Inspection Intervals:
While universal standards don't exist, many jurisdictions recommend the following schedule:
- Visual Inspection: Monthly or quarterly, depending on usage and environmental conditions.
- Hydrostatic Test: Every 3-5 years, dependent on container type, usage, and regulations.
- Non-Destructive Testing (NDT): As needed, usually triggered by abnormalities found during visual inspections or hydrostatic tests.
This schedule is a general guideline; always consult the relevant regulations and manufacturer's recommendations for the specific CNG container in use.
What to Look for During CNG Container Inspections
A thorough inspection involves a methodical approach, paying close attention to various aspects of the container. Here's a detailed checklist:
Visual Inspection Checklist:
- External Condition: Check for dents, cracks, corrosion, leaks, or any signs of physical damage. Pay special attention to seams, welds, and valve connections.
- Valve Condition: Inspect the valves for damage, leaks, proper operation, and secure connections. Ensure that the safety devices are functional.
- Pressure Gauge: Verify the accuracy of the pressure gauge. A malfunctioning gauge can lead to overfilling or underfilling, both of which are extremely dangerous.
- Protective Coating: If applicable, check the condition of any protective coatings to ensure they are intact and preventing corrosion.
- Markings and Labels: Confirm that all identification markings and safety labels are legible and clearly visible.
Hydrostatic Test Procedure:
The hydrostatic test is performed by a qualified technician and involves:
- Cleaning: Thoroughly cleaning the container to remove any debris or contaminants.
- Filling with Water: Filling the container with water under controlled pressure.
- Pressure Test: Applying a pressure significantly higher than the operating pressure to assess the container's ability to withstand stress.
- Leak Detection: Carefully inspecting the container for any leaks during and after the pressure test.
- Documentation: Meticulously recording the test results and any observations.
Non-Destructive Testing (NDT) Methods:
NDT techniques provide a detailed assessment of the container's internal condition. Common methods include:
- Ultrasonic Testing: Uses high-frequency sound waves to detect internal flaws.
- Radiographic Testing: Employs X-rays or gamma rays to create images of the container's internal structure.
These tests require specialized equipment and expertise. They're essential for detecting hidden defects that could compromise the container's integrity.
Maintaining Accurate Records: A Crucial Aspect of CNG Safety
Maintaining comprehensive and accurate records of all inspections is paramount. These records must include:
- Date and time of inspection: Precise documentation ensures traceability and compliance.
- Type of inspection: Clearly specify whether it was a visual, hydrostatic, or NDT inspection.
- Inspector's qualifications: Confirmation of the inspector's competence is crucial.
- Inspection findings: Detailed notes on any observed defects or abnormalities.
- Corrective actions: Record of any repairs or replacements made.
- Container identification: Unique identification numbers ensure that records are linked to the correct container.
These records serve as a critical safety and compliance tool, enabling proactive maintenance and preventing potential hazards.
Legal and Regulatory Compliance: Understanding the Rules
Compliance with all relevant local, regional, and national regulations concerning CNG container inspections is non-negotiable. These regulations often specify:
- Inspection frequencies: Mandated schedules for various types of inspections.
- Testing procedures: Specific methods and standards for hydrostatic testing and NDT.
- Record-keeping requirements: Guidelines for maintaining accurate and detailed inspection records.
- Qualified personnel: Specifications for the qualifications and certifications of individuals performing inspections.
Failure to comply with these regulations can result in severe penalties, including hefty fines and legal action.
Conclusion: Prioritizing Safety Through Regular Inspections
Regular inspections are not merely a compliance requirement; they are a critical aspect of ensuring the safe and efficient operation of CNG containers. The potential consequences of neglecting these inspections are too significant to ignore. By adhering to strict inspection schedules, employing qualified personnel, and maintaining meticulous records, we can significantly reduce the risks associated with CNG containers and create a safer environment for everyone. Remember, proactive maintenance is the cornerstone of preventing accidents and ensuring the long-term reliability and safety of these critical components. Prioritizing safety through regular inspections is an investment in safeguarding lives, property, and the environment.
Latest Posts
Latest Posts
-
Rainfall And Bird Beaks Gizmo Answers
Mar 05, 2025
-
The Tall Woman And Her Short Husband Cultural Revolution Effect
Mar 05, 2025
-
The Great Gatsby Summary Chapter By Chapter
Mar 05, 2025
-
Mth1112 Pre Calc With Algebra Formula Sheet
Mar 05, 2025
-
Substance Use Disorder Case Study Reflection Sample
Mar 05, 2025
Related Post
Thank you for visiting our website which covers about Cng Containers Need To Be Inspected _________. . We hope the information provided has been useful to you. Feel free to contact us if you have any questions or need further assistance. See you next time and don't miss to bookmark.