Compared To The Qd Bushing The Split Taper
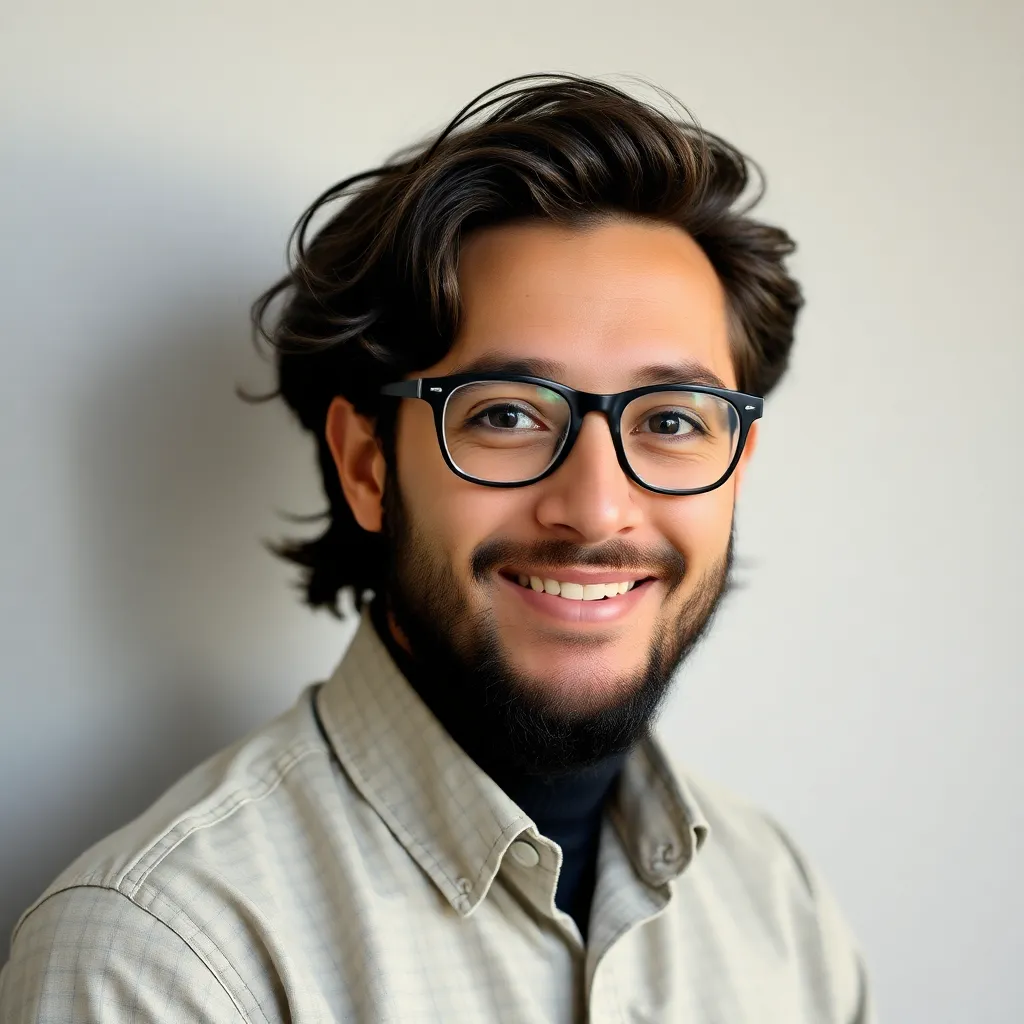
Onlines
May 07, 2025 · 7 min read
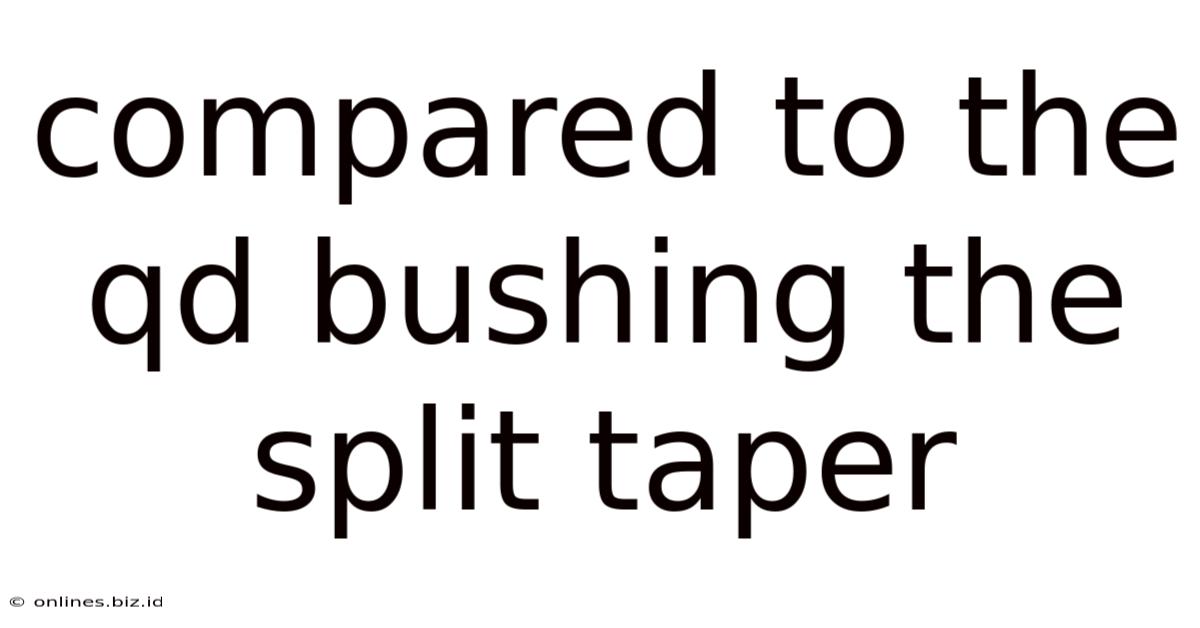
Table of Contents
Split Taper vs. QD Bushing: A Comprehensive Comparison for Enhanced Mechanical Design
Choosing the right bushing type is crucial for ensuring smooth, efficient, and long-lasting performance in various mechanical applications. Two popular choices often debated are split taper bushings and quick disconnect (QD) bushings. While both offer solutions for connecting and aligning components, their designs, applications, and performance characteristics differ significantly. This article delves deep into a comprehensive comparison of split taper and QD bushings, helping you make informed decisions based on your specific needs.
Understanding Split Taper Bushings
Split taper bushings, also known as split clamping bushings, are characterized by their unique construction. As the name suggests, they are split along their length, typically into two halves. This split allows for easy installation and removal without requiring disassembly of the entire assembly. The tapered design ensures a tight, secure fit when the two halves are clamped together, effectively locking the connected components in place.
Advantages of Split Taper Bushings:
- Ease of Installation and Removal: The split design significantly simplifies the installation and removal process. This is particularly advantageous in applications where accessing the bushing for replacement or maintenance is challenging.
- Self-Aligning Capabilities: The tapered design allows for a degree of self-alignment, accommodating minor misalignments between connected components. This is critical in applications where precise alignment might be difficult to achieve.
- High Load Capacity: When properly installed, split taper bushings can handle significant axial and radial loads. The clamping force created by the tapered design contributes to their high load-bearing capacity.
- Vibration Dampening: The tight fit and clamping action between the bushing halves contribute to improved vibration dampening, reducing noise and wear on the connected components.
- Cost-Effectiveness in Certain Applications: For applications requiring frequent component changes or installations in hard-to-reach areas, the ease of installation can translate to significant cost savings in labor.
Disadvantages of Split Taper Bushings:
- Potential for Loosening: While generally secure, split taper bushings can loosen over time, especially under high vibration or cyclical loading conditions. Regular inspection and tightening might be necessary.
- Limited Precision: Compared to other bushing types, achieving extremely precise alignment can be more challenging with split taper bushings. The self-aligning capability has its limitations.
- Installation Requires Specialized Tools: Depending on the size and design, specialized tools or clamps might be necessary for proper installation to ensure even clamping pressure across the entire length of the bushing.
- Material Limitations: The choice of materials for split taper bushings is limited by the need for sufficient strength and stiffness to withstand clamping forces. This might restrict their application in extreme temperature or corrosive environments.
- Wear and Tear: Over time, the clamping surfaces of the bushing can wear, reducing their clamping force and potentially leading to loosening or component misalignment.
Understanding Quick Disconnect (QD) Bushings
Quick disconnect (QD) bushings, also known as quick-release bushings, are designed for rapid connection and disconnection of components. Unlike split taper bushings, QD bushings typically utilize a locking mechanism, such as a lever, cam, or threaded collar, to secure and release the connection. This mechanism allows for quick assembly and disassembly without the need for extensive tools or adjustments.
Advantages of QD Bushings:
- Rapid Connection and Disconnection: The primary advantage of QD bushings is their speed and ease of connection and disconnection. This is crucial in applications requiring frequent assembly and disassembly, such as in tooling or machinery setups.
- Improved Efficiency: The rapid connection capability enhances workflow efficiency, reducing downtime and improving productivity.
- Simplicity of Design: QD bushings generally feature a simpler design compared to split taper bushings, potentially resulting in lower manufacturing costs.
- Versatility: QD bushings come in various sizes, materials, and configurations to accommodate a wide range of applications and load requirements.
- Suitable for Automated Systems: Their simple mechanism makes them well-suited for integration into automated systems where quick and repeatable connections are essential.
Disadvantages of QD Bushings:
- Lower Load Capacity: Compared to split taper bushings, QD bushings typically have a lower load capacity due to the design of their locking mechanism.
- Potential for Accidental Disconnection: The ease of disconnection can also be a disadvantage, as there's a higher risk of accidental disconnection under certain conditions, especially under vibration or impact loads.
- Higher Cost in Specific Applications: While generally less complex in design, certain advanced QD bushings with specialized locking mechanisms or materials can be more expensive than simpler split taper designs.
- Maintenance: While generally low-maintenance, the locking mechanism might require occasional lubrication or replacement to ensure smooth operation.
- Alignment Limitations: QD bushings might offer less self-aligning capability than split taper bushings, requiring more precise alignment during installation.
Head-to-Head Comparison: Split Taper vs. QD Bushing
Feature | Split Taper Bushing | Quick Disconnect (QD) Bushing |
---|---|---|
Installation | More complex, may require specialized tools | Simple and quick |
Removal | More complex, may require specialized tools | Simple and quick |
Load Capacity | Generally higher | Generally lower |
Alignment | Self-aligning, but with limitations | Less self-aligning, requires precision |
Vibration Dampening | Better | Generally lower |
Cost | Can be cost-effective in certain scenarios | Can be more expensive in certain cases |
Speed | Slower | Much faster |
Maintenance | Potential for loosening, requires inspection | Relatively low maintenance |
Applications | High load applications, fixed connections | Frequent assembly/disassembly, automated systems |
Choosing the Right Bushing: A Decision Matrix
The optimal choice between a split taper and a QD bushing depends heavily on your specific application requirements. Consider the following factors:
- Load Requirements: For applications requiring high load capacities, split taper bushings are generally preferred. For lighter loads, QD bushings are sufficient.
- Frequency of Connection/Disconnection: If frequent connection and disconnection are needed, QD bushings offer significantly improved efficiency. For fixed connections, split taper bushings are suitable.
- Alignment Precision: If precise alignment is crucial, consider the limitations of each bushing type. For applications requiring very high precision, alternative solutions might be necessary.
- Environmental Conditions: Consider the operating environment, particularly temperature and corrosion resistance, when selecting the appropriate bushing material.
- Budget: Evaluate the overall cost, including initial purchase price, installation labor, and potential maintenance costs, for both options.
Case Studies: Illustrating Practical Applications
Case Study 1: Heavy-Duty Machinery: In a heavy-duty industrial press, where components must withstand significant forces and remain securely connected, a split taper bushing might be ideal. Its high load capacity and relative self-aligning capability make it a suitable choice for this demanding environment. The infrequent need for disassembly makes the more complex installation process less of a concern.
Case Study 2: Automated Assembly Line: In an automated assembly line producing small electronic components, QD bushings are perfect. Their rapid connection/disconnection capability is crucial for minimizing downtime and maximizing production throughput. The lighter load requirements of these applications make the lower load capacity of QD bushings acceptable.
Case Study 3: Hydraulic Systems: In hydraulic systems, where leakage is a major concern, the precise fit achievable with a properly installed split taper bushing may be preferred over a QD bushing. The potential for slight misalignment or leakage is minimized with the robust clamping action of a split taper bushing, making it a more suitable choice in such applications.
Conclusion: Informed Selection for Optimal Performance
Selecting between split taper and QD bushings requires a thorough understanding of the application's specific needs and limitations. This detailed comparison highlights the strengths and weaknesses of each bushing type, enabling engineers and designers to make informed decisions that optimize performance, efficiency, and cost-effectiveness. Careful consideration of load requirements, connection frequency, alignment precision, environmental factors, and budget will ultimately lead to the optimal choice for your mechanical design. Remember to consult with engineering specialists for complex or critical applications to ensure the selection of the most appropriate bushing type for reliable and durable performance.
Latest Posts
Latest Posts
-
Soy Empleado De Una Compania Employer Employee Boss Manager
May 08, 2025
-
Which Factor Would The Nurse Consider When Communicating With Adolescents
May 08, 2025
-
Parallel Lines Investigation A 4 2 Answers
May 08, 2025
-
The Graph Below Represents The Solution Set Of Which Inequality
May 08, 2025
-
Which Of The Following Is An Example Of Tax Shifting
May 08, 2025
Related Post
Thank you for visiting our website which covers about Compared To The Qd Bushing The Split Taper . We hope the information provided has been useful to you. Feel free to contact us if you have any questions or need further assistance. See you next time and don't miss to bookmark.