Compute The Elastic Moduli For The Following Polymers
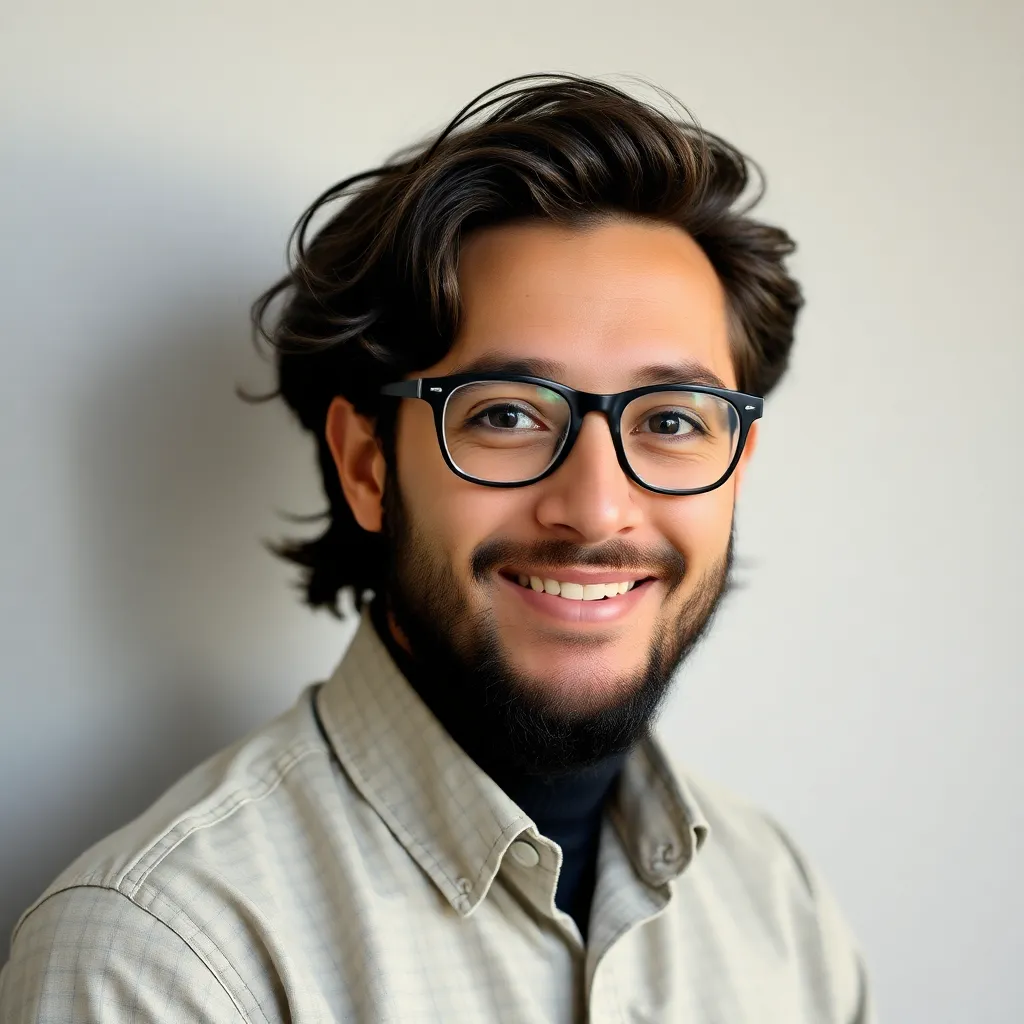
Onlines
May 12, 2025 · 6 min read
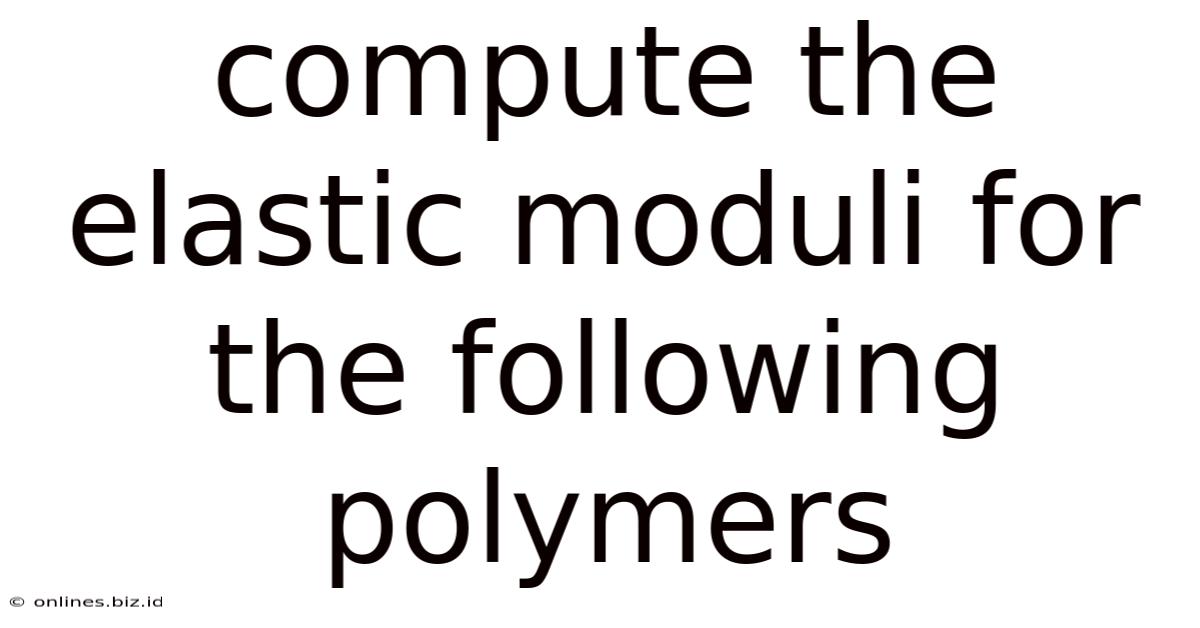
Table of Contents
Computing Elastic Moduli for Polymers: A Comprehensive Guide
Determining the elastic moduli of polymers is crucial for material selection and design in various engineering applications. Unlike crystalline materials with well-defined structures, polymers exhibit complex viscoelastic behavior, making the computation of their elastic moduli a multifaceted challenge. This article delves into the methods and considerations involved in computing the elastic moduli for various polymers, exploring both theoretical approaches and experimental techniques.
Understanding Elastic Moduli
Before diving into computational methods, it's vital to understand what elastic moduli represent. Elastic moduli quantify a material's stiffness or resistance to deformation under an applied stress. The most common elastic moduli are:
- Young's Modulus (E): Measures the tensile stiffness – the resistance to stretching or elongation. A higher Young's modulus indicates a stiffer material.
- Shear Modulus (G): Represents the resistance to shear deformation – the tendency to deform when subjected to parallel forces in opposite directions.
- Bulk Modulus (K): Indicates the resistance to compression – the ability to withstand changes in volume under pressure.
These moduli are interconnected through Poisson's ratio (ν), which describes the ratio of lateral strain to axial strain under uniaxial stress:
E = 2G(1 + ν) = 3K(1 - 2ν)
Factors Affecting Polymer Elastic Moduli
The elastic moduli of polymers are significantly influenced by various factors, including:
- Polymer Chain Structure: The molecular weight, chain conformation (linear, branched, cross-linked), and degree of crystallinity drastically affect stiffness. Higher molecular weight and crystallinity generally lead to higher moduli. Branching reduces stiffness. Crosslinking significantly increases stiffness.
- Temperature: Polymers exhibit a strong temperature dependence. Below the glass transition temperature (Tg), they behave as glassy solids with higher moduli. Above Tg, they transition to a rubbery state with significantly lower moduli.
- Pressure: Increased pressure generally leads to higher elastic moduli due to closer packing of polymer chains.
- Additives and Fillers: The incorporation of fillers (e.g., carbon nanotubes, silica) or plasticizers can significantly alter the elastic moduli. Fillers often increase stiffness, while plasticizers reduce it.
- Processing Conditions: Manufacturing processes such as extrusion, molding, and drawing can affect the final structure and hence the elastic moduli. Orientation of polymer chains during processing can lead to anisotropy in the moduli.
Computational Methods for Determining Elastic Moduli
Several computational methods can estimate the elastic moduli of polymers, each with its strengths and limitations:
1. Molecular Dynamics (MD) Simulations:
MD simulations model the motion of individual atoms and molecules in a polymer system. By applying virtual forces and observing the resulting deformations, one can compute the elastic moduli. This method is particularly useful for understanding the relationship between molecular structure and macroscopic properties. However, MD simulations can be computationally expensive, especially for large systems.
Strengths:
- Provides detailed insights into molecular-level mechanisms influencing elasticity.
- Can handle complex polymer architectures and interactions.
Limitations:
- Computationally expensive, limiting the system size and simulation time.
- Accuracy depends on the force field used to describe interatomic interactions.
2. Finite Element Analysis (FEA):
FEA is a powerful technique for modeling the mechanical behavior of materials under various loading conditions. By discretizing the polymer into a mesh of finite elements, FEA can predict the stress-strain relationship and subsequently compute the elastic moduli. This method is particularly useful for analyzing complex geometries and boundary conditions.
Strengths:
- Can handle complex geometries and boundary conditions.
- Relatively efficient for large-scale simulations compared to MD.
Limitations:
- Requires accurate material models and input parameters.
- Accuracy depends on the mesh quality and element type.
3. Continuum Mechanics Models:
Continuum mechanics approaches treat the polymer as a continuous medium, ignoring the individual molecular details. Various constitutive models, such as neo-Hookean, Mooney-Rivlin, and Ogden models, can be employed to describe the stress-strain relationship. These models often incorporate parameters fitted to experimental data.
Strengths:
- Computationally efficient.
- Can be used for a wide range of polymers and loading conditions.
Limitations:
- Less insightful into the molecular origins of elasticity.
- Accuracy depends on the choice of constitutive model and the fitting parameters.
Experimental Techniques for Determining Elastic Moduli
Experimental methods provide crucial validation data for computational models and offer direct measurements of elastic moduli. Common experimental techniques include:
1. Tensile Testing:
This classic technique involves stretching a polymer specimen and measuring the force and elongation. Young's modulus can be calculated from the slope of the stress-strain curve in the linear elastic region.
2. Shear Testing:
Shear testing involves applying shear forces to a polymer sample and measuring the resulting deformation. The shear modulus is determined from the slope of the shear stress-shear strain curve.
3. Compression Testing:
Compression testing measures the resistance to compressive forces. The bulk modulus can be estimated from the slope of the stress-strain curve in the linear elastic region.
4. Dynamic Mechanical Analysis (DMA):
DMA measures the viscoelastic properties of polymers over a range of frequencies and temperatures. This provides information on both elastic and viscous components of the material response and can be used to determine the storage modulus (elastic component) and loss modulus (viscous component).
Case Studies: Computing Elastic Moduli for Specific Polymers
Let's consider a few examples of common polymers and the challenges associated with computing their elastic moduli:
1. Polyethylene (PE): PE exists in various forms (high-density PE, low-density PE, etc.), each exhibiting different degrees of crystallinity and branching. Computing its elastic moduli requires considering the specific type of PE and its processing conditions. MD simulations can provide insights into the influence of crystallinity and chain conformation on stiffness.
2. Polypropylene (PP): Similar to PE, PP's properties vary with its tacticity (isotactic, atactic, syndiotactic), influencing its crystallinity and hence its elastic moduli. FEA could be useful in predicting the moduli of PP components with complex shapes.
3. Polystyrene (PS): PS is a relatively brittle polymer. Computing its elastic moduli requires accurate modeling of its glass transition behavior and its susceptibility to crazing under stress. Continuum mechanics models, coupled with experimental data, might be suitable for this purpose.
4. Polyvinyl Chloride (PVC): PVC is often plasticized to improve flexibility. Computing its elastic moduli requires considering the effects of the plasticizer on the polymer chain interactions and mobility. MD simulations could be used to understand these effects at the molecular level.
Conclusion
Computing the elastic moduli of polymers is a complex task requiring a combination of theoretical and experimental approaches. The choice of computational method depends on the specific polymer, the level of detail required, and the available computational resources. Accurate determination of elastic moduli is crucial for the rational design of polymer-based materials and components in a wide variety of applications. By carefully considering the factors influencing polymer elasticity and employing appropriate computational and experimental techniques, engineers and materials scientists can obtain reliable predictions of material behavior and optimize material selection for diverse engineering needs. This understanding is crucial for developing advanced polymeric materials with tailored properties for specific applications, contributing to advancements across various industries.
Latest Posts
Latest Posts
-
What European Industries Benefited From African Resources
May 12, 2025
-
What Is The Relationship Between Co2 And O2 For Kelp
May 12, 2025
-
What Is Revealed About Jay Gatsby Aka James Gatz
May 12, 2025
-
Establishing A Team Identity Is Facilitated By
May 12, 2025
-
Quincia Is Studying How The Lack Of
May 12, 2025
Related Post
Thank you for visiting our website which covers about Compute The Elastic Moduli For The Following Polymers . We hope the information provided has been useful to you. Feel free to contact us if you have any questions or need further assistance. See you next time and don't miss to bookmark.