Considerations For Choosing An Appropriate Quality Assurance Surveillance Method
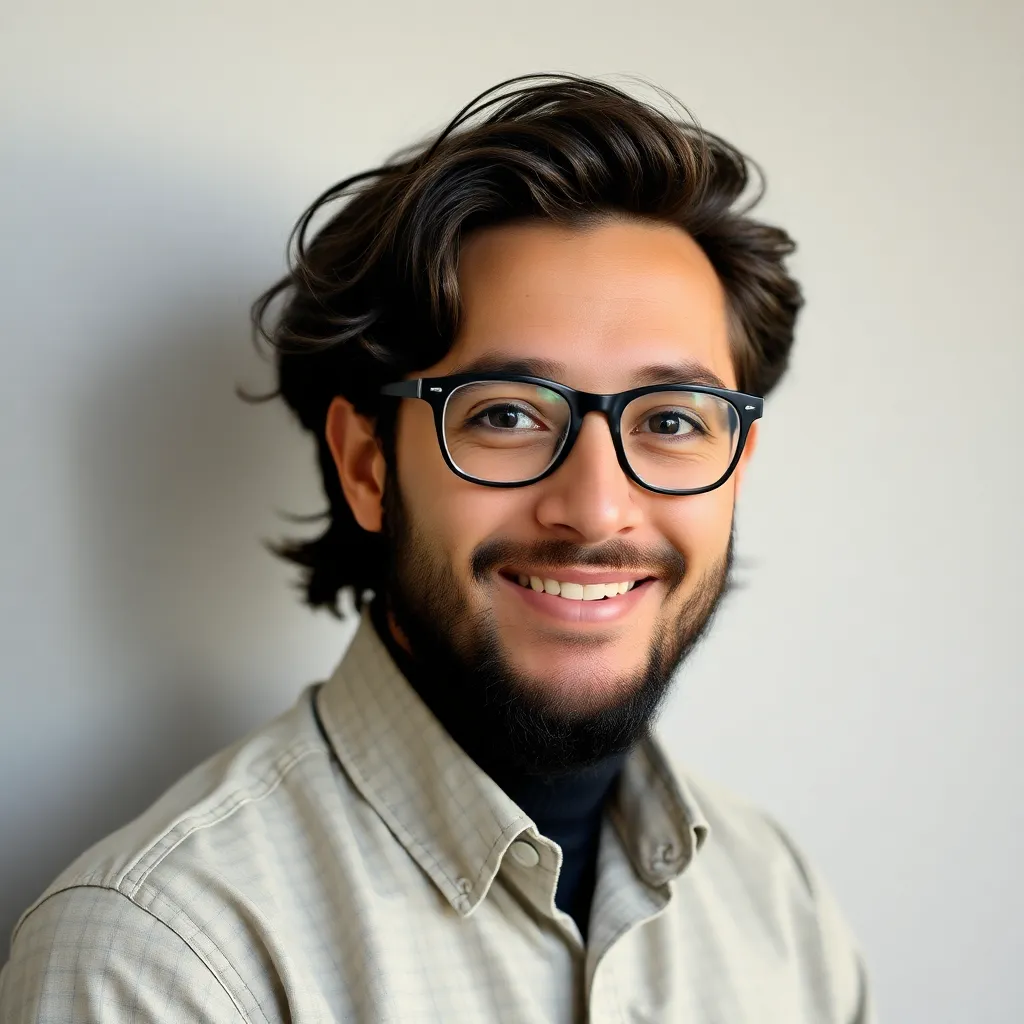
Onlines
May 08, 2025 · 6 min read
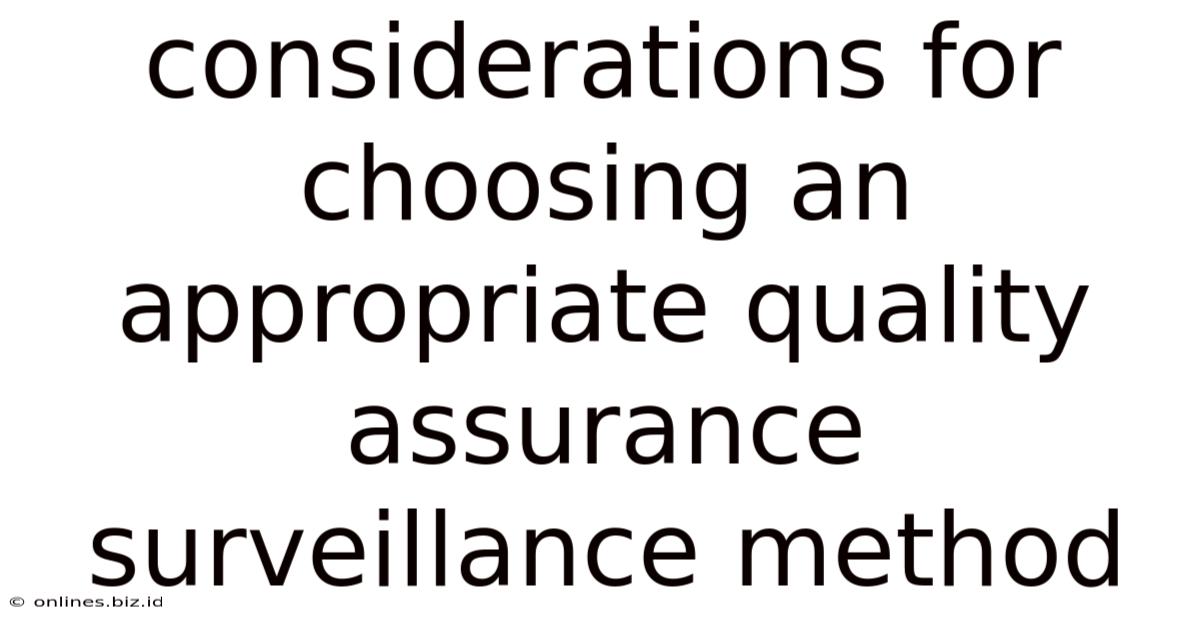
Table of Contents
Considerations for Choosing an Appropriate Quality Assurance Surveillance Method
Selecting the right quality assurance (QA) surveillance method is crucial for maintaining product quality, ensuring regulatory compliance, and protecting consumer safety. The optimal approach isn't one-size-fits-all; it depends heavily on various factors specific to the product, industry, and organization. This comprehensive guide explores key considerations in choosing an appropriate QA surveillance method, enabling you to make informed decisions that bolster your organization's quality management system.
Understanding Quality Assurance and Surveillance
Before diving into specific methods, let's establish a firm understanding of the core concepts. Quality assurance (QA) is a systematic process designed to prevent defects and ensure that products or services consistently meet predefined quality standards. Surveillance, within the context of QA, refers to the ongoing monitoring and evaluation activities that verify the effectiveness of the QA system and identify any deviations from established norms. Effective surveillance is proactive, preventing problems before they escalate into major issues.
Key Factors Influencing Surveillance Method Selection
The selection of a suitable QA surveillance method is not arbitrary. Several critical factors must be carefully considered:
1. Product Characteristics:
- Complexity: A complex product with numerous components and intricate manufacturing processes demands a more rigorous surveillance approach than a simpler product. This may involve a combination of methods.
- Criticality: Products with critical safety implications (e.g., medical devices, pharmaceuticals) require stringent surveillance, often involving multiple layers of checks and independent audits.
- Perishability: Perishable goods necessitate frequent and rapid surveillance to prevent spoilage and waste. Real-time monitoring and quick response mechanisms are vital.
- Shelf life: Products with extended shelf lives may require periodic surveillance focusing on long-term stability and degradation.
2. Manufacturing Process:
- Automation level: Highly automated processes may rely on automated data collection and analysis for surveillance, while manual processes might necessitate more direct observation and inspection.
- Batch size: Batch manufacturing requires distinct surveillance strategies compared to continuous manufacturing. Sampling techniques and statistical process control (SPC) are often employed.
- Supplier involvement: The involvement of external suppliers requires careful surveillance of their processes and products to ensure consistent quality.
3. Regulatory Requirements:
- Industry standards: Compliance with industry-specific standards and regulations (e.g., ISO 9001, GMP, FDA regulations) dictates the necessary surveillance procedures. These regulations often specify mandatory inspections, testing, and documentation.
- Legal liabilities: Products with significant legal liabilities require meticulous surveillance to minimize risks and demonstrate compliance. Thorough documentation is paramount.
4. Organizational Capabilities:
- Resources: The availability of personnel, equipment, and budget directly impacts the feasibility of different surveillance methods.
- Expertise: The technical expertise of personnel is essential for selecting and implementing appropriate surveillance techniques. Specialized training may be necessary.
- Technology infrastructure: The availability of data management systems, software, and analytical tools influences the type of surveillance that can be effectively implemented.
5. Risk Assessment:
- Potential hazards: Identifying potential hazards and risks associated with the product or process is fundamental to choosing appropriate surveillance methods. This involves a thorough hazard analysis and risk assessment (HARA).
- Risk mitigation strategies: Surveillance methods should be selected to effectively mitigate identified risks. This may include preventative measures, corrective actions, and contingency plans.
Available Quality Assurance Surveillance Methods
A range of surveillance methods exists, each with strengths and limitations. The choice often involves a combination of methods tailored to the specific needs.
1. Inspection and Testing:
This fundamental method involves physically examining products or components to identify defects or non-conformances. It can be performed at various stages:
- Incoming inspection: Verifying the quality of raw materials and components from suppliers.
- In-process inspection: Monitoring the quality of materials and products during manufacturing.
- Final inspection: Checking the final product before release to the market.
- Destructive testing: Testing that involves destroying the product to assess its properties (e.g., tensile strength, impact resistance).
- Non-destructive testing: Testing that doesn't damage the product (e.g., ultrasonic testing, X-ray inspection).
Advantages: Direct assessment of product quality, simple to implement for some products.
Disadvantages: Can be time-consuming and costly, especially for complex products, may not detect all defects, potentially destructive.
2. Statistical Process Control (SPC):
SPC employs statistical methods to monitor and control the manufacturing process. Control charts are used to track key process parameters and identify trends indicating potential problems.
Advantages: Proactive identification of process variations, efficient monitoring of continuous processes, data-driven decision-making.
Disadvantages: Requires statistical expertise, not suitable for all processes, requires careful selection of key parameters.
3. Audits:
Audits involve systematic and independent examinations of various aspects of the QA system. They can be internal, conducted by the organization itself, or external, performed by independent auditors.
- Internal audits: Assess the effectiveness of the QA system within the organization.
- External audits: Verify compliance with external standards and regulations.
Advantages: Comprehensive evaluation of the QA system, identification of systemic weaknesses, ensures compliance.
Disadvantages: Can be time-consuming and expensive, may disrupt operations.
4. Data Analysis and Reporting:
Analyzing data collected from various sources (production records, inspection reports, customer feedback) provides valuable insights into product quality and process performance. This can involve:
- Trend analysis: Identifying patterns and trends in product defects or process variations.
- Root cause analysis: Investigating the root causes of quality problems.
- Process capability analysis: Assessing the ability of the process to meet specified quality requirements.
Advantages: Data-driven decision-making, identification of trends and patterns, proactive problem-solving.
Disadvantages: Requires sophisticated data management systems and analytical skills, can be complex to interpret.
5. Customer Feedback:
Collecting and analyzing customer feedback is crucial for understanding customer satisfaction and identifying areas for improvement. Methods include:
- Surveys: Collecting feedback through questionnaires.
- Customer complaints: Tracking and analyzing customer complaints.
- Focus groups: Gathering feedback from selected customers.
Advantages: Direct assessment of customer satisfaction, identification of product defects or usability issues, continuous improvement.
Disadvantages: Can be subjective and difficult to quantify, may not represent all customers.
6. Supplier Surveillance:
For products involving external suppliers, monitoring supplier performance is essential. Methods include:
- Supplier audits: Evaluating the supplier's quality management system.
- Product inspections: Inspecting incoming materials and components.
- Performance monitoring: Tracking key performance indicators (KPIs) of the supplier.
Advantages: Ensures consistent quality of materials and components, strengthens supplier relationships.
Disadvantages: Requires resources to monitor multiple suppliers, can be complex to manage.
Integrating Surveillance Methods: A Holistic Approach
Effective QA often involves integrating multiple surveillance methods. A layered approach, incorporating various techniques, offers a robust and comprehensive system. For instance, SPC could monitor the production process, while periodic audits evaluate the overall QA system, and customer feedback identifies areas needing improvement.
Documentation and Record Keeping: The Cornerstone of Effective Surveillance
Meticulous record-keeping is essential for successful QA surveillance. All surveillance activities must be documented thoroughly, including:
- Inspection and testing results: Detailed records of all inspections and tests performed, including the date, time, inspector, and results.
- SPC data: Control charts and other statistical data used to monitor process performance.
- Audit reports: Comprehensive reports detailing the findings and recommendations of audits.
- Customer feedback: Documentation of customer complaints, surveys, and focus group results.
- Corrective and preventative actions (CAPA): Detailed records of all CAPA implemented to address quality issues.
Conclusion: Choosing the Right Path to Quality
The selection of an appropriate QA surveillance method is a strategic decision with significant implications for product quality, regulatory compliance, and business success. By carefully considering the factors discussed above—product characteristics, manufacturing processes, regulatory requirements, organizational capabilities, and risk assessment—you can create a tailored surveillance program that safeguards your organization's reputation and ensures the delivery of consistently high-quality products and services. Remember that the most effective approach frequently involves a synergistic combination of methods, complemented by rigorous documentation and continuous improvement. This holistic approach is the key to building a sustainable and reliable quality management system.
Latest Posts
Latest Posts
-
When Brainstorming You Should Go For Quantity Over Quality
May 08, 2025
-
Employee Assistance Programs Address Which Of The Following
May 08, 2025
-
Match The Clinical Reasoning Process With Its Descriptor
May 08, 2025
-
Could Dabc Be Congruent To Dadc By Sss Explain
May 08, 2025
-
Chapter 17 Summary Their Eyes Were Watching God
May 08, 2025
Related Post
Thank you for visiting our website which covers about Considerations For Choosing An Appropriate Quality Assurance Surveillance Method . We hope the information provided has been useful to you. Feel free to contact us if you have any questions or need further assistance. See you next time and don't miss to bookmark.