Consist Of Hollow Tubes Which Provide Support
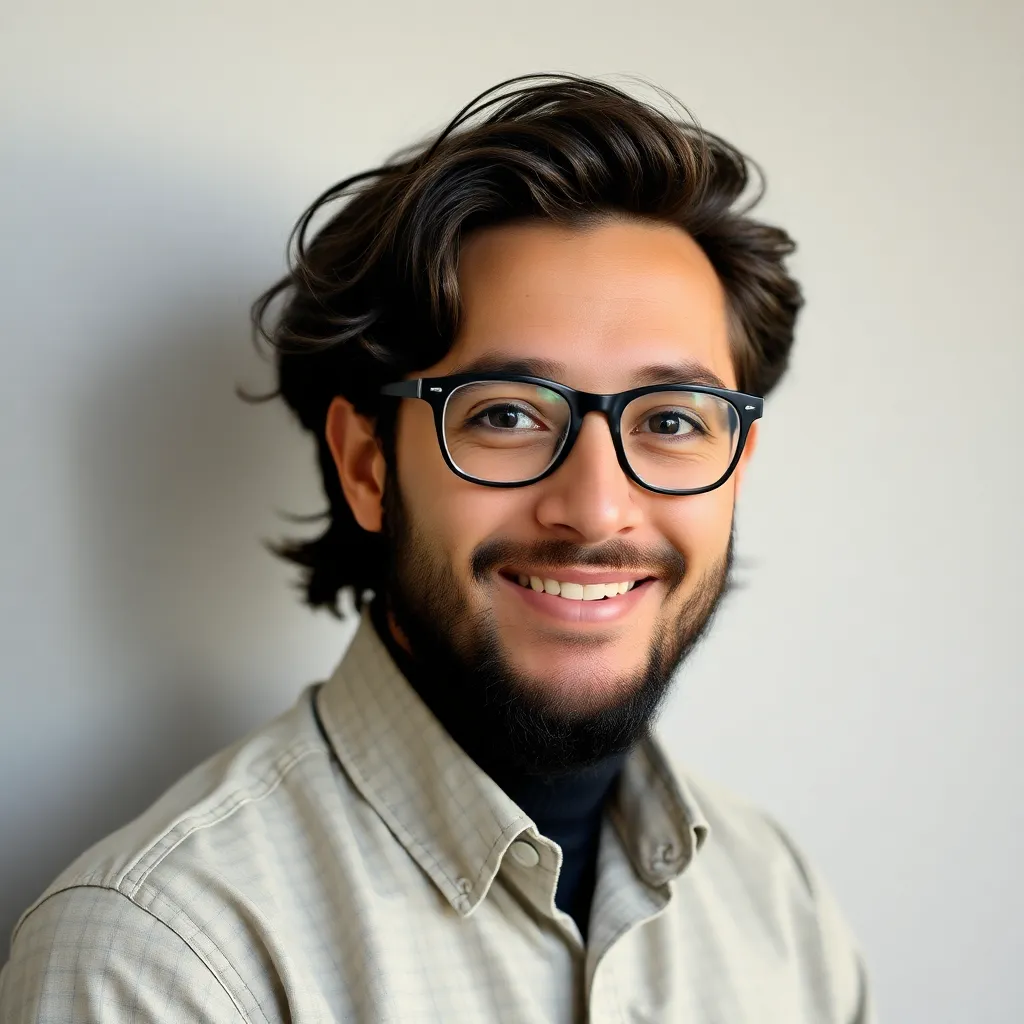
Onlines
May 10, 2025 · 7 min read
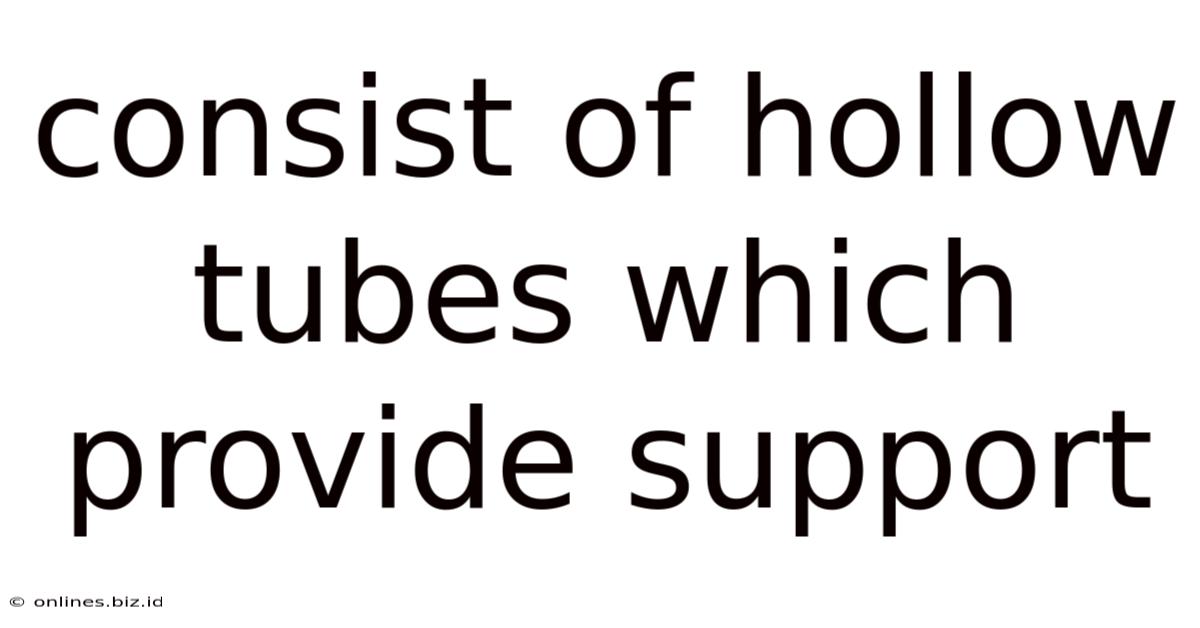
Table of Contents
Structures Composed of Hollow Tubes: A Deep Dive into Efficiency and Design
Hollow tubes are ubiquitous in nature and engineering, forming the foundational elements of incredibly strong and lightweight structures. From the bones in our bodies to the skyscrapers piercing the skyline, the consistent use of hollow tubes highlights their exceptional ability to provide support while minimizing material usage. This article will delve into the reasons behind this efficiency, exploring the diverse applications and design considerations associated with structures built from these remarkable components.
The Strength of Hollow Tubes: A Physics Perspective
The superior strength-to-weight ratio of hollow tubes compared to solid rods of the same material is a fundamental principle in structural mechanics. This advantage stems from the efficient distribution of material away from the center, maximizing the distance of the material from the neutral axis.
Understanding the Neutral Axis
The neutral axis is the imaginary line within a structural member that experiences neither tension nor compression during bending. When a hollow tube is subjected to bending stress, the material furthest from the neutral axis experiences the greatest stress. Because a hollow tube concentrates its material further from the neutral axis than a solid rod of equivalent weight, it can withstand significantly higher bending loads before failure.
Moment of Inertia and Bending Resistance
The moment of inertia (I) is a crucial geometrical property that quantifies a structure's resistance to bending. A higher moment of inertia indicates greater resistance to bending. Hollow tubes possess a significantly higher moment of inertia compared to solid rods of the same mass, contributing directly to their enhanced strength and stiffness. This is because the material is distributed further from the center, effectively increasing its lever arm and resistance to bending.
Torsional Stiffness
Hollow tubes also exhibit superior torsional stiffness, meaning they resist twisting more effectively than solid rods. This is particularly crucial in applications where rotational forces are involved, such as transmission shafts in machinery or structural members subjected to wind loads. The hollow design allows for a more even distribution of shear stress, enhancing the overall torsional resistance.
Buckling Resistance
Buckling, the sudden and catastrophic failure of a structural member under compressive loads, is a significant concern in many engineering applications. Hollow tubes, due to their higher moment of inertia and optimized material distribution, are inherently more resistant to buckling than solid rods of the same material and mass.
Applications of Hollow Tube Structures Across Industries
The exceptional properties of hollow tubes have led to their widespread adoption across numerous industries. Their versatility and efficiency make them ideal for a vast array of applications, some of which are discussed below:
Civil Engineering: Skyscrapers and Bridges
In civil engineering, hollow tubes form the backbone of many large-scale structures. Steel tubular structures are prevalent in skyscrapers, providing exceptional strength and stiffness while minimizing the overall weight of the building. The use of hollow steel tubes allows for taller, more slender designs, pushing the boundaries of architectural possibilities. Similarly, bridges, particularly those with long spans, often incorporate hollow tube elements in their design to maximize load-bearing capacity and minimize material usage.
Aerospace Engineering: Aircraft and Spacecraft
The aerospace industry relies heavily on hollow tube structures due to their remarkable strength-to-weight ratio. Aircraft fuselages and wings frequently utilize hollow tubes made from lightweight yet strong materials like aluminum alloys or composites. These materials provide the necessary strength to withstand the immense stresses experienced during flight, while minimizing the overall weight of the aircraft, thus enhancing fuel efficiency. Similarly, spacecraft structures frequently incorporate hollow tubes to provide support while minimizing mass, critical for launching and maneuvering in space.
Mechanical Engineering: Machinery and Automotive
In mechanical engineering, hollow tubes are commonly used in applications requiring both strength and flexibility. Transmission shafts, for example, often employ hollow tubes to transmit power efficiently while minimizing weight and rotational inertia. In the automotive industry, tubular chassis frames have gained popularity due to their superior strength-to-weight ratio, enabling the creation of lighter, more fuel-efficient vehicles while maintaining safety standards.
Biomedical Engineering: Implants and Prosthetics
The design principles of hollow tubes extend to biomedical engineering, where hollow tubes are utilized in the creation of various implants and prosthetics. Bone replacements, for instance, often incorporate hollow tube structures designed to mimic the natural architecture of bones. This design enhances biocompatibility and helps to integrate seamlessly with the surrounding tissue. Similar principles are employed in the design of artificial limbs and other medical implants.
Furniture and Sporting Goods
The efficiency and aesthetic appeal of hollow tubes have also found application in the furniture and sporting goods industries. Lightweight yet strong furniture often incorporates hollow metal or composite tubes for its frame. Similarly, sporting goods, such as bicycle frames and hockey sticks, often utilize hollow tubes to provide stiffness and impact resistance while minimizing weight.
Design Considerations for Hollow Tube Structures
The design of structures incorporating hollow tubes requires careful consideration of several factors to ensure safety, efficiency, and longevity.
Material Selection
The choice of material is critical, depending on the specific application and environmental conditions. Steel, aluminum alloys, and composites are commonly used, each offering a unique combination of strength, weight, cost, and corrosion resistance. The selection process considers factors like the required strength, stiffness, weight limitations, cost, and the operating environment.
Tube Diameter and Wall Thickness
Optimizing the tube diameter and wall thickness is essential for achieving the desired strength-to-weight ratio. Finite element analysis (FEA) and other advanced computational techniques are often used to determine the optimal dimensions for a given load scenario. A proper balance must be achieved, avoiding excessive material usage while ensuring sufficient strength and stability.
Connections and Joints
The method of connecting hollow tubes is crucial to the structural integrity of the overall system. Welded joints, bolted connections, and adhesive bonding are some common techniques. The choice of connection method depends on the application, the materials used, and the desired strength and stiffness of the joint. Proper design of the joints is essential to avoid stress concentrations and ensure the overall structural integrity.
Fatigue and Corrosion
Hollow tube structures, like any other structural element, are susceptible to fatigue and corrosion. Fatigue failure occurs when a structure is subjected to repeated cyclic loading, eventually leading to crack initiation and propagation. Corrosion can degrade the material properties and compromise the structural integrity. Proper design considerations, including material selection, surface treatments, and protective coatings, are essential to mitigate these risks.
Future Trends in Hollow Tube Structures
Research and development continue to push the boundaries of hollow tube structures, exploring new materials, advanced design techniques, and innovative applications.
Advanced Materials
The use of advanced materials such as carbon fiber reinforced polymers (CFRP) and other composites is gaining traction. These materials offer exceptional strength-to-weight ratios, allowing for the creation of even lighter and stronger structures. Research is underway to develop new composite materials with enhanced properties to further improve the performance of hollow tube structures.
Additive Manufacturing
Additive manufacturing, also known as 3D printing, offers the potential to create complex hollow tube structures with intricate geometries that would be difficult or impossible to manufacture using traditional methods. This opens up new design possibilities and enables the creation of customized structures tailored to specific applications.
Smart Structures
The integration of sensors and actuators into hollow tube structures is leading to the development of "smart structures" capable of self-monitoring and self-repairing. These advancements enable improved safety, reduced maintenance costs, and enhanced structural performance.
Conclusion
Hollow tubes represent a remarkably efficient and versatile structural element used across a wide array of industries. Their superior strength-to-weight ratio, coupled with their adaptability to diverse design requirements, makes them indispensable components in countless applications. From the intricate framework of aircraft to the towering heights of skyscrapers, the use of hollow tubes demonstrates the power of understanding fundamental engineering principles to create efficient and robust structures capable of withstanding even the most demanding conditions. Ongoing advancements in materials science and manufacturing techniques promise even more innovative applications of hollow tube structures in the future, continuing their reign as a cornerstone of structural engineering.
Latest Posts
Latest Posts
-
Model 2 Illustrates How Nature Recycles What Natural Resource
May 11, 2025
-
In The Following Figure Which Area Represents Producer Surplus
May 11, 2025
-
Which Of The Following Is True About Nail Extension Undersides
May 11, 2025
-
The Highlighted Structure Articulates With Which Bone
May 11, 2025
-
A Nurse Is Preparing A Presentation About Muscle Function
May 11, 2025
Related Post
Thank you for visiting our website which covers about Consist Of Hollow Tubes Which Provide Support . We hope the information provided has been useful to you. Feel free to contact us if you have any questions or need further assistance. See you next time and don't miss to bookmark.