Control Valve Should Always Be In What Position
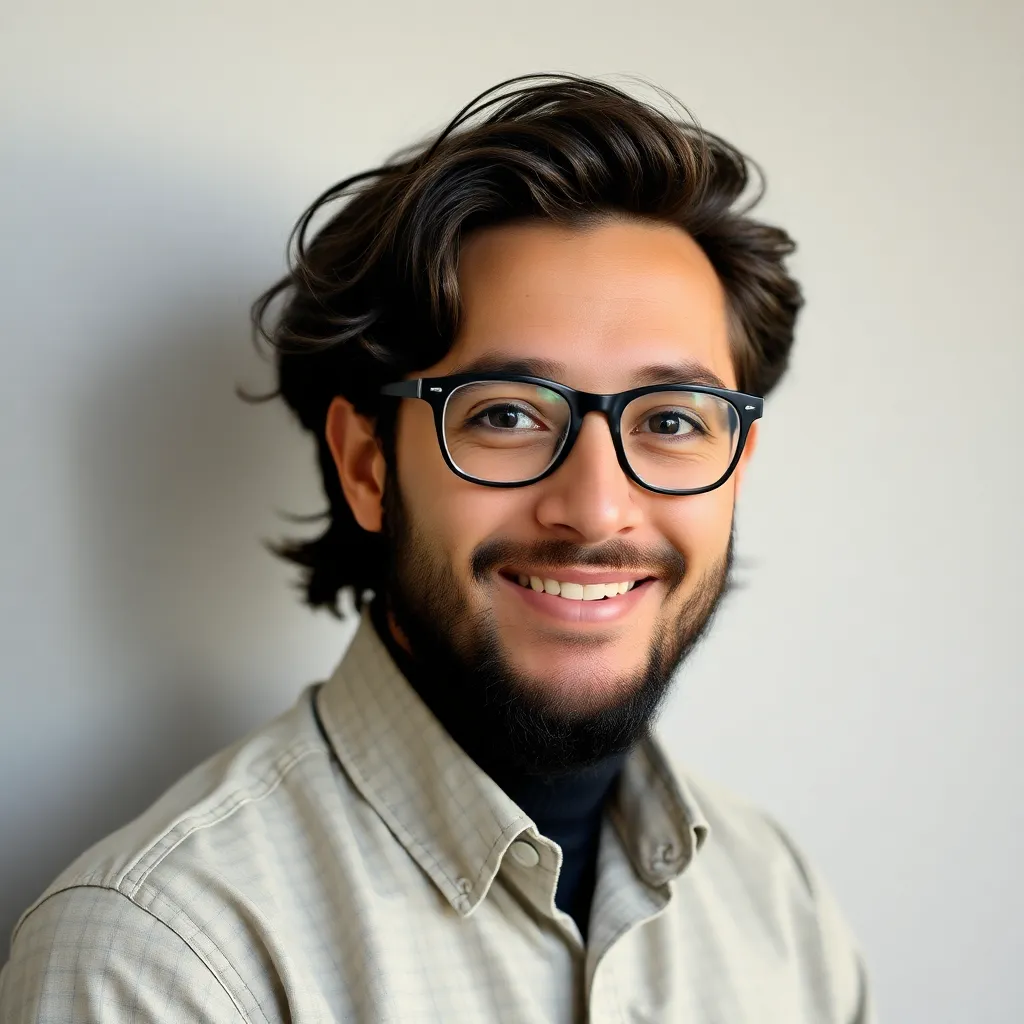
Onlines
Mar 06, 2025 · 5 min read
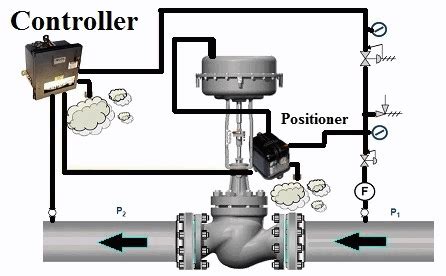
Table of Contents
Control Valve Positioning: A Comprehensive Guide to Optimal Performance and Safety
Control valves are ubiquitous in industrial processes, regulating the flow of liquids, gases, and slurries. Their proper positioning is paramount not only for efficient process control but also for safety and the longevity of the valve itself. There's no single "always" position, but rather, optimal positioning depends on several crucial factors. This comprehensive guide explores these factors, offering insights into best practices and troubleshooting common issues related to control valve positioning.
Understanding Control Valve Functionality
Before diving into ideal positions, it's crucial to understand how control valves operate. These valves are actuators that precisely adjust the flow rate of a process stream based on a controller signal. This signal, often from a process sensor (e.g., temperature, pressure, level), dictates the valve's opening or closing, thereby influencing the process variable. Different valve types exist, including globe valves, ball valves, butterfly valves, and diaphragm valves, each with unique characteristics impacting their suitability and optimal position.
Key Components and Mechanisms
Control valves comprise several key components working in concert:
- Actuator: The "muscle" of the valve, converting the controller signal into mechanical movement (e.g., pneumatic, electric, hydraulic).
- Valve Body: Houses the internal components and provides structural integrity.
- Valve Stem: Connects the actuator to the valve plug or disc.
- Valve Plug/Disc: The element that restricts or allows flow.
- Positioner: A feedback mechanism ensuring the valve reaches and maintains the desired position accurately.
Determining the Optimal Control Valve Position: It's Not One-Size-Fits-All
The "ideal" position for a control valve is not static; it's dynamic and context-dependent. It hinges on several interconnected factors:
-
Process Requirements: The nature of the process dictates the operational parameters and therefore the valve's position. A process requiring precise temperature control will need more frequent adjustments and a different "setpoint" than a process with less stringent requirements.
-
Valve Type: Different valve types have inherent characteristics affecting their optimal operating range. For instance, a ball valve might perform best at fully open or fully closed positions, while a globe valve offers better control at intermediate positions.
-
Flow Characteristics: The relationship between the valve's position and flow rate is nonlinear. Understanding this characteristic curve (Cv) is vital for efficient control. Properly sizing the valve for the application ensures it operates within its effective range.
-
Maintenance and Wear: Prolonged operation at extreme positions (fully open or fully closed) can lead to accelerated wear and tear. Frequent cycling between extremes can also contribute to component fatigue. Maintaining a valve in a more moderate position, even if it means slightly less precise control in certain situations, can extend its lifespan.
Common Control Valve Positions and Their Implications
Let's examine typical valve positions and their associated implications:
1. Fully Open Position:
- Advantages: Maximum flow rate, minimal pressure drop.
- Disadvantages: Increased wear and tear on the valve components if maintained for prolonged periods. May be less responsive to quick adjustments required during process upsets. Potentially higher energy consumption due to less restrictive flow.
2. Fully Closed Position:
- Advantages: Complete flow shut-off, essential for safety and maintenance.
- Disadvantages: Can lead to stagnation and potential build-up of deposits or crystallization, especially for viscous fluids. May experience leakage if the valve seal is not properly maintained. Similar wear and tear issues as the fully open position if held for prolonged periods.
3. Intermediate Positions:
- Advantages: Optimizes the balance between flow control and valve life. Allows for fine-tuning of the process variable. Minimizes wear and tear compared to the extremes.
- Disadvantages: May require more precise and frequent adjustments, especially for processes with fluctuating demands. Requires careful selection of valve type and sizing to ensure effective control at these positions.
Factors Influencing Optimal Positioning: A Deeper Dive
Several interconnected factors further refine our understanding of optimal valve positioning:
-
Process Dynamics: Fast-acting processes require valves with swift response times and may operate more frequently near their extremes. Slow-moving processes allow for more gradual adjustments and may benefit from operation in intermediate positions.
-
Control Strategy: The control algorithm employed (e.g., PID control) plays a crucial role. A well-tuned controller minimizes unnecessary valve movements, reducing wear and promoting energy efficiency.
-
Material Compatibility: The valve's materials must be compatible with the process fluid to prevent corrosion, degradation, and potential leaks. This choice also impacts how the valve ages and its optimal operating parameters.
-
Environmental Conditions: Temperature extremes, vibration, and other environmental factors can influence the valve's performance and dictate its maintenance schedule and optimal operational range.
-
Safety Considerations: In safety-critical applications, redundant valves or fail-safe mechanisms may be employed, potentially altering the optimal positioning strategy for individual valves within the system.
Troubleshooting and Maintenance: Keeping Your Valves in Top Shape
Regular maintenance and troubleshooting are critical for ensuring your control valves operate optimally:
-
Regular Inspections: Visual inspections should identify signs of leakage, wear, or damage. Checking for proper seating and lubrication is also crucial.
-
Calibration and Testing: Periodic calibration ensures the valve's position accurately reflects the controller signal. Testing its functionality under various conditions is important for early detection of issues.
-
Valve Positioner Maintenance: The positioner needs regular checks for proper functioning and calibration.
-
Cleaning and Lubrication: Depending on the process fluid and environmental conditions, cleaning and lubrication may be required to minimize friction and ensure smooth operation.
-
Addressing Leakage: Leakage can be a sign of wear or damage and should be addressed promptly.
-
Actuator Diagnostics: Checking the actuator for proper operation and strength is crucial for ensuring accurate valve movement.
Conclusion: A Holistic Approach to Control Valve Positioning
Determining the ideal control valve position isn't a simple task; it's a nuanced process requiring careful consideration of numerous interconnected factors. There's no single "always" position. Rather, a holistic approach, encompassing process requirements, valve characteristics, maintenance considerations, and environmental factors, is essential. Prioritizing regular maintenance, troubleshooting, and operator training will significantly enhance the performance, safety, and longevity of your control valves, contributing to the overall efficiency and reliability of your industrial processes. By understanding these principles and implementing best practices, you can optimize your control valve positioning for peak efficiency, safety, and cost-effectiveness.
Latest Posts
Latest Posts
-
Which Of The Following Is Not Electronic Phi Ephi
Mar 06, 2025
-
6 5 Antiderivatives And Indefinite Integrals Homework
Mar 06, 2025
-
Which Of The Following Is True Of Cui
Mar 06, 2025
-
Student Exploration Coral Reefs 2 Biotic Factors
Mar 06, 2025
-
Which Of The Following Can Be Controlled By Copyright
Mar 06, 2025
Related Post
Thank you for visiting our website which covers about Control Valve Should Always Be In What Position . We hope the information provided has been useful to you. Feel free to contact us if you have any questions or need further assistance. See you next time and don't miss to bookmark.