Effective Capacity Is The Capacity Allowances Such As Maintenance.
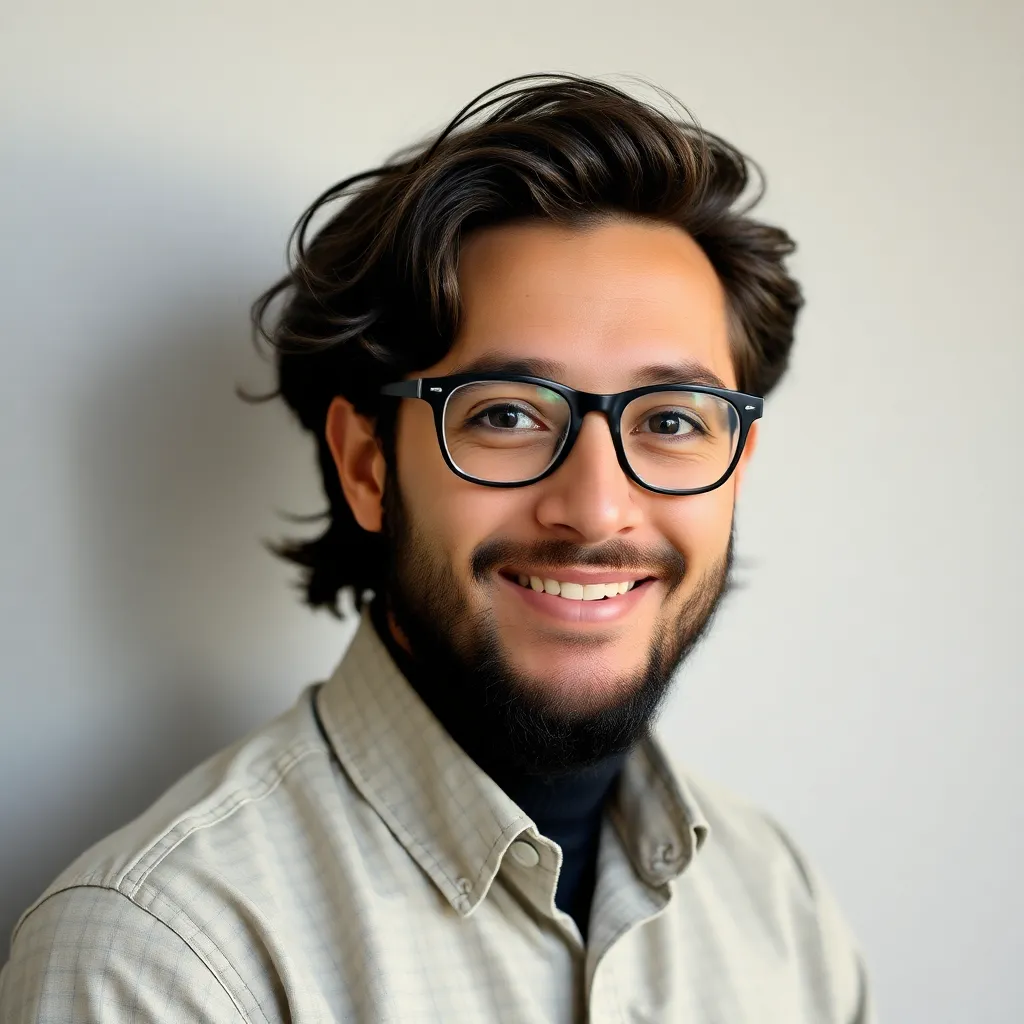
Onlines
Apr 19, 2025 · 6 min read

Table of Contents
Effective Capacity: Understanding Capacity Allowances and Their Impact on Production
Effective capacity, a crucial concept in operations management, represents the actual output a system can achieve, considering various constraints and allowances. Unlike design capacity, which represents the maximum theoretical output, effective capacity accounts for real-world factors that limit production. A key component of effective capacity is the incorporation of capacity allowances, which include time set aside for planned downtime, maintenance, and other non-production activities. Understanding and effectively managing these allowances is critical for optimizing production efficiency and meeting customer demands.
What are Capacity Allowances?
Capacity allowances are the portions of production time deliberately allocated for activities other than direct production. These allowances act as buffers, mitigating the impact of unavoidable delays and ensuring the smooth functioning of the production system. They are essential for preventing bottlenecks and maintaining a consistent output rate. Key types of capacity allowances include:
1. Maintenance Allowances:
Maintenance is a critical aspect of capacity planning. Equipment malfunctions, breakdowns, and scheduled maintenance are inevitable. Allocating sufficient time for preventive and corrective maintenance is crucial to prevent costly production downtime and ensure the longevity of equipment. This allowance encompasses both planned maintenance (e.g., routine inspections, lubrication) and unplanned maintenance (e.g., repairs due to unexpected failures). Ignoring maintenance allowances can lead to significant production losses and increased repair costs in the long run.
2. Quality Control Allowances:
Quality control is integral to any manufacturing process. Time needs to be allocated for inspecting raw materials, monitoring the production process, and conducting quality checks on finished goods. This allowance helps identify and rectify defects early, preventing the production of defective products and minimizing waste. A robust quality control system, incorporating sufficient allowance time, enhances product quality and customer satisfaction.
3. Setup and Changeover Allowances:
Many production systems require setups and changeovers between different products or batches. These involve switching tools, adjusting machinery, and preparing for the next production run. These activities consume valuable time, and failing to account for them in capacity planning can lead to significant production delays. Accurate estimation of setup and changeover times is essential for effective capacity planning. Lean manufacturing principles, such as Single Minute Exchange of Die (SMED), focus on minimizing these changeover times to maximize effective capacity.
4. Scrap and Rework Allowances:
Even with stringent quality control measures, some level of scrap and rework is inevitable. Products may be defective, require modifications, or need to be discarded. Allocating time for handling scrap, reworking defective items, and managing waste is vital. This allowance helps maintain a consistent flow of good quality products and prevents the accumulation of defective items. Analyzing the root causes of scrap and rework can lead to process improvements and a reduction in this allowance over time.
5. Material Handling Allowances:
Moving materials within a production facility consumes time and resources. This includes transporting raw materials to production areas, moving work-in-progress between workstations, and distributing finished goods to storage or shipping. Inefficient material handling can create bottlenecks and disrupt production flow. Optimizing material handling processes, such as implementing efficient storage systems and utilizing automated guided vehicles (AGVs), can reduce the time allocated to this allowance.
6. Employee Absenteeism and Break Allowances:
Employee absenteeism and breaks are inevitable factors affecting effective capacity. Employees require rest breaks, and unforeseen absences due to illness or other reasons will occur. Including allowances for breaks and absenteeism ensures that the production schedule remains realistic and avoids overworking the remaining workforce. Robust HR policies and employee well-being programs can help minimize absenteeism.
7. Downtime Allowances (Unplanned):
Unplanned downtime encompasses unexpected events such as equipment malfunctions, power outages, or supply chain disruptions. While impossible to perfectly predict, allocating a buffer for such events is crucial. This allowance minimizes the impact of unexpected disruptions on production schedules. A robust risk management strategy can help to mitigate the frequency and duration of unplanned downtime.
Calculating Effective Capacity
Calculating effective capacity involves subtracting the total time allocated for capacity allowances from the design capacity. The formula can be expressed as:
Effective Capacity = Design Capacity – Allowances
For instance, if a production line has a design capacity of 1000 units per day, and the total allowances (maintenance, setup, quality control, etc.) amount to 20% of the production time, then the effective capacity would be:
Effective Capacity = 1000 units/day – (0.20 * 1000 units/day) = 800 units/day
The Importance of Accurate Allowance Estimation
Accurate estimation of capacity allowances is paramount for effective capacity planning. Underestimating allowances can lead to unrealistic production schedules, missed deadlines, and increased stress on the workforce. Overestimating allowances, on the other hand, can lead to underutilization of resources and lost potential output.
Several factors influence the accuracy of allowance estimation:
- Historical Data: Analyzing past production data to identify the frequency and duration of downtime, setup times, and other allowances provides a valuable baseline.
- Process Analysis: Carefully examining each step of the production process can reveal potential bottlenecks and areas where allowances might be necessary.
- Industry Benchmarks: Comparing allowance percentages with industry benchmarks can provide insights into typical allowance levels for similar production processes.
- Expert Judgment: The input of experienced personnel can provide valuable insights into the potential duration of various allowances.
- Simulation Modeling: Simulation models can help explore different scenarios and predict the impact of varying allowance levels on production output.
Optimizing Capacity Allowances for Enhanced Efficiency
Optimizing capacity allowances is not about eliminating them entirely, but rather about finding the optimal balance between sufficient allowances to ensure smooth operations and minimizing excessive allowances that reduce overall productivity. Strategies for optimizing capacity allowances include:
- Implementing Preventative Maintenance: Regular preventative maintenance reduces the need for unplanned downtime caused by equipment failures.
- Improving Quality Control Processes: A robust quality control system reduces the number of defective products, minimizing rework and scrap allowances.
- Reducing Setup and Changeover Times: Implementing lean manufacturing principles, such as SMED, can significantly reduce setup times.
- Optimizing Material Handling: Improving material flow and storage can minimize time spent on material handling activities.
- Investing in Advanced Technologies: Automation, robotics, and other advanced technologies can reduce downtime and improve efficiency.
- Employee Training and Development: Well-trained employees are more efficient and less prone to errors, reducing rework and scrap.
- Effective Scheduling and Planning: Proper scheduling and planning can ensure efficient use of resources and minimize idle time.
Effective Capacity and its Impact on Business Decisions
Effective capacity is a critical factor in numerous business decisions:
- Production Planning: Accurate knowledge of effective capacity is essential for creating realistic production schedules and avoiding overcommitment.
- Capacity Expansion: When evaluating the need for capacity expansion, understanding effective capacity is crucial to determine whether existing capacity can be optimized or if additional capacity is truly necessary.
- Inventory Management: Effective capacity influences inventory management decisions, ensuring sufficient inventory to meet demand without excessive storage costs.
- Pricing Strategies: Understanding effective capacity can help determine appropriate pricing strategies to ensure profitability.
- Resource Allocation: Effective capacity guides resource allocation decisions, ensuring that resources are allocated efficiently to meet production targets.
Conclusion: The Cornerstone of Efficient Production
Effective capacity, incorporating comprehensive capacity allowances, is not merely a theoretical concept; it's the cornerstone of efficient and successful production. By carefully considering and optimizing capacity allowances, businesses can ensure a smooth, consistent production process, meet customer demands, minimize waste, and maximize profitability. Ignoring capacity allowances, however, can lead to significant production bottlenecks, missed deadlines, increased costs, and ultimately, business failure. Therefore, a thorough understanding and meticulous management of effective capacity, including its constituent allowances, are crucial for any organization aiming for sustained success in a competitive market. Proactive planning, continuous improvement, and data-driven decision-making are essential components of effective capacity management.
Latest Posts
Latest Posts
-
Getting To Know The Ph Scale Worksheet Answer Key
Apr 19, 2025
-
How To See Pcib Microsoft Project
Apr 19, 2025
-
3 14 Unit Test Entering The Modern Era
Apr 19, 2025
-
Unit 3 Parallel And Perpendicular Lines Homework 6 Answer Key
Apr 19, 2025
-
The Following Excerpt Represents Monophonic Texture
Apr 19, 2025
Related Post
Thank you for visiting our website which covers about Effective Capacity Is The Capacity Allowances Such As Maintenance. . We hope the information provided has been useful to you. Feel free to contact us if you have any questions or need further assistance. See you next time and don't miss to bookmark.