Electrical Bonding Investigation Plan Quick Check
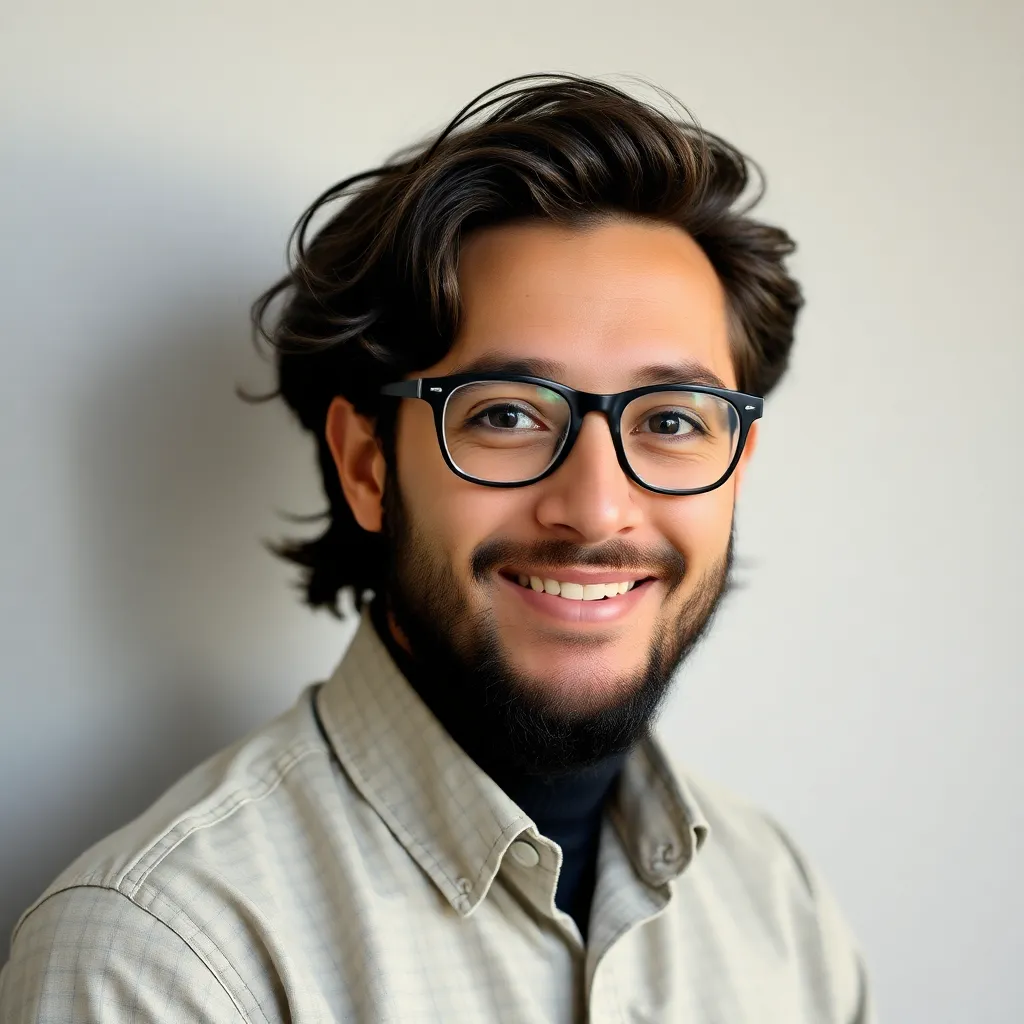
Onlines
Apr 08, 2025 · 6 min read

Table of Contents
Electrical Bonding Investigation Plan: A Quick Check
Ensuring electrical safety is paramount in any setting, from industrial facilities to residential homes. A critical aspect of this safety is proper electrical bonding. A comprehensive electrical bonding investigation plan is essential to identify potential hazards and ensure compliance with relevant electrical codes and regulations. This quick check guide provides a structured approach to investigating electrical bonding, highlighting key areas to inspect and document. This detailed plan allows for a thorough examination, preventing future accidents and potential liabilities.
Understanding Electrical Bonding
Before diving into the investigation plan, let's clarify what electrical bonding entails. Electrical bonding is the process of connecting metallic parts of an electrical system together, to create a low-impedance path for fault currents. This low-impedance path ensures that in the event of a fault (e.g., a short circuit), the fault current is directed safely to ground, minimizing the risk of electric shock or fire. Improper bonding can lead to dangerous voltage potentials on exposed metallic surfaces, posing a significant threat to personnel and equipment.
The Importance of a Thorough Investigation
A reactive approach to electrical safety, addressing issues only after an incident occurs, is far less effective than a proactive approach. Regular inspections and investigations are crucial. A thorough investigation plan helps identify weaknesses in the electrical bonding system before they become hazards. This proactive approach significantly reduces the risk of accidents, equipment damage, and legal liabilities. It also ensures compliance with relevant safety standards and regulations.
Electrical Bonding Investigation Plan: A Quick Check List
This quick check list provides a structured approach to investigating electrical bonding. Remember to always consult relevant electrical codes and regulations specific to your location and the type of installation.
Phase 1: Preparation and Planning
- Scope Definition: Clearly define the scope of the investigation. Specify the areas to be investigated, the types of equipment involved, and the specific bonding systems under scrutiny.
- Team Assembly: Assemble a qualified team with experience in electrical systems and bonding. This might include electricians, electrical engineers, and safety professionals.
- Documentation Review: Review existing documentation, including electrical drawings, previous inspection reports, and maintenance records. This provides a baseline understanding of the existing bonding system.
- Safety Precautions: Establish and implement comprehensive safety precautions. This includes lock-out/tag-out procedures, personal protective equipment (PPE), and appropriate safety training for all team members. This is critical for the safety of your team.
Phase 2: Visual Inspection and Testing
- Visual Inspection of Bonding Conductors: Conduct a thorough visual inspection of all bonding conductors. Look for signs of damage, corrosion, loose connections, or inadequate sizing. Pay close attention to areas subject to vibration or environmental exposure. Document all findings meticulously.
- Grounding Electrode System Check: Inspect the grounding electrode system (GES) for proper installation and connection to the bonding system. Check the grounding electrode for corrosion, damage, or inadequate size. Verify its effectiveness with a ground resistance test.
- Equipment Bonding Check: Inspect the bonding of equipment to the grounding system. Check the integrity of bonding jumpers and connections. Ensure that all metallic enclosures and non-current-carrying metallic parts are effectively bonded. Look for evidence of overheating or arcing.
- Bonding Jumper Sizing: Verify that the bonding jumpers are adequately sized to carry fault currents without excessive voltage drop. Refer to relevant electrical codes and standards for proper sizing. Improper sizing can compromise safety.
- Continuity Testing: Perform continuity tests on all bonding conductors and connections. This verifies the existence of a low-impedance path for fault currents. Use appropriate test equipment and document the results.
- Ground Resistance Testing: Measure the ground resistance of the grounding electrode system. This ensures the system effectively dissipates fault currents to earth. Acceptable resistance values vary depending on local codes and ground conditions.
- Potential Difference Measurement: Measure the potential difference between various metallic parts to identify any voltage imbalances. High voltage differences indicate potential hazards.
Phase 3: Documentation and Reporting
- Detailed Report: Prepare a detailed report documenting all findings from the visual inspection and testing procedures. This report should include:
- Date and time of the investigation.
- Names and qualifications of team members.
- Detailed description of the investigated system.
- Photographs of all observed conditions.
- Results of all tests performed.
- Identification of any deficiencies or non-compliances.
- Recommendations for corrective actions.
- Corrective Action Plan: Develop a corrective action plan to address any identified deficiencies. This plan should include specific actions, timelines, and responsible parties.
- Follow-up Inspection: Schedule a follow-up inspection to verify that the corrective actions have been implemented effectively and the bonding system is functioning properly.
Common Bonding Issues and Solutions:
This section expands on some frequently encountered bonding problems and outlines practical solutions.
1. Corroded Bonding Conductors:
- Problem: Corrosion weakens conductors, increasing resistance and potentially leading to failure during a fault.
- Solution: Clean or replace corroded conductors. Use appropriate corrosion inhibitors where feasible.
2. Loose Connections:
- Problem: Loose connections create high-resistance points, jeopardizing the effectiveness of the bonding system.
- Solution: Tighten or replace loose connections. Ensure proper torque is applied to prevent future loosening.
3. Inadequate Grounding Electrode System:
- Problem: A poorly designed or installed grounding electrode system fails to effectively dissipate fault currents to earth.
- Solution: Improve the grounding electrode system by adding additional grounding rods, enhancing ground contact, or using a more suitable grounding electrode material.
4. Incorrect Bonding Jumper Sizing:
- Problem: Undersized bonding jumpers overheat and fail during a high-fault current.
- Solution: Replace undersized jumpers with appropriately sized conductors according to the relevant electrical codes.
5. Missing Bonds:
- Problem: Missing bonds leave metallic parts unbonded, creating potential shock hazards.
- Solution: Install the missing bonds, ensuring proper connection and continuity.
6. Damaged Bonding Clamps:
- Problem: Damaged clamps create high-resistance points or may completely fail.
- Solution: Replace damaged clamps with new ones, ensuring proper installation and tightness.
7. Improperly Bonded Equipment:
- Problem: Metallic enclosures and components may not be properly bonded to the system, increasing shock hazards.
- Solution: Verify all metallic parts are effectively bonded to the main bonding system.
Software and Tools for Electrical Bonding Investigations
While this guide focuses on the practical aspects of a bonding investigation, various software applications and tools can enhance the process:
- CAD Software: Electrical CAD software allows for detailed visualization and analysis of electrical systems, aiding in identifying potential bonding deficiencies before they occur.
- Fault Current Calculation Software: Specialized software can calculate fault currents, enabling more accurate sizing of bonding conductors and ensuring system resilience.
- Ground Resistance Measurement Devices: High-quality ground resistance meters are vital for accurately assessing the effectiveness of the grounding electrode system.
- Clamp Meters: Clamp meters are used for quick continuity checks and current measurement.
Conclusion
A comprehensive electrical bonding investigation plan is an essential part of any proactive electrical safety program. This quick check guide provides a structured approach to investigating electrical bonding, ensuring the system’s safety and compliance. By consistently implementing these procedures, organizations can effectively mitigate risks, prevent accidents, and safeguard their personnel and assets. Remember, safety should always be the paramount consideration, and adherence to relevant electrical codes and standards is crucial. Regular inspections and a proactive approach are far more effective and cost-efficient than reactive measures taken after an incident occurs.
Latest Posts
Latest Posts
-
Summary Of Love And Friendship By Jane Austen
Apr 17, 2025
-
The Book Of Unknown American Pdf Free
Apr 17, 2025
-
Por Un Amigo Que Los Marquez
Apr 17, 2025
-
Desert Locusts Are Devastating To Agriculture Because
Apr 17, 2025
-
Pedagogy Of The Oppressed Chapter 2
Apr 17, 2025
Related Post
Thank you for visiting our website which covers about Electrical Bonding Investigation Plan Quick Check . We hope the information provided has been useful to you. Feel free to contact us if you have any questions or need further assistance. See you next time and don't miss to bookmark.