Equipment May Be Placed In Inactive Equipment Maintenance
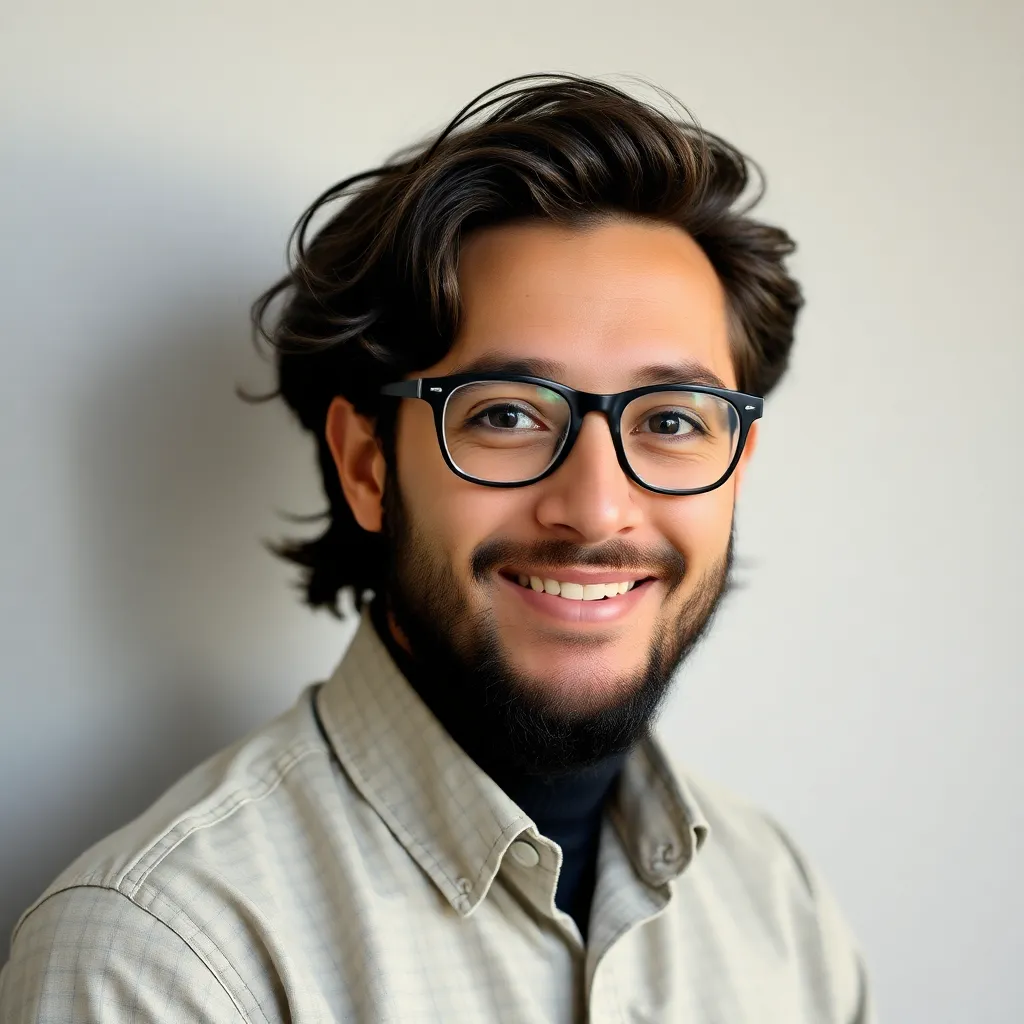
Onlines
Apr 07, 2025 · 6 min read
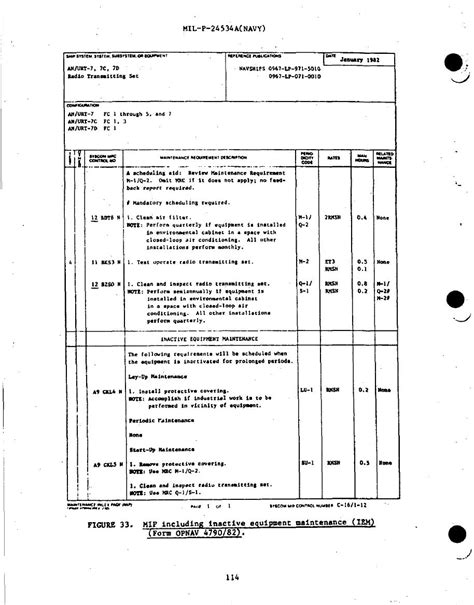
Table of Contents
Equipment May Be Placed in Inactive Equipment Maintenance: A Comprehensive Guide
Maintaining a robust and efficient maintenance program is crucial for any organization relying on equipment for its operations. A key component of this program is understanding and effectively utilizing inactive equipment maintenance. This involves more than just turning off the machine; it's a strategic process aimed at preserving asset value, ensuring safety, and preparing equipment for future reactivation. This comprehensive guide will delve into the nuances of placing equipment in inactive maintenance, exploring best practices, considerations, and the overall benefits of a well-structured inactive maintenance program.
Understanding Inactive Equipment Maintenance
Inactive equipment maintenance refers to the procedures and practices implemented when equipment is not in active use but is expected to be reactivated at a future date. This differs from decommissioning, where equipment is permanently removed from service. The goal of inactive maintenance is to prevent deterioration, maintain safety, and minimize the effort required to return the equipment to operational status.
Key Differences from Decommissioning and Active Maintenance
It’s important to distinguish inactive maintenance from other maintenance strategies:
- Active Maintenance: This involves regular inspections, lubrication, and repairs performed on equipment actively in use to prevent failures and optimize performance.
- Decommissioning: This is the permanent removal of equipment from service, often involving dismantling, disposal, or repurposing. No expectation of future reactivation exists.
- Inactive Maintenance: This focuses on preservation and readiness for future use. It involves specific actions to mitigate degradation and facilitate quick reactivation.
Strategies for Inactive Equipment Maintenance
The specific procedures for inactive maintenance will vary depending on the type of equipment, its complexity, and the anticipated duration of inactivity. However, several core strategies apply across the board:
1. Thorough Cleaning and Inspection
Before placing equipment in inactive status, a thorough cleaning and inspection are crucial. This helps identify any existing damage or potential issues that need addressing before long-term storage. Cleaning prevents corrosion, build-up of debris, and pest infestations. The inspection should cover all components, including mechanical parts, electrical systems, and safety features. Documentation of the inspection findings is essential.
2. Appropriate Storage Conditions
Proper storage is paramount to prevent deterioration. Environmental factors like humidity, temperature, and dust can significantly impact equipment condition. Storage areas should be clean, dry, and temperature-controlled where possible. Equipment should be protected from the elements using covers, enclosures, or specialized storage containers.
3. Preservation Techniques
Specific preservation techniques help to protect against corrosion and degradation:
- Corrosion Inhibitors: Applying corrosion inhibitors to metal surfaces creates a protective barrier against rust and oxidation.
- Dehumidifiers: Using dehumidifiers in storage areas reduces moisture levels, minimizing corrosion and mold growth.
- Desiccants: Placing desiccants (moisture-absorbing materials) inside equipment enclosures helps control humidity.
- Lubrication: Applying lubricants to moving parts helps prevent seizing and corrosion.
4. Regular Monitoring and Scheduled Inspections
While the equipment is inactive, regular monitoring is still necessary. The frequency of inspections will depend on factors like the equipment's criticality, the storage environment, and the expected duration of inactivity. Scheduled inspections should involve visual checks for signs of damage, corrosion, or pest infestation.
5. Documentation and Record Keeping
Maintaining meticulous records is crucial for inactive equipment. This documentation should include:
- Equipment Identification: Unique identifiers, model numbers, serial numbers, etc.
- Inspection Dates and Findings: Detailed reports of all inspections performed.
- Maintenance Activities: A record of all preservation measures taken.
- Storage Location: Precise location of the equipment within the storage facility.
- Contact Person: Designated individual responsible for managing the equipment.
This comprehensive record-keeping system ensures traceability and facilitates efficient reactivation when necessary.
Types of Equipment and Specific Inactive Maintenance Considerations
Different types of equipment require tailored inactive maintenance strategies.
1. Electrical Equipment
Electrical equipment presents unique challenges due to the risk of electrical hazards and degradation of components. Inactive maintenance for electrical equipment includes:
- Disconnecting Power: Completely disconnecting power from the equipment to prevent accidental activation and electrical shocks.
- Grounding: Ensuring proper grounding to prevent electrical surges and static discharge.
- Moisture Protection: Protecting against moisture to prevent corrosion and short circuits.
- Regular Inspections: Regular inspections to detect signs of degradation, such as corrosion or damage to insulation.
2. Mechanical Equipment
Mechanical equipment, such as pumps, motors, and engines, require different considerations:
- Lubrication: Applying appropriate lubricants to moving parts to prevent seizing.
- Corrosion Protection: Applying corrosion inhibitors to metal surfaces.
- Storage Position: Storing equipment in a position that minimizes stress on components.
- Regular Inspections: Checking for signs of corrosion, rust, or damage.
3. Hydraulic and Pneumatic Equipment
Equipment utilizing hydraulic or pneumatic systems necessitates specific attention:
- Fluid Drainage: Draining fluids to prevent degradation and contamination.
- Component Protection: Protecting components against dust and moisture.
- System Pressure Release: Releasing system pressure to prevent damage to components.
- Regular Inspections: Checking for leaks or signs of damage.
Benefits of Effective Inactive Equipment Maintenance
Implementing a robust inactive maintenance program offers several significant benefits:
- Extended Equipment Lifespan: Proper preservation significantly extends the usable lifespan of equipment, reducing replacement costs.
- Reduced Repair Costs: Preventing degradation minimizes the need for extensive repairs upon reactivation.
- Improved Safety: Regular inspections and preservation techniques reduce safety risks associated with equipment malfunction.
- Faster Reactivation: Well-maintained inactive equipment requires less time and effort to reactivate, enabling rapid response to changing demands.
- Cost Savings: Preventing premature failure and minimizing repair costs translates to significant long-term cost savings.
- Enhanced Operational Efficiency: A ready supply of well-maintained equipment ensures smoother operations and minimizes downtime.
- Improved Asset Management: A structured inactive maintenance program contributes to better overall asset management and inventory control.
Implementing a Successful Inactive Equipment Maintenance Program
Implementing a successful program involves several key steps:
1. Establish Clear Procedures and Guidelines
Develop detailed procedures outlining the steps involved in placing equipment into and out of inactive maintenance. These procedures should be readily accessible to all relevant personnel.
2. Assign Responsibilities
Clearly define roles and responsibilities for different aspects of inactive maintenance, including inspections, storage, and record-keeping.
3. Provide Training
Provide adequate training to personnel involved in inactive maintenance to ensure they understand the procedures and safety precautions.
4. Utilize Technology
Implement technology solutions for inventory management, tracking inspections, and scheduling maintenance tasks.
5. Regular Review and Improvement
Regularly review and update the inactive maintenance program to ensure it remains effective and adapts to changing needs and equipment.
Conclusion
Effective inactive equipment maintenance is a critical aspect of a comprehensive maintenance strategy. By implementing the strategies and considerations outlined in this guide, organizations can significantly extend the lifespan of their assets, reduce costs, and enhance safety. A well-structured program ensures equipment is readily available when needed, minimizing downtime and improving operational efficiency. Remember, proactive preservation is far more cost-effective than reactive repairs, making a commitment to inactive maintenance a smart investment for any organization.
Latest Posts
Latest Posts
-
An Effect Of The Steamboats Popularity Was That
Apr 07, 2025
-
Which Choice Does Not Represent A Drug Exception Option
Apr 07, 2025
-
Wisdom In The Christian Worldview Includes The Following
Apr 07, 2025
-
10 1 Skills Practice Areas Of Parallelograms And Triangles
Apr 07, 2025
-
Carmen Temer Gripe Su Hijo Tener
Apr 07, 2025
Related Post
Thank you for visiting our website which covers about Equipment May Be Placed In Inactive Equipment Maintenance . We hope the information provided has been useful to you. Feel free to contact us if you have any questions or need further assistance. See you next time and don't miss to bookmark.