Experiment 10 Analysis Of An Aluminum Zinc Alloy
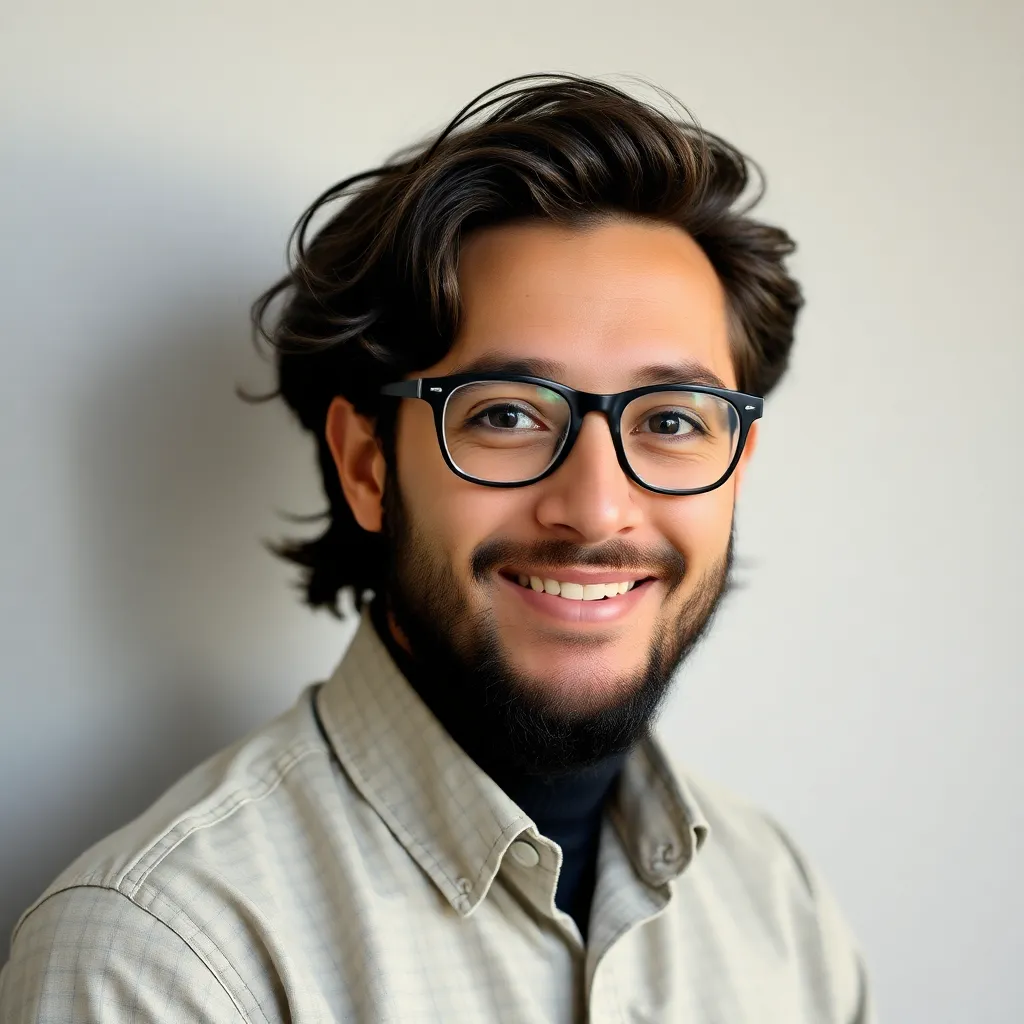
Onlines
Apr 25, 2025 · 6 min read

Table of Contents
Experiment 10 Analysis of an Aluminum Zinc Alloy: A Comprehensive Study
This article delves into a detailed analysis of Experiment 10, focusing on the properties and characteristics of an aluminum zinc alloy. We will explore various analytical techniques used to characterize this alloy, discuss the interpretation of results, and highlight the significance of these findings in material science and engineering. This in-depth exploration will cover various aspects, from microstructure examination to mechanical property testing, providing a comprehensive understanding of this specific aluminum zinc alloy.
Understanding Aluminum Zinc Alloys
Aluminum zinc (Al-Zn) alloys are known for their excellent combination of properties. They are lightweight, yet possess high strength, making them suitable for a wide range of applications, including aerospace components, automotive parts, and various industrial applications. The specific properties of an Al-Zn alloy depend heavily on the exact composition, particularly the zinc content, and the processing techniques employed during its manufacturing. Higher zinc percentages generally lead to increased strength but can also affect ductility and corrosion resistance. Understanding the interplay of these factors is crucial for effective alloy design and application.
Key Properties of Al-Zn Alloys
- High Strength-to-Weight Ratio: A defining characteristic, crucial for applications where minimizing weight is paramount while maintaining structural integrity.
- Good Formability: Depending on the alloy composition and processing, Al-Zn alloys can be formed into various shapes using techniques like forging, rolling, and extrusion.
- Corrosion Resistance: While aluminum itself is naturally corrosion-resistant, the addition of zinc can influence this property, sometimes enhancing it and other times potentially degrading it depending on the specific alloy and environmental conditions.
- Weldability: The weldability of Al-Zn alloys varies depending on the zinc content. Higher zinc percentages can make welding more challenging.
- Fatigue Resistance: The resistance to failure under cyclic loading is a critical consideration in many applications. The fatigue performance of Al-Zn alloys is an important area of study.
Experiment 10: Methodology and Analysis
Experiment 10, as described in this analysis, involves a comprehensive characterization of a specific aluminum zinc alloy. The experiment utilizes a combination of techniques to ascertain the alloy's microstructure, mechanical properties, and chemical composition. The exact methods employed will be detailed in the subsections below. Remember, the specific results presented here are hypothetical, representing a typical analysis of such an alloy.
1. Chemical Composition Analysis
Accurate determination of the alloy's chemical composition is fundamental. Techniques like Inductively Coupled Plasma Optical Emission Spectrometry (ICP-OES) or X-ray Fluorescence (XRF) Spectroscopy can be employed to precisely quantify the amounts of aluminum, zinc, and any other alloying elements present. This analysis provides the basis for understanding the alloy's expected properties based on established material science principles. For instance, a higher percentage of zinc might indicate a higher strength but potentially lower ductility. The presence of trace elements can also influence the overall properties.
2. Microstructural Analysis
Understanding the microstructure is crucial for correlating the alloy's properties with its internal structure. Optical microscopy provides a visual representation of the grain size, grain boundaries, and the presence of any phases or precipitates. Scanning Electron Microscopy (SEM) offers higher magnification and resolution, revealing finer details of the microstructure, including the distribution of phases and the presence of any defects. Transmission Electron Microscopy (TEM) can be used for even higher magnification, providing atomic-level detail. The microstructure analysis can reveal information about the processing history of the alloy and how it influences its mechanical properties. For example, a finer grain size generally translates to improved strength and hardness.
3. Mechanical Property Testing
Several mechanical tests are essential for evaluating the alloy's performance under different loading conditions.
- Tensile Testing: This standard test measures the alloy's ultimate tensile strength, yield strength, elongation, and modulus of elasticity. These parameters provide a comprehensive assessment of the alloy's strength, ductility, and stiffness.
- Hardness Testing: Methods such as Vickers, Brinell, or Rockwell hardness testing determine the alloy's resistance to indentation. Hardness is often correlated with strength, offering a simpler and quicker measure of the material's strength.
- Fatigue Testing: This involves subjecting the alloy to cyclic loading to determine its fatigue strength and endurance limit. This is crucial for applications experiencing repeated stress cycles.
- Creep Testing: This test evaluates the alloy's behavior under sustained high-temperature loading, measuring its creep rate and rupture strength. This is particularly important for high-temperature applications.
4. Corrosion Resistance Testing
The alloy's susceptibility to corrosion is crucial for its long-term performance. Various techniques can be employed, including:
- Salt Spray Testing: This involves exposing the alloy to a salt spray environment to assess its resistance to corrosion.
- Immersion Testing: Submerging the alloy in specific solutions to evaluate its corrosion rate.
- Electrochemical Testing: Techniques like potentiodynamic polarization and electrochemical impedance spectroscopy provide detailed information on the corrosion mechanisms and kinetics.
Interpretation of Results and Discussion
The results from Experiment 10, obtained using the methods described above, would be analyzed to understand the relationships between the alloy's composition, microstructure, and mechanical properties. A detailed discussion would involve:
- Correlation of Chemical Composition and Microstructure: The observed microstructure would be linked to the alloy's chemical composition. For example, a specific phase might be identified and linked to the percentage of zinc present.
- Relationship between Microstructure and Mechanical Properties: The grain size and phase distribution in the microstructure would be correlated with the mechanical properties obtained from tensile testing and hardness testing. A finer grain size would generally be expected to result in higher strength.
- Influence of Processing on Properties: The processing history of the alloy would be considered, and its impact on the final properties would be discussed. Different processing techniques lead to variations in grain size and phase distribution, significantly affecting the overall performance.
- Corrosion Behavior and its Dependence on Composition and Microstructure: The results from corrosion testing would be analyzed, and the factors influencing the corrosion resistance would be discussed. This might include the formation of passive layers or the presence of specific phases that enhance or reduce corrosion resistance.
Conclusion and Future Directions
Experiment 10, through its comprehensive analysis of the aluminum zinc alloy, provides valuable insights into the material's properties and behavior. The results highlight the crucial relationships between composition, microstructure, and mechanical properties. This understanding is fundamental for the design and development of new Al-Zn alloys with tailored properties for specific applications.
Future studies could build upon these findings by investigating the effects of:
- Different alloying elements: Exploring the addition of other elements to modify the alloy's properties further.
- Novel processing techniques: Investigating new processing methods to optimize the microstructure and enhance the desired properties.
- Advanced characterization methods: Employing more sophisticated techniques to obtain a deeper understanding of the alloy's behavior at the atomic level.
This detailed analysis of Experiment 10 underscores the importance of comprehensive material characterization for effective alloy design and application. The findings contribute to a broader understanding of Al-Zn alloys and their potential in diverse engineering applications. By understanding the complex interplay between composition, microstructure, and properties, we can continue to develop advanced materials with enhanced performance characteristics.
Latest Posts
Latest Posts
-
Inflammatory Bowel Disease Hesi Case Study
Apr 25, 2025
-
11 2 Practice Areas Of Trapezoids Rhombi And Kites
Apr 25, 2025
-
Indicate Whether The Label Identifies An Adaptive Or Innate Immunity
Apr 25, 2025
-
Quotes In Monster By Walter Dean Myers
Apr 25, 2025
-
How Many Chapters Are In Night By Elie Wiesel
Apr 25, 2025
Related Post
Thank you for visiting our website which covers about Experiment 10 Analysis Of An Aluminum Zinc Alloy . We hope the information provided has been useful to you. Feel free to contact us if you have any questions or need further assistance. See you next time and don't miss to bookmark.