Fiche Processus Achat Iso 9001 Version 2015
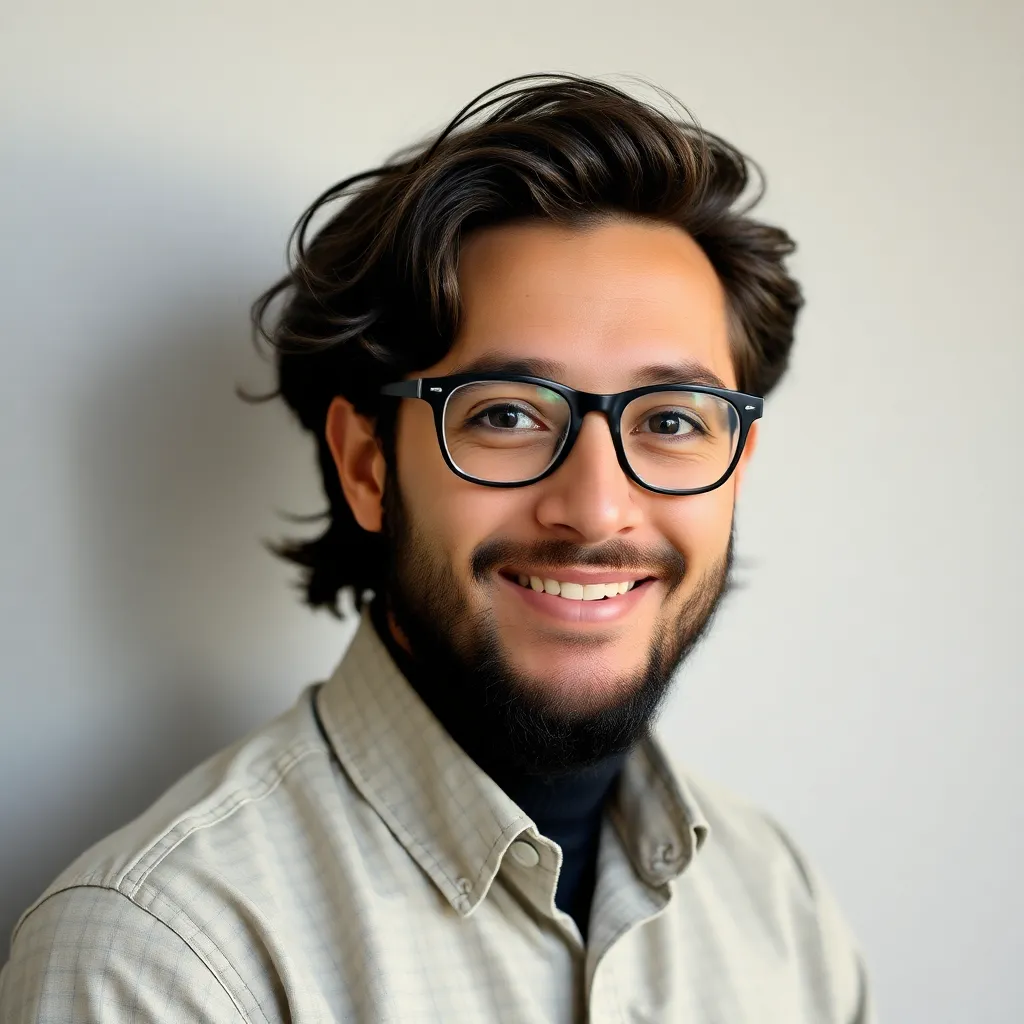
Onlines
May 09, 2025 · 5 min read
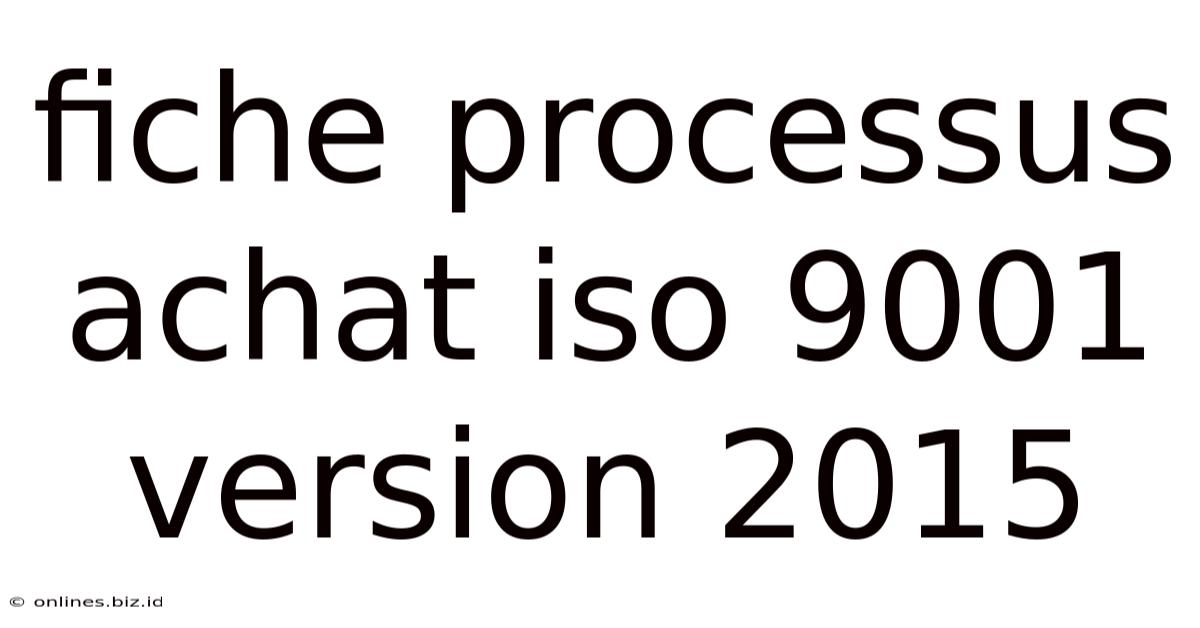
Table of Contents
Fiche Processus Achat ISO 9001 Version 2015: A Comprehensive Guide
The ISO 9001:2015 standard emphasizes a process-based approach to quality management. Understanding and documenting your processes is crucial for certification and maintaining a robust quality management system (QMS). This article delves into the specifics of creating a comprehensive "fiche processus achat" (purchasing process documentation) compliant with ISO 9001:2015. We'll explore key elements, best practices, and considerations for effective implementation.
Understanding the Purchasing Process within ISO 9001:2015
The purchasing process, often overlooked, is a vital component of any successful QMS. It directly impacts product quality, supplier relationships, and overall operational efficiency. ISO 9001:2015 doesn't prescribe a specific purchasing process, but it mandates that organizations identify, control, and monitor all processes impacting product quality. A well-defined purchasing process ensures consistent procurement of goods and services that meet specified requirements.
Key Elements of a Compliant Fiche Processus Achat
Your "fiche processus achat" should clearly outline the following:
-
Process Objective: Define the overall goal of the purchasing process. This should be aligned with the organization's broader quality objectives. For example: "To ensure the timely procurement of high-quality goods and services that meet specified requirements and contribute to customer satisfaction."
-
Process Scope: Clearly define the boundaries of the purchasing process. Specify the types of goods and services covered, the value thresholds, and any exceptions.
-
Inputs: List all inputs required for the process. This includes:
- Purchase Requisition: Details of required goods or services, quantities, specifications, and deadlines.
- Supplier Information: List of approved suppliers, their certifications, and performance history.
- Budgetary Information: Financial limits for the purchase.
- Specifications and Drawings: Technical details outlining required quality characteristics.
-
Activities/Steps: This is the core of your document. Detail each step of the purchasing process in chronological order:
- Need Identification & Requisition: How are purchase needs identified and formalized?
- Supplier Selection: Criteria for selecting suppliers (e.g., price, quality, delivery, certifications). Explain the process for evaluating and approving suppliers. This might involve pre-qualification questionnaires, audits, or performance reviews.
- Negotiation and Contract Management: How are prices negotiated? What contractual terms are in place?
- Order Placement and Tracking: Methods for placing orders and monitoring their progress.
- Goods/Services Receipt and Inspection: Procedures for inspecting incoming goods/services to ensure they conform to specifications. This often involves quality control checks and acceptance criteria.
- Payment Processing: The payment process should be clearly defined.
- Supplier Performance Evaluation: How is supplier performance monitored and reviewed? This includes metrics for on-time delivery, quality, and responsiveness.
-
Outputs: List the tangible outputs of the purchasing process:
- Approved Supplier List: A regularly updated list of approved suppliers.
- Purchase Orders: Formal documentation of the purchase agreement.
- Inspection Reports: Documentation of the inspection process and results.
- Supplier Performance Metrics: Data on supplier performance.
-
Responsibilities and Authorities: Clearly define who is responsible for each step of the process. Specify the authority levels for decision-making, such as approving purchase orders or resolving supplier issues.
-
Resources: Identify the resources needed to execute the purchasing process effectively:
- Personnel: Skills and experience required.
- Equipment: Any specialized equipment used in inspection or other activities.
- Software: ERP systems, procurement software, etc.
-
Process Control: Outline methods for controlling and monitoring the purchasing process. This includes:
- Key Performance Indicators (KPIs): Metrics to measure the effectiveness of the process (e.g., on-time delivery, defect rate, supplier lead times).
- Corrective Actions: Procedures for addressing issues or non-conformances.
- Preventive Actions: Proactive measures to prevent future problems.
-
Record Management: Specify the types of records to be maintained and the retention period.
Best Practices for Creating a Compliant Fiche Processus Achat
- Use Clear and Concise Language: Avoid jargon and technical terms that might not be understood by everyone involved.
- Use Flowcharts or Diagrams: Visual aids can help illustrate the process flow and make it easier to understand.
- Regular Review and Updates: The purchasing process should be reviewed and updated regularly to reflect changes in business requirements or supplier performance.
- Involve Relevant Stakeholders: Engage purchasing personnel, quality control staff, and suppliers in the development and review of the process document.
- Ensure Traceability: Maintain clear documentation to enable easy tracing of materials and services throughout the entire supply chain.
- Implement a Risk-Based Approach: Identify and assess potential risks within the purchasing process and implement appropriate controls.
Integrating the Fiche Processus Achat into your QMS
The "fiche processus achat" should be integrated seamlessly into your overall QMS. This involves:
- Alignment with other Processes: The purchasing process should be aligned with other relevant processes, such as design, production, and customer service.
- Integration with Documentation System: The document should be easily accessible to all relevant personnel.
- Regular Monitoring and Measurement: The effectiveness of the purchasing process should be regularly monitored and measured against pre-defined KPIs.
Addressing Common Challenges
-
Supplier Management: Establishing strong relationships with reliable suppliers is crucial. This includes clear communication, collaborative problem-solving, and fair evaluation of performance.
-
Non-Conformances: Have a well-defined process for handling non-conformances related to purchased goods or services, including root cause analysis and corrective actions.
-
Supply Chain Disruptions: Develop contingency plans to mitigate the impact of potential supply chain disruptions, such as natural disasters or geopolitical instability.
Conclusion: A Foundation for Quality
A well-documented "fiche processus achat" is the cornerstone of a robust purchasing process. By adhering to the principles of ISO 9001:2015 and implementing best practices, organizations can ensure the consistent procurement of high-quality goods and services, leading to improved product quality, enhanced customer satisfaction, and a more efficient supply chain. Remember to regularly review and update your documentation to reflect changes and maintain compliance. This proactive approach will contribute significantly to the overall success and effectiveness of your quality management system. By meticulously documenting your purchasing process, you lay a solid foundation for achieving and maintaining ISO 9001:2015 certification and establishing a culture of continuous improvement within your organization.
Latest Posts
Latest Posts
-
Jasmin Belongs To The Chess Club
May 09, 2025
-
Which Of The Following Best Characterized German Military Tactics
May 09, 2025
-
5 01 Quiz Dna Rna And Proteins
May 09, 2025
-
Which Statement Accurately Analyzes This Passage From A Historical Perspective
May 09, 2025
-
What Does The Bacb Say About Communication And Multiple Relationships
May 09, 2025
Related Post
Thank you for visiting our website which covers about Fiche Processus Achat Iso 9001 Version 2015 . We hope the information provided has been useful to you. Feel free to contact us if you have any questions or need further assistance. See you next time and don't miss to bookmark.