Fixed-order Quantity Inventory Models Are Event Triggered
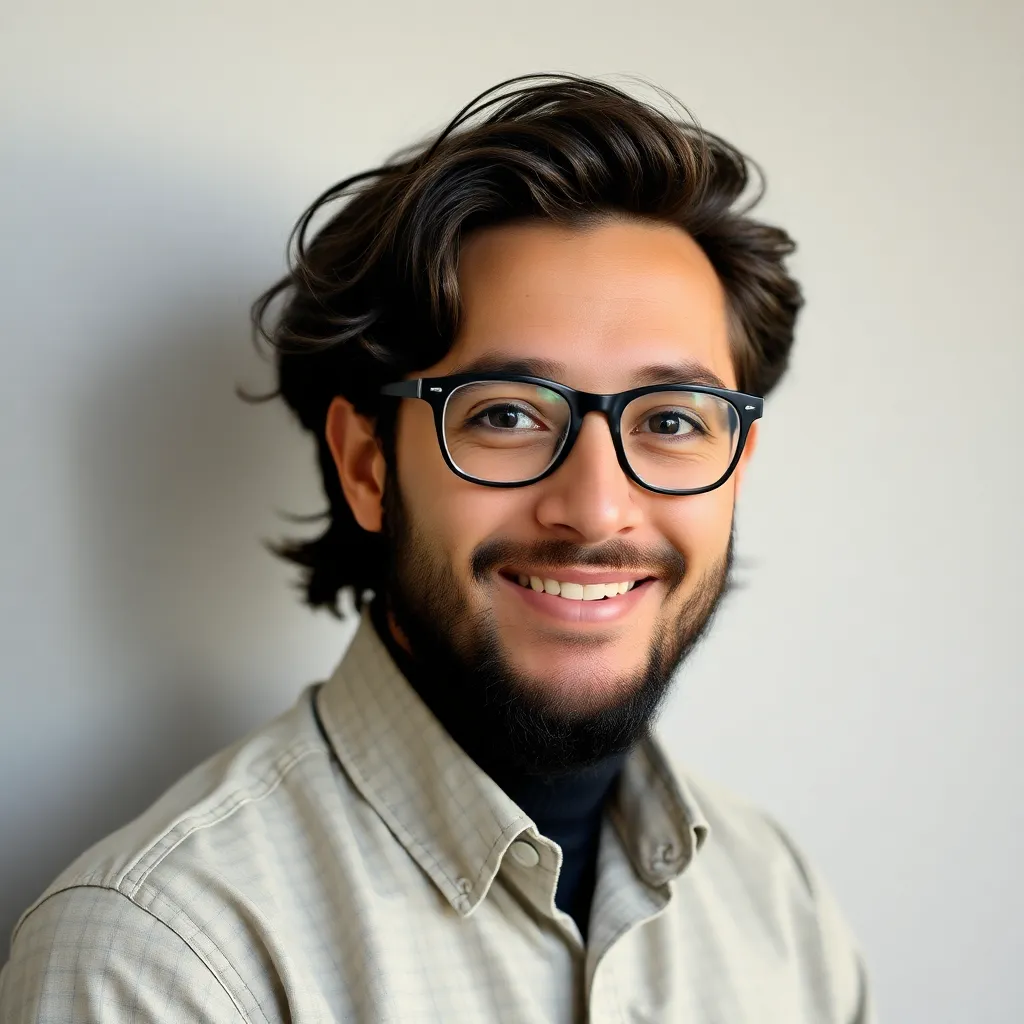
Onlines
May 10, 2025 · 6 min read
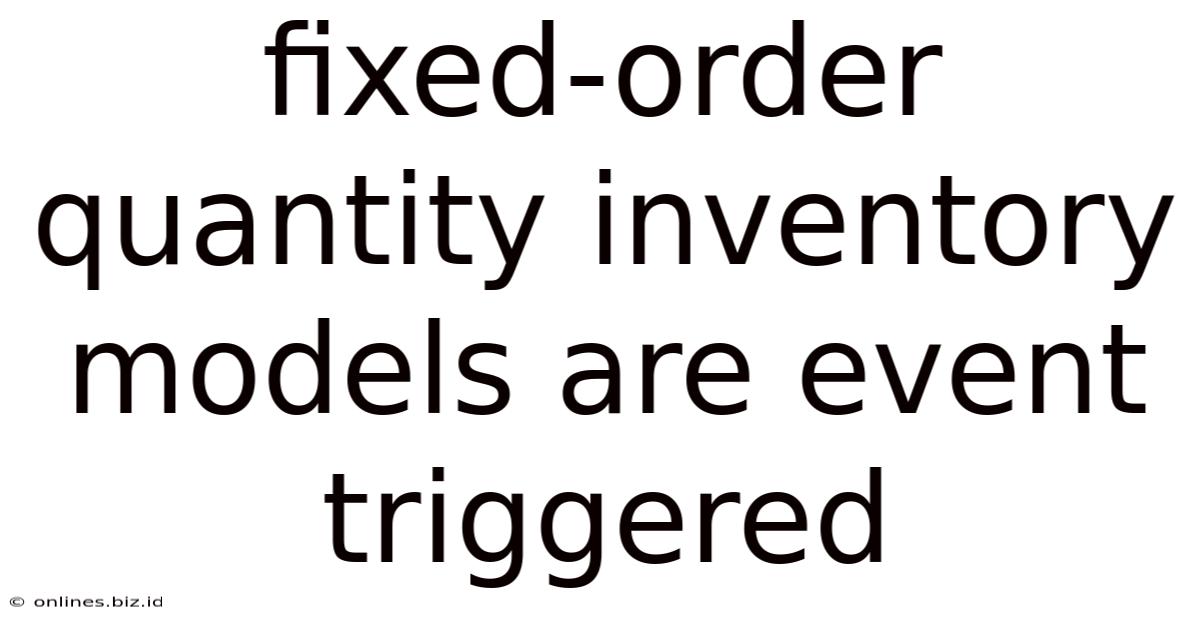
Table of Contents
Fixed-Order Quantity Inventory Models: Event-Triggered Replenishment Strategies
Fixed-order quantity (FOQ) inventory models, also known as Q-models, are a cornerstone of inventory management. These models dictate that a fixed quantity of inventory (Q) is ordered whenever the inventory level falls to a predetermined reorder point (ROP). Unlike fixed-time period models, FOQ models are event-triggered, meaning the replenishment order is initiated by a specific event – the stock reaching the ROP – rather than at a fixed time interval. This event-driven nature offers several advantages and requires careful consideration of various factors for optimal implementation.
Understanding the Mechanics of Event-Triggered FOQ Models
The core principle behind an FOQ model is simple yet powerful. When the inventory level dips to the ROP, a replenishment order for a quantity Q is automatically placed. This process repeats cyclically. The simplicity belies the sophistication involved in determining the optimal values for Q and ROP. These values are intricately linked to several key factors:
1. Demand Rate (D):
This represents the average rate at which inventory is consumed over a specific period. Accurate forecasting of demand is crucial for effective inventory management. Inaccurate demand forecasting can lead to either stockouts (lost sales, dissatisfied customers) or excessive inventory holding costs. Sophisticated forecasting techniques, considering seasonality and trends, are often employed to minimize forecasting errors.
2. Lead Time (L):
Lead time is the time elapsed between placing an order and receiving the inventory. This encompasses various aspects, including order processing, transportation, and supplier lead times. Lead time variability significantly impacts the ROP calculation. Longer and more variable lead times necessitate higher ROPs to buffer against potential stockouts during order fulfillment.
3. Holding Cost (H):
This represents the cost associated with storing one unit of inventory for a specific period. Factors contributing to holding costs include warehousing costs, insurance, obsolescence, and capital tied up in inventory. Minimizing holding costs is a primary goal in inventory optimization.
4. Ordering Cost (S):
This encompasses the fixed cost incurred each time an order is placed. It includes administrative costs, order processing fees, and transportation charges. FOQ models aim to reduce the frequency of orders to minimize ordering costs.
5. Shortage Cost (or Backorder Cost) (b):
This represents the cost incurred when demand exceeds available inventory. This cost can include lost sales revenue, customer dissatisfaction, expedited shipping charges, and potential damage to reputation. Balancing the cost of holding excess inventory with the cost of stockouts is a critical aspect of FOQ model optimization.
Determining Optimal Q and ROP: The Economic Order Quantity (EOQ) and Safety Stock
The optimal order quantity (Q*) is often determined using the Economic Order Quantity (EOQ) formula:
Q = √(2DS/H)*
This formula balances the ordering cost (S) and holding cost (H). A higher Q reduces the number of orders but increases holding costs, while a lower Q increases ordering frequency but reduces holding costs. The EOQ represents the quantity that minimizes the total inventory cost (ordering cost + holding cost).
The reorder point (ROP) is calculated to account for lead time demand and safety stock:
ROP = D * L + Zσ<sub>L</sub>
Where:
- D is the demand rate
- L is the lead time
- Z is the number of standard deviations corresponding to the desired service level (e.g., Z = 1.645 for a 95% service level)
- σ<sub>L</sub> is the standard deviation of lead time demand
Safety stock (Zσ<sub>L</sub>) acts as a buffer against demand variability during lead time. Higher service levels require larger safety stocks, increasing holding costs but reducing the risk of stockouts. The choice of service level depends on the cost of stockouts versus the cost of holding excess inventory.
Advantages of Event-Triggered FOQ Models
The event-triggered nature of FOQ models provides several key advantages:
-
Reduced Ordering Costs: By ordering in larger quantities, the number of orders placed is reduced, leading to lower ordering costs. This is particularly beneficial when ordering costs are significant.
-
Economies of Scale: Larger order quantities can sometimes lead to lower per-unit costs from suppliers due to volume discounts.
-
Simplified Inventory Management: The straightforward nature of the model simplifies inventory tracking and management, reducing the administrative burden.
-
Improved Inventory Control: The fixed order quantity ensures a consistent level of inventory, facilitating better control over inventory levels and minimizing the risk of stockouts.
-
Predictable Ordering Patterns: The event-triggered system allows for predictable ordering patterns, improving supply chain planning and coordination.
Limitations of FOQ Models and Considerations for Implementation
While FOQ models are widely used, they possess certain limitations:
-
Demand Variability: The accuracy of the model relies heavily on accurate demand forecasting. High demand variability can lead to inaccurate ROP calculations and either stockouts or excessive inventory. More sophisticated forecasting techniques, potentially incorporating machine learning, might be necessary to mitigate this.
-
Lead Time Variability: Similar to demand variability, unpredictable lead times can affect the accuracy of ROP calculations. Strategies to reduce lead time variability, such as establishing strong supplier relationships and improving logistics, are beneficial.
-
Bulk Discounts: The EOQ formula doesn't explicitly account for potential quantity discounts. While the EOQ provides a starting point, a more comprehensive analysis might be needed to evaluate the trade-off between holding costs and potential discounts.
-
Perishability and Obsolescence: The model is less suitable for perishable or rapidly obsolescing goods where holding costs increase significantly over time. In such scenarios, alternative inventory models might be more appropriate.
-
Space Constraints: The model doesn't directly consider warehouse space limitations. In situations with limited storage capacity, the order quantity might need to be adjusted to accommodate available space.
Advanced Considerations and Enhancements to FOQ Models
Several advancements and modifications enhance the applicability and effectiveness of FOQ models:
-
Inventory Classification: Categorizing inventory items based on their value and demand (e.g., using ABC analysis) allows for more targeted inventory management strategies. High-value items might warrant more sophisticated models with tighter control, while low-value items might utilize simpler approaches.
-
Safety Stock Optimization: Advanced statistical techniques can be employed to optimize safety stock levels, considering demand and lead time variability more precisely. This can lead to more efficient inventory management with reduced holding costs.
-
Simulation and Optimization Software: Specialized software packages can simulate various scenarios and optimize Q and ROP values based on various parameters and cost functions. This allows for a more robust and data-driven approach to inventory management.
-
Integration with ERP Systems: Integrating FOQ models with Enterprise Resource Planning (ERP) systems facilitates automated order placement and real-time inventory tracking, improving efficiency and accuracy.
-
Demand Forecasting Techniques: Employing advanced forecasting techniques, including time series analysis, exponential smoothing, and machine learning algorithms, can significantly improve the accuracy of demand forecasts, leading to more effective inventory control.
Conclusion: Event-Triggered FOQ Models – A Dynamic Approach to Inventory Management
Fixed-order quantity inventory models, driven by the event of reaching the reorder point, offer a robust and efficient approach to inventory management. While the basic EOQ formula provides a foundation, successful implementation requires careful consideration of various factors, including demand and lead time variability, ordering and holding costs, and service level requirements. By incorporating advanced techniques, such as optimized safety stock calculations, demand forecasting refinements, and integration with ERP systems, businesses can leverage the power of event-triggered FOQ models to achieve substantial improvements in inventory control, cost reduction, and customer service. The key to success lies in understanding the underlying mechanics, adapting the model to specific circumstances, and continuously monitoring and refining the approach based on actual performance data. The dynamic nature of event-triggered replenishment ensures responsiveness to real-world fluctuations, creating a more agile and efficient inventory management system.
Latest Posts
Latest Posts
-
A Po3 Has Been Assigned Temporary Additional Duty Under Instruction
May 10, 2025
-
Foundations Of Government Chapter 1 Test Form A
May 10, 2025
-
Prepare Wells Technical Institutes Income Statement For The Year
May 10, 2025
-
Which Of The Following Statements About Display Rules Is Correct
May 10, 2025
-
Summary Of Diary Of A Madman
May 10, 2025
Related Post
Thank you for visiting our website which covers about Fixed-order Quantity Inventory Models Are Event Triggered . We hope the information provided has been useful to you. Feel free to contact us if you have any questions or need further assistance. See you next time and don't miss to bookmark.