For Each Statement About Product Quality Control Testing
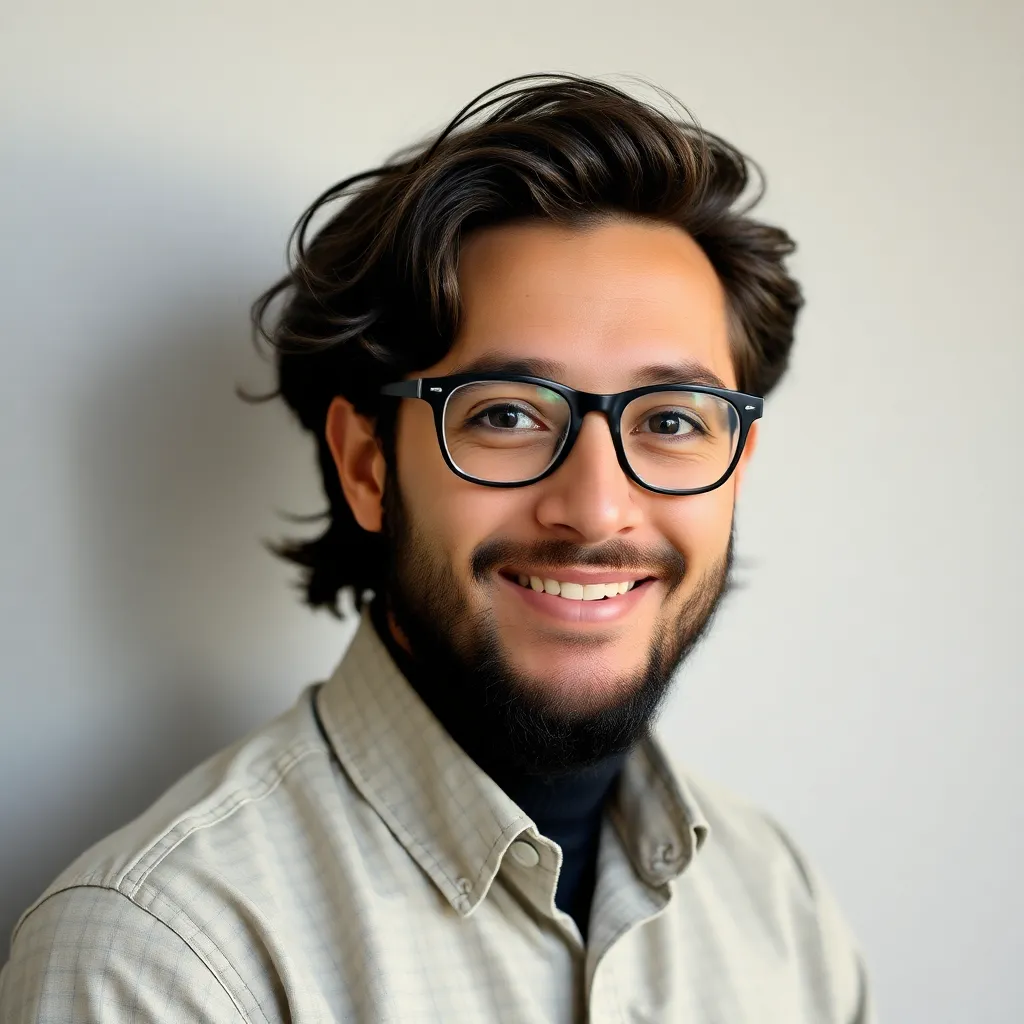
Onlines
Mar 15, 2025 · 7 min read
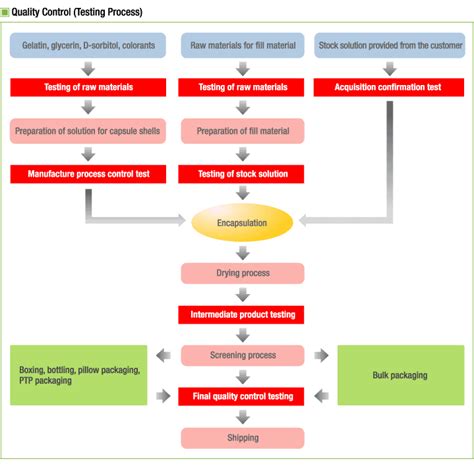
Table of Contents
For Each Statement About Product Quality Control Testing: A Comprehensive Guide
Product quality control (QC) testing is the cornerstone of any successful manufacturing or service-based business. It's the process of ensuring that products or services meet predetermined standards before reaching the customer. This involves a rigorous series of inspections and tests designed to identify defects, inconsistencies, and areas for improvement. This article delves deep into various statements about product quality control testing, providing detailed explanations, examples, and best practices.
Understanding the Fundamentals of Product Quality Control Testing
Before we dive into specific statements, let's establish a common understanding of the core principles of product quality control testing. Effective QC testing involves:
-
Defining clear quality standards: This is the crucial first step. Standards should be specific, measurable, achievable, relevant, and time-bound (SMART). They define acceptable tolerances for dimensions, performance, functionality, and other relevant aspects.
-
Implementing appropriate testing methods: The choice of testing methods depends on the product and its characteristics. Methods can range from simple visual inspections to complex, automated testing procedures.
-
Documenting all processes and results: Comprehensive documentation is vital for traceability, accountability, and continuous improvement. This includes detailed records of testing procedures, results, and any corrective actions taken.
-
Utilizing statistical analysis: Statistical methods help analyze test data, identify trends, and assess the overall quality of the product. Control charts and other statistical tools are frequently employed.
-
Continuous improvement: QC testing isn't a one-time event; it's an ongoing process. Regular analysis of test results allows for continuous improvement in the manufacturing process and reduction of defects.
Analyzing Statements About Product Quality Control Testing
Let's now dissect several statements concerning product quality control testing, providing detailed analysis and practical insights for each.
Statement 1: "Product quality control testing is only necessary for manufacturing companies."
FALSE. While manufacturing companies are heavily reliant on product quality control testing, this is a misconception. The principle of ensuring quality standards extends to all types of businesses, including service-based organizations. For example:
-
Software companies: Rigorous testing is crucial to ensure software functionality, security, and user experience. This involves unit testing, integration testing, system testing, and user acceptance testing.
-
Hospitality industry: Hotels and restaurants regularly inspect cleanliness, service quality, and food safety to maintain standards. Customer feedback surveys also serve as a form of quality control.
-
Healthcare: Hospitals and clinics implement strict protocols for sterilization, medication accuracy, and patient care to ensure quality and safety.
Statement 2: "100% inspection is always the most effective quality control method."
FALSE. While aiming for perfection is admirable, 100% inspection is often impractical and cost-prohibitive, particularly for high-volume production. It can also lead to inspector fatigue and reduced accuracy. Statistical sampling methods, such as acceptance sampling, provide a more efficient and cost-effective way to assess product quality. These methods involve inspecting a statistically representative sample of the product batch to infer the quality of the entire lot. The sample size is determined using statistical calculations based on the desired level of confidence and acceptable quality level (AQL).
Statement 3: "Automated testing is always superior to manual testing."
FALSE. Automated and manual testing each have their strengths and weaknesses. Automated testing is ideal for repetitive tasks, large datasets, and situations requiring high speed and precision. However, it can be costly to implement and maintain, and may not be suitable for all types of testing. Manual testing, on the other hand, allows for more in-depth analysis, creative problem-solving, and the identification of subtle usability issues that automation may miss. A balanced approach, combining both automated and manual testing, often yields the best results. The optimal balance will vary depending on the specific product and testing requirements.
Statement 4: "Quality control testing is solely responsible for ensuring product quality."
FALSE. Product quality is a holistic endeavor involving multiple aspects throughout the product lifecycle, beginning from design and development. While QC testing plays a critical role in identifying defects, it's not the sole guarantor of quality. A robust quality management system (QMS) is crucial, encompassing processes like design review, material selection, manufacturing processes, and supplier management. A strong focus on preventive measures, such as robust design principles and process improvement, is equally essential to minimizing defects before they occur.
Statement 5: "Quality control testing should only focus on identifying defects."
FALSE. While defect detection is a crucial aspect, a comprehensive QC program should also aim to provide valuable insights for continuous improvement. Analyzing test data can reveal underlying issues in the manufacturing process, design flaws, and areas where improvements can be made to enhance product quality and efficiency. This data-driven approach fosters continuous improvement and enhances overall product quality over time. Root cause analysis techniques, such as the 5 Whys method, can be used to uncover the underlying causes of defects and to prevent similar issues from recurring.
Statement 6: "Customer feedback is not a part of product quality control testing."
FALSE. Customer feedback is an invaluable source of information about product quality and can significantly enhance the effectiveness of QC testing. Customer reviews, surveys, and support interactions can identify issues that may not be apparent through internal testing. This feedback allows manufacturers to address issues promptly, improve product design and functionality, and enhance overall customer satisfaction. Integrating customer feedback into the QC process creates a closed-loop system that continuously improves product quality based on real-world usage.
Statement 7: "Quality control testing is a cost center and adds no value to the business."
FALSE. This is a short-sighted perspective. Investing in robust quality control testing ultimately saves money by reducing product recalls, warranty claims, and reputational damage. The cost of correcting defects discovered after a product reaches the market is substantially higher than identifying and fixing them during the manufacturing process. High-quality products lead to increased customer satisfaction, brand loyalty, and ultimately, higher profits. Effective quality control adds significant value by ensuring that the product meets customer expectations and maintains the company's reputation.
Statement 8: "The only goal of quality control testing is to meet minimum regulatory requirements."
FALSE. While complying with regulatory standards is essential, it should not be the sole objective. A focus solely on minimum compliance limits potential for innovation and competitive advantage. Striving for superior quality that surpasses regulatory requirements differentiates a product in the market and enhances its competitiveness. Proactive quality management, including rigorous testing and continuous improvement efforts, positions a business for success beyond mere regulatory compliance.
Statement 9: "All quality control tests must be destructive."
FALSE. Destructive testing, while necessary in some cases, is not always required. Non-destructive testing methods allow for product evaluation without damaging the product. Examples include visual inspection, ultrasonic testing, X-ray inspection, and magnetic particle inspection. These methods are often preferred for high-value products or when destructive testing is impractical or too costly. The choice between destructive and non-destructive testing depends on the specific product, testing requirements, and cost-benefit analysis.
Statement 10: "Quality control testing is a solely technical process."
FALSE. Quality control testing involves a multitude of factors beyond technical aspects. Effective QC testing necessitates strong communication, teamwork, and collaboration across various departments, including engineering, manufacturing, and customer service. Data analysis skills and understanding of statistical methods are also essential for interpreting test results and making informed decisions. Furthermore, a strong emphasis on continuous improvement and a culture of quality are crucial to ensuring the long-term success of a product QC program.
Conclusion: The Ongoing Importance of Product Quality Control Testing
Product quality control testing is not a simple process but a multifaceted system crucial for business success. By understanding the principles outlined above and avoiding common misconceptions, businesses can build robust QC programs that improve product quality, enhance customer satisfaction, and drive profitability. Continuous improvement, data-driven decision making, and a collaborative approach are key to maximizing the effectiveness of QC testing and ensuring long-term success in the competitive marketplace. Remember that proactive quality management, encompassing all stages of product development and beyond, is vital for building a strong reputation and achieving sustainable growth.
Latest Posts
Latest Posts
-
Summary Of The Crucible Act 2
Mar 15, 2025
-
What Do You Give A Dog That Loves Computers
Mar 15, 2025
-
Mitosis And The Cell Cycle Webquest Answer Key
Mar 15, 2025
-
The Outsiders Book Summary Of Each Chapter
Mar 15, 2025
-
Amoeba Sisters Video Recap Cell Transport
Mar 15, 2025
Related Post
Thank you for visiting our website which covers about For Each Statement About Product Quality Control Testing . We hope the information provided has been useful to you. Feel free to contact us if you have any questions or need further assistance. See you next time and don't miss to bookmark.