For Inventoriable Costs To Become Expenses Under The Matching Principle
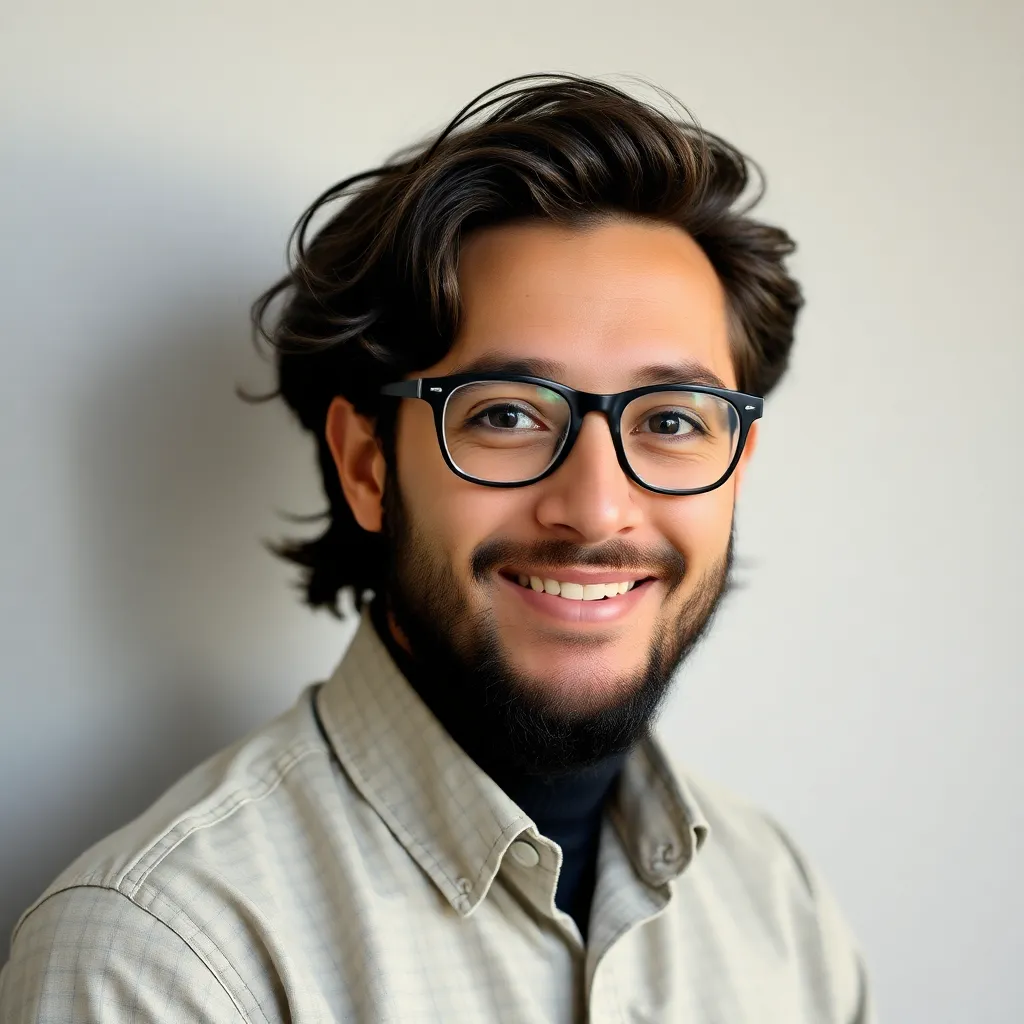
Onlines
May 10, 2025 · 6 min read
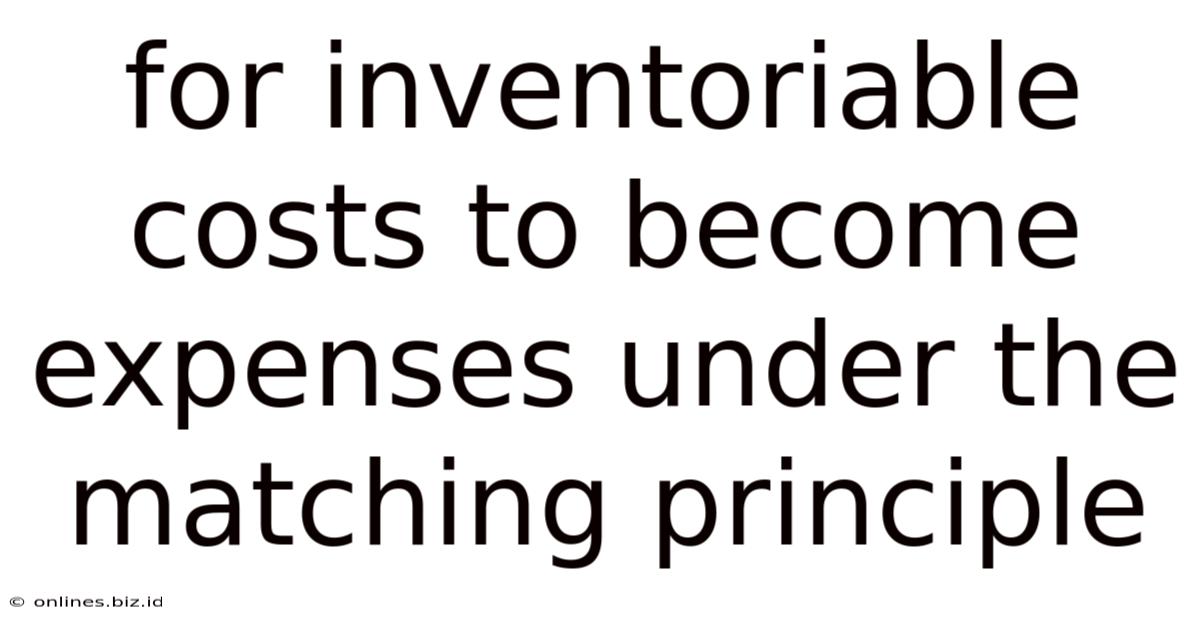
Table of Contents
For Inventoriable Costs to Become Expenses Under the Matching Principle
The matching principle is a fundamental concept in accounting that dictates that expenses should be recognized in the same period as the revenues they help generate. This ensures a fair and accurate representation of a company's financial performance. However, not all costs are immediately expensed. Inventoriable costs, those associated with acquiring or producing goods intended for sale, follow a different path. Understanding how inventoriable costs transition from assets to expenses under the matching principle is crucial for accurate financial reporting. This article delves deep into this process, exploring the various aspects and nuances involved.
Understanding Inventoriable Costs
Inventoriable costs are all the costs directly related to acquiring or producing goods held for sale in the ordinary course of business. These costs are capitalized, meaning they are recorded as assets on the balance sheet until the goods are sold. Only then do they become expenses on the income statement. Several key components make up inventoriable costs:
Direct Materials
These are the raw materials that directly become part of the finished product. For a bakery, this includes flour, sugar, and eggs. For a car manufacturer, it would be steel, rubber, and glass. The cost of these materials is a direct and integral part of the final product’s cost.
Direct Labor
This encompasses the wages and benefits paid to employees directly involved in the production process. For example, the wages of bakers in a bakery or assembly line workers in a car factory are considered direct labor. This cost is directly attributable to the creation of the goods.
Manufacturing Overhead
This includes all indirect costs associated with the manufacturing process. These are costs that are difficult to trace directly to a specific product but are necessary for its production. Examples include:
- Factory rent: The cost of renting the space where production takes place.
- Factory utilities: Electricity, water, and gas used in the factory.
- Factory equipment depreciation: The allocation of the cost of factory equipment over its useful life.
- Indirect labor: Wages of factory supervisors, maintenance personnel, and other support staff.
The accurate allocation of manufacturing overhead is crucial for proper cost accounting. Methods such as machine hours or direct labor hours are commonly used to allocate these costs to individual products.
The Journey from Inventoriable Cost to Expense: The Role of Inventory
The core principle governing the transition of inventoriable costs from assets to expenses is the concept of cost of goods sold (COGS). COGS represents the direct costs of producing the goods sold during a specific period. This is where the matching principle comes into play. The revenue generated from the sale of goods is matched with the cost of producing those goods in the same accounting period. The process works as follows:
-
Capitalization: When inventoriable costs are incurred, they are not immediately expensed. Instead, they are added to the value of inventory on the balance sheet. This is because the costs are associated with assets (the goods) that are still available for sale.
-
Valuation of Inventory: Several methods exist to value inventory, including FIFO (First-In, First-Out), LIFO (Last-In, First-Out), and weighted-average cost. The chosen method significantly impacts the value of inventory and, consequently, the COGS.
-
Cost of Goods Sold (COGS): When goods are sold, their associated inventoriable costs are transferred from the inventory account to the cost of goods sold (COGS) account. This is the mechanism by which the matching principle is satisfied. The revenue recognized from the sale is offset by the cost of producing the goods sold.
-
Expense Recognition: COGS is an expense account on the income statement. By transferring the inventoriable costs to COGS, these costs are finally recognized as expenses. This aligns the expense recognition with the revenue generation, fulfilling the matching principle.
Detailed Breakdown of the Matching Process
Let’s illustrate this process with a simplified example. Imagine a small furniture maker produces 100 chairs. The inventoriable costs are as follows:
- Direct Materials: $10 per chair
- Direct Labor: $5 per chair
- Manufacturing Overhead: $3 per chair
Total inventoriable cost per chair: $18
If the furniture maker sells 70 chairs during the accounting period, the calculation for COGS would be:
COGS = 70 chairs x $18/chair = $1260
This $1260 is then recorded as an expense on the income statement. The remaining 30 chairs, representing unsold inventory, would remain as an asset on the balance sheet with a value of:
Unsold Inventory Value = 30 chairs x $18/chair = $540
Implications of Inventory Valuation Methods
The choice of inventory valuation method significantly impacts the COGS and, consequently, the net income. Here’s a brief overview:
-
FIFO (First-In, First-Out): Assumes that the oldest goods are sold first. During periods of inflation, this method leads to a lower COGS and higher net income because older, cheaper goods are expensed.
-
LIFO (Last-In, First-Out): Assumes that the newest goods are sold first. During periods of inflation, this method leads to a higher COGS and lower net income because newer, more expensive goods are expensed. LIFO is not permitted under International Financial Reporting Standards (IFRS).
-
Weighted-Average Cost: Calculates the average cost of all goods available for sale and uses this average cost to determine COGS. This method provides a smoother representation of cost fluctuations compared to FIFO and LIFO.
Importance of Accurate Inventory Management
Accurate inventory management is crucial for the proper application of the matching principle. If inventory is mismanaged, the COGS calculation will be inaccurate, leading to misstated financial results. This can have significant implications for various stakeholders, including investors, creditors, and tax authorities. Effective inventory management techniques include:
- Regular stock taking: Periodically counting and verifying the physical inventory to ensure accuracy.
- Inventory tracking systems: Using technology to track inventory levels and movements.
- Proper storage and handling: Protecting inventory from damage and loss.
- Efficient ordering and procurement: Minimizing inventory holding costs while ensuring sufficient supply.
Beyond the Basics: Addressing Complexities
The application of the matching principle to inventoriable costs is not always straightforward. Several complexities can arise:
-
Joint Products and By-Products: When multiple products are produced from a single production process, allocating costs to individual products requires careful consideration.
-
Spoilage and Waste: Costs associated with spoiled or wasted goods need to be appropriately accounted for and expensed.
-
Abnormal Waste: Costs resulting from abnormal spoilage or waste are expensed immediately, not capitalized as part of inventory.
-
Net Realizable Value: In cases where the market value of inventory falls below its cost, the inventory may need to be written down to its net realizable value, impacting the COGS.
Conclusion: The Matching Principle in Action
The matching principle is a cornerstone of accrual accounting, ensuring that a company's financial statements reflect its economic performance accurately. The transition of inventoriable costs to expenses via the cost of goods sold (COGS) is a vital element of this principle. Understanding the components of inventoriable costs, the inventory valuation methods, and the potential complexities involved is crucial for accurate financial reporting and decision-making. Proper inventory management and a thorough understanding of accounting principles ensure that the matching principle is applied correctly, providing a clear and reliable picture of a company’s financial health. Through careful tracking and application of these principles, businesses can accurately reflect their profitability and build a strong foundation for financial stability.
Latest Posts
Latest Posts
-
The Benefit Of Naturalistic Observation Studies Is
May 10, 2025
-
Tomb Of The Triclinium Ap Art History
May 10, 2025
-
Which In Text Citation Is Formatted Correctly
May 10, 2025
-
Which Of The Following Budgets Shows The Companys Planned Profit
May 10, 2025
-
Cell Homeostasis Virtual Lab Worksheet Answers Pdf
May 10, 2025
Related Post
Thank you for visiting our website which covers about For Inventoriable Costs To Become Expenses Under The Matching Principle . We hope the information provided has been useful to you. Feel free to contact us if you have any questions or need further assistance. See you next time and don't miss to bookmark.