Hazard Prevention And Control Should Contain Both
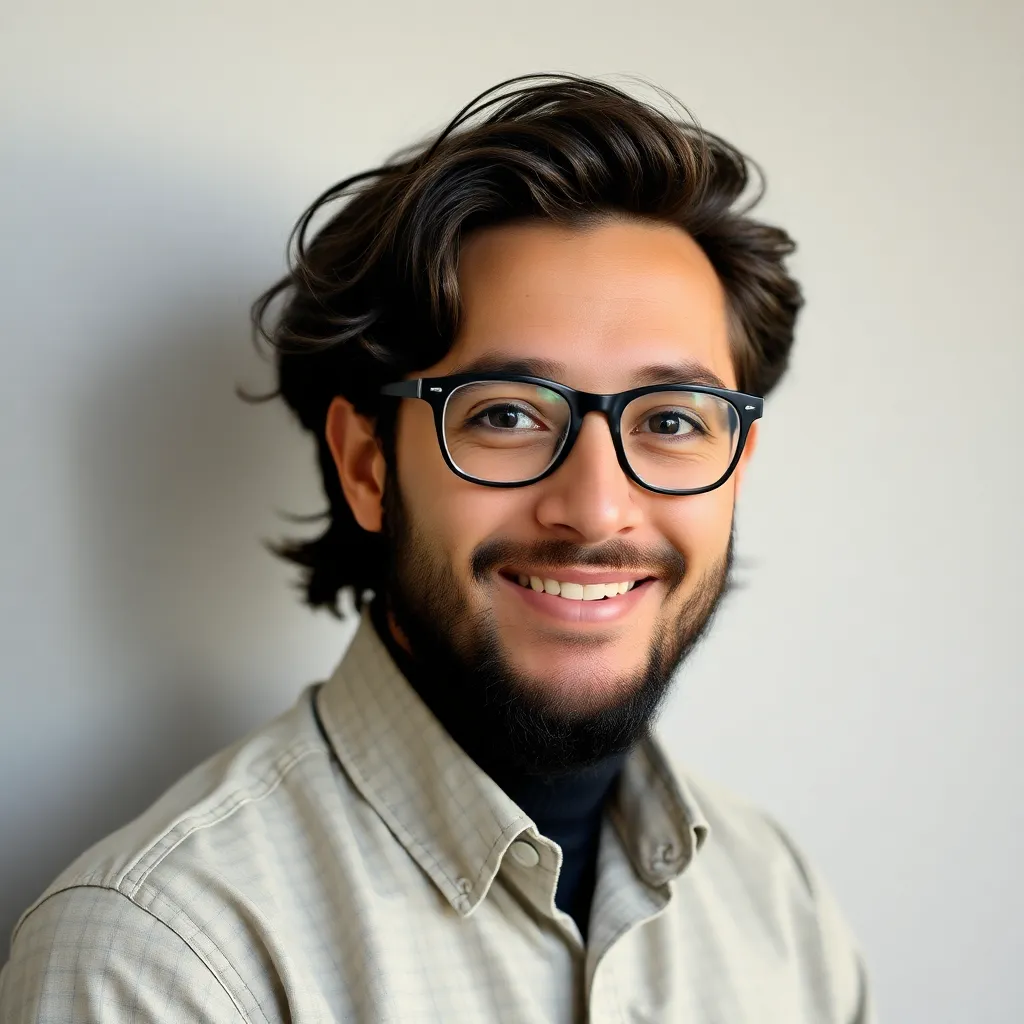
Onlines
Apr 25, 2025 · 8 min read

Table of Contents
Hazard Prevention and Control: A Comprehensive Guide
Hazard prevention and control is a critical aspect of ensuring a safe and healthy work environment. It involves proactively identifying, assessing, and mitigating potential hazards before they can cause harm. This comprehensive guide delves into the multifaceted nature of hazard prevention and control, exploring key principles, practical strategies, and best practices. We'll cover both the theoretical underpinnings and practical applications, equipping you with the knowledge to build a robust hazard prevention and control system.
Understanding Hazards and Risks
Before diving into prevention and control strategies, it's crucial to understand the fundamental concepts of hazards and risks.
What is a Hazard?
A hazard is anything with the potential to cause harm. This encompasses a wide range of elements, including:
- Physical hazards: These include things like noise, vibration, radiation, extreme temperatures, electricity, and ergonomic issues (poor posture, repetitive movements).
- Chemical hazards: This category involves exposure to harmful substances such as gases, liquids, solids, or dusts.
- Biological hazards: These are hazards stemming from living organisms, including bacteria, viruses, fungi, and parasites. This is particularly relevant in healthcare, agriculture, and waste management.
- Ergonomic hazards: These relate to the design of the workplace and tasks, leading to musculoskeletal disorders (MSDs) due to repetitive movements, awkward postures, forceful exertions, or vibration.
- Psychosocial hazards: Stress, harassment, bullying, and violence are all examples of psychosocial hazards that can significantly impact employee well-being and productivity.
- Safety hazards: This encompasses a broad range of physical hazards such as unsafe equipment, slips, trips, and falls, inadequate lighting, and fire hazards.
What is Risk?
Risk is the likelihood that a hazard will cause harm, combined with the severity of that harm. Risk assessment considers both the probability of an incident occurring and the potential consequences. A high-risk situation involves a high probability of a significant incident, while a low-risk situation presents a lower probability of a less severe incident.
The Hierarchy of Hazard Control
The hierarchy of hazard control is a fundamental principle guiding the approach to hazard management. It prioritizes elimination or substitution as the most effective control measures, followed by engineering controls, administrative controls, and finally, personal protective equipment (PPE).
1. Elimination
Elimination involves completely removing the hazard from the workplace. This is the most effective control measure, as it removes the potential for harm entirely. For example, eliminating a hazardous chemical process altogether might involve switching to a safer alternative.
2. Substitution
Substitution involves replacing a hazardous substance or process with a less hazardous alternative. For instance, replacing a solvent with a water-based cleaner or using robotic automation to reduce manual handling tasks.
3. Engineering Controls
Engineering controls involve modifying the workplace or equipment to reduce the risk. This can include things like installing machine guards, improving ventilation, or implementing lockout/tagout procedures to prevent accidental energy release. Engineering controls are often preferred because they are built-in safeguards and don't rely on employee behavior.
4. Administrative Controls
Administrative controls focus on modifying work practices and procedures to minimize risk. This might include implementing job rotation, providing training, developing safe work procedures, improving communication, and establishing clear lines of responsibility. They often involve changes to work schedules, procedures, or training.
5. Personal Protective Equipment (PPE)
Personal protective equipment (PPE) is the least effective control measure in the hierarchy. PPE includes items like safety glasses, gloves, respirators, and hearing protection. While PPE is essential in some situations, it should be considered only after all other control measures have been implemented. PPE protects the individual but does not address the root cause of the hazard.
Hazard Identification and Risk Assessment
Identifying hazards and assessing risks are crucial first steps in hazard prevention and control. These processes involve systematically examining the workplace to pinpoint potential hazards and evaluate the associated risks.
Methods for Hazard Identification
Several methods can be employed to identify hazards effectively:
- Workplace inspections: Regular inspections by trained personnel can identify hazards and assess their potential risks.
- Job safety analysis (JSA): JSAs involve systematically breaking down a task into individual steps and identifying potential hazards at each stage.
- Hazard and operability study (HAZOP): A HAZOP is a structured approach to identifying potential hazards in a process or system.
- Failure mode and effects analysis (FMEA): FMEA is a systematic method for identifying potential failures in a system or process and analyzing their potential effects.
- Checklists and surveys: Checklists and surveys can be used to identify potential hazards in specific areas or tasks.
- Near-miss reporting: Encouraging employees to report near-miss incidents can help identify potential hazards before they cause accidents.
Risk Assessment Process
A risk assessment involves evaluating the likelihood and severity of harm from identified hazards. This typically involves:
- Identifying hazards: List all potential hazards.
- Determining the likelihood of occurrence: Assess the probability of each hazard occurring.
- Determining the severity of harm: Evaluate the potential consequences if the hazard occurs.
- Evaluating the level of risk: Combine the likelihood and severity to determine the overall level of risk (high, medium, low).
- Implementing control measures: Develop and implement control measures to reduce the risk to an acceptable level.
- Review and update: Regularly review and update the risk assessment as the workplace changes.
Implementing Hazard Control Measures
Once hazards and risks have been identified and assessed, appropriate control measures should be implemented. This involves choosing the most effective control measures from the hierarchy and ensuring they are implemented correctly.
Practical Examples of Control Measures
- Eliminating the hazard: Removing asbestos from a building.
- Substituting a hazardous substance: Replacing a solvent with a water-based alternative.
- Engineering controls: Installing machine guards, implementing lockout/tagout procedures, improving ventilation.
- Administrative controls: Implementing job rotation, providing training, developing safe work procedures.
- Personal Protective Equipment (PPE): Providing safety glasses, gloves, respirators, and hearing protection.
Monitoring and Review
Hazard prevention and control is an ongoing process. Regular monitoring and review are essential to ensure the effectiveness of implemented control measures and to identify any new hazards that may have emerged.
Monitoring Activities
- Regular inspections: Conducting regular inspections to identify any hazards that may have been missed or that have developed over time.
- Accident investigation: Investigating accidents and near misses to identify contributing factors and improve preventative measures.
- Health surveillance: Monitoring the health of employees to detect any early signs of work-related illnesses.
- Performance indicators: Tracking key performance indicators (KPIs) to monitor the effectiveness of the hazard prevention and control system.
Review and Update
The risk assessment and hazard control measures should be reviewed and updated regularly. This is especially important when:
- There are changes in the workplace or work processes.
- New hazards are identified.
- There are accidents or near misses.
- There are changes in legislation or best practices.
Legal and Regulatory Compliance
Organizations have a legal and ethical responsibility to ensure the safety and health of their employees. Compliance with relevant health and safety legislation is crucial. This includes:
- OSHA (Occupational Safety and Health Administration) regulations (in the US): These regulations set standards for workplace safety and health.
- WHMIS (Workplace Hazardous Materials Information System) (in Canada): This system provides information on hazardous materials in the workplace.
- COSHH (Control of Substances Hazardous to Health) regulations (in the UK): These regulations control exposure to hazardous substances.
- Other regional and national regulations: Many countries have their own specific health and safety regulations.
Compliance involves understanding and adhering to all relevant regulations, implementing appropriate control measures, and maintaining comprehensive records.
Training and Communication
Effective hazard prevention and control requires a commitment from all levels of the organization. Training and communication play a crucial role in fostering a strong safety culture.
Employee Training
Employees should receive adequate training on hazard identification, risk assessment, and the use of control measures. Training should be tailored to the specific hazards present in the workplace and the roles of the employees.
Communication Strategies
Effective communication is vital for sharing information about hazards and control measures. This can involve:
- Regular safety meetings: Holding regular meetings to discuss safety issues and provide updates on hazard control measures.
- Safety newsletters: Publishing newsletters to communicate safety information to employees.
- Signage and posters: Using signage and posters to communicate safety messages in the workplace.
- Incident reporting systems: Implementing systems for reporting incidents and near misses.
Building a Strong Safety Culture
A strong safety culture is essential for effective hazard prevention and control. This involves creating a workplace where safety is a top priority and everyone takes responsibility for their own safety and the safety of others.
Key Elements of a Strong Safety Culture
- Leadership commitment: Leaders must demonstrate a strong commitment to safety.
- Employee involvement: Employees should be actively involved in the hazard prevention and control process.
- Open communication: There should be open communication between management and employees about safety concerns.
- Accountability: Individuals should be held accountable for their safety performance.
- Continuous improvement: The hazard prevention and control system should be continuously improved.
By implementing these strategies and principles, organizations can create a safer and healthier work environment, reducing the risk of accidents and illnesses. Remember that hazard prevention and control is an ongoing process, requiring constant vigilance, adaptation, and a commitment to continuous improvement.
Latest Posts
Latest Posts
-
Interactive Grammar Tutorial Present Tense Of Ar Verbs
Apr 25, 2025
-
Graphing Radical Functions Quiz Part 1
Apr 25, 2025
-
Gizmo Answer Key Heat Transfer By Conduction
Apr 25, 2025
-
Advance Study Assignment The Alkaline Earths And The Halogens
Apr 25, 2025
-
When A Stimulus Delta Is Presented A Particular Response Is
Apr 25, 2025
Related Post
Thank you for visiting our website which covers about Hazard Prevention And Control Should Contain Both . We hope the information provided has been useful to you. Feel free to contact us if you have any questions or need further assistance. See you next time and don't miss to bookmark.