How To Calculate Time To Fatigue
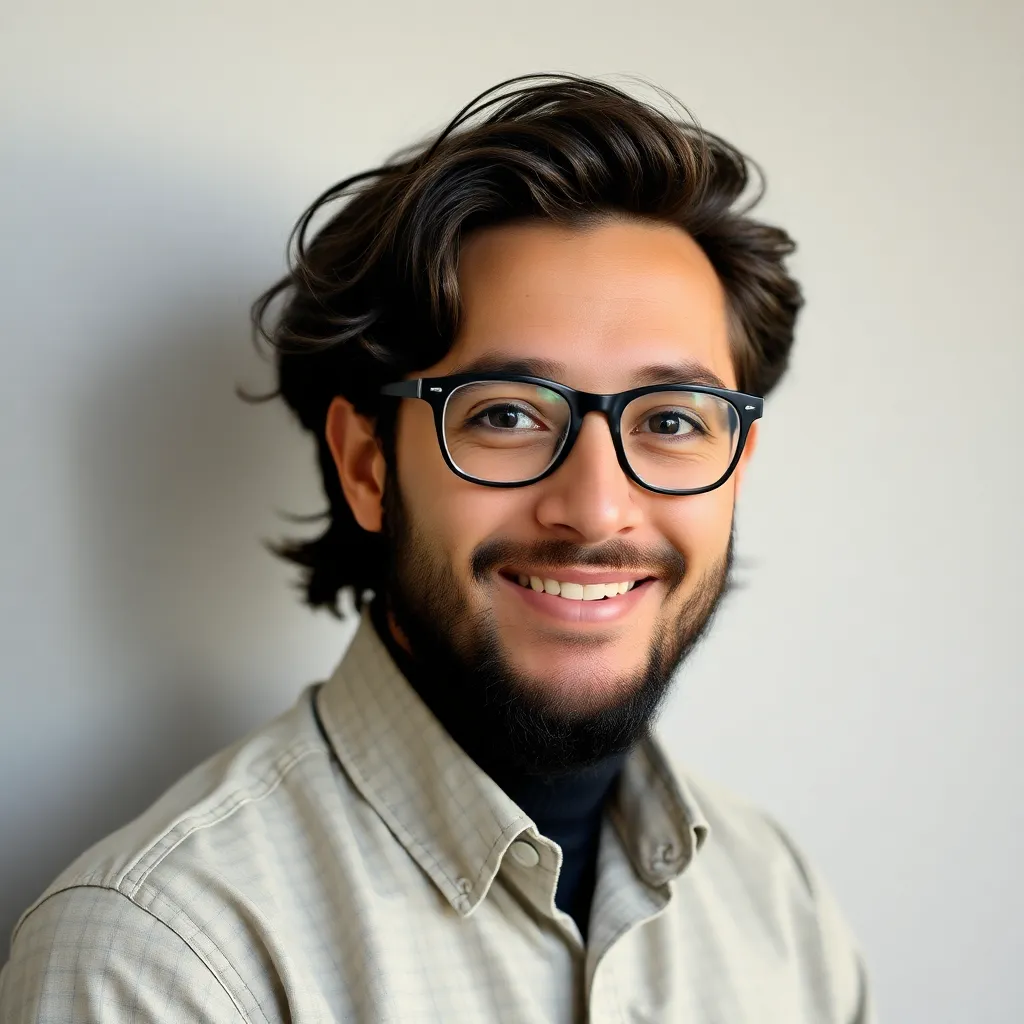
Onlines
May 08, 2025 · 6 min read

Table of Contents
How to Calculate Time to Fatigue: A Comprehensive Guide
Determining Time to Fatigue (TTF) is crucial across various disciplines, from materials science and engineering to human performance analysis. Understanding how long a material or system can withstand stress before failure is paramount for safety, efficiency, and cost-effectiveness. This comprehensive guide explores different methods for calculating TTF, considering the diverse factors influencing fatigue life.
What is Time to Fatigue (TTF)?
Time to fatigue, or time to failure under fatigue loading, refers to the duration a component or system can operate under cyclical loading before exhibiting signs of fatigue failure. This failure can manifest in various ways, including crack initiation and propagation, fracture, or significant degradation of material properties. The TTF is not a fixed value; it's a statistical prediction influenced by numerous variables.
Factors Affecting Time to Fatigue
Accurately predicting TTF requires a thorough understanding of the factors influencing fatigue behavior. These factors can be broadly categorized as:
1. Material Properties:
- Material Strength: Higher strength materials generally exhibit greater resistance to fatigue. However, the relationship isn't always linear; high-strength materials can sometimes be more susceptible to certain types of fatigue failure.
- Material Hardness: Hardness correlates with fatigue resistance, although the precise relationship depends on the specific material and loading conditions.
- Microstructure: The internal structure of the material, including grain size, grain boundaries, and the presence of defects, significantly influences fatigue life. Fine-grained materials often show superior fatigue resistance.
- Fracture Toughness: This parameter reflects a material's resistance to crack propagation. Higher fracture toughness generally means longer fatigue life.
2. Loading Conditions:
- Stress Amplitude: The magnitude of the cyclic stress significantly impacts TTF. Higher stress amplitudes lead to shorter fatigue lives.
- Mean Stress: The average stress level over a cycle also plays a crucial role. Higher mean stresses tend to reduce fatigue life.
- Frequency: The rate of cyclic loading can influence fatigue behavior. Higher frequencies can accelerate fatigue damage accumulation.
- Stress Ratio (R): This is the ratio of minimum stress to maximum stress in a cycle (R = σmin/σmax). It significantly affects fatigue life; lower R values generally lead to shorter fatigue lives.
- Loading Type: The type of loading (e.g., tension-compression, bending, torsion) influences the stress distribution and, consequently, the fatigue life.
3. Environmental Factors:
- Temperature: Elevated temperatures can accelerate fatigue damage, reducing TTF.
- Corrosion: Corrosive environments can significantly degrade material properties and accelerate fatigue crack growth, reducing TTF drastically.
- Humidity: Similar to corrosion, high humidity can promote material degradation and reduce fatigue life.
Methods for Calculating Time to Fatigue
Various methods exist for calculating or predicting TTF, each with its own assumptions and limitations:
1. S-N Curves (Stress-Life Approach):
This classic method uses experimental data to generate an S-N curve, which plots stress amplitude (S) against the number of cycles to failure (N). The curve is often represented logarithmically. By knowing the stress amplitude experienced by a component, one can estimate its fatigue life (N) from the curve. However, this method is primarily applicable to high-cycle fatigue (HCF), where failure occurs after a large number of cycles. For low-cycle fatigue (LCF), where failure occurs after a relatively small number of cycles, other methods are more suitable.
Limitations: S-N curves are material-specific and require extensive experimental testing. They don't directly provide TTF but rather the number of cycles to failure, which needs to be converted to time using the loading frequency.
2. Strain-Life Approach:
This approach focuses on the plastic strain experienced by a component under cyclic loading. It's particularly useful for LCF where plastic deformation is significant. The strain-life approach often involves the Coffin-Manson equation, which relates plastic strain amplitude to fatigue life.
Limitations: Accurate prediction requires detailed knowledge of material behavior under cyclic plastic deformation, which may necessitate complex material characterization.
3. Crack Propagation Models:
These models focus on the growth of pre-existing cracks under cyclic loading. The most common approach uses the Paris-Erdogan equation, which describes the rate of crack growth (da/dN) as a function of stress intensity factor range (ΔK). By integrating this equation, one can estimate the time required for a crack to grow to a critical size leading to failure.
Limitations: The accuracy of crack propagation models depends on the precise determination of initial crack size and the material's crack growth resistance. It's essential to accurately model the stress intensity factor, which can be complex for complicated geometries.
4. Finite Element Analysis (FEA):
FEA is a powerful computational technique used to simulate the stress and strain distribution within a component under cyclic loading. By combining FEA with fatigue analysis software, it's possible to predict TTF by monitoring the stress and strain levels at critical locations within the component.
Limitations: FEA requires detailed geometric modeling and accurate material properties. The computational cost can be substantial, particularly for complex geometries and loading conditions.
5. Probabilistic Methods:
TTF is inherently a probabilistic quantity due to the numerous uncertainties associated with material properties, loading conditions, and environmental factors. Probabilistic methods, such as Monte Carlo simulations, can account for these uncertainties and provide a more realistic prediction of TTF, including the probability of failure within a specific timeframe.
Limitations: Probabilistic methods require a good understanding of the statistical distribution of the input parameters and can be computationally intensive.
Practical Applications of TTF Calculation
Calculating TTF has widespread applications in various fields:
- Aerospace Engineering: Predicting the fatigue life of aircraft components is crucial for ensuring flight safety.
- Automotive Engineering: Determining the fatigue life of engine components, chassis parts, and other critical components is essential for vehicle reliability.
- Civil Engineering: Assessing the fatigue life of bridges, buildings, and other structures is vital for ensuring their structural integrity and safety.
- Biomedical Engineering: Understanding the fatigue life of implantable medical devices is crucial for patient safety.
- Manufacturing: Predicting the fatigue life of tools and machinery can help optimize maintenance schedules and reduce downtime.
Conclusion: A Multifaceted Approach
Calculating TTF is not a straightforward process. It necessitates a thorough understanding of material behavior under cyclic loading, the influence of various factors on fatigue life, and the limitations of different calculation methods. A multi-faceted approach, combining experimental data, analytical models, and numerical simulations, often provides the most accurate and reliable prediction of TTF. Remember that TTF predictions are inherently probabilistic, and incorporating uncertainties into the analysis is crucial for making informed decisions about component design, maintenance, and safety. The choice of method depends heavily on the specific application, available resources, and the desired level of accuracy. Continuous research and development in fatigue analysis continue to improve the accuracy and efficiency of TTF prediction.
Latest Posts
Latest Posts
-
Current Version Of The Firewall Software Used By Global Enterprises
May 08, 2025
-
When Is Organizational Culture Considered Dysfunctional
May 08, 2025
-
Financial Risk Refers To Which One Of These
May 08, 2025
-
Which Comment Is About The Diction Of A Story
May 08, 2025
-
Es Mejor Que En Casa Nosotros Cenar
May 08, 2025
Related Post
Thank you for visiting our website which covers about How To Calculate Time To Fatigue . We hope the information provided has been useful to you. Feel free to contact us if you have any questions or need further assistance. See you next time and don't miss to bookmark.