Identify The Characteristics Of Operations Where Repetitive Processing Is Used.
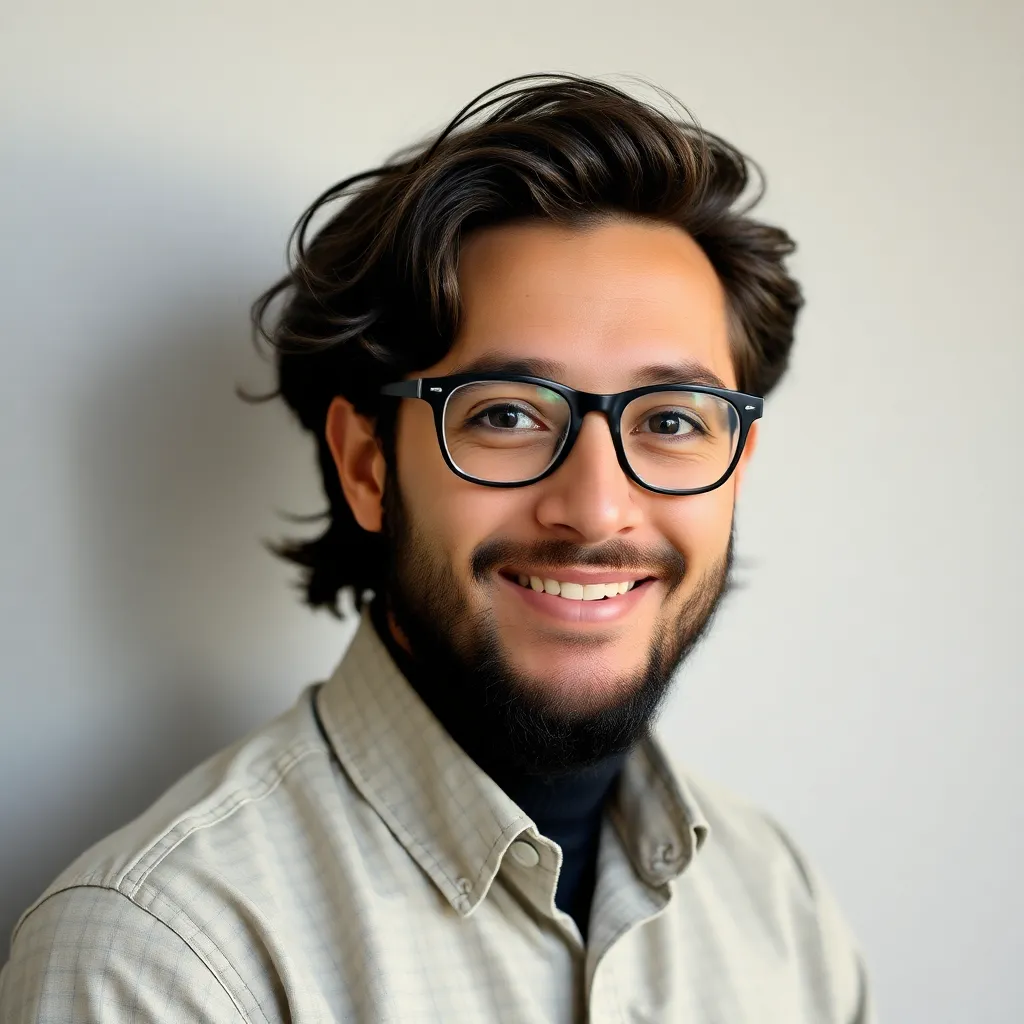
Onlines
May 08, 2025 · 6 min read
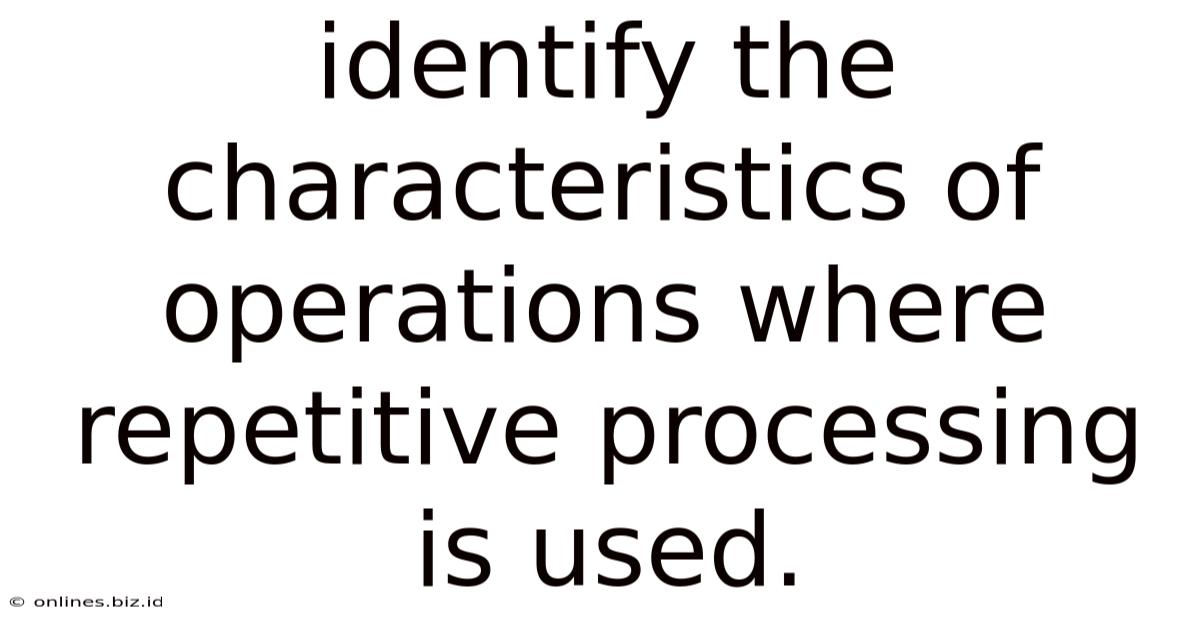
Table of Contents
Identify the Characteristics of Operations Where Repetitive Processing is Used
Repetitive processing, also known as mass production or high-volume manufacturing, is a production strategy where the same operations are performed repeatedly on a large number of identical or very similar units. This approach is fundamentally different from job-shop production, where each product is unique and requires a different set of operations. Understanding the characteristics of operations utilizing repetitive processing is crucial for businesses aiming for efficiency, scalability, and cost-effectiveness. This article delves deep into these characteristics, examining various aspects impacting implementation and success.
Key Characteristics of Operations Employing Repetitive Processing
Several key characteristics distinguish operations employing repetitive processing from other production methods. These characteristics are interconnected and often influence each other. Let's examine them in detail:
1. High Volume and Standardized Output
The most prominent feature of repetitive processing is the high volume of identical or nearly identical products produced. This high volume necessitates a streamlined, efficient process capable of handling large quantities. The output is standardized, meaning products consistently meet pre-defined specifications. Variations are minimal, allowing for efficient quality control and predictable production cycles. Think of automobile assembly lines or the production of electronic components – these industries thrive on high-volume, standardized output.
2. Specialized Equipment and Machinery
Repetitive processing heavily relies on specialized equipment and machinery. These machines are designed for specific tasks within the overall production process, maximizing efficiency and minimizing production time. This specialization leads to significant capital investment but ultimately results in faster production rates and lower per-unit costs. Imagine a bottling plant: specialized machinery handles everything from filling bottles to capping and labeling, each stage optimized for speed and precision.
3. Standardized Work Procedures and Processes
To ensure consistent quality and efficiency, repetitive processing demands standardized work procedures and processes. Every step in the production line is meticulously documented, outlining the exact methods, tools, and materials required. This standardization minimizes errors, reduces training time for workers, and simplifies quality control. Deviation from these standardized processes is carefully monitored and controlled.
4. Assembly Line or Flow Production Layout
The physical layout of the production facility plays a critical role in repetitive processing. A common layout is the assembly line or flow production arrangement. This layout ensures a smooth flow of materials and work-in-progress through the production process, minimizing bottlenecks and maximizing efficiency. Products move from one workstation to the next, with each workstation performing a specific operation. The layout is designed to optimize the movement of materials and minimize wasted space and time.
5. Division of Labor and Specialization
In repetitive processing operations, division of labor is highly pronounced. Workers specialize in specific tasks, becoming highly proficient at their assigned roles. This specialization leads to increased efficiency and reduces the time required to train new employees. However, it can also lead to job monotony if not carefully managed. Careful consideration should be given to employee well-being and job satisfaction.
6. Emphasis on Efficiency and Productivity
The primary goal of repetitive processing is to maximize efficiency and productivity. This means minimizing waste (material, time, energy) and maximizing output. Performance metrics are closely monitored, and improvements are constantly sought through process optimization, technological advancements, and employee training. Continuous improvement methodologies like Lean manufacturing and Six Sigma are commonly employed.
7. Predictable Production Schedules and Costs
Due to the standardized nature of the process, repetitive processing enables predictable production schedules and costs. This predictability allows for better planning, inventory management, and resource allocation. Businesses can accurately forecast demand and adjust production accordingly, minimizing the risk of shortages or overproduction. This is a significant advantage compared to job-shop production, where scheduling and cost estimation can be more complex.
8. Lower Per-Unit Costs
The high volume and efficient processes inherent in repetitive processing result in lower per-unit costs. The fixed costs associated with equipment and facility are spread over a large number of units, leading to significant economies of scale. This is a key reason why repetitive processing is preferred for mass-market products.
9. Limited Product Variety
While efficiency is a major benefit, repetitive processing often involves limited product variety. Modifying the production process to accommodate different products can be expensive and time-consuming. This limitation is often a trade-off for the benefits of high volume and low cost. Flexibility in product offerings is often reduced.
10. Potential for Automation
Repetitive processing lends itself well to automation. Many tasks can be automated using robots, programmable logic controllers (PLCs), and other automated systems. Automation increases efficiency, improves consistency, and reduces labor costs, although initial investment can be significant.
Examples of Industries Utilizing Repetitive Processing
Numerous industries heavily rely on repetitive processing to meet high demands for standardized products. Here are some prominent examples:
- Automotive Manufacturing: The assembly line is the quintessential example of repetitive processing. Cars are built using a standardized process, with each workstation performing a specific operation.
- Electronics Manufacturing: The production of smartphones, computers, and other electronic devices involves repetitive processing of components and sub-assemblies.
- Food Processing: Mass production of packaged foods, such as canned goods, snacks, and beverages, relies heavily on repetitive processing techniques.
- Pharmaceutical Manufacturing: The production of pills, capsules, and other pharmaceutical products is highly standardized and automated, utilizing repetitive processing.
- Textile Manufacturing: The production of fabrics, clothing, and other textile products often involves repetitive processing on automated machinery.
- Plastic Manufacturing: The production of plastic products, like bottles, containers, and toys, frequently employs repetitive processing techniques.
Challenges and Considerations in Repetitive Processing
While highly efficient, repetitive processing presents some challenges:
- High Initial Investment: The specialized equipment and machinery required for repetitive processing represent a significant upfront investment.
- Lack of Flexibility: Adapting the production process to produce different products can be costly and time-consuming.
- Job Monotony: The repetitive nature of the work can lead to job dissatisfaction and reduced employee motivation if not properly addressed through job rotation, enrichment, or other strategies.
- Dependence on Technology: Malfunction of machinery can disrupt the entire production process, highlighting the reliance on technology.
- Quality Control: While standardization aims for consistency, rigorous quality control mechanisms are essential to detect and rectify errors.
Conclusion: Optimizing Repetitive Processing for Success
Repetitive processing, while demanding in its initial setup and ongoing maintenance, offers significant advantages for businesses producing high volumes of standardized products. By understanding its characteristics, implementing appropriate technologies, and addressing potential challenges, businesses can harness its power to achieve efficiency, scalability, and cost-effectiveness. Careful attention to employee well-being, continuous improvement methodologies, and robust quality control systems is crucial for long-term success in this highly efficient production model. The future of repetitive processing likely involves further automation and the integration of advanced technologies such as AI and machine learning to optimize processes even further.
Latest Posts
Latest Posts
-
What Should You Try To Balance When Reducing Decision Making Risk
May 08, 2025
-
A Store Sells Notebooks For 3 Each
May 08, 2025
-
The Structure Of The Brush Border Aids Digestion By
May 08, 2025
-
Ecg Workout Exercises In Arrhythmia Interpretation Answer Key
May 08, 2025
-
Deciding Which Long Term Investment A Firm Should Make Is A
May 08, 2025
Related Post
Thank you for visiting our website which covers about Identify The Characteristics Of Operations Where Repetitive Processing Is Used. . We hope the information provided has been useful to you. Feel free to contact us if you have any questions or need further assistance. See you next time and don't miss to bookmark.