If Manufactreurs Had A Perfect Systme
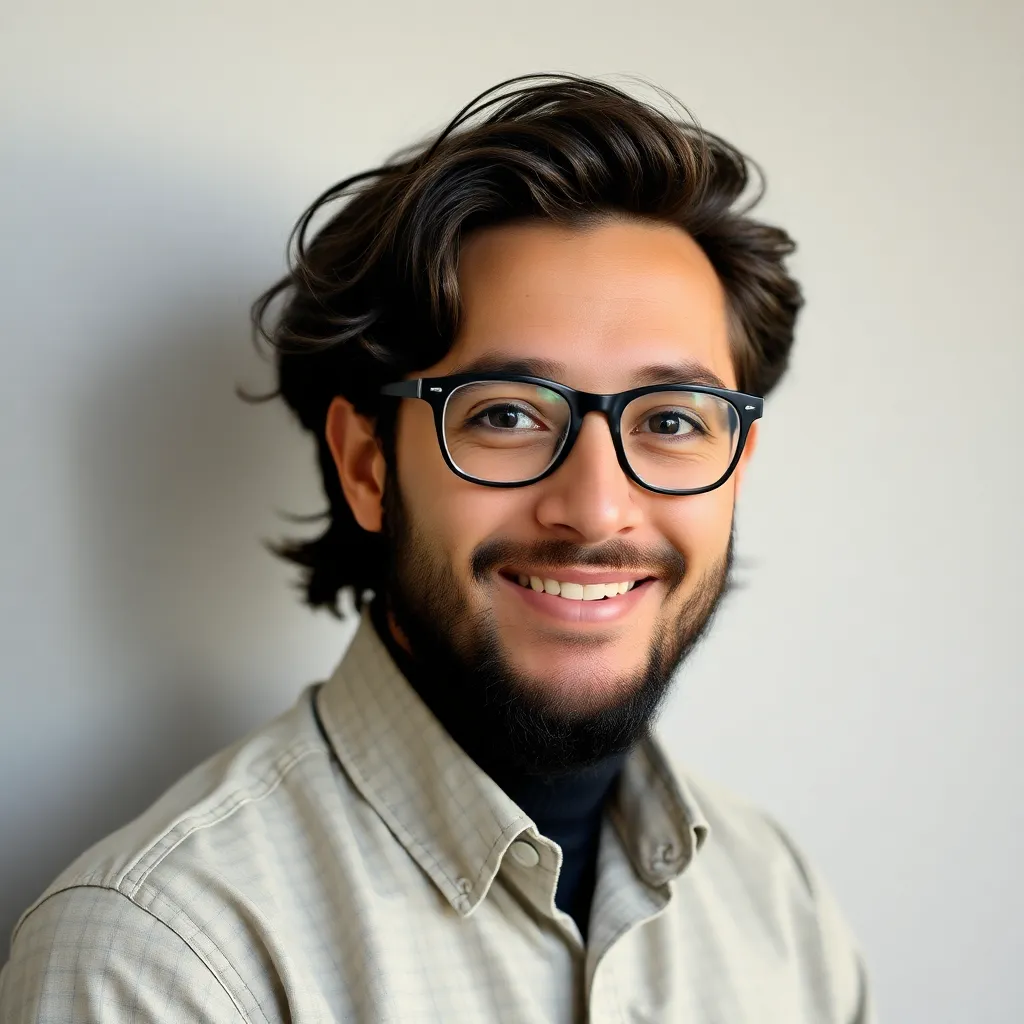
Onlines
Mar 06, 2025 · 6 min read
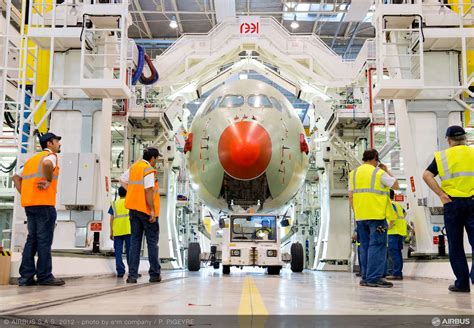
Table of Contents
If Manufacturers Had a Perfect System: A Vision of Seamless Production and Supply Chain Management
The pursuit of perfection is a driving force in manufacturing. While achieving a truly "perfect" system is an aspirational goal, understanding the components of such a system allows manufacturers to strive for continuous improvement and optimize their operations. This article delves into the hypothetical scenario of a perfect manufacturing system, exploring its key features, benefits, and the challenges in achieving it.
The Pillars of a Perfect Manufacturing System
A perfect manufacturing system would be characterized by seamless integration across all aspects of the production process, from initial design and raw material sourcing to final product delivery and customer support. Several key pillars would underpin this ideal:
1. Predictive and Preventative Maintenance
Predictive maintenance, using sensors and data analytics to anticipate equipment failures, would eliminate costly downtime. Instead of reactive maintenance – fixing problems after they occur – the system would proactively address potential issues, ensuring consistent production flow. This involves sophisticated data analysis, machine learning algorithms, and real-time monitoring of critical equipment parameters.
2. Real-Time Data Visibility and Control
A perfect system would offer complete transparency throughout the production process. Real-time data on production rates, inventory levels, quality metrics, and energy consumption would be readily available to all stakeholders. This visibility enables proactive decision-making, efficient resource allocation, and immediate identification and resolution of bottlenecks. This relies heavily on robust data collection systems, interconnected networks, and user-friendly dashboards.
3. Automated and Intelligent Processes
Automation wouldn't just be about replacing human labor; it would involve intelligent automation that adapts to changing conditions. Robots and automated systems would be integrated seamlessly, capable of learning, problem-solving, and self-optimization. This means incorporating AI and machine learning into the production line, creating a flexible and adaptable manufacturing environment.
4. Zero-Defect Manufacturing
The goal would be zero defects in the final product. This requires rigorous quality control measures integrated throughout the process, including advanced inspection technologies, statistical process control (SPC), and automated quality checks. A culture of continuous improvement would be essential, constantly refining processes to minimize errors. This might involve implementing technologies like computer vision for automated defect detection.
5. Sustainable and Ethical Practices
A perfect system wouldn't ignore its environmental and social impact. Sustainability would be integrated into every stage, from sourcing materials responsibly to minimizing waste and energy consumption. Ethical labor practices, fair wages, and safe working conditions would be paramount. This demands a holistic approach, considering the entire lifecycle of the product and its impact on the planet and society.
6. Optimized Supply Chain Management
The supply chain would be flawlessly integrated, ensuring a constant flow of materials and minimizing lead times. Advanced forecasting techniques, real-time tracking, and strong relationships with suppliers would ensure timely delivery of components and raw materials. This would necessitate strong partnerships with reliable suppliers, efficient logistics management, and the utilization of advanced technologies like blockchain for transparent supply chain tracking.
7. Customer-Centric Design and Production
The entire system would be geared towards meeting customer needs efficiently and effectively. Feedback mechanisms would be integrated to gather customer data, which would then inform product development and production planning. This involves sophisticated market research, agile product development processes, and personalized customer service.
Benefits of a Perfect Manufacturing System
The benefits of a perfect manufacturing system are far-reaching:
- Increased Efficiency and Productivity: Automation and optimized processes would lead to significantly higher output with reduced labor costs.
- Reduced Costs: Predictive maintenance, zero-defect manufacturing, and streamlined supply chains would minimize waste and downtime, lowering overall production costs.
- Improved Product Quality: Rigorous quality control measures would ensure consistently high-quality products, enhancing customer satisfaction and brand reputation.
- Enhanced Sustainability: Environmentally friendly practices would minimize the environmental impact of manufacturing operations.
- Greater Flexibility and Adaptability: Intelligent automation and real-time data visibility would allow for quick responses to changing market demands.
- Improved Customer Satisfaction: Faster delivery times, higher quality products, and personalized customer service would lead to increased customer loyalty.
- Stronger Competitive Advantage: A more efficient and effective manufacturing system would give companies a significant competitive edge in the market.
Challenges in Achieving a Perfect System
While the concept of a perfect manufacturing system is enticing, achieving it presents significant challenges:
- High Initial Investment: Implementing advanced technologies like AI, robotics, and predictive maintenance systems requires substantial upfront investment.
- Integration Complexity: Integrating different systems and technologies seamlessly can be technically challenging and require specialized expertise.
- Data Security and Privacy: Managing large volumes of sensitive data requires robust security measures to protect against cyber threats and ensure data privacy.
- Workforce Adaptation: The transition to automation may require retraining and upskilling the workforce to adapt to new roles and responsibilities.
- Unexpected Events and Disruptions: Even the most sophisticated systems can be affected by unforeseen events such as natural disasters, supply chain disruptions, or pandemics.
- Maintaining and Updating Technology: Continuous investment is needed to maintain and upgrade advanced technologies to ensure the system remains efficient and effective.
- Achieving Total Quality Control: Eliminating all defects is an extremely challenging goal, requiring meticulous attention to detail and continuous improvement efforts.
The Path to Perfection: Continuous Improvement
While a truly "perfect" system may remain an aspirational goal, manufacturers can continually strive for improvement by focusing on incremental advancements. This involves:
- Data-driven decision making: Using data analytics to identify areas for improvement and optimize processes.
- Embracing Industry 4.0 technologies: Implementing smart manufacturing technologies such as IoT, AI, and cloud computing.
- Investing in employee training and development: Equipping the workforce with the skills needed to operate and maintain advanced technologies.
- Building strong supply chain partnerships: Collaborating with reliable suppliers to ensure a stable supply of raw materials.
- Implementing robust quality control systems: Continuously monitoring and improving quality control processes to minimize defects.
- Adopting agile methodologies: Implementing flexible and adaptable production processes to respond to changing market demands.
- Focusing on sustainability: Integrating sustainable practices throughout the manufacturing process.
Conclusion
The pursuit of a perfect manufacturing system is a journey, not a destination. While achieving complete perfection may remain elusive, the relentless pursuit of continuous improvement, driven by data, technology, and a commitment to excellence, allows manufacturers to create increasingly efficient, effective, and sustainable operations. By focusing on the key pillars outlined above and embracing a culture of innovation, manufacturers can move closer to their vision of a seamless and optimized production process. This ultimately translates to increased profitability, enhanced customer satisfaction, and a more sustainable future for the manufacturing industry. The journey toward a "perfect" system, while challenging, is inherently rewarding, paving the way for a more competitive and responsible manufacturing landscape.
Latest Posts
Latest Posts
-
To Suffer Which Hope Thinks Infinite
Mar 08, 2025
-
Amenable To Scientific Study Using A Quantitative Approach
Mar 08, 2025
-
Always Avascular Cells Receive Nutrients From Deeper Tissue Layers
Mar 08, 2025
-
Ap Lit Unit 3 Progress Check Mcq
Mar 08, 2025
-
Which Is True Of Providing Oral Care For Patients
Mar 08, 2025
Related Post
Thank you for visiting our website which covers about If Manufactreurs Had A Perfect Systme . We hope the information provided has been useful to you. Feel free to contact us if you have any questions or need further assistance. See you next time and don't miss to bookmark.