In Today's Quality Control Programs Emphasis Is Placed On
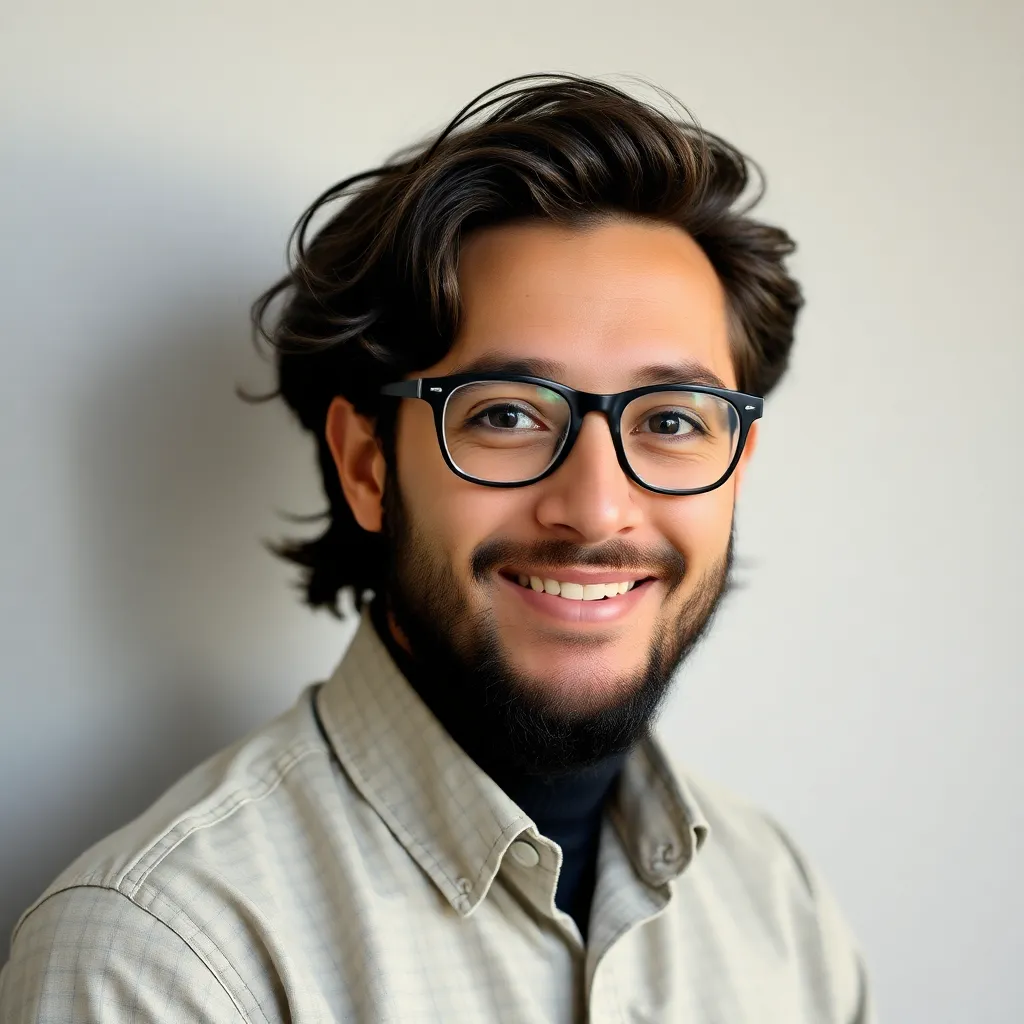
Onlines
May 11, 2025 · 6 min read
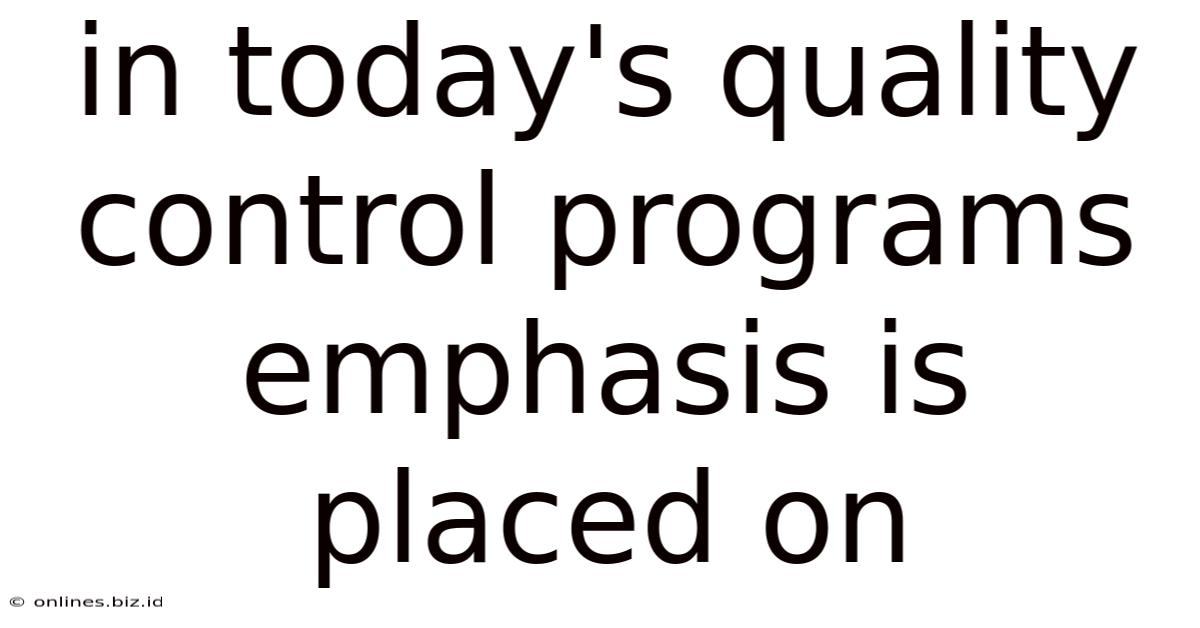
Table of Contents
In Today's Quality Control Programs, Emphasis is Placed on Proactive Prevention and Continuous Improvement
The landscape of quality control (QC) has undergone a dramatic transformation. No longer is it simply a reactive process of identifying defects after production. Today's successful QC programs are proactive, emphasizing prevention and continuous improvement as core tenets. This shift is driven by several factors, including increased global competition, heightened consumer expectations, and the rise of advanced technologies that enable more sophisticated monitoring and analysis. This article will delve into the key elements of modern QC programs, exploring the emphasis on prevention, data-driven decision making, and the crucial role of employee empowerment.
The Shift from Reactive to Proactive Quality Control
Traditionally, QC was largely a reactive process. Inspections were conducted at the end of the production line, identifying defects after they had already occurred. This approach was costly, inefficient, and often resulted in significant waste and customer dissatisfaction. The focus was on finding defects, not preventing them.
Modern QC programs are fundamentally different. The emphasis has shifted dramatically towards proactive prevention. This involves implementing rigorous processes and systems to prevent defects from occurring in the first place. This proactive approach includes:
1. Robust Design and Process Engineering:
A cornerstone of proactive QC is designing products and processes that are inherently less prone to defects. This involves incorporating robust design principles from the outset, considering factors like material selection, manufacturing tolerances, and potential points of failure. Design for Manufacturability (DFM) and Design for Six Sigma (DFSS) methodologies are often employed to optimize designs for quality and reduce the likelihood of defects.
2. Preventive Maintenance and Calibration:
Regular maintenance of equipment and tools is critical. Preventive maintenance schedules, meticulously planned and executed, minimize downtime and prevent equipment malfunctions that could lead to defects. Regular calibration of measuring instruments ensures accuracy and consistency in quality checks. This prevents inaccurate readings and flawed production.
3. Supplier Quality Management:
Quality control doesn't end with internal processes. Modern QC programs place significant emphasis on managing the quality of materials and components sourced from suppliers. This involves establishing robust supplier selection criteria, conducting regular audits of supplier facilities, and implementing collaborative quality improvement programs with key suppliers. This proactive approach ensures that the quality of incoming materials meets required standards.
4. Statistical Process Control (SPC):
SPC is a powerful tool for proactively monitoring and controlling processes. By using statistical methods to analyze process data, organizations can identify trends and variations that may indicate potential problems before they escalate into significant defects. This allows for timely interventions to prevent issues before they impact product quality.
Data-Driven Decision Making in Modern Quality Control
The availability of vast amounts of data and advanced analytics has revolutionized QC. Modern programs are heavily reliant on data-driven decision-making. This involves:
1. Real-time Data Collection and Monitoring:
Modern manufacturing processes generate a wealth of data, from machine sensor readings to production output statistics. Efficient data collection systems are crucial for capturing this information and making it readily accessible for analysis. Real-time monitoring dashboards provide immediate insights into process performance, allowing for quick identification and resolution of potential issues.
2. Advanced Analytics and Predictive Modeling:
Sophisticated analytical techniques, including machine learning and artificial intelligence (AI), are being increasingly used to analyze QC data. These tools can identify patterns and anomalies that might be missed by traditional methods. Predictive modeling allows for anticipating potential problems and proactively implementing corrective actions before defects occur.
3. Data Visualization and Reporting:
Effectively communicating QC data is crucial. Modern QC programs utilize data visualization tools to create clear and concise reports that communicate key findings to stakeholders. Interactive dashboards and visualizations make it easy to track performance, identify trends, and understand the impact of implemented improvements.
The Role of Employee Empowerment in Quality Control
A crucial aspect of modern QC programs is the empowerment of employees at all levels. This involves:
1. Training and Skill Development:
Investing in employee training is essential. Employees need to be adequately trained on QC procedures, statistical methods, and the use of relevant software and tools. This ensures that they have the skills and knowledge necessary to effectively contribute to quality improvement efforts.
2. Problem-Solving and Continuous Improvement Initiatives:
Modern QC programs encourage employee participation in problem-solving and continuous improvement initiatives. Lean methodologies, such as Kaizen, promote a culture of continuous improvement, where employees are actively involved in identifying and resolving quality issues. This fosters a sense of ownership and accountability amongst employees.
3. Open Communication and Feedback Mechanisms:
Open communication is essential for fostering a culture of quality. Establish clear channels for employees to communicate concerns, provide feedback, and suggest improvements. Regular feedback sessions and suggestion boxes provide valuable opportunities for employees to contribute to quality improvement.
Integrating Quality Control Throughout the Organization
Effective QC is not confined to a single department. Modern programs aim for complete organizational integration. This involves:
1. Cross-functional Collaboration:
Quality control is a shared responsibility. Effective QC programs involve collaboration between various departments, including engineering, manufacturing, procurement, and sales. Cross-functional teams can effectively address quality issues from a holistic perspective, considering the entire product lifecycle.
2. Alignment with Strategic Goals:
QC initiatives must be aligned with the overall strategic goals of the organization. This ensures that quality initiatives contribute directly to achieving the organization's objectives. Clear quality goals and metrics should be established and tracked to measure progress.
3. Culture of Continuous Improvement:
Finally, a culture of continuous improvement is paramount. This involves embedding quality principles into all aspects of the organization's operations. Regular review and improvement of QC processes are vital, ensuring that the program remains effective and adapts to evolving needs and challenges.
The Future of Quality Control
The future of quality control is likely to be characterized by:
- Increased automation and digitization: Automation and advanced technologies will play an increasingly important role in streamlining QC processes and enhancing efficiency. AI-powered systems will be capable of performing complex analysis and making informed decisions, freeing up human resources for more strategic tasks.
- Greater emphasis on data security and integrity: As QC programs become more reliant on data, ensuring the security and integrity of this data becomes paramount. Robust data management systems and security protocols will be essential.
- Enhanced customer engagement: Customer feedback will play an increasingly important role in driving quality improvement initiatives. Organizations will leverage customer feedback mechanisms to gather valuable insights and address customer concerns proactively.
In conclusion, modern quality control programs are a far cry from the reactive, end-of-line inspections of the past. The emphasis has shifted towards proactive prevention, leveraging data-driven insights and empowering employees to contribute to continuous improvement. By embracing these principles, organizations can enhance product quality, improve efficiency, and build stronger customer relationships, ultimately gaining a significant competitive advantage in today's market. The evolution of QC continues, driven by technological advancements and a growing awareness of the crucial role quality plays in business success. The organizations that prioritize proactive, data-driven, and employee-empowered quality control strategies will be best positioned to thrive in the years to come.
Latest Posts
Latest Posts
-
According To The Chart When Did A Pdsa Cycle Occur
May 12, 2025
-
Bioflix Activity Gas Exchange The Respiratory System
May 12, 2025
-
Economic Value Creation Is Calculated As
May 12, 2025
-
Which Items Typically Stand Out When You Re Scanning Text
May 12, 2025
-
Assume That Price Is An Integer Variable
May 12, 2025
Related Post
Thank you for visiting our website which covers about In Today's Quality Control Programs Emphasis Is Placed On . We hope the information provided has been useful to you. Feel free to contact us if you have any questions or need further assistance. See you next time and don't miss to bookmark.