Iso 9000 Currently Stresses _____ Of A Certified Organization.
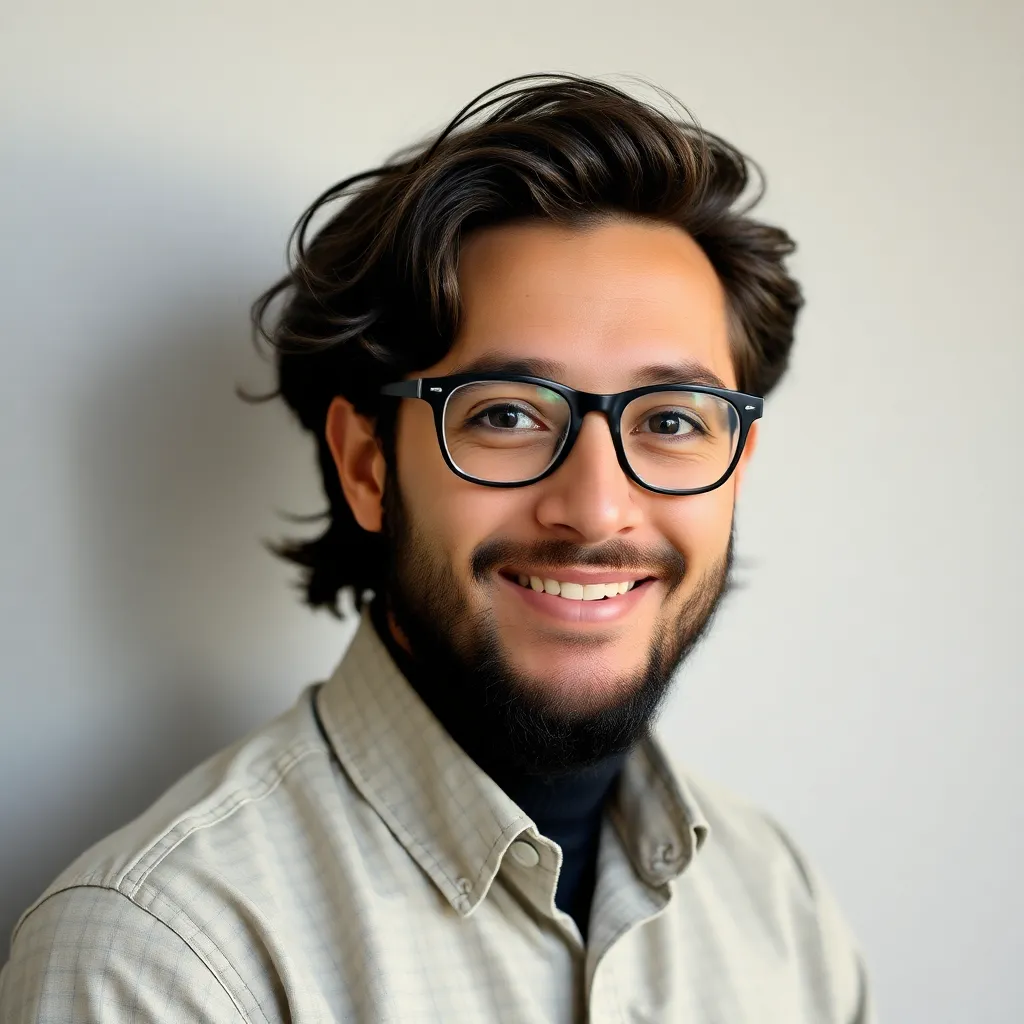
Onlines
May 12, 2025 · 6 min read
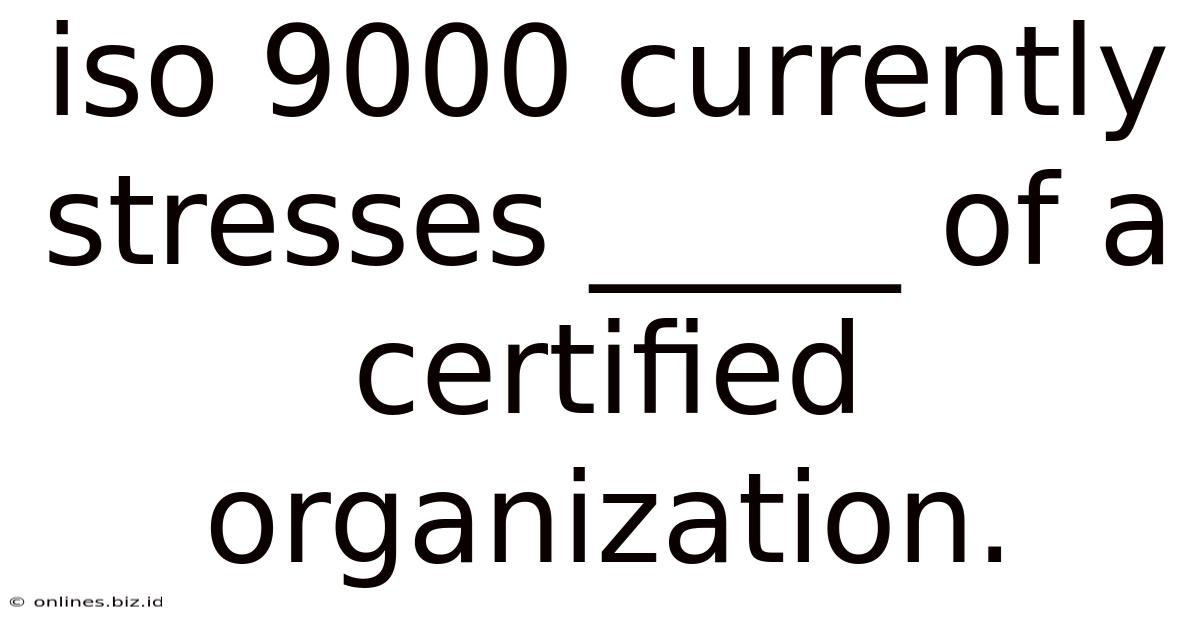
Table of Contents
ISO 9000 Currently Stresses Continuous Improvement of a Certified Organization
The ISO 9000 family of standards, specifically ISO 9001:2015, no longer focuses solely on meeting specified requirements. While conformity to customer requirements remains crucial, the current emphasis is firmly placed on continuous improvement. This shift reflects a deeper understanding of the dynamic nature of business and the need for organizations to adapt and evolve to remain competitive. This article will delve into the various aspects of continuous improvement as it relates to ISO 9001:2015 certification, examining its core principles, implementation strategies, and the significant benefits it brings to certified organizations.
The Evolution of ISO 9001 and the Emphasis on Continuous Improvement
Early iterations of ISO 9000 focused primarily on quality control and ensuring products or services met pre-defined specifications. The emphasis was largely reactive, addressing issues as they arose. However, the business landscape has changed dramatically. Globalization, technological advancements, and increasingly demanding customers necessitate a more proactive and dynamic approach to quality management.
The current standard, ISO 9001:2015, represents a significant departure from previous versions. It introduces a risk-based thinking approach, encouraging organizations to proactively identify and mitigate potential problems before they escalate. This proactive approach is intrinsically linked to continuous improvement, as identifying risks and addressing weaknesses are integral steps in the improvement cycle.
The standard emphasizes a process approach, recognizing that interconnected processes drive organizational performance. By understanding these processes and their interactions, organizations can identify areas for improvement, streamlining workflows and enhancing efficiency. This process approach is the foundation for the continuous improvement cycle.
Key Principles of Continuous Improvement within ISO 9001:2015
ISO 9001:2015 isn't just about achieving certification; it's about using the framework as a catalyst for ongoing growth and refinement. Several core principles underpin the continuous improvement concept within the standard:
1. Plan-Do-Check-Act (PDCA) Cycle:
The PDCA cycle, also known as the Deming cycle, is the cornerstone of continuous improvement. It involves:
- Plan: Defining objectives, identifying processes, and establishing methods for improvement. This stage requires careful analysis of current processes, identification of areas for improvement, and setting measurable targets.
- Do: Implementing the planned changes on a small scale, preferably as a pilot program, to test their effectiveness.
- Check: Monitoring the results of the implemented changes, collecting data, and analyzing its impact on the processes. This stage involves rigorous data analysis to determine whether the changes resulted in the desired improvements.
- Act: Standardizing successful changes, implementing them across the organization, and documenting the entire process for future reference. This stage also includes addressing any issues encountered during implementation and making further adjustments as needed.
The PDCA cycle is iterative, meaning organizations constantly repeat the cycle, refining their processes and making incremental improvements over time.
2. Data-Driven Decision Making:
Effective continuous improvement relies heavily on data. Organizations must meticulously collect and analyze data related to their processes, identifying trends, patterns, and areas for potential improvement. This data informs decision-making, ensuring that improvements are targeted and effective. Without solid data, improvements become arbitrary and may not yield the desired results. This emphasis on data reflects the standard's focus on evidence-based management.
3. Proactive Risk Management:
ISO 9001:2015 emphasizes proactive risk management. Organizations should identify potential risks and opportunities that could affect their ability to meet customer requirements and continuously improve. By proactively identifying and mitigating risks, organizations can prevent problems from occurring and avoid costly disruptions. This proactive approach prevents reactive firefighting and fosters a more stable and efficient operational environment.
4. Customer Focus:
Continuous improvement is ultimately driven by customer needs and expectations. Understanding customer requirements and feedback is essential for identifying areas for improvement and ensuring that changes align with customer satisfaction. Regular customer feedback mechanisms and surveys provide vital insights into areas requiring attention. Meeting and exceeding customer expectations is a key driver of long-term success and organizational sustainability.
5. Employee Empowerment:
Engaging employees in the continuous improvement process is critical. Empowering employees to identify and propose improvements fosters a culture of innovation and ownership. Employees closest to the processes often have the best insight into areas for improvement. Providing training and opportunities for employee involvement fosters a more engaged and productive workforce.
Implementing Continuous Improvement Strategies
Implementing continuous improvement within the framework of ISO 9001:2015 requires a structured and systematic approach. Organizations can leverage several strategies to effectively drive continuous improvement:
- Regular Management Reviews: These reviews provide an opportunity to assess the effectiveness of the quality management system (QMS), identify areas for improvement, and set objectives for future enhancements.
- Internal Audits: Internal audits help organizations identify nonconformities and opportunities for improvement within their QMS. This systematic internal evaluation is crucial for early detection and prevention of issues.
- Corrective and Preventive Actions (CAPA): A robust CAPA system is essential for addressing identified problems, preventing recurrence, and continuously improving processes.
- Process Mapping and Analysis: Visualizing processes through process mapping helps identify bottlenecks, redundancies, and other inefficiencies that can be targeted for improvement. This visual representation facilitates a more thorough understanding of the processes and their interdependencies.
- Benchmarking: Comparing performance against industry best practices or leading competitors can identify areas for improvement and set targets for enhanced performance.
- Kaizen Events: Short, focused improvement initiatives involving cross-functional teams can quickly address specific process issues and promote a culture of continuous improvement. These events create a collaborative environment for focused problem-solving.
- Lean and Six Sigma Methodologies: These powerful methodologies provide a structured approach to process improvement, focusing on eliminating waste and reducing variation.
Benefits of Continuous Improvement for ISO 9001 Certified Organizations
The benefits of embracing continuous improvement within an ISO 9001 framework are numerous and far-reaching:
- Enhanced Customer Satisfaction: Continuous improvement directly leads to better products and services, boosting customer satisfaction and loyalty.
- Increased Efficiency and Productivity: Streamlined processes and reduced waste contribute to improved efficiency and productivity throughout the organization.
- Reduced Costs: By identifying and eliminating inefficiencies, organizations can significantly reduce operational costs.
- Improved Product and Service Quality: A focus on continuous improvement leads to higher quality products and services, enhancing the organization's reputation and competitive advantage.
- Greater Employee Engagement: Empowering employees and involving them in the improvement process fosters a more engaged and motivated workforce.
- Increased Profitability: The combined effect of enhanced efficiency, reduced costs, and improved product quality translates into increased profitability.
- Stronger Competitive Advantage: Organizations that consistently improve their processes and products are better positioned to compete in the marketplace.
- Improved Risk Management: Proactive risk identification and mitigation contribute to a more stable and resilient organization.
- Enhanced Organizational Learning: The continuous improvement process fosters a culture of learning and adaptation, enabling the organization to respond effectively to changing circumstances.
Conclusion: Continuous Improvement – The Heart of ISO 9001
ISO 9001:2015 certification is not a destination but a journey. The emphasis on continuous improvement reflects a fundamental shift in how organizations approach quality management. It's no longer enough to simply meet requirements; organizations must strive for constant improvement to remain competitive and thrive in today's dynamic business environment. By embracing the principles and strategies outlined in this article, organizations can harness the full potential of ISO 9001 and use it as a springboard for sustained growth and success. The commitment to continuous improvement is not merely a requirement of the standard; it is the heart of its effectiveness and the key to long-term organizational success. The journey of continuous improvement is ongoing; it’s a commitment to excellence that defines truly successful organizations.
Latest Posts
Related Post
Thank you for visiting our website which covers about Iso 9000 Currently Stresses _____ Of A Certified Organization. . We hope the information provided has been useful to you. Feel free to contact us if you have any questions or need further assistance. See you next time and don't miss to bookmark.