Leaders Safety Course Module 6 Answers
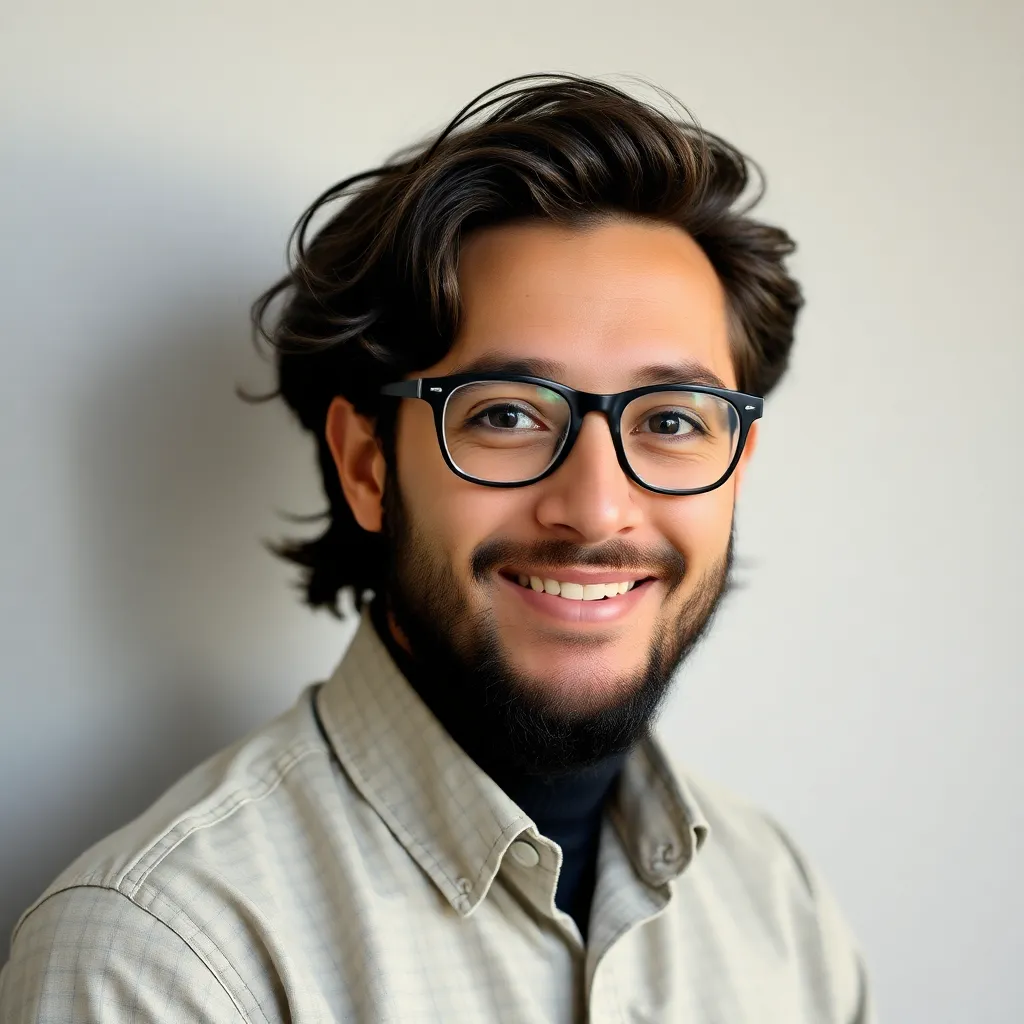
Onlines
Mar 20, 2025 · 6 min read
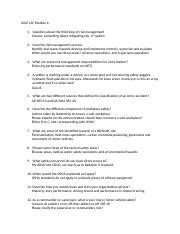
Table of Contents
Leader's Safety Course Module 6 Answers: A Comprehensive Guide
This article provides a comprehensive overview of the likely content covered in Module 6 of a typical Leader's Safety Course, offering insights into potential questions and comprehensive answers. Note that specific questions and answers will vary depending on the course provider and curriculum. This guide aims to equip you with the knowledge and understanding needed to excel in this module, regardless of the specific course materials. Always refer to your official course materials for the most accurate and up-to-date information.
Module 6 typically focuses on advanced hazard identification, risk assessment, and control strategies. Specific topics may include:
Understanding Advanced Hazard Identification Techniques
This section builds upon the foundational knowledge of hazard identification learned in previous modules. It delves deeper into sophisticated techniques to uncover hidden or less obvious hazards.
Proactive Hazard Hunting:
-
Beyond the Obvious: This section emphasizes moving beyond readily apparent hazards and focusing on latent conditions – those that may not immediately present a risk but have the potential to cause an incident under specific circumstances. Examples include poorly maintained equipment that might fail under stress, inadequate training leading to human error, or systemic issues within processes.
-
Scenario Planning: This involves creating hypothetical scenarios to identify potential hazards and near misses. By thinking through different possibilities, you can proactively identify vulnerabilities and implement preventative measures before an incident occurs. Example: What would happen if the power went out during a critical operation? What backup systems are in place?
-
Job Safety Analysis (JSA): A systematic method for identifying hazards associated with specific tasks. It involves breaking down a task into individual steps and analyzing each step for potential hazards. Key elements include identifying the hazard, assessing the risk, and implementing control measures. JSAs are particularly valuable for high-risk tasks.
-
HAZOP (Hazard and Operability Study): A more complex technique used for larger projects or processes. It involves a structured team review using guide words (e.g., "more," "less," "as well as," "no," "part of") to systematically explore deviations from the intended design or operation and identify potential hazards.
Using Technology for Hazard Identification:
-
Near Miss Reporting Systems: Effective near miss reporting is crucial for identifying potential hazards before they escalate into accidents. This section would cover best practices for encouraging reporting, analyzing near misses to identify trends and underlying causes, and using this information to improve safety procedures.
-
Data Analysis: This involves collecting and analyzing safety data to identify trends, patterns, and areas where improvements are needed. Statistical analysis can reveal hidden correlations between different factors and highlight high-risk areas.
-
Software Tools: Many software tools are available to assist with hazard identification, risk assessment, and management. This section might introduce some of these tools and their applications.
Advanced Risk Assessment and Control Strategies
Building on the fundamental understanding of risk assessment, this section introduces more sophisticated methods for evaluating and controlling risks.
Qualitative Risk Assessment Techniques:
-
Risk Matrix: A common tool for visually representing the likelihood and severity of identified hazards. It involves plotting hazards on a matrix and assigning risk levels based on their combinations. This section would emphasize understanding the different scales used and the limitations of relying solely on a risk matrix.
-
Fault Tree Analysis (FTA): A deductive method for analyzing the causes of an undesirable event (a top event). It involves working backward from the top event to identify the contributing factors and their probabilities. FTA is particularly useful for understanding complex systems and identifying the most critical causes.
-
Event Tree Analysis (ETA): A complementary technique to FTA. It starts with an initiating event and analyzes the possible outcomes based on the success or failure of safety systems. ETA is useful for analyzing the probability of various accident scenarios.
Quantitative Risk Assessment Techniques:
-
Probabilistic Risk Assessment (PRA): A more sophisticated technique that uses numerical data to estimate the probability of various accident scenarios and their consequences. PRA is often used for high-stakes industries, such as nuclear power or aviation.
-
Bow-Tie Analysis: A visual tool that combines aspects of FTA and ETA, showing the events leading up to an incident (the left-hand side of the bow tie), the incident itself (the knot), and the consequences (the right-hand side). It helps to identify preventative and mitigating controls.
Hierarchy of Controls:
This section reinforces the importance of using a hierarchical approach to risk control, prioritizing the most effective methods:
-
Elimination: Removing the hazard altogether.
-
Substitution: Replacing the hazard with something less hazardous.
-
Engineering Controls: Implementing physical or engineering changes to reduce or eliminate the hazard.
-
Administrative Controls: Implementing changes in work practices, procedures, or training to mitigate the risk.
-
Personal Protective Equipment (PPE): Providing workers with PPE to protect them from hazards as a last resort.
Implementing and Monitoring Control Measures
Effective risk management isn't just about identifying and assessing risks; it's about implementing and regularly monitoring control measures.
Implementing Control Measures:
-
Clear Communication: Ensuring that all relevant personnel are aware of and understand the implemented control measures.
-
Training and Competency: Providing adequate training to ensure that workers are competent to perform their tasks safely and know how to use the control measures effectively.
-
Documentation: Maintaining detailed records of all hazard identification, risk assessment, and control measures. This is crucial for auditing and continuous improvement.
Monitoring and Review:
-
Regular Inspections: Conducting regular inspections to ensure that control measures are effective and are being followed.
-
Audits: Carrying out periodic audits to assess the overall effectiveness of the safety management system.
-
Incident Reporting and Investigation: Establishing robust procedures for reporting and investigating incidents to learn from mistakes and identify areas for improvement. This involves root cause analysis to determine the underlying causes of incidents and prevent recurrence.
-
Continuous Improvement: Using the information gathered from inspections, audits, and incident investigations to continuously improve the safety management system. This is a cyclical process of identifying hazards, assessing risks, implementing controls, monitoring effectiveness, and making improvements based on findings.
Leadership Roles in Safety
This section emphasizes the crucial role of leaders in creating and maintaining a strong safety culture.
Leading by Example:
Leaders must demonstrate a strong commitment to safety by following all safety rules and regulations themselves. This sets the tone for the entire organization and encourages others to prioritize safety.
Empowering Employees:
Leaders should empower employees to identify hazards, report near misses, and participate in safety initiatives. A strong safety culture relies on open communication and collaboration.
Accountability and Responsibility:
Leaders should hold themselves and their teams accountable for safety performance. This includes establishing clear roles, responsibilities, and lines of accountability for safety management.
Promoting a Positive Safety Culture:
Leaders play a crucial role in creating a positive safety culture where safety is valued and prioritized above all else. This involves promoting open communication, encouraging participation in safety initiatives, and recognizing and rewarding safe behavior.
This detailed overview provides a solid foundation for understanding the potential content of Module 6 in a Leader's Safety Course. Remember to consult your official course materials for specific information and to ensure you are fully prepared for any assessment. Safe practices are essential, and continuous learning is key to maintaining a safe and productive workplace.
Latest Posts
Latest Posts
-
Rn Learning System Communication Final Quiz
Mar 21, 2025
-
Sedra Smith Microelectronic Circuits 8th Edition Solutions Pdf
Mar 21, 2025
-
Interactive Tutorial Forming Questions In Spanish
Mar 21, 2025
-
Tienes Tu Cuaderno No No 1 Of 1 Tengo
Mar 21, 2025
-
What Inference Does The Text Best Support
Mar 21, 2025
Related Post
Thank you for visiting our website which covers about Leaders Safety Course Module 6 Answers . We hope the information provided has been useful to you. Feel free to contact us if you have any questions or need further assistance. See you next time and don't miss to bookmark.